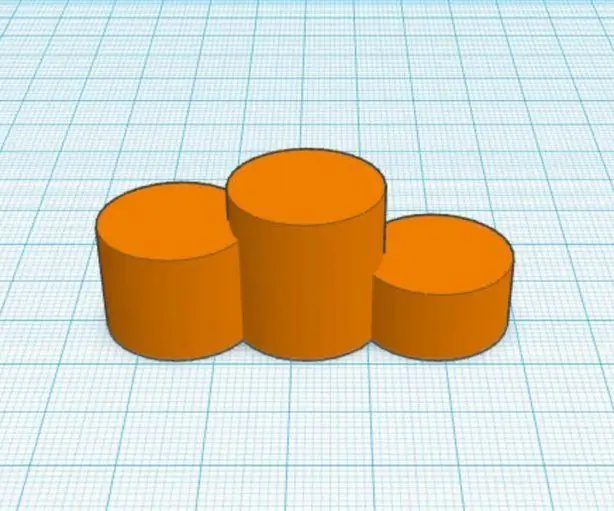
Spisu treści:
- Krok 1: Podstawy wyświetlaczy ciekłokrystalicznych
- Krok 2: Podstawowy schemat blokowy GreenPAK Design
- Krok 3: Zaprojektuj pobór prądu
- Krok 4: Schemat urządzenia GreenPAK
- Krok 5: Interfejs I²C
- Krok 6: Sterownik segmentu wyjściowego
- Krok 7: Kontrola źródła wewnętrznego oscylatora i zegara kasety
- Krok 8: Wyjście zegara płyty montażowej lub sterowanie pinami wyjściowymi segmentu 15
- Krok 9: Prototyp systemu LCD
- Krok 10: Polecenia I²C do sterowania LCD
- Krok 11: Polecenia I²C dla testu LCD
- Krok 12: Wyniki testu
2025 Autor: John Day | [email protected]. Ostatnio zmodyfikowany: 2025-06-01 06:10
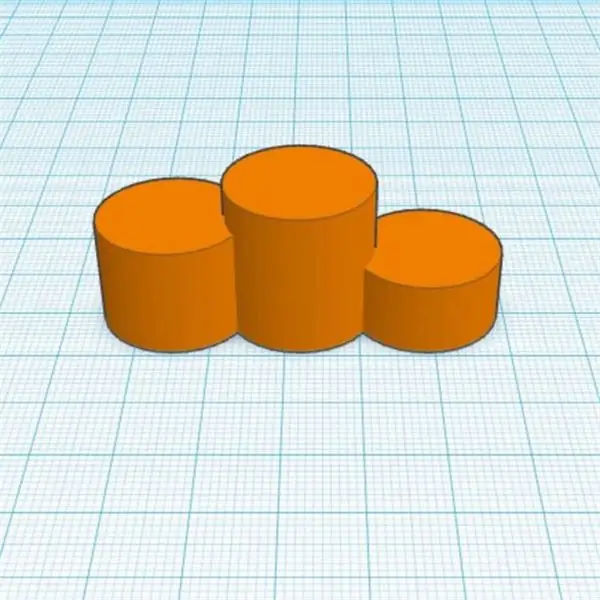
Wyświetlacze ciekłokrystaliczne (LCD) są szeroko stosowane w zastosowaniach komercyjnych i przemysłowych ze względu na ich dobre właściwości wizualne, niski koszt i niskie zużycie energii. Te właściwości sprawiają, że LCD jest standardowym rozwiązaniem dla urządzeń zasilanych bateryjnie, takich jak instrumenty przenośne, kalkulatory, zegarki, radia itp.
Jednak, aby właściwie kontrolować to, co pokazuje wyświetlacz LCD, sterownik elektroniczny wyświetlacza LCD musi generować odpowiednie przebiegi napięcia na pinach wyświetlacza LCD. Przebiegi powinny mieć charakter AC (prądu przemiennego), ponieważ napięcia DC (prąd stały) trwale uszkodzą urządzenie. Odpowiedni sterownik będzie przesyłał te sygnały do wyświetlacza LCD przy minimalnym zużyciu energii.
Istnieją dwa typy wyświetlaczy LCD, statyczne, z tylko jedną płytą montażową i jednym pinem do kontroli poszczególnych segmentów oraz multipleksowane, z wieloma płytami bazowymi i wieloma segmentami podłączonymi dla każdego pinu.
Ta instrukcja przedstawi projekt jednego statycznego sterownika LCD z urządzeniem SLG46537V GreenPAK™. Zaprojektowany sterownik LCD mógłby obsługiwać do 15 segmentów LCD, wykorzystując kilka mikroamperów prądu z zasilacza i oferować interfejs I²C do sterowania.
W poniższych sekcjach zostaną pokazane:
● podstawowe informacje o wyświetlaczach LCD;
● szczegółowy projekt sterownika LCD SLG46537V GreenPAK;
● jak obsługiwać siedmiosegmentowy, 4-cyfrowy statyczny wyświetlacz LCD za pomocą dwóch urządzeń GreenPAK.
Poniżej opisaliśmy kroki potrzebne do zrozumienia, jak zaprogramowano rozwiązanie, aby stworzyć statyczny sterownik LCD z interfejsem I²C. Jeśli jednak chcesz tylko uzyskać wynik programowania, pobierz oprogramowanie GreenPAK, aby wyświetlić już ukończony plik projektu GreenPAK. Podłącz GreenPAK Development Kit do komputera i naciśnij program, aby utworzyć statyczny sterownik LCD z interfejsem I²C.
Krok 1: Podstawy wyświetlaczy ciekłokrystalicznych
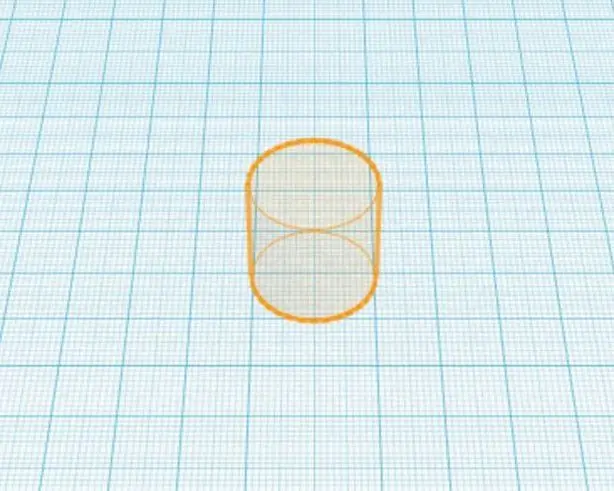
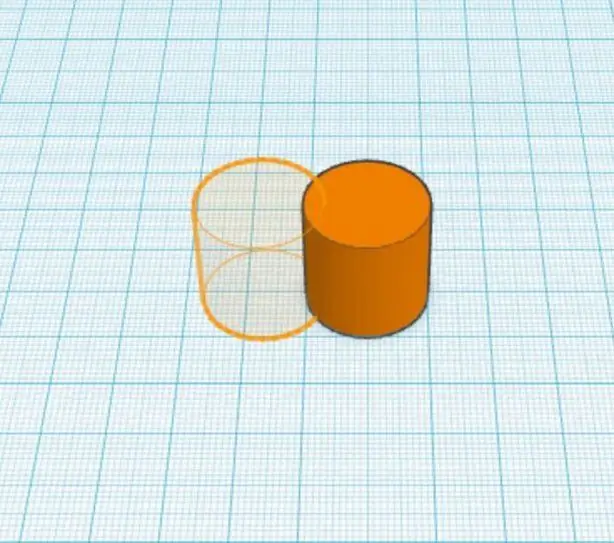
Wyświetlacze ciekłokrystaliczne (LCD) to technologia, która nie emituje światła, kontroluje jedynie sposób, w jaki przechodzi zewnętrzne źródło światła. Tym zewnętrznym źródłem światła może być dostępne światło otoczenia, w przypadku wyświetlacza odblaskowego, lub światło z podświetlanej diody LED lub lampy, w przypadku wyświetlacza transmisyjnego. Wyświetlacze LCD zbudowane są z dwóch płyt szklanych (górna i dolna), pomiędzy którymi znajduje się cienka warstwa ciekłokrystaliczna (LC) oraz dwa polaryzatory światła (Nota aplikacyjna AN-001 - Podstawy technologii LCD, Hitachi, Nota aplikacyjna AN-005 - Wyświetlacz Tryby, Hitachi). Polaryzator jest filtrem świetlnym dla lekkiego pola elektromagnetycznego. Tylko składowe światła w odpowiednim kierunku pola elektromagnetycznego przechodzą przez polaryzator, podczas gdy inne składowe są blokowane.
Ciekły kryształ to materiał organiczny, który obraca pole elektromagnetyczne światła o 90 stopni lub więcej. Jednak po przyłożeniu pola elektrycznego do LC nie powoduje ono już obracania światła. Dzięki dodaniu przezroczystych elektrod w górnej i dolnej szybie wyświetlacza możliwe jest kontrolowanie, kiedy światło przechodzi, a kiedy nie, za pomocą zewnętrznego źródła pola elektrycznego. Rysunek 1 (patrz nota aplikacyjna AN-001 - Podstawy technologii LCD, Hitachi) powyżej ilustruje ten sposób sterowania. Na rysunku 1 wyświetlacz jest ciemny, gdy nie ma pola elektrycznego. Dzieje się tak, ponieważ oba polaryzatory filtrują światło w tym samym kierunku. Jeśli polaryzatory są ortogonalne, wyświetlacz będzie ciemny, gdy obecne jest pole elektryczne. Jest to najczęstsza sytuacja w przypadku wyświetlaczy odblaskowych.
Minimalne pole elektryczne lub napięcie do sterowania wyświetlaczem LCD nazywa się progiem włączenia. Na LC ma wpływ tylko napięcie, a w materiale LC prawie nie ma prądu. Elektrody w LCD tworzą małą pojemność i jest to jedyne obciążenie dla sterownika. To jest powód, dla którego LCD jest urządzeniem o niskim poborze mocy do wyświetlania informacji wizualnych.
Należy jednak pamiętać, że wyświetlacz LCD nie może działać zbyt długo ze źródłem napięcia prądu stałego (DC). Przyłożenie napięcia stałego spowoduje reakcje chemiczne w materiale LC, trwale go uszkadzając (Nota Aplikacyjna AN-001 - Podstawy Technologii LCD, Hitachi). Rozwiązaniem jest zastosowanie napięcia przemiennego (AC) w elektrodach LCD.
W statycznych wyświetlaczach LCD elektroda płyty montażowej jest wbudowana w jedną szybę, a poszczególne segmenty lub piksele wyświetlacza LCD są umieszczane w drugiej szybie. Jest to jeden z najprostszych typów LCD i ten o najlepszym współczynniku kontrastu. Jednak ten typ wyświetlacza zwykle wymaga zbyt wielu pinów do sterowania każdym pojedynczym segmentem.
Ogólnie rzecz biorąc, sterownik sterownika dostarcza razem sygnał zegarowy o przebiegu prostokątnym dla płyty montażowej i sygnał zegarowy dla segmentów na płycie przedniej. Gdy zegar płyty tylnej jest w fazie z zegarem segmentu, napięcie średniej kwadratowej (RMS) między obiema płaszczyznami wynosi zero, a segment jest przezroczysty. W przeciwnym razie, jeśli napięcie RMS jest wyższe niż próg włączenia LCD, segment staje się ciemny. Przebiegi dla płyty tylnej, segmentu włączenia i wyłączenia pokazano na rysunku 2. Jak widać na rysunku, segment ON jest przesunięty w fazie w stosunku do sygnału płyty tylnej. Segment wyłączony jest w fazie w stosunku do sygnału płyty montażowej. Przyłożone napięcie może wynosić od 3 do 5 woltów w przypadku tanich wyświetlaczy o małej mocy.
Sygnał zegarowy dla płyty montażowej i segmentów LCD zwykle mieści się w zakresie od 30 do 100 Hz, minimalnej częstotliwości, aby uniknąć wizualnego efektu migotania na wyświetlaczu LCD. Unika się wyższych częstotliwości, aby zmniejszyć zużycie energii całego systemu. System złożony z LCD i sterowników zużywałby mało prądu, rzędu mikroamperów. Dzięki temu doskonale nadają się do zastosowań o niskim poborze mocy i zasilaniu bateryjnym.
W kolejnych sekcjach szczegółowo przedstawiono projekt sterownika statycznego LCD z urządzeniem GreenPAK, który może generować sygnał zegarowy płyty tylnej oraz sygnał zegarowy pojedynczego segmentu dla komercyjnego wyświetlacza LCD.
Krok 2: Podstawowy schemat blokowy GreenPAK Design
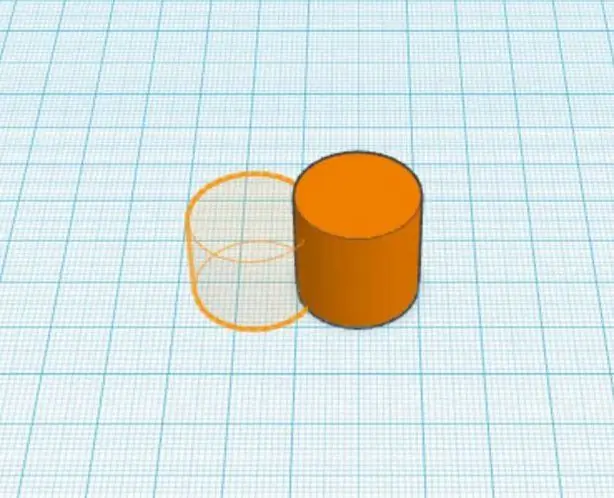
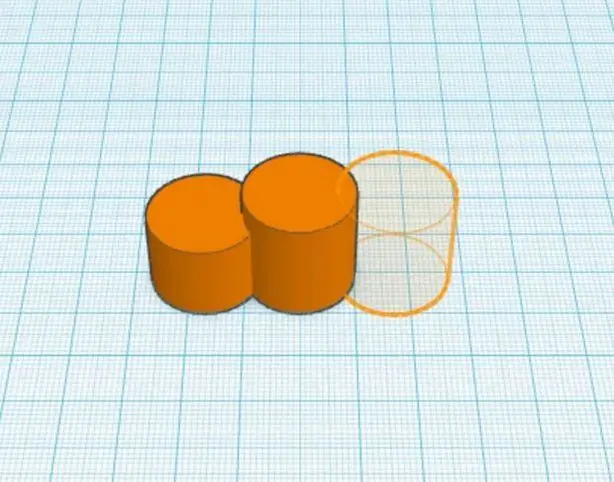
Schemat blokowy ilustrujący projekt GreenPAK pokazano na rysunku 3. Podstawowe bloki projektu to interfejs I²C, sterownik segmentu wyjściowego, oscylator wewnętrzny i selektor źródła zegara na płycie tylnej.
Blok interfejsu I²C steruje każdym indywidualnym wyjściem segmentu i źródłem zegara tylnej płyty LCD. Blok interfejsu I²C jest jedynym wejściem systemowym do sterowania wyjściem segmentu.
Gdy linia kontrolna segmentu wewnętrznego jest ustawiona (wysoki poziom), odpowiedni segment LCD jest ciemny, nieprzezroczysty. Gdy linia kontrolna segmentu wewnętrznego jest zresetowana (niski poziom), odpowiedni segment LCD jest przezroczysty.
Każda linia kontrolna segmentu wewnętrznego jest podłączona do sterownika wyjściowego. Blok sterownika segmentu wyjściowego będzie generował sygnał zegara w fazie w odniesieniu do zegara płyty tylnej dla segmentów przezroczystych. W przypadku ciemnych segmentów sygnał ten jest przesunięty w fazie w stosunku do zegara kasety.
Źródło zegara płyty montażowej jest również wybierane z interfejsem I²C. Gdy wybrane jest źródło zegara wewnętrznego backplane, wewnętrzny oscylator jest włączony. Wewnętrzny oscylator wygeneruje częstotliwość zegara 48Hz. Ten sygnał będzie używany przez blok sterownika segmentu wyjściowego i jest adresowany do pinu wyjściowego zegara płyty tylnej (GreenPAK pin 20).
Gdy wybrane jest zewnętrzne źródło zegara płyty montażowej, wewnętrzny oscylator jest wyłączany. Odniesieniem sterownika segmentu wyjściowego jest wejście zegara zewnętrznego panelu tylnego (GreenPAK pin 2). W tym przypadku pin wyjściowy zegara płyty montażowej może być wykorzystany jako dodatkowa linia sterowania segmentu, segment OUT15.
Na tej samej linii I²C można używać więcej niż jednego urządzenia GreenPAK. W tym celu każde urządzenie musi mieć zaprogramowany inny adres I²C. W ten sposób można zwiększyć liczbę obsługiwanych segmentów LCD. Jedno urządzenie jest skonfigurowane do generowania źródła zegara płyty tylnej, sterującej 14 segmentami, a inne są skonfigurowane do korzystania z zewnętrznego źródła zegara płyty tylnej. Każde dodatkowe urządzenie mogłoby w ten sposób napędzać więcej 15 segmentów. Do tej samej linii I²C można podłączyć do 16 urządzeń, a następnie sterować do 239 segmentów wyświetlacza LCD.
W tej instrukcji ten pomysł jest używany do sterowania 29 segmentami wyświetlacza LCD za pomocą 2 urządzeń GreenPAK. Funkcjonalność pinów urządzenia została podsumowana w Tabeli 1.
Krok 3: Zaprojektuj pobór prądu
Ważnym problemem w tym projekcie jest pobór prądu, który powinien być jak najniższy. Szacowany prąd spoczynkowy urządzenia GreenPAK wynosi 0,75 µA przy zasilaniu 3,3 V i 1,12 µA przy zasilaniu 5 V. Pobór prądu wewnętrznego oscylatora wynosi 7,6 µA i 8,68 µA odpowiednio dla zasilania 3,3 V i 5 V. Nie oczekuje się znaczącego wzrostu poboru prądu ze strat przełączania, ponieważ ta konstrukcja działa przy niskiej częstotliwości taktowania. Szacowany maksymalny prąd pobierany w tym projekcie jest niższy niż 15 µA, gdy oscylator wewnętrzny jest włączony, i 10 µA, gdy oscylator wewnętrzny jest wyłączony. Zmierzony prąd pobierany w obu sytuacjach jest pokazany w sekcji Wyniki testu.
Krok 4: Schemat urządzenia GreenPAK
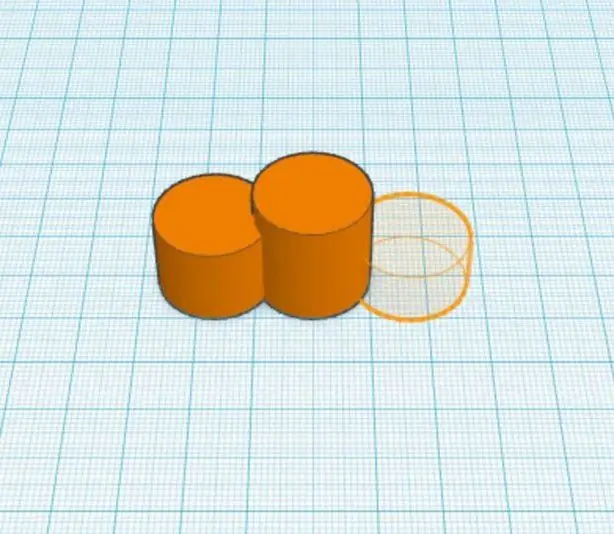
Projekt zaprojektowany w oprogramowaniu GreenPAK pokazano na rysunku 4. Schemat ten zostanie opisany przy użyciu podstawowych schematów blokowych jako odniesienia.
Krok 5: Interfejs I²C
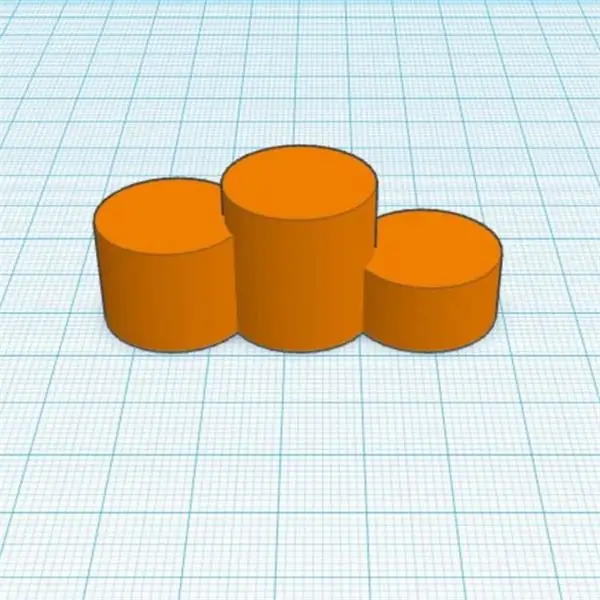
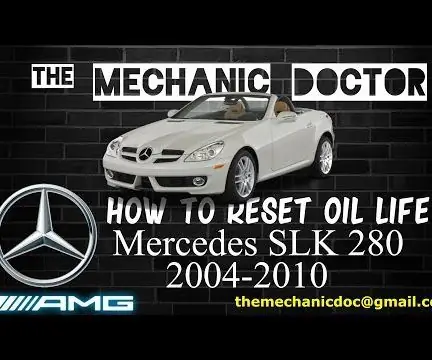
Blok interfejsu I²C jest używany jako główny blok sterujący sterowania pracą urządzenia. Bliski widok połączeń bloków i skonfigurowanych właściwości pokazano na rysunku 5.
Ten blok jest podłączony do PIN 8 i PIN 9, które są odpowiednio pinami I²C SCL i SDA. Wewnątrz urządzenia blok I²C oferuje 8 wejść wirtualnych. Początkowa wartość każdego wejścia wirtualnego jest pokazana w oknie właściwości (patrz Rysunek 5). Wejścia wirtualne od OUT0 do OUT6 są używane jako linie sterujące segmentem. Te linie sterujące odpowiadają wyjściu segmentu 1 do wyjścia segmentu 7 i są połączone ze sterownikiem wyjścia segmentu. Wirtualne wejście OUT7 służy do sterowania linią selektora źródła zegara na płycie tylnej o nazwie sieciowej BCKP_SOURCE. Ta siatka będzie używana przez inne bloki w projekcie. Kod sterujący I²C jest skonfigurowany z inną wartością dla każdego układu scalonego w projekcie.
Na wyjściu Asynchronous State Machine (ASM) dostępnych jest 8 dodatkowych linii sterujących segmentu wewnętrznego, jak pokazano na rysunku 6 powyżej. Linie wyjściowe segmentu 8 (SEG_OUT_8 w oknie właściwości) poprzez linię wyjściową segmentu 15 (SEG_OUT_15) sterowane są wyjściem ASM na stan 0. W bloku ASM nie ma zmiany stanu, jest zawsze w stanie 0. Wyjścia ASM są podłączony do sterowników wyjściowych segmentu.
Segmentowe sterowniki wyjściowe będą generować sygnał wyjściowy urządzenia.
Krok 6: Sterownik segmentu wyjściowego
Sterownik segmentu wyjściowego jest zasadniczo tabelą przeglądową (LUT) skonfigurowaną jako port logiczny XOR. Dla każdego segmentu wyjściowego musi to być port XOR podłączony do linii sterującej segmentu oraz do zegara kasety (BCKP_CLOCK). Port XOR jest odpowiedzialny za generowanie sygnału w fazie i poza fazą do segmentu wyjściowego. Gdy linia kontrolna segmentu jest na wysokim poziomie, wyjście portu XOR odwróci sygnał zegarowy płyty tylnej i wygeneruje sygnał poza fazą do pinu segmentowego. Różnica napięcia między płytą montażową LCD a segmentem LCD, w tym przypadku, ustawi segment LCD jako ciemny segment. Gdy linia sterowania segmentu jest na niskim poziomie, wyjście portu XOR będzie podążać za sygnałem zegara płyty tylnej, a następnie wygeneruje sygnał w fazie do pinu segmentu. Ponieważ w tym przypadku między płytą montażową LCD a segmentem nie występuje napięcie, segment jest przezroczysty dla światła.
Krok 7: Kontrola źródła wewnętrznego oscylatora i zegara kasety
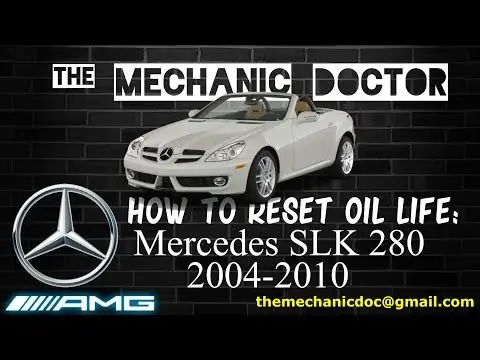
Oscylator wewnętrzny jest używany, gdy sygnał BCKP_CLOCK z interfejsu I²C jest ustawiony na wysoki poziom. Bliski widok schematu sterowania źródłem zegara pokazano na rysunku 7 powyżej.
Oscylator jest skonfigurowany jako częstotliwość RC 25 kHz, z najwyższym dzielnikiem wyjściowym dostępnym na oscylator OUT0 (8/64). Cała konfiguracja jest widoczna w oknie właściwości pokazanym na rysunku 7. W ten sposób wewnętrzny oscylator wygeneruje częstotliwość zegara 48 Hz.
Oscylator jest aktywny tylko wtedy, gdy sygnał BCKP_SOURCE jest na wysokim poziomie wraz z sygnałem POR. Ta kontrola odbywa się poprzez podłączenie tych dwóch sygnałów do portu NAND 4-L1 LUT. Wyjście NAND jest następnie połączone z wejściem pinu sterującego wyłączaniem oscylatora.
Signal BCKP_SOURCE steruje MUXem zbudowanym z 3-L10 LUT. Gdy sygnał BCKP_SOURCE jest na niskim poziomie, źródło zegara płyty tylnej pochodzi z PIN2. Gdy ten sygnał jest na wysokim poziomie, źródło zegara płyty tylnej pochodzi z wewnętrznego oscylatora.
Krok 8: Wyjście zegara płyty montażowej lub sterowanie pinami wyjściowymi segmentu 15
Pin 20 w tej konstrukcji pełni podwójną funkcję, która zależy od wybranego źródła zegara backplane. Działanie tego pinu jest sterowane za pomocą jednej 4-wejściowej LUT, jak pokazano na Rysunku 8. Przy 4-bitowej LUT możliwe jest powiązanie działania portu XOR z wyjściowym MUX. Gdy sygnał BCKP_SOURCE jest na wysokim poziomie, wyjście LUT będzie podążać za zegarem wewnętrznego oscylatora. Następnie pin 20 działa jako wyjście zegara płyty montażowej. Gdy sygnał BCKP_SOURCE jest na niskim poziomie, wyjście LUT będzie operacją XOR między SEG_OUT_15, z wyjścia ASM, a sygnałem zegara płyty tylnej. Konfiguracja 4-bitowej tablicy LUT do wykonania tej operacji jest pokazana na rysunku 8.
Krok 9: Prototyp systemu LCD

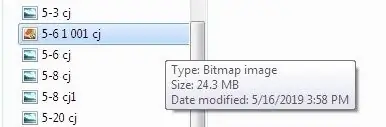
Aby zademonstrować zastosowanie rozwiązania projektowego GreenPAK, na płytce stykowej zmontowano prototyp systemu LCD. W przypadku prototypu siedmiosegmentowy, 4-cyfrowy statyczny wyświetlacz LCD jest obsługiwany przez dwa urządzenia GreenPAK na płytce DIP. Jedno urządzenie (IC1) wykorzystuje wewnętrzny oscylator do sterowania płytą montażową LCD, a drugie urządzenie (IC2) wykorzystuje ten sygnał jako odniesienie wejścia płyty montażowej. Oba układy scalone są kontrolowane przez interfejs I²C przez mikrokontroler (MCU) STM32F103C8T6 w minimalnej płytce rozwojowej.
Rysunek 9 pokazuje schemat połączeń między dwoma układami GreenPAK IC, wyświetlaczem LCD i płytą MCU. Na schemacie urządzenie GreenPAK z referencyjną U1 (IC1) napędami LCD cyfra pierwsza i druga (LCD po lewej stronie). Urządzenie GreenPAK z referencyjnymi dyskami U2 (IC2) LCD cyfra trzecia i czwarta plus segment COL (LCD prawa strona). Zasilanie obu urządzeń pochodzi z regulatora w płytce rozwojowej mikrokontrolera. Dwie zdejmowane zworki między zasilaczem a pinami VDD każdego urządzenia GreenPAK są dodawane do pomiaru prądu za pomocą multimetru.
Zdjęcie zmontowanego prototypu pokazano na rysunku 10.
Krok 10: Polecenia I²C do sterowania LCD
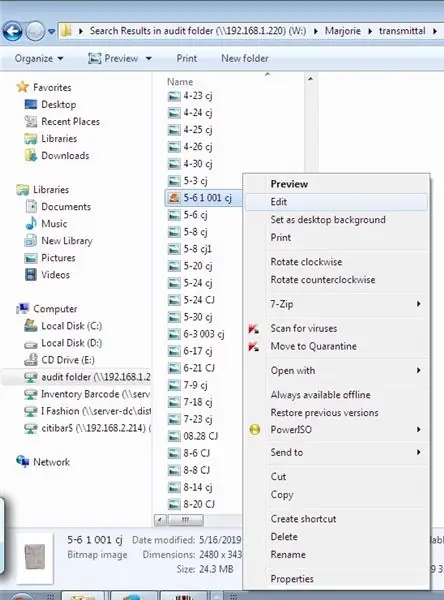

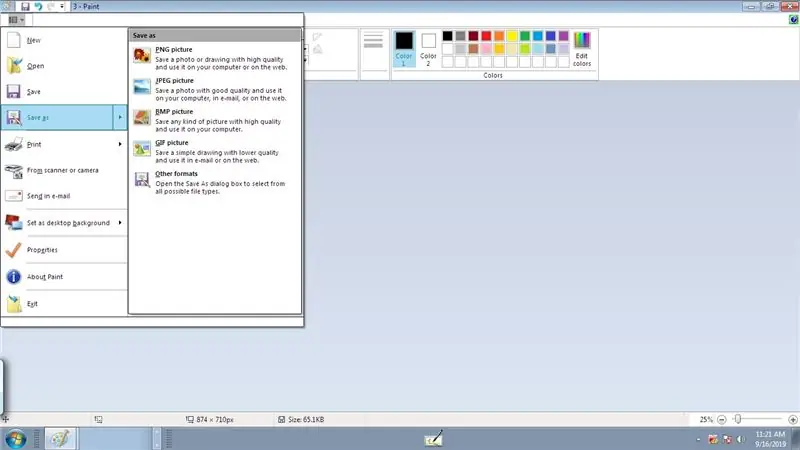
Dwa urządzenia GreenPAK na płytce prototypowej są zaprogramowane według tego samego projektu, z wyjątkiem wartości bajtu kontrolnego. Bajt kontrolny IC1 to 0 (adres I²C 0x00), natomiast bajt kontrolny I²C to 1 (adres I²C 0x10). Połączenia między segmentami wyświetlacza a sterownikami urządzeń podsumowano w powyższej tabeli.
Połączenia zostały dobrane w ten sposób, aby stworzyć bardziej przejrzysty schemat i uprościć montaż połączeń płytki stykowej.
Sterowanie wyjściem segmentu odbywa się za pomocą poleceń zapisu I²C do wejść wirtualnych I²C i rejestrów wyjściowych ASM. Jak opisano w nocie aplikacyjnej AN-1090 Simple I²C IO Controllers with SLG46531V (patrz Application Note AN-1090 Simple I²C IO Controllers with SLG46531V, Dialog Semiconductor), polecenie zapisu I²C ma następującą strukturę:
● Start;
● Bajt kontrolny (bit R/W to 0);
● adres słowny;
● Dane;
● Zatrzymaj się.
Wszystkie polecenia zapisu I²C są wykonywane na adresie Word 0xF4 (wirtualne wejścia I²C) i 0xD0 (wyjście ASM dla stanu 0). Polecenia do zapisu w IC1 i sterowania cyfrą 1 i 2 na wyświetlaczu LCD są podsumowane w Tabeli 3. W reprezentacji sekwencji poleceń, nawias otwarty „[”oznacza sygnał Start, a nawias zamykający „]” oznacza sygnał Stop.
Dwa bajty powyżej sterują segmentami LCD cyfry 1 i cyfry 2 razem. W tym przypadku podejście polega na użyciu w oprogramowaniu indywidualnej tabeli przeglądowej (LUT) dla każdej cyfry, biorąc pod uwagę segmenty w obu bajtach. Wartości bajtów z tabeli przeglądowej należy mieszać za pomocą operacji bitowej OR, a następnie wysłać do układu scalonego. Tabela 4 pokazuje wartość Bajt0 i Bajt1 dla każdej wartości liczbowej, która powinna być wpisana w każdą cyfrę wyświetlacza.
Na przykład, aby zapisać w cyfrze 1 liczbę 3, a w cyfrze 2 liczbę 4, Bajt0 to 0xBD (0x8D bitowe OR z 0xB0), a Bajt 1 to 0x33 (0x30 bitowe OR z 0x03).
Polecenia do zapisu w IC2 i sterowania cyfrą 3 i 4 są opisane w tabeli 5.
Logika kontroli cyfr 3 i 4 jest podobna do kontroli cyfr 1 i 2. Tabela 6 pokazuje LUT dla tych dwóch cyfr.
Różnica w IC2 to segment COL. Ten segment jest kontrolowany przez Byte1. Aby ustawić ten segment na ciemny, należy wykonać operację bitową OR między Byte1 a wartością 0x40.
Krok 11: Polecenia I²C dla testu LCD
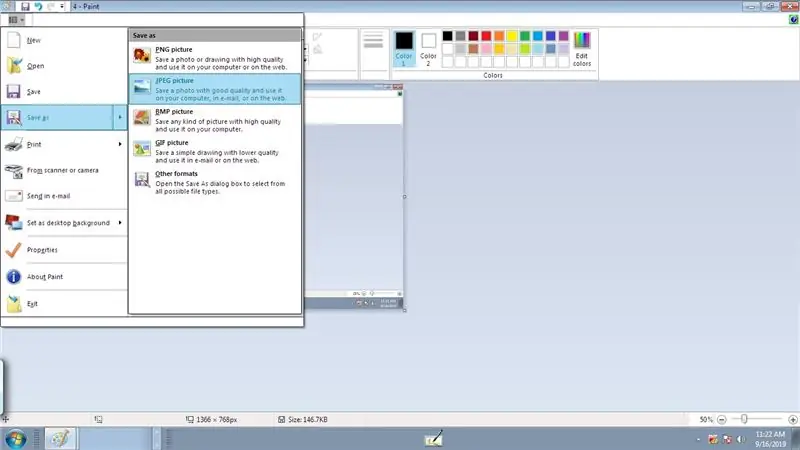
Do testu LCD opracowano oprogramowanie układowe w języku C dla płyty MCU. To oprogramowanie wyśle sekwencję poleceń do obu układów scalonych na płytce prototypowej. Kod źródłowy tego oprogramowania znajduje się w sekcji Dodatek. Całe rozwiązanie zostało opracowane przy użyciu Atollic TrueStudio dla STM32 9.0.1 IDE.
Sekwencję poleceń i odpowiednie wartości pokazane na wyświetlaczu podsumowano w Tabeli 7 powyżej.
Krok 12: Wyniki testu
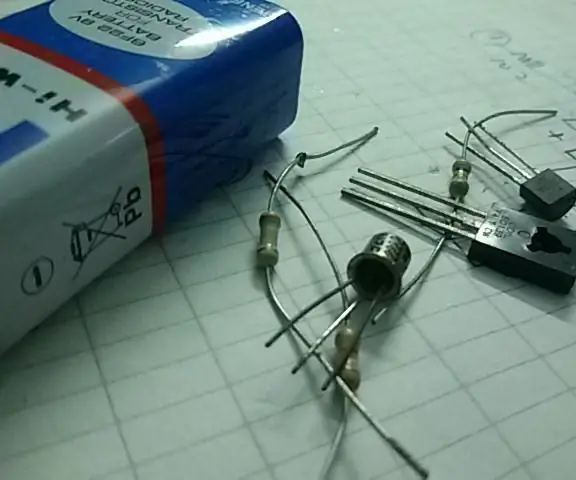
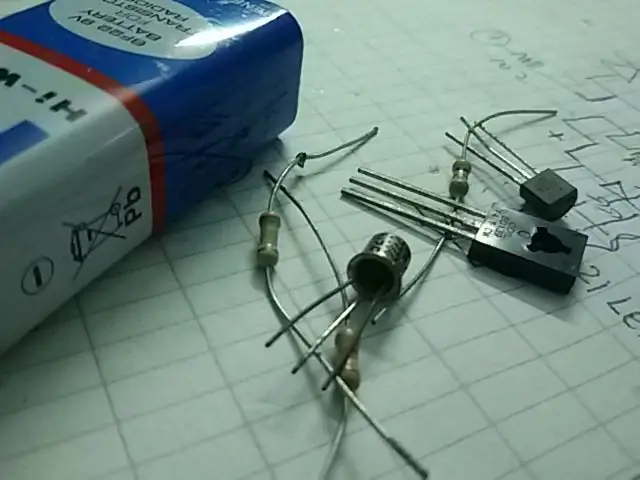
Test prototypu polega na sprawdzeniu wyświetlanych wartości po poleceniu MCU i pomiarze prądu ujścia przez każdy układ scalony podczas pracy.
Obrazy wyświetlacza LCD dla każdej wartości polecenia pokazano w Tabeli 8 powyżej.
Pobór prądu dla każdego urządzenia został zmierzony multimetrem w najniższym zakresie prądowym 200 µA. Obrazy mierzonego prądu dla każdego urządzenia podczas rozruchu i normalnej pracy przedstawiono w Tabeli 9 powyżej.
Dyskusja wniosków i wyników
Przedstawiono projekt statycznego sterownika LCD małej mocy z urządzeniem GreenPAK. Ta konstrukcja wyraźnie pokazuje jedną z największych cech urządzeń GreenPAK: ich niski prąd spoczynkowy. Ponieważ urządzenia GreenPAK są rozwiązaniem sprzętowym, możliwa jest praca w trybie niskoczęstotliwościowym, w tym przypadku 48 Hz. Rozwiązanie oparte na MCU będzie wymagało wyższej częstotliwości pracy, nawet przez okresowo krótkie okresy czasu, a następnie będzie pobierało więcej energii. A porównując urządzenie GreenPAK z CPLD (Complex Programmable Logic Device), wyraźnie widać, że zwykle CPLD ma prąd spoczynkowy wyższy niż 20 µA.
Warto zauważyć, że ten projekt można łatwo zmodyfikować, aby lepiej dopasować się do wymagań konkretnego projektu. Dobrym przykładem jest pinout kontroli segmentu. Można je łatwo zmienić, aby jednocześnie uprościć płytkę drukowaną i tworzenie oprogramowania. Jest to interesująca cecha, gdy porównamy urządzenie z gotowym układem ASIC (Application Specific Integrated Circuit). Zazwyczaj układy ASIC są projektowane tak, aby pasowały do szerokiego zakresu aplikacji, a wstępna procedura oprogramowania powinna zostać napisana, aby prawidłowo skonfigurować układ scalony przed operacją. Konfigurowalne urządzenie można zaprojektować tak, aby było gotowe do użycia po włączeniu zasilania. W ten sposób można skrócić czas tworzenia oprogramowania dla wstępnej konfiguracji IC.
Kod źródłowy aplikacji można znaleźć tutaj w Dodatku A.
Zalecana:
Jak zrobić sterownik kierunku silnika prądu stałego E-Bike: 4 kroki
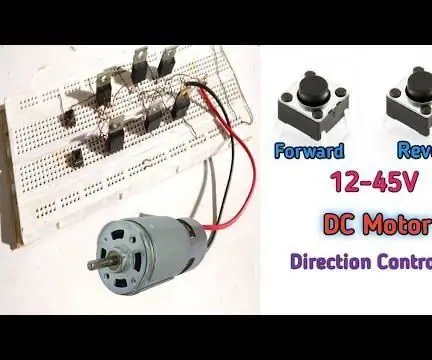
Jak zrobić sterownik kierunku silnika prądu stałego E-Bike: jest to sterownik kierunku silnika prądu stałego dla twojego roweru elektrycznego. W tym obwodzie użyłem mostka N-Channel MOSFET H i zatrzasku SR. Kontrola obwodu mostka H Kierunek przepływu prądu. Obwód zatrzasku SR zapewnia pozytywny sygnał na obwodzie mostka H. Komp
Jak zrobić sterownik wysokoprądowy dla silnika krokowego: 5 kroków
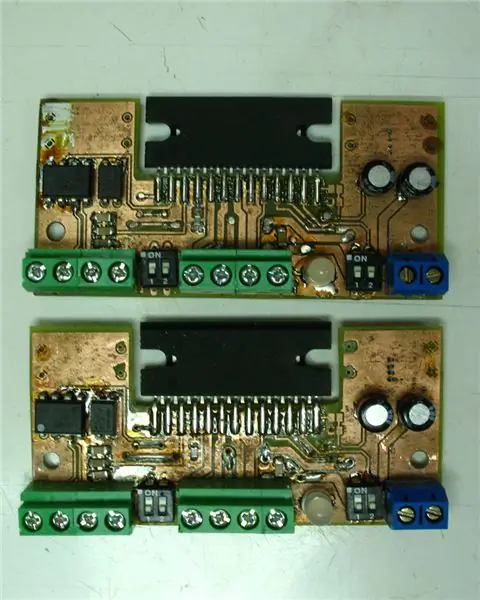
Jak zrobić sterownik wysokoprądowy dla silnika krokowego: tutaj zobaczymy, jak zrobić sterownik silnika krokowego za pomocą kontrolera Toshiba TB6560AHQ. Jest to w pełni funkcjonalny kontroler, który potrzebuje tylko 2 zmiennych jako danych wejściowych i wykonuje całą pracę. Ponieważ potrzebowałem dwóch z nich, oba zrobiłem za pomocą
Statyczny system oświetlenia awaryjnego oparty na pomiarze energii elektrycznej: 8 kroków
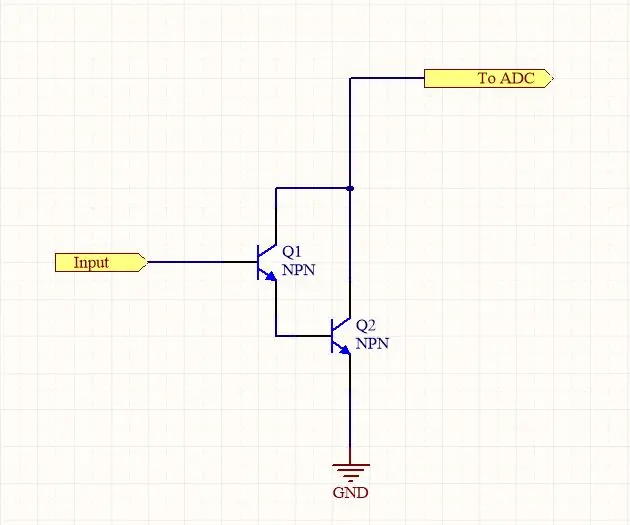
Statyczny system oświetlenia awaryjnego oparty na pomiarach energii elektrycznej: Czy kiedykolwiek myślałeś o stworzeniu systemu oświetlenia awaryjnego, gdy główne zasilanie zostanie wyłączone? A ponieważ masz nawet odrobinę wiedzy w zakresie elektroniki, powinieneś wiedzieć, że możesz łatwo sprawdzić dostępność zasilania sieciowego, po prostu mierząc
Jak zrobić prosty sterownik Flyback: 4 kroki (ze zdjęciami)
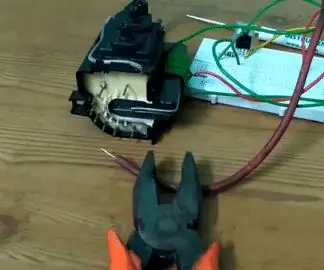
Jak zrobić prosty sterownik Flyback: Transformator Flyback (FBT) jest specjalnie zaprojektowanym transformatorem, który jest używany w wyświetlaczach CRT. Jest w stanie generować ponad 50 kV. W tym instruktażu poinstruuję, jak zrobić prosty sterownik flyback za pomocą mosfetu mocy. Sprawdź moje sieci
Jak zrobić kalendarz dziadków & Notatnik (nawet jeśli nie wiesz, jak to zrobić): 8 kroków (ze zdjęciami)
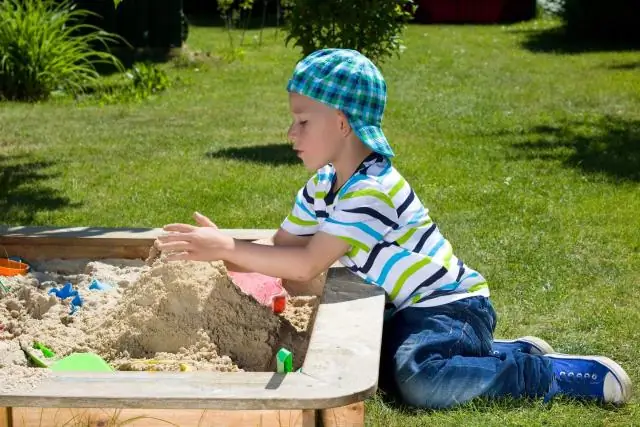
Jak zrobić kalendarz dziadków & Notatnik (nawet jeśli nie wiesz jak to zrobić): To bardzo ekonomiczny (i bardzo ceniony!) prezent świąteczny dla dziadków. W tym roku zrobiłem 5 kalendarzy za mniej niż 7 USD każdy.Materiały:12 wspaniałych zdjęć Twojego dziecka, dzieci, siostrzenic, siostrzeńców, psów, kotów lub innych krewnych 12 różnych elementów