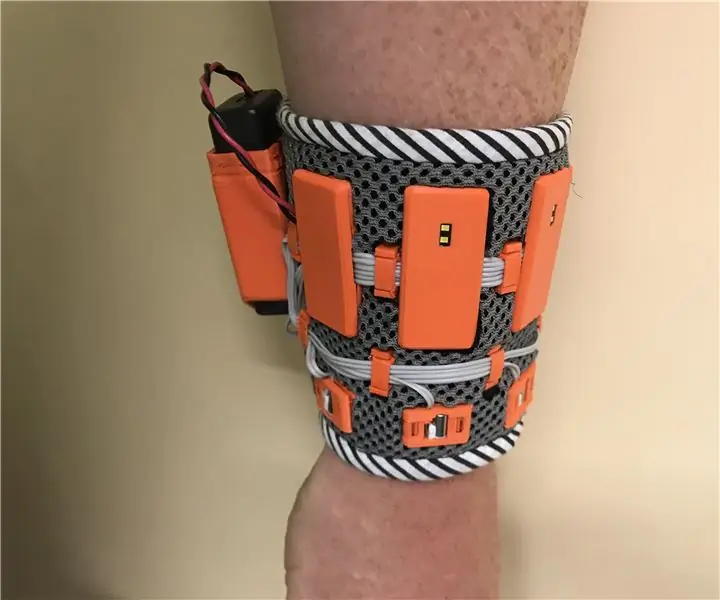
Spisu treści:
2025 Autor: John Day | [email protected]. Ostatnio zmodyfikowany: 2025-01-23 15:03
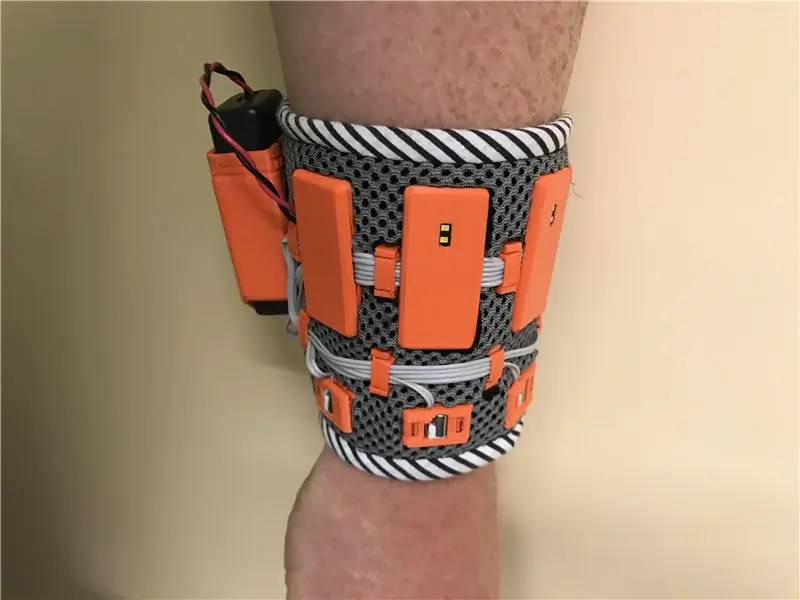
Szybki i beznadziejny system Sideway Warning jako boczny pomysł Personal Photonics z Media Computing Group Aachen, finansowany przez niemieckie Ministerstwo Edukacji i Nauki. Ilekroć pojawi się coś cichszego, czego nie możesz usłyszeć (z powodu wady słuchu lub po prostu dlatego, że samochody elektryczne są znacznie cichsze niż stare), wibracja na ramieniu powinna dać ci wskazówkę, że warto się przyjrzeć Strona. 5 Silniki wibracyjne (właściwie tylko trzy są używane (napędzane przez ULN2803), pozostałe są zapasowe, jeśli coś pójdzie nie tak) są używane w połączeniu z trzema czujnikami odległości VL53L1X. Są one sterowane za pomocą Wattuino Pro Mini (3, 3V), zasilanego baterią z podwójnym pakietem baterii AAA. Obudowy drukowane w 3D zatrzaskują wszystko na opasce.
Ze względu na światło słoneczne i ruchy ramion system nie działał tak dobrze w prawdziwym życiu, ale przynajmniej fajnie było go wypróbować, nauczyliśmy się łączyć kilka czujników czasu lotu jednocześnie (dzięki Lukasowi Ossmannowi za kodowanie) i ponownie go używać ładna opaska na nadgarstek na coś fajnego (dzięki Sophy Stönner jako projektantce).
Krok 1:
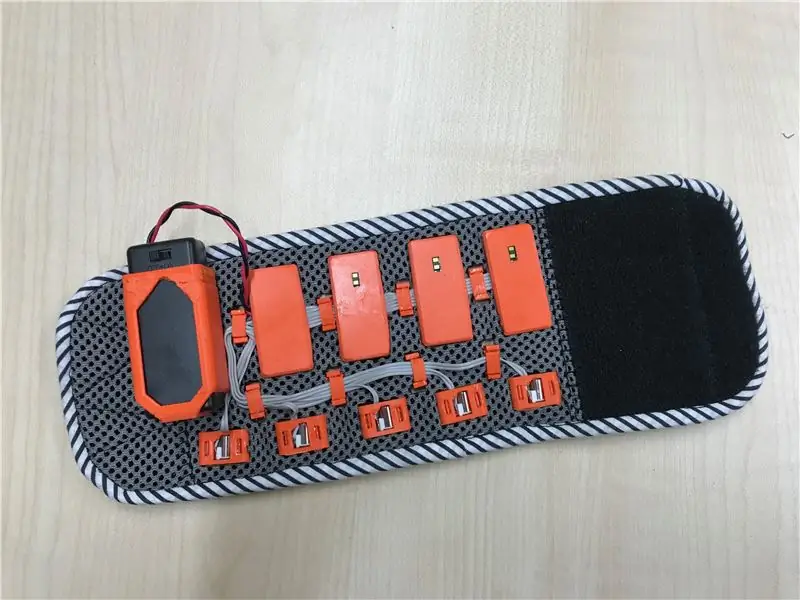
Najpierw wydrukuj części w 3D w polu OpenScad. Względnie na początku można znaleźć - częściowo zakomentowane - części. Musisz wydrukować 3 razy sensorHolderTop i holderBottom oraz jeden raz controllerHolderTop i -Bottom. Następnie wydrukuj jeden raz uchwyt baterii (który może wymagać modyfikacji dla używanego zestawu baterii). Dodatkowe klipsy do kabli i silników wibracyjnych pochodzą z naszego zestawu narzędzi HaptiVision, pliki projektowe 3D można znaleźć tutaj. Przynajmniej obudowa silnika może być dostosowana w zależności od wielkości silnika wibracyjnego, ale istnieje również ogólnie łatwa do dostosowania wersja.
Po wydrukowaniu uszyj własną lub użyj istniejącej opaski, w której oprócz akumulatora, który zostanie wszyty, zrobisz otwory na uchwyty.
Krok 2: Okablowanie
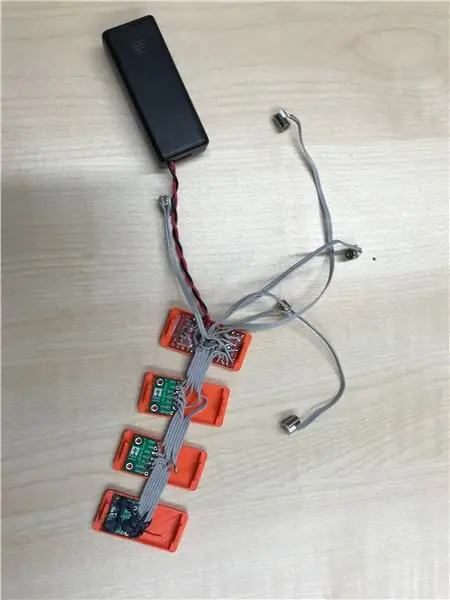
Trochę pracy, ale naprawdę prosto do przodu: najpierw frezuje się małą płytkę drukowaną dla ULN, która jest zasadniczo przylutowana z tyłu kontrolera. Pakiet baterii jest podłączony do VDD i Gnd płyty kontrolera, a także do każdego czujnika. Następnie wszystkie czujniki i płytka kontrolera są połączone równolegle na magistrali I2C. Jeden przewód każdego silnika przechodzi do pinów 3, 6 i 10 przez ULN z tyłu, drugi do GND, podczas gdy XSHUT każdego czujnika przechodzi do A0, A1, A2 w celu wyboru czujnika.
Krok 3: Prześlij kod i wypróbuj
Na koniec można wgrać kod i przetestować system. Istnieje kilka opcji korzystania z czujnika, można przełączać się między różnymi trybami odległości, a także czasem pomiaru (rodzaj czasu ekspozycji). Do sprzężenia zwrotnego drgań mot stosuje się górny i dolny termometr, a także system filtrowania hałasu. b
Każdy czujnik jest sprawdzany jeden po drugim za pomocą pinu XSHUT do ich włączania i wyłączania, następnie sygnał jest filtrowany, a silniki wibracyjne są sterowane odpowiednio do odległości z PWM.
Zalecana:
Pierwsze kroki z IDE STM32f767zi Cube i prześlij własny szkic: 3 kroki

Rozpoczęcie pracy z IDE STM32f767zi i przesłanie własnego szkicu: KUP (kliknij test, aby kupić/odwiedzić stronę internetową) OPROGRAMOWANIE STM32F767Z WSPIERANE· IDE STM32CUBE· KEIL MDK ARM µVISION· EWARM IAR EMBEDDED WORKBENCH· Dostępne różne oprogramowanie ARDUINO służy do programowania mikrokontrolerów STM
Pierwsze kroki z płytą La COOL: 4 kroki (ze zdjęciami)
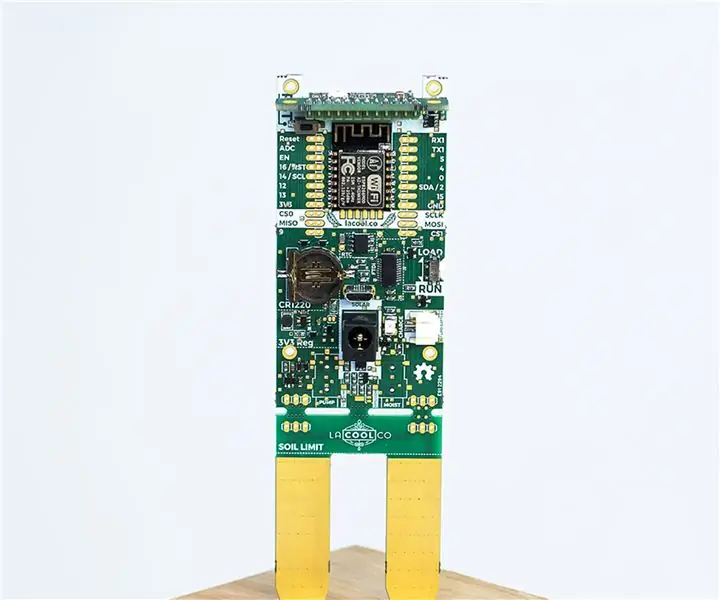
Pierwsze kroki z płytą La COOL: wprowadzenie”Kiedy wpadliśmy na pomysł na płytkę La COOL, wyobraziłem sobie połączenie Arduino z Wi-Fi i modułową agronomiczną stacją pogodową. Do pracy autonomicznej musiał zużywać bardzo mało energii i chciałem móc sterować
Systemy ostrzegania o powodzi - poziomy wody + przewodnik monitorowania czujników IoT: 6 kroków
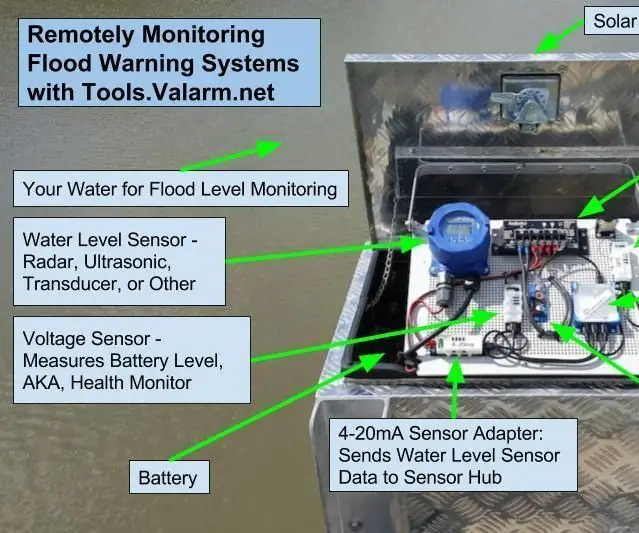
Systemy ostrzegania przed powodzią - poziomy wody + przewodnik po monitorowaniu czujników IoT: Czy musisz monitorować poziom wody? W tym samouczku dowiesz się, jak tworzyć systemy monitorowania poziomu wody. Te urządzenia Industrial IoT są wdrażane jako systemy ostrzegania przed powodzią w USA. Aby zapewnić bezpieczeństwo Tobie i Twojej społeczności, Smart Cities musi
Pierwsze kroki z Arduino: Co musisz wiedzieć: 4 kroki (ze zdjęciami)
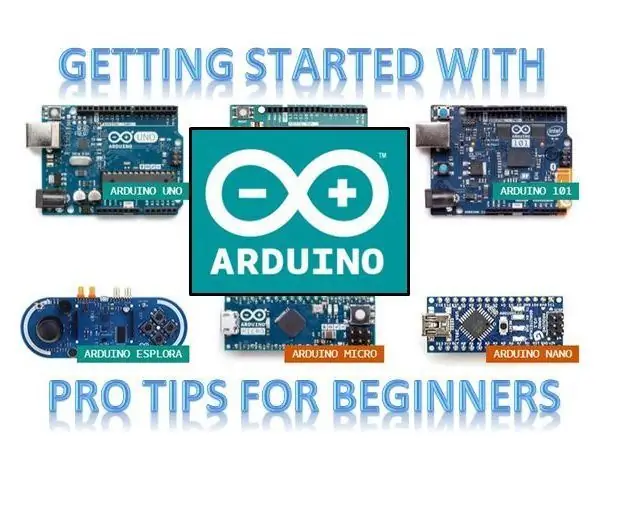
Pierwsze kroki z Arduino: Co musisz wiedzieć: Pracuję z Arduino i elektroniką od wielu lat i wciąż się uczę. W tym stale rozwijającym się świecie mikrokontrolerów łatwo się zgubić i krążyć wokół siebie, próbując znaleźć informacje. W tej instrukcji
Monitorowanie temperatury pomieszczenia kontrolowane przez Raspberry Pi z wyjściem obrazu Gnuplot i możliwością ostrzegania e-mailem: 7 kroków
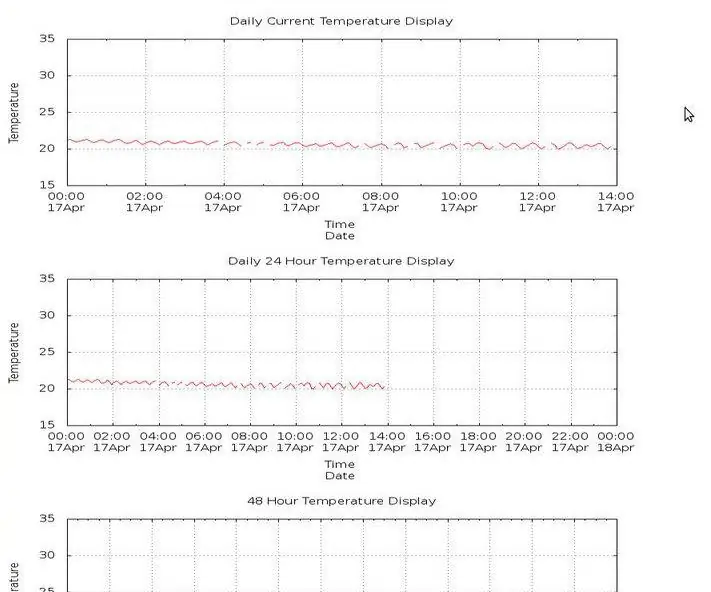
Monitorowanie temperatury w pomieszczeniu kontrolowane przez Raspberry Pi z wyjściem obrazu Gnuplot i możliwością ostrzegania e-mailem: Tam, gdzie pracuję, jest bardzo ważne pomieszczenie, w którym znajduje się wiele komputerów. Temperatura otoczenia w tym pomieszczeniu musi być bardzo niska, aby zoptymalizować wydajność tych systemów. Poproszono mnie o opracowanie systemu monitorowania, który ma możliwość