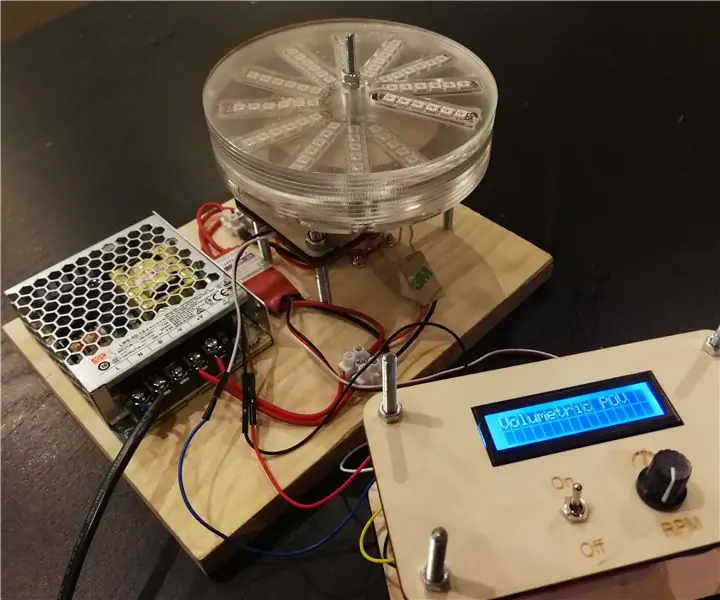
Spisu treści:
2025 Autor: John Day | [email protected]. Ostatnio zmodyfikowany: 2025-01-23 15:03
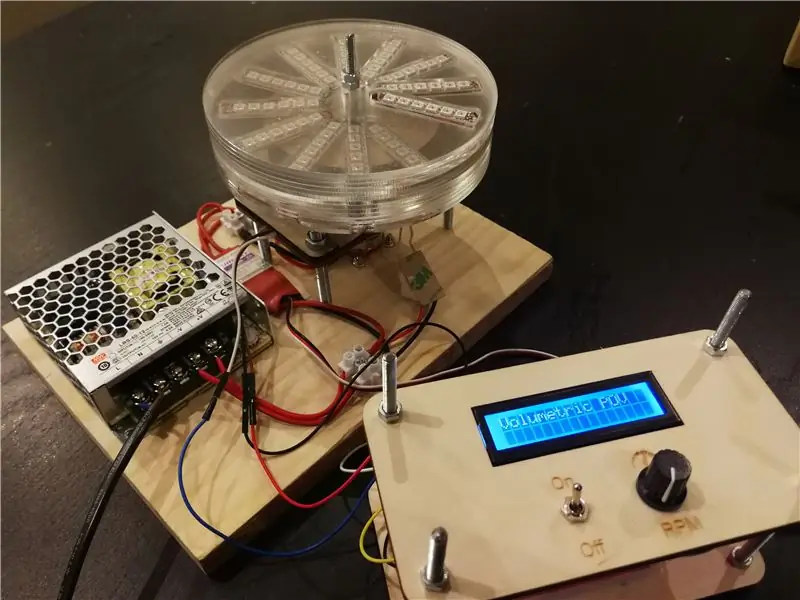
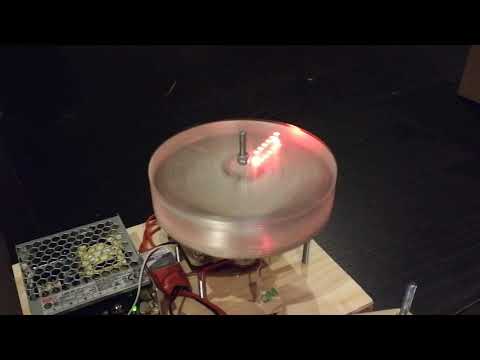

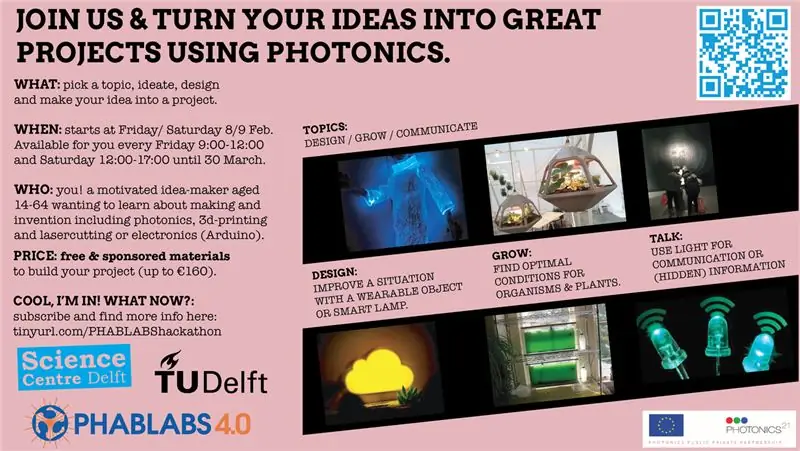
Kilka tygodni temu otrzymałem w ostatniej chwili zaproszenie do udziału w PhabLabs Hackathon w Science Center Delft w Holandii. Dla entuzjastycznego hobbysty, takiego jak ja, który normalnie może poświęcić tylko ograniczoną ilość czasu na majsterkowanie, uznałem to za doskonałą okazję do zaplanowania poświęcenia czasu na przekształcenie jednego z moich wielu pomysłów, w ramach Hackathonu: Fotonika, w rzeczywisty projekt. A dzięki wspaniałym urządzeniom w Makerspace w Science Center Delft odrzucenie tego zaproszenia było po prostu niemożliwe.
Jednym z pomysłów, które miałem już od jakiegoś czasu w związku z fotoniką, było to, że chciałem zrobić coś z Persistence of Vision (POV). Istnieje już mnóstwo przykładów dostępnych online, jak zbudować podstawowy wyświetlacz POV przy użyciu podstawowych komponentów: mikrokontrolera, starego wentylatora/dysku twardego/silnika i jednego ciągu diod LED podłączonych prostopadle do osi obracającego się urządzenia. Przy stosunkowo prostej konfiguracji możesz już stworzyć imponujący dwuwymiarowy obraz, np.:
Inna odmiana wyświetlaczy POV łączy ciąg diod równoległych do osi obracającego się urządzenia. Spowoduje to trójwymiarowy cylindryczny wyświetlacz POV, np.:
Zamiast łączyć ciąg diod równolegle do osi obracającego się urządzenia, można również łukować ciąg diod. Spowoduje to wyświetlenie sferycznego (kulisty) POV, np.: https://www.instructables.com/id/POV-Globe-24bit-… Następnym poziomem jest zbudowanie kilku warstw diod led w celu stworzenia wolumetrycznego wyświetlacza 3D. Oto kilka przykładów takich wolumetrycznych wyświetlaczy POV 3D, które wykorzystałem jako inspirację do tego konkretnego projektu:
- https://www.instructables.com/id/PropHelix-3D-POV-…
- https://github.com/mbjd/3DPOV
- https://hackaday.io/project/159306-volumetric-pov-…
- https://hackaday.com/2014/04/21/volumen-the-most-a…
Ponieważ twórcy powyższych przykładów dostarczyli bardzo przydatnych informacji, sensowne było zremiksowanie części ich projektów. Ale ponieważ Hackathon ma być wyzwaniem, postanowiłem również zbudować inny rodzaj wolumetrycznego wyświetlacza 3D POV. Niektórzy z nich używali wirników i dużej ilości gorącego kleju, aby elementy nie latały dookoła. Inni stworzyli niestandardowe płytki PCB do swojego projektu. Po zapoznaniu się z kilkoma innymi projektami 3D POV zobaczyłem miejsce na trochę „innowacji” lub postawiłem sobie kilka wyzwań:
- Bez wcześniejszego doświadczenia w tworzeniu niestandardowych płytek PCB i ze względu na ograniczenia czasowe Hackathonu, wybieram bardziej podstawowe podejście do prototypu. Ale zamiast tworzyć rzeczywiste wirniki, byłem ciekaw, jak taki wolumetryczny wyświetlacz 3D POV będzie wyglądał przy użyciu cylindra zbudowanego z warstw akrylowego plastiku.
- Brak użycia lub minimalne użycie gorącego kleju, aby urządzenie było mniej niebezpieczne
Krok 1: Użyte materiały i narzędzia
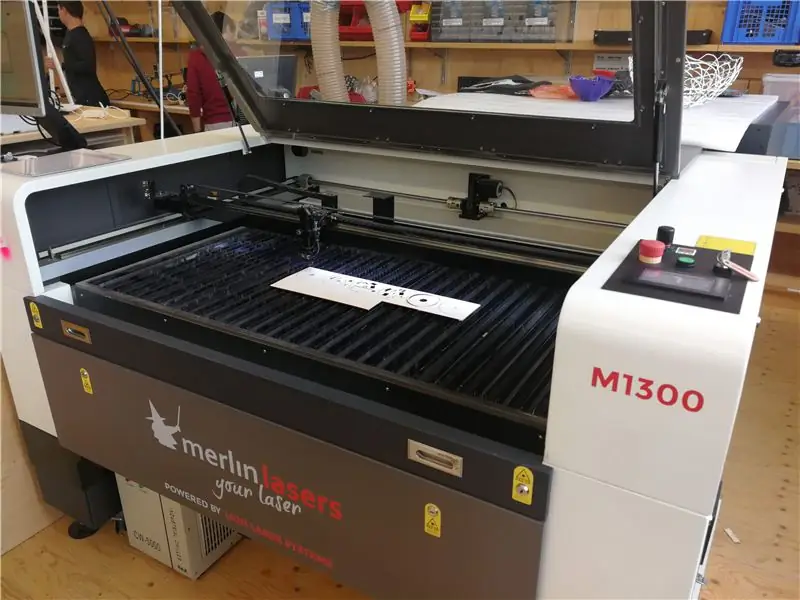
Dla sterownika silnika
- Arduino Pro Micro 5V/16Mhz
- Mała deska do krojenia chleba
- 3144 Czujnik przełącznika Halla
- Magnes o średnicy: 1cm, wysokości: 3mm
- Przełącznik dwustabilny - MTS-102
- Potencjometr 10K
- Dupontowe przewody połączeniowe
- 16 x nakrętki M5
- Moduł wyświetlacza LCD z niebieskim podświetleniem (HD44780 16×2 znaków)
- Rezystor 10K - rezystor podciągający dla czujnika efektu Halla
- Rezystor 220Ohm-do kontrolowania kontrastu ekranu LCD
- Średnica pręta gwintowanego: 5mm
- Sklejka, Grubość: 3mm
Do podstawy platformy
- Kawałek złomu drewna (250 x 180 x 18 mm)
- Mean Well - 12V 4.2A - Zasilacz impulsowy LRS-50-12
- Kabel z wtyczką zasilania 220 V
- Przetwornik bezprzewodowy DC-DC - 5V 2A (nadajnik)
- Turnigy D2836/8 1100KV bezszczotkowy silnik Outrunner
- Turnigy Plush 30-amperowy regulator prędkości W/BEC
- Złącza zaciskowe
- 12 x nakrętek M6 do zabezpieczenia platformy za pomocą prętów gwintowanych o średnicy 6mm.
- 3 śruby M2 (długość 18 mm) do mocowania przykręcanego adaptera do silnika bezszczotkowego
- 4 x nakrętki i śruby M3 do mocowania silnika bezszczotkowego do kawałka drewna
- Średnica pręta gwintowanego: 6 mm (4 x długość 70 mm)
- Średnica pręta gwintowanego: 4 mm (1 x długość 80 mm)
- Sklejka, Grubość: 3mm
Do obudowy obrotowej
- Przetwornik bezprzewodowy DC-DC - 5V 2A (odbiornik)
- Drukowany w 3D adapter przykręcany (filament PLA, biały)
- Malutkie 3,6
- IC 74AHCT125 Poczwórny konwerter/przerzutnik poziomów logicznych (3 V do 5 V)
- Rezystor 10K - rezystor podciągający dla czujnika efektu Halla
- Kondensator 1000uF 16V
- Średnica pręta gwintowanego 4mm
- Magnes o średnicy: 1cm, wysokości: 3mm
- Sklejka, Grubość: 3mm
- Sklejka, Grubość: 2mm
- Arkusz akrylowy, grubość: 2 mm
- Średnica pręta stalowego: 2mm
- Nakrętki i śruby
- Taśma ledowa o długości 0,5 metra APA102C 144 diody / metr
Narzędzia użyte
- Wycinarka laserowa Merlin M1300 - cięcie laserowe sklejki i arkusza akrylowego
- Ultimaker 2+ do drukowania 3D adaptera przykręcanego
- Stacja lutownicza i lutownica
- Wiertarka stołowa
- Wkrętaki
- szczypce
- Młotek
- Suwmiarka
- Brzeszczot
- Klucze
- Rurki termokurczliwe
Używane oprogramowanie
- Fuzja 360
- Ultimaker Cura
- Arduino IDE i Teensyduino (zawierające Teensy Loader)
Krok 2: Sterownik silnika do regulacji prędkości obrotowej
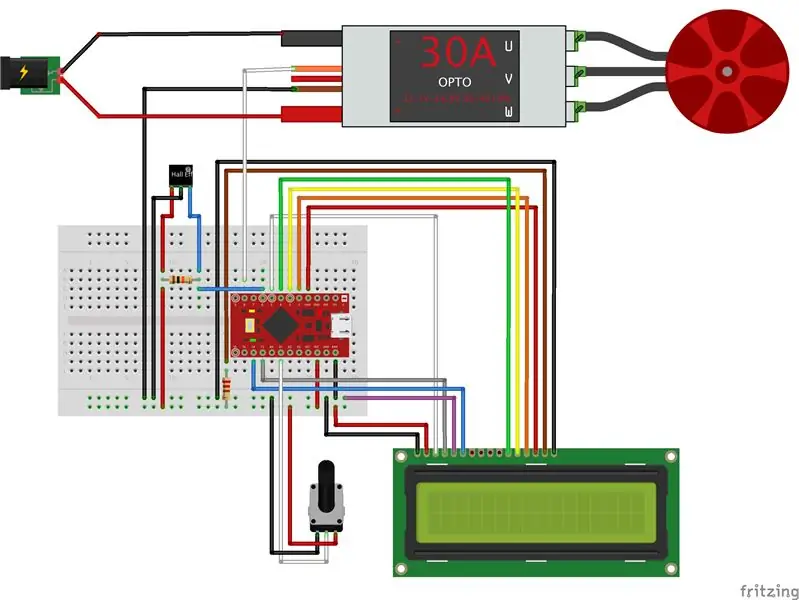
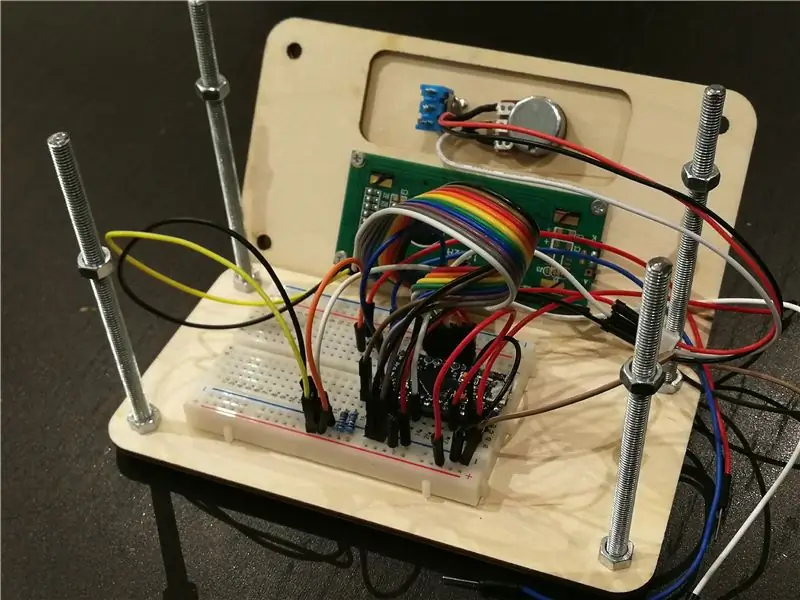
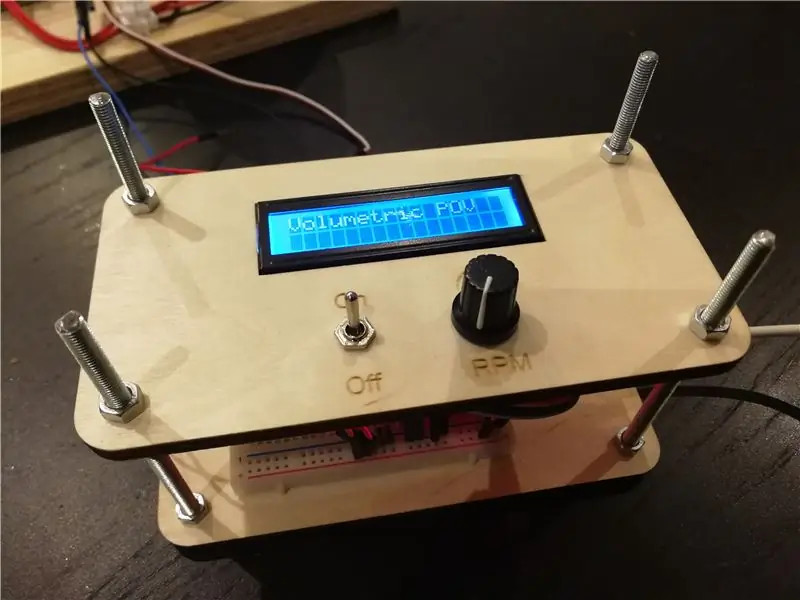
Sterownik silnika wysyła sygnał do elektronicznego sterownika prędkości Turnigy (ESC), który kontroluje liczbę obrotów zapewnianych przez silnik bezszczotkowy.
Dodatkowo chciałem mieć możliwość wyświetlania rzeczywistych obrotów na minutę cylindra POV. Dlatego zdecydowałem się dołączyć czujnik efektu Halla i wyświetlacz LCD 16x2 do sterownika silnika.
W załączonym pliku zip (MotorControl_Board.zip) znajdziesz trzy pliki dxf, które pozwolą Ci wyciąć laserowo jedną płytę bazową i dwie płyty górne dla jednostki sterującej silnika. Proszę używać sklejki o grubości 3mm. Dwie górne płyty można umieścić jedna na drugiej, co umożliwi przykręcenie wyświetlacza LCD 16x2.
Dwa otwory w górnej płycie są przeznaczone na jeden przełącznik on/off i jeden potencjometr do sterowania prędkością silnika bezszczotkowego (nie podłączyłem jeszcze przełącznika on/off). Aby skonstruować moduł sterownika silnika, należy pociąć pręt gwintowany o średnicy 5 mm na 4 kawałki o żądanej wysokości. Za pomocą 8 nakrętek M5 możesz najpierw przymocować podstawę. Następnie przymocowałem małą płytkę stykową do płyty bazowej za pomocą dwustronnej naklejki samoprzylepnej dołączonej do płytki stykowej. Załączony schemat pokazuje, jak należy połączyć komponenty, aby działały z kodem źródłowym (MotorControl.ino) dołączonym do tego kroku. Użyłem rezystora podciągającego 10K dla czujnika Halla. Rezystor 220 Ohm działał wystarczająco dobrze, aby tekst był widoczny na ekranie LCD.
Upewnij się, że izolujesz piny czujnika efektu Halla za pomocą rurek termokurczliwych, tak jak pokazano na zdjęciach. Prawidłowe działanie czujnika Halla będzie zależeć od magnesu, który zostanie umieszczony w obrotowej obudowie w kroku 3.
Po zakończeniu okablowania można zabezpieczyć 2 górne płyty za pomocą wyświetlacza LCD, przełącznika i potencjometru za pomocą ponownie 8 nakrętek M5, jak pokazano na zdjęciach.
W zależności od modelu używanego silnika może być konieczne dostosowanie następującego wiersza kodu w pliku MotorControl.ino:
throttle = map(averagePotValue, 0, 1020, 710, 900);
Ten wiersz kodu (wiersz 176) odwzorowuje pozycję potencjometru 10K na sygnał dla ESC. ESC przyjmuje wartości od 700 do 2000. A ponieważ silnik, którego użyłem do tego projektu, zaczął obracać się w okolicach 823, ograniczyłem obroty silnika, ograniczając maksymalną wartość do 900.
Krok 3: Budowanie platformy do bezprzewodowej transmisji mocy
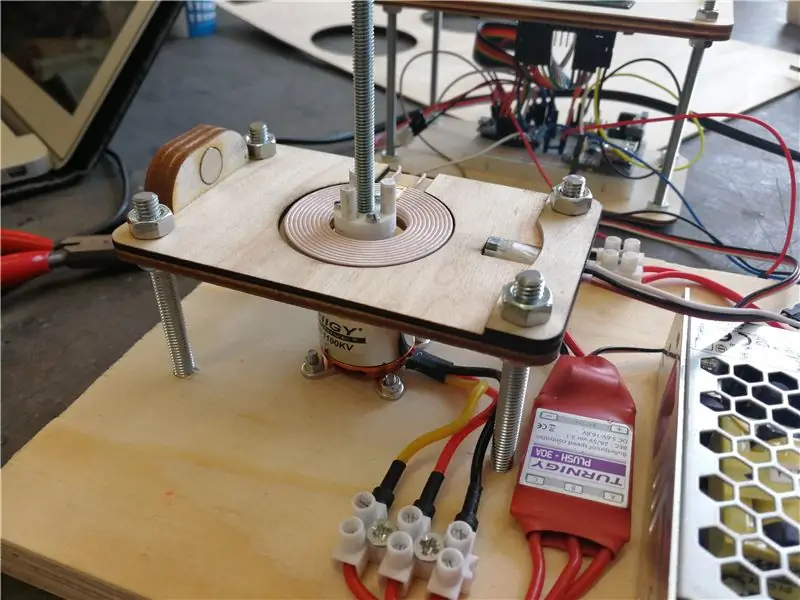
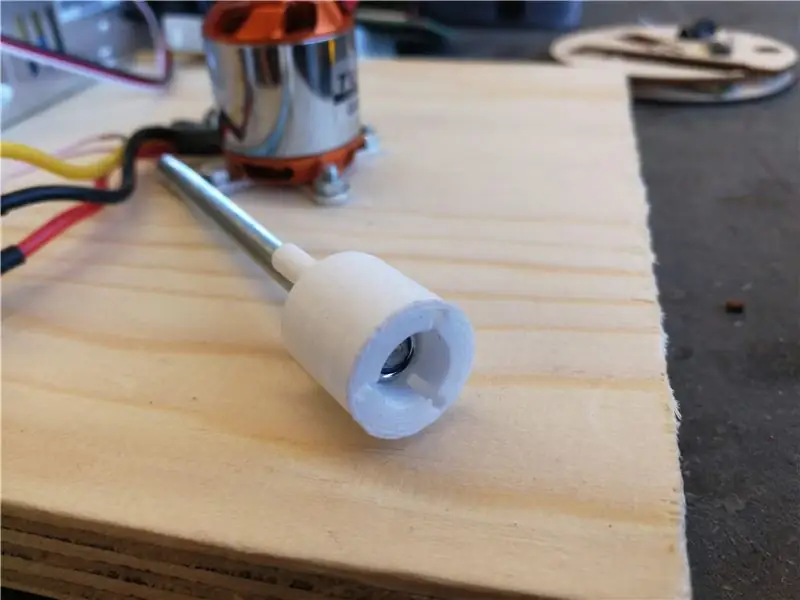
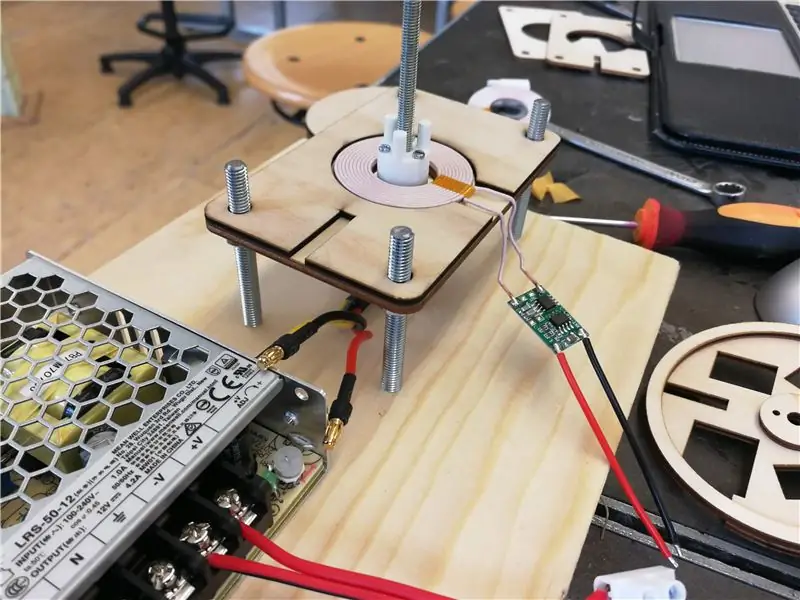
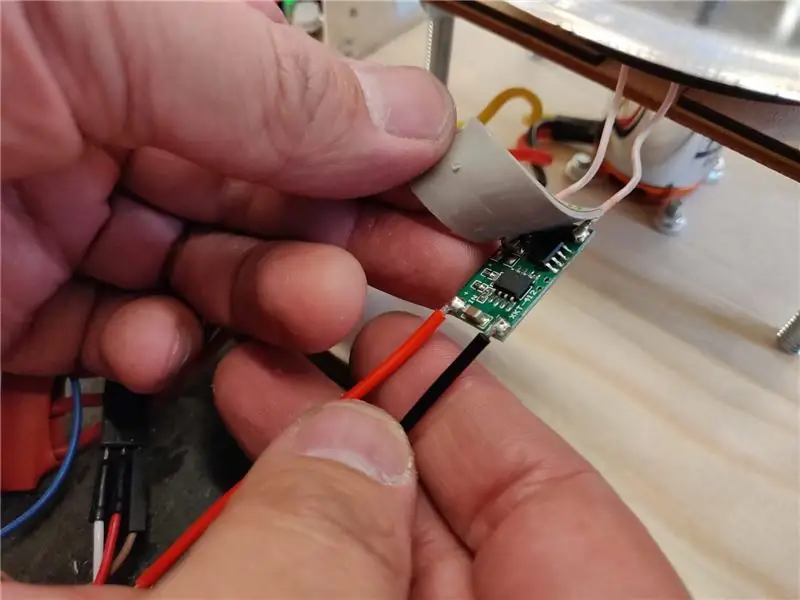
W dzisiejszych czasach istnieją zasadniczo dwa sposoby zasilania urządzeń, które muszą się obracać: pierścienie ślizgowe lub przesyłanie mocy bezprzewodowo za pomocą cewek indukcyjnych. Ponieważ wysokiej jakości pierścienie ślizgowe, które mogą obsługiwać wysokie obroty, są zwykle bardzo drogie i bardziej podatne na zużycie, zdecydowałem się na opcję bezprzewodową za pomocą bezprzewodowego konwertera DC-DC 5 V. Zgodnie ze specyfikacją powinno być możliwe przesyłanie do 2 A przy użyciu takiego konwertera.
Konwerter Wireless DC-DC składa się z dwóch elementów, nadajnika i odbiornika. Należy pamiętać, że płytka PCB podłączona do cewki indukcyjnej nadawczej jest mniejsza niż ta odbiorcza.
Sama platforma jest zbudowana z kawałka drewna odpadowego (250 x 180 x 18 mm).
Na platformie przykręciłem zasilacz Mean Well 12V. Wyjście 12 V jest podłączone do ESC (patrz schematy w kroku 1) i PCB części nadawczej bezprzewodowego konwertera DC-DC.
W załączonym pliku Platform_Files.zip znajdziesz pliki dxf do laserowego wycięcia platformy ze sklejki o grubości 3mm:
- Platform_001.dxf i Platform_002.dxf: Musisz umieścić je na sobie. Stworzy to zagłębiony obszar dla indukcyjnej cewki nadawczej.
- Magnet_Holder.dxf: Laserowo wycina ten projekt trzy razy. Jeden z trzech razy dołącz krąg. W pozostałych dwóch cięciach laserowych: usuń okrąg z wycięcia. Po wycięciu sklej ze sobą trzy kawałki tworząc uchwyt na magnes (średnica 10mm, grubość: 3mm). Użyłem kleju superglue do przyklejenia magnesu w uchwycie Magnet. Upewnij się, że przyklejasz właściwą stronę magnesu do uchwytu, ponieważ czujnik Halla będzie działał tylko z jedną stroną magnesu.
- Platform_Sensor_Cover.dxf: Ten element pomoże ci utrzymać czujnik Halla podłączony do jednostki sterującej silnika na miejscu, jak pokazano na pierwszym obrazku.
- Platform_Drill_Template.dxf: Użyłem tego kawałka jako szablonu do wiercenia otworów w kawałku złomu. Cztery większe otwory o średnicy 6 mm służą do mocowania prętów gwintowanych o średnicy 6 mm do podtrzymywania platformy. 4 mniejsze otwory służą do mocowania silnika bezszczotkowego do kawałka drewna. Największy otwór w środku był wymagany dla osi wystającej z silnika bezszczotkowego. Ponieważ śruby do silnika i pręty gwintowane do platformy muszą być zamocowane na spodzie platformy, konieczne jest powiększenie tych otworów o kilka mm głębokości, aby umożliwić dopasowanie nakrętek.
Niestety w przypadku tego projektu wał silnika bezszczotkowego wystawał z „niewłaściwej” strony. Ale udało mi się odwrócić wał za pomocą poniższej instrukcji, którą znalazłem na Youtube:
Po zabezpieczeniu silnika i prętów wsporczych platformę można zbudować z elementów platformy wyciętych laserowo. Samą platformę można zabezpieczyć za pomocą 8 nakrętek M6. Uchwyt magnetyczny można przykleić do platformy na granicy, jak pokazano na pierwszym zdjęciu.
Załączony plik "Bolt-On Adapter.stl" można wydrukować za pomocą drukarki 3D. Ten adapter jest niezbędny do zamocowania pręta gwintowanego o średnicy 4 mm do silnika bezszczotkowego za pomocą 3 śrub M2 o długości 18 mm.
Krok 4: Obrotowa obudowa
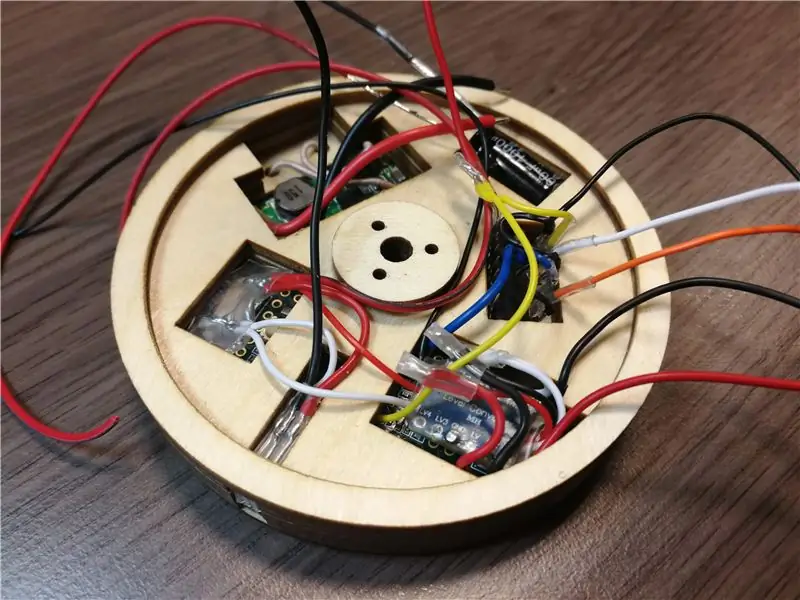
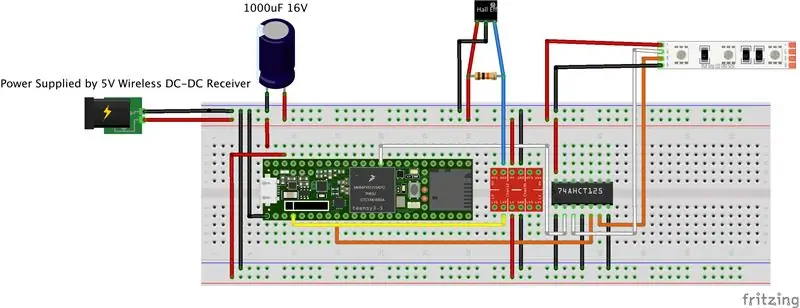
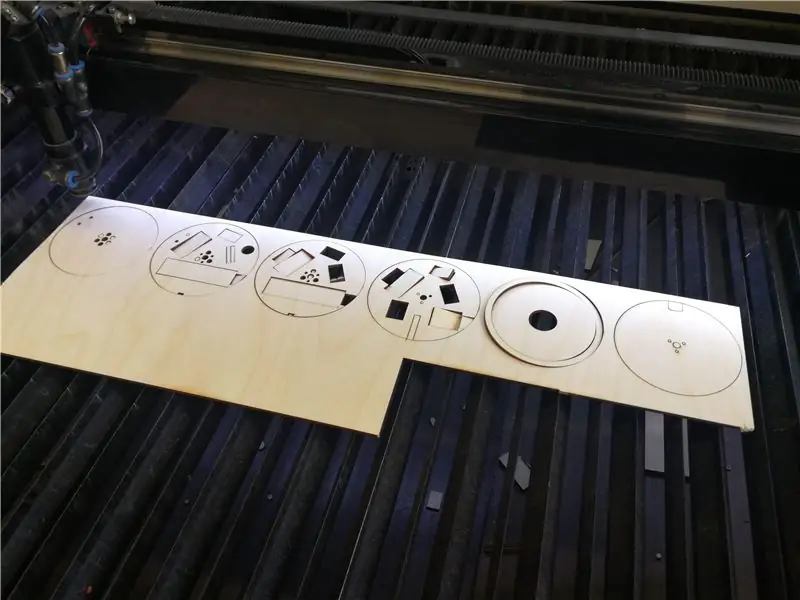
Załączony plik Base_Case_Files.zip zawiera pliki dxf do laserowego wycinania 6 warstw w celu skonstruowania obudowy dla elementów sterujących taśmą led APA102C.
Warstwy 1-3 projektu Case są przeznaczone do sklejenia. Ale upewnij się, że magnes (średnica 10mm, wysokość: 3mm) został umieszczony w okrągłym wycięciu w warstwie 2 przed sklejeniem trzech warstw. Upewnij się również, że magnes jest przyklejony odpowiednim biegunem do spodu, ponieważ czujnik efektu Halla umieszczony na platformie zbudowanej w kroku 3 będzie reagował tylko na jedną stronę magnesu.
Konstrukcja obudowy zawiera przegródki na elementy wymienione na załączonych schematach połączeń. IC 74AHCT125 jest wymagany do konwersji sygnału 3,3 V z Teensy na sygnał 5 V wymagany dla taśmy ledowej APA102. Warstwy 4 i 5 można również skleić. Górna warstwa 6 może być ułożona na innych warstwach. Wszystkie warstwy pozostaną we właściwej pozycji za pomocą 3 stalowych prętów o średnicy 2mm. Istnieją trzy małe otwory na pręty stalowe o średnicy 2 mm otaczające większy otwór na obracający się pręt gwintowany 4 mm przymocowany do silnika bezszczotkowego. Po przylutowaniu wszystkich komponentów zgodnie ze schematem, całą obudowę można umieścić na przykręcanym adapterze wydrukowanym w kroku 3. Upewnij się, że wszelkie otwarte przewody są odpowiednio zaizolowane za pomocą rurek termokurczliwych. Należy pamiętać, że prawidłowe działanie czujnika Halla w tych krokach zależy od magnesu umieszczonego w uchwycie magnetycznym opisanym w kroku 3.
Załączony kod dowodu koncepcji 3D_POV_POC.ino zaświeci niektóre diody na czerwono. Szkic powoduje wyświetlenie kwadratu, gdy walec zacznie się obracać. Ale zanim zacznie się obracanie, diody wymagane do symulacji kwadratu są domyślnie włączone. Jest to pomocne przy testowaniu prawidłowego działania diod w następnym kroku.
Krok 5: Cylinder obrotowy z paskami Led
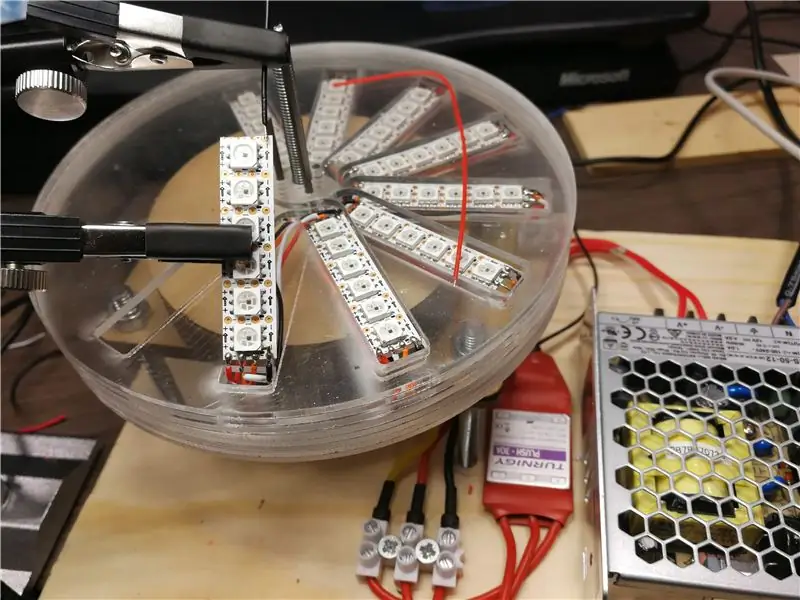
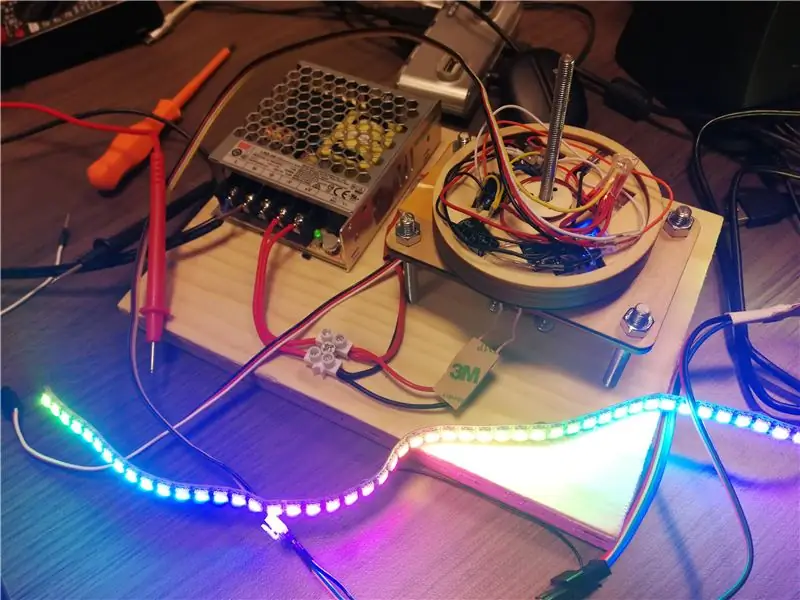
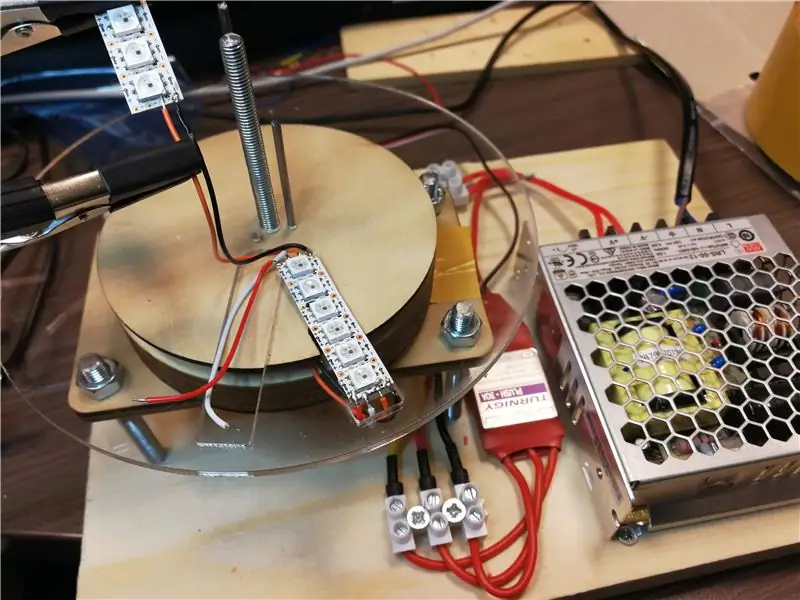
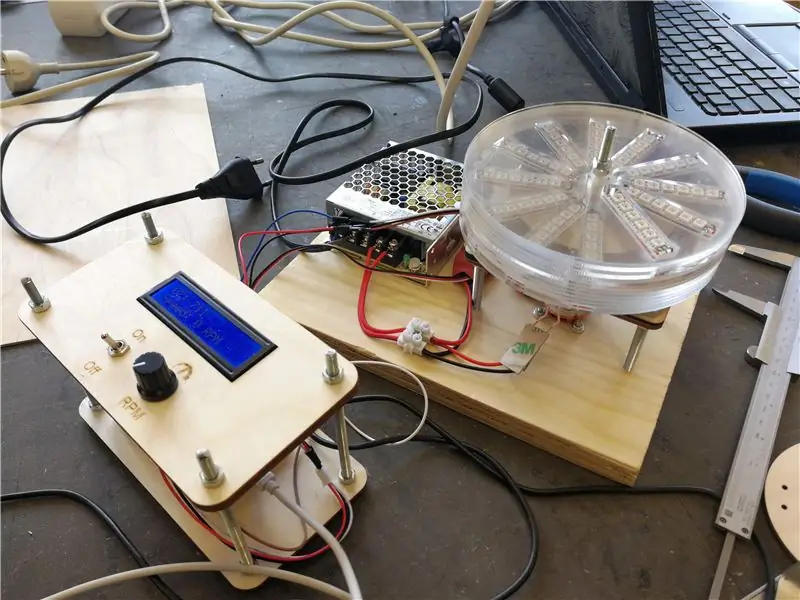
Załączony plik Rotor_Cylinder_Files.zip zawiera pliki dxf do cięcia arkusza akrylowego o grubości 2 mm. Powstałe w ten sposób 14 dysków jest niezbędnych do zbudowania przezroczystego cylindra dla tego projektu POV. Dyski muszą być ułożone jeden na drugim. Konstrukcja cylindrycznych dysków umożliwia lutowanie 12 taśm ledowych jako jednego długiego paska ledowego. Zaczynając od pierwszego krążka należy przykleić do krążka mały pasek led zawierający 6 ledów za pomocą naklejek samoprzylepnych na pasku ledowym. Najpierw przylutuj przewody do taśmy led przed przymocowaniem taśm led do dysku za pomocą naklejek samoprzylepnych. W przeciwnym razie ryzykujesz, że lutownica stopi akrylowy dysk.
Gdy krążek #13 zostanie nałożony na przezroczysty cylinder, stalowy pręt 2mm używany do utrzymywania wszystkich warstw we właściwych pozycjach może być teraz również przycięty na odpowiednią długość, wyrównany do górnej części krążka #13 cylindra. Dysk nr 14 może być następnie użyty do utrzymania stalowych prętów 2 mm na miejscu za pomocą dwóch nakrętek M4.
Ze względu na czas potrzebny do zbudowania całego urządzenia, nie byłem w stanie zaprogramować bardziej stabilnych wizualnie, interesujących wyświetlaczy 3D na czas hackathonu. Jest to również powód, dla którego dostarczony kod do sterowania diodami LED jest nadal bardzo podstawowy, aby potwierdzić koncepcję, pokazując na razie tylko czerwony kwadrat w 3 wymiarach.
Krok 6: Wyciągnięte wnioski
Malutkie 3,6
- Zamówiłem Teensy 3.5 do tego projektu, ale dostawca przez pomyłkę wysłał mi Teensy 3.6. Ponieważ chciałem ukończyć projekt w czasie hackathonu, postanowiłem ruszyć z Teensy 3.6. Powodem, dla którego chciałem użyć Teensy 3.5, były porty, które są odporne na 5 V. Tak nie jest w przypadku Teensy 3.6. Z tego też powodu musiałem wprowadzić do konfiguracji dwukierunkowy konwerter logiczny. W przypadku Teensy 3.5 nie byłoby to wymagane.
- Problem z narastaniem mocy: Po włączeniu urządzenia następuje wzrost mocy za pośrednictwem bezprzewodowego modułu ładowania DC-DC w celu zasilania Teensy 3.6. Niestety, przyspieszenie jest zbyt wolne, aby Teensy 3.6 mógł się poprawnie uruchomić. Jako obejście muszę obecnie zasilić Teensy 3.6 przez złącze micro USB, a następnie podłączyć zasilacz 12 V do bezprzewodowego nadajnika DC-DC. Gdy bezprzewodowy odbiornik DC-DC również zasila Teensy, mogę odłączyć kabel USB. Ludzie podzielili się swoim hackiem z MIC803 w związku z problemem powolnego zwiększania mocy tutaj:
Moduł ekranu LCD
Nieregularne zachowanie przy zasilaniu zewnętrznym. Ekran działa poprawnie, gdy jest zasilany przez USB. Ale kiedy zasilam ekran LCD przez płytkę stykową za pomocą 5V dostarczanego przez BEC lub niezależnego zasilacza, tekst zaczyna się kodować po kilku sekundach od zmiany tekstu. Nadal muszę zbadać przyczynę tego problemu
Mechaniczny
Aby przetestować mój sterownik silnika w celu zmierzenia rzeczywistych obrotów, pozwoliłem silnikowi się obracać ze śrubą na adapterze, śrubą i obudową podstawy przymocowaną do silnika. Podczas jednego z pierwszych próbnych przebiegów śruby łączące uchwyt silnika z silnikiem odkręcają się pod wpływem drgań. Na szczęście zauważyłem ten problem na czas, dzięki czemu uniknięto potencjalnej katastrofy. Rozwiązałem ten problem, dokręcając śruby nieco mocniej do silnika, a także użyłem kilku kropli Loctite, aby jeszcze mocniej zabezpieczyć śruby
Oprogramowanie
Podczas eksportowania szkiców Fusion 360 jako plików DXF do wycinarki laserowej linie pomocnicze są eksportowane jako zwykłe linie
Krok 7: Potencjalne ulepszenia
Co bym zrobił inaczej w oparciu o doświadczenie, które zdobyłem przy tym projekcie:
- Używanie paska ledowego zawierającego co najmniej 7 diod led zamiast 6 diod led na warstwę, aby uzyskać ładniejsze wizualizacje tekstowe
- Kup inny silnik bezszczotkowy, w którym wał wystaje już po właściwej (dolnej) stronie silnika. (np.: https://hobbyking.com/de_de/ntm-prop-drive-28-36-1000kv-400w.html) Zaoszczędzi ci to kłopotów z cięciem wału lub przesuwaniem wału na właściwą stronę, tak jak ja musiałem zrobić teraz.
- Poświęć więcej czasu na wyważanie urządzenia, aby zminimalizować wibracje, mechaniczne lub modelując je w Fusion 360.
Myślałem też o kilku potencjalnych ulepszeniach, którymi mógłbym się przyjrzeć, jeśli czas pozwoli:
- Rzeczywiste wykorzystanie funkcji karty SD w Teensy do tworzenia dłuższych animacji
- Zwiększ gęstość obrazowania za pomocą mniejszych diod LED (APA102(C) 2020). Kiedy kilka tygodni temu zaczynałem ten projekt, paski led zawierające te małe diody (2x2 mm) nie były łatwo dostępne na rynku. Można je kupić jako osobne komponenty SMD, ale rozważyłbym tę opcję tylko wtedy, gdy chcesz wlutować te komponenty na niestandardowej płytce drukowanej.
- Przesyłaj obrazy 3D bezprzewodowo do urządzenia (Wifi lub Bluetooth). Powinno to również umożliwić zaprogramowanie urządzenia do wizualizacji dźwięku/muzyki.
- Konwertuj animacje Blendera do formatu pliku, który może być używany z urządzeniem
- Umieść wszystkie paski led na płycie podstawy i skup światło na warstwach akrylu. Na każdej innej warstwie można wygrawerować małe obszary, aby odbijały światło, gdy pominięto je w diodach. Światło powinno być skierowane na grawerowane obszary. Powinno to być możliwe dzięki stworzeniu tunelu prowadzącego światło lub użyciu soczewek na diodach led do skupienia światła.
- Poprawa stabilności wyświetlacza wolumetrycznego 3D i regulacja prędkości obrotowej poprzez oddzielenie obrotowej podstawy od silnika bezszczotkowego za pomocą kół zębatych i paska rozrządu.
Krok 8: Wykrzycz
Szczególne podziękowania składam następującym osobom:
- Mojej fantastycznej żonie i córkom za wsparcie i zrozumienie.
- Teun Verkerk za zaproszenie mnie na Hackathon
- Nabi Kambiz, Nuriddin Kadouri i Aidan Wyber za wsparcie, pomoc i wskazówki w całym Hackatonie
- Luuk Meints, artysta i współuczestnik tego Hackatonu, który był tak miły, że dał mi osobisty 1-godzinny kurs wprowadzający do Fusion 360, który pozwolił mi wymodelować wszystkie części, których potrzebowałem do tego projektu.
Zalecana:
DIY przezroczysty panel boczny z monitora z recyklingu!: 8 kroków (ze zdjęciami)
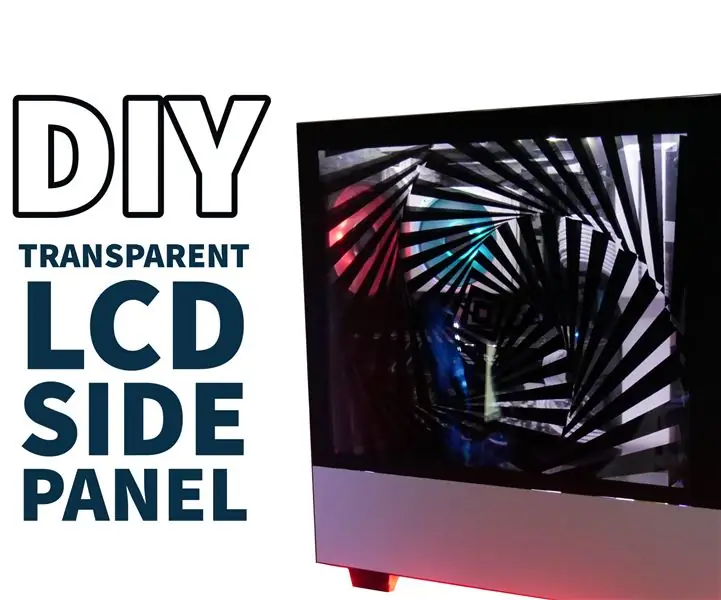
DIY przezroczysty panel boczny z przetworzonego monitora!: Widziałem naprawdę fajne wideo obudowy komputera o nazwie „Snowblind”, która miała przezroczysty ekran LCD jako panel boczny. Byłem zdumiony, jak było fajnie. Jedynym problemem było to, że było naprawdę drogo. Dlatego spróbowałem zrobić własną! W tym ja
Przezroczysty smartfon: 4 kroki (ze zdjęciami)
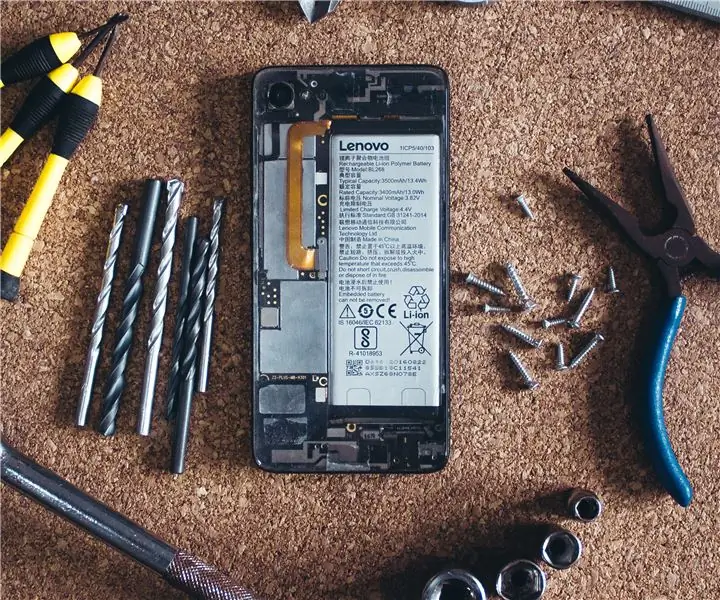
Transparentny smartfon: Zapisz się na mój kurs „Elektronika w pigułce” tutaj: https://www.udemy.com/electronics-in-a-nutshell/?… Zajrzyj również na mój kanał na YouTube, aby uzyskać więcej projektów i samouczków z elektroniki : https://www.youtube.com/channel/UCelOORs7UioZ4TZF…A
Płyty holograficzne - fotonika Challenger Hackathon PhabLabs: 6 kroków
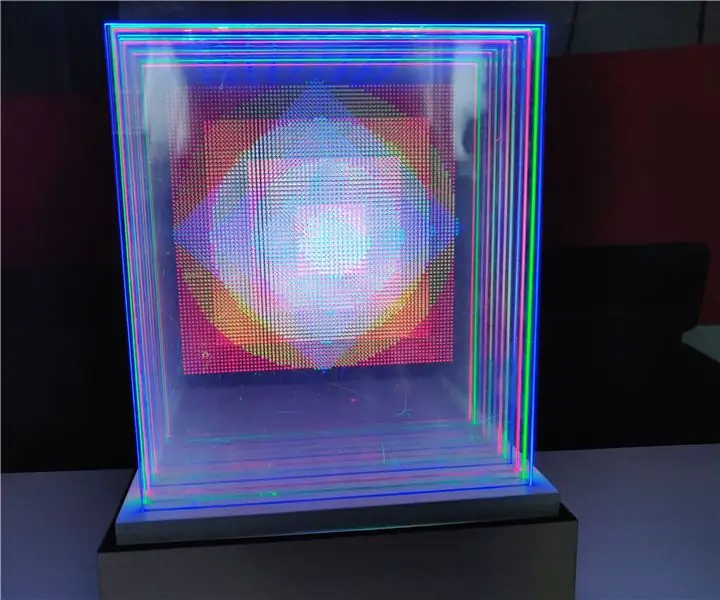
Płyty holograficzne - Photonics Challenger Hackathon PhabLabs: Na początku tego roku zostałem poproszony o udział w PhabLabs Photonics Hackathon w Science Center Delft w Holandii. Tutaj mają świetne miejsce do pracy z wieloma maszynami, które można wykorzystać do stworzenia czegoś, co normalnie
Spraw, aby silnik prądu stałego był przezroczysty: 4 kroki (ze zdjęciami)
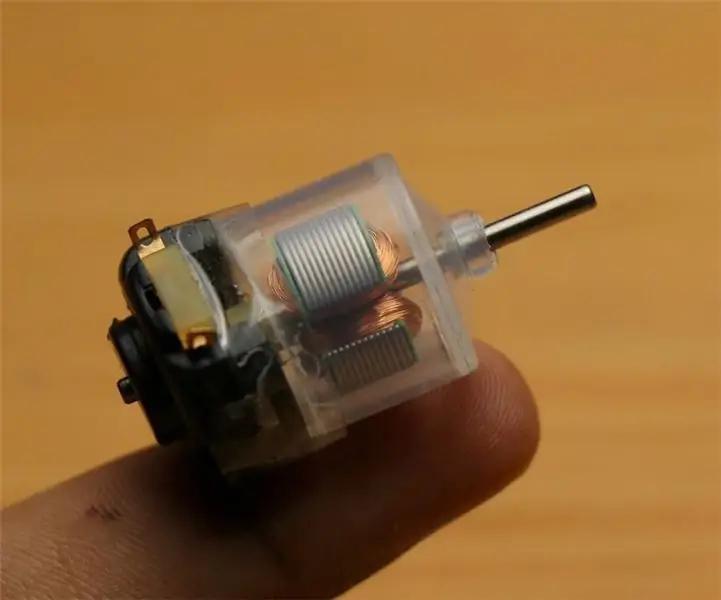
Spraw, aby silnik prądu stałego był przezroczysty: witajcie przyjaciele w tej instrukcji, pokażę wam, jak w bardzo prostych krokach zmodyfikować silnik prądu stałego na przezroczysty silnik prądu stałego, a jedną specjalną rzeczą są materiały potrzebne do tego, aby był dostępny w twoim domu :) Jest to idealny projekt na Science Fair t
Zrób wyświetlacz wolumetryczny: 7 kroków
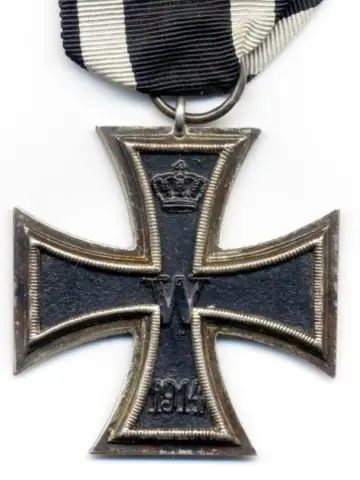
Zrób wyświetlacz wolumetryczny: BEZPŁATNY wyświetlacz wolumetryczny 3D ze skrawków leżących w warsztacie. To moja pierwsza instrukcja, więc proszę o wybaczenie. Wyświetlacz ma bardzo niską rozdzielczość, 4 x 4 x czas. Obrazy wyglądają lepiej, gdy stoisz z dala od ekran trochę.Dołączyłem