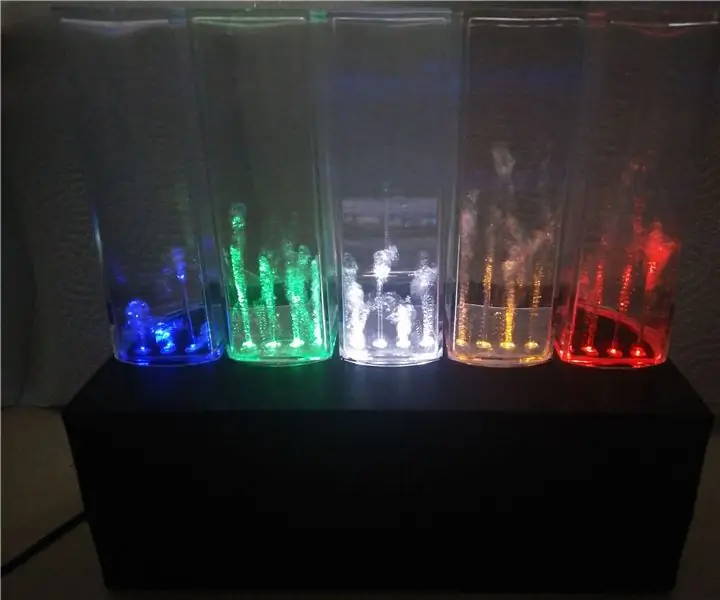
Spisu treści:
- Krok 1: Części
- Krok 2: Zdemontuj adapter Bluetooth
- Krok 3: Konfigurowanie układu scalonego na płycie perforowanej
- Krok 4: Dodawanie mosfetów
- Krok 5: Umieszczenie diod i rezystorów 5W
- Krok 6: Dodanie gniazda panelu, Bluetooth i potencjometrów
- Krok 7: Przygotowanie głośników wodnych
- Krok 8: Dodawanie przewodów Arduino
- Krok 9: Rezystory silnika i potencjometry
- Krok 10: Drukowanie 3D
- Krok 11: Montaż
- Krok 12: Kodeks
- Krok 13: Produkt końcowy
2025 Autor: John Day | [email protected]. Ostatnio zmodyfikowany: 2025-01-23 15:03
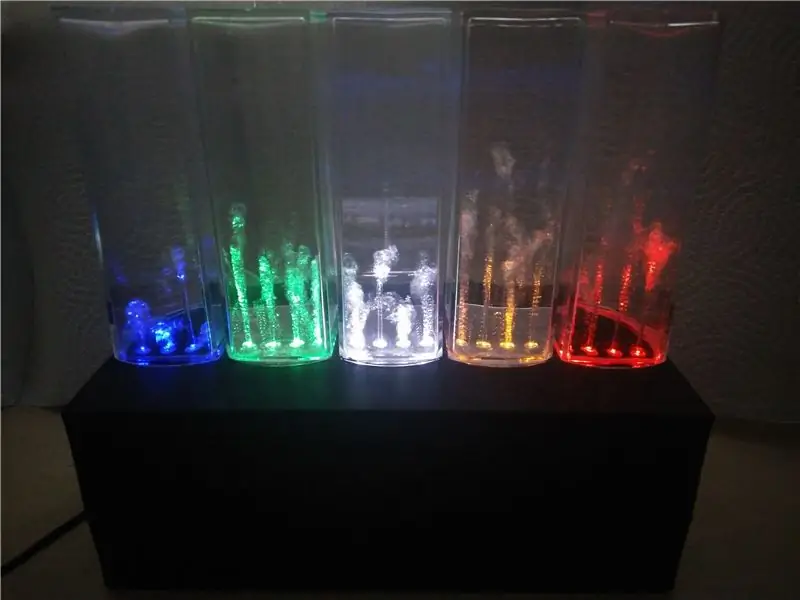
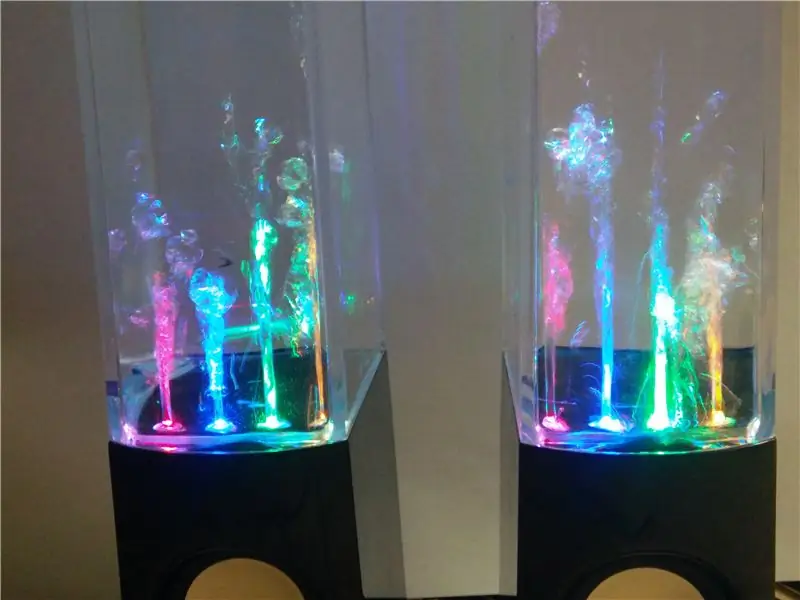
W moim pierwszym Instructable zamierzam przejść przez kroki potrzebne do stworzenia głośników wodnych, które działają jako korektor.
Głośniki wodne ze sklepu są świetne do oglądania, ale czułem, że mogą zrobić więcej. tyle lat temu zmodyfikowałem zestaw, aby pokazać częstotliwość odtwarzania muzyki. Używałem wtedy Color Organ Triple Deluxe II, w połączeniu z zestawem fotokomórek, potencjometrów i tranzystorów udało mi się uruchomić zestaw 3 głośników.
Kilka lat temu słyszałem o IC MSGEQ7, który ma możliwość rozdzielenia dźwięku na 7 wartości danych do odczytu przez arduino. W tym projekcie wykorzystuję arduino mega 2560, ponieważ ma wymaganą liczbę pinów PWM do napędzania pięciu wież ciśnień.
Ten projekt wykorzystuje umiejętności lutowania na płycie perforowanej, module Bluetooth, arduino i gotowych głośnikach wodnych. W całym projekcie zauważyłem kilka rzeczy, które powinienem był zrobić inaczej, więc na pewno je wskażę.
Zacznijmy
Krok 1: Części
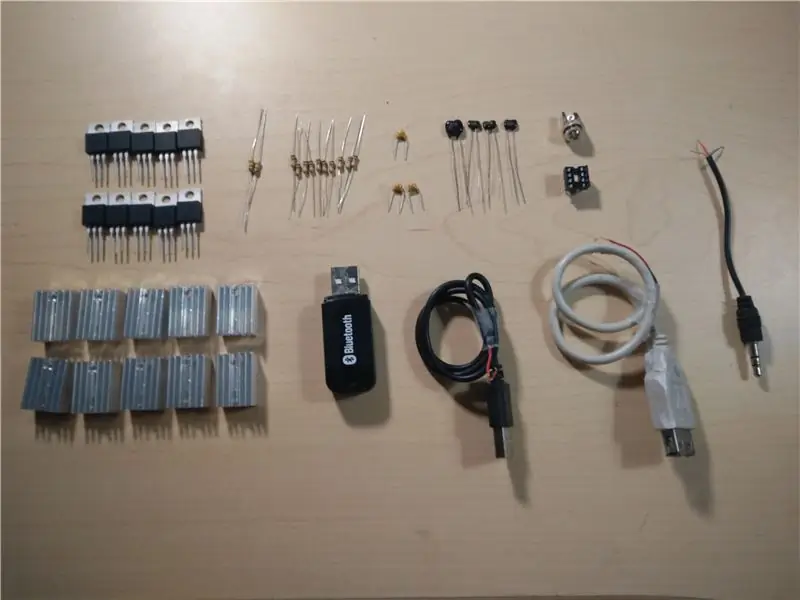
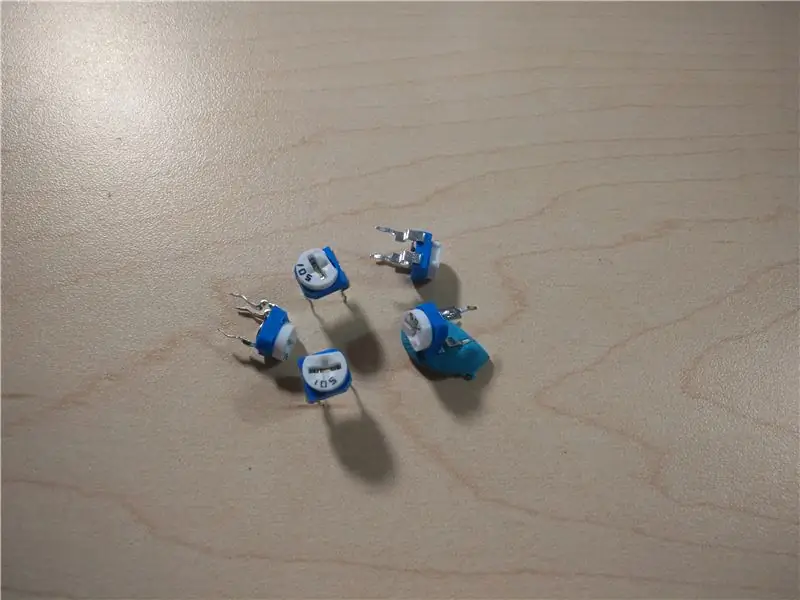
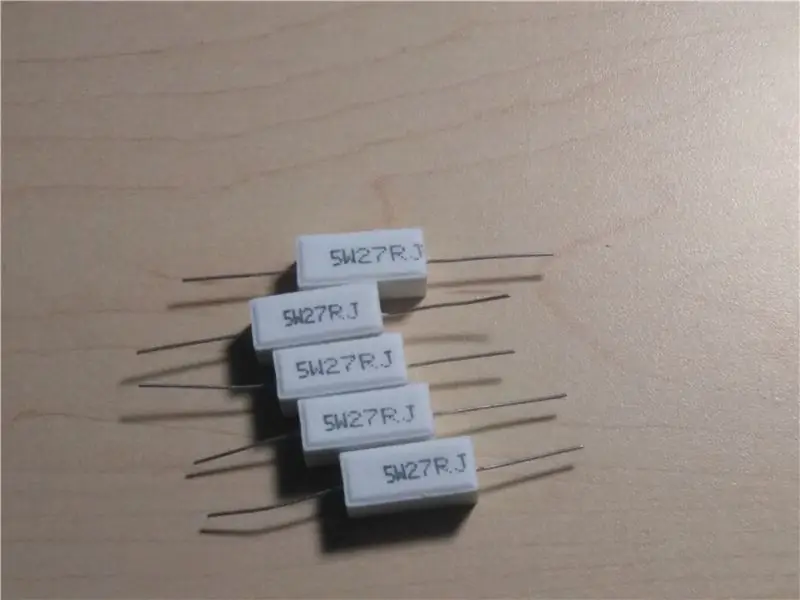
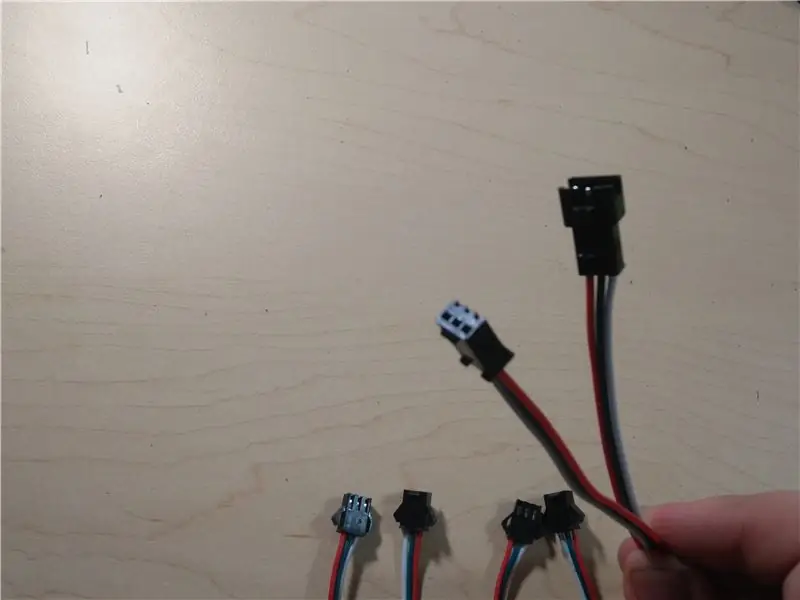
W tym projekcie wykorzystano sporo części. Wiele części miałem przy biurku, inne części kupiłem w lokalnym sklepie z częściami.
Będziesz potrzebować:
UWAGA: ilość części w nawiasach
(1) Arduino Mega 2560
(1) moduł Bluetooth USB
(1) 8-pinowe gniazdo DIP
(1) MSGEQ7 - polecam kupić to od Sparkfun Electronics, ponieważ eBay jest pełen fałszywych wersji tego układu scalonego
(1) Gniazdo słuchawkowe
(1) Kabel słuchawkowy z końcówką żeńską
(1) standardowa żeńska wtyczka USB z przyzwoitą długością kabla
(5) złącze 3-przewodowe (pary) zwykle sprzedawane jako złącze 3-przewodowe do taśm LED ws2812b (patrz zdjęcie)
(10) FQP30N06L N-kanałowy mosfet
(5) Standardowa dioda blokująca 1N4001
(4) 3mm czerwona dioda LED
(4) żółta dioda LED 3mm
(4) Biała dioda LED 3mm
(4) 3mm zielona dioda LED
(4) 3mm niebieska dioda LED
(10) 10k rezystorów 1/4 wata
(8) rezystory 100 omów
(8) rezystory 150 omów
(5) potencjometry 500 omów
(5) potencjometry 2k OHM
(5) Rezystory 27 omów 5 wat
(2) Rezystory 100k OHM
(2) kondensatory 100nF
(1) Kondensator 33pF - Musi być tą wartością; Umieściłem wiele kondensatorów równolegle, aby osiągnąć tę wartość
(1) Kondensator 10nF
(1) Włącznik - ON (otwór montażowy miał 3 mm, zwykle wymieniany jako mini przełącznik w serwisie eBay)
(4) śruby 1/8 "x 1 1/2" (moje zostały oznaczone jako śruby do pieca z Home Depot, plik 3d jest skonfigurowany dla tego rozmiaru nakrętki i śruby)
(2) około 12-calowe odcinki kabla Ethernet
Części drukowane w 3D, jeśli nie posiadasz drukarki, strony takie jak 3dhubs.com są świetnym źródłem informacji.
Gorący klej
Lutowane + lutownica
Męskie szpilki nagłówka
Krok 2: Zdemontuj adapter Bluetooth

Pierwotnie zamierzałem użyć męskiego kabla USB, ale gniazdo było na nim zepsute, postanowiłem wtedy zdemontować przejściówkę i usunąć port USB. Za pomocą multimetru udało mi się znaleźć uziemienie, testując piny do zewnętrznej obudowy portu USB. (są połączone)
UWAGA: Właściwie musiałem wymienić ten adapter w trakcie projektu, ponieważ powodował hałas o wysokiej częstotliwości na porcie audio, nowy też nie jest w 100% lepszy. ale mam inny odbiornik, który działa, ma jednak własną baterię i włącznik / wyłącznik, dzięki czemu głośniki wodne nie są tak plug and play. chociaż te odbiorniki są tanie, płacenie więcej nie zawsze oznacza, że otrzymujesz wysoką jakość.
Krok 3: Konfigurowanie układu scalonego na płycie perforowanej

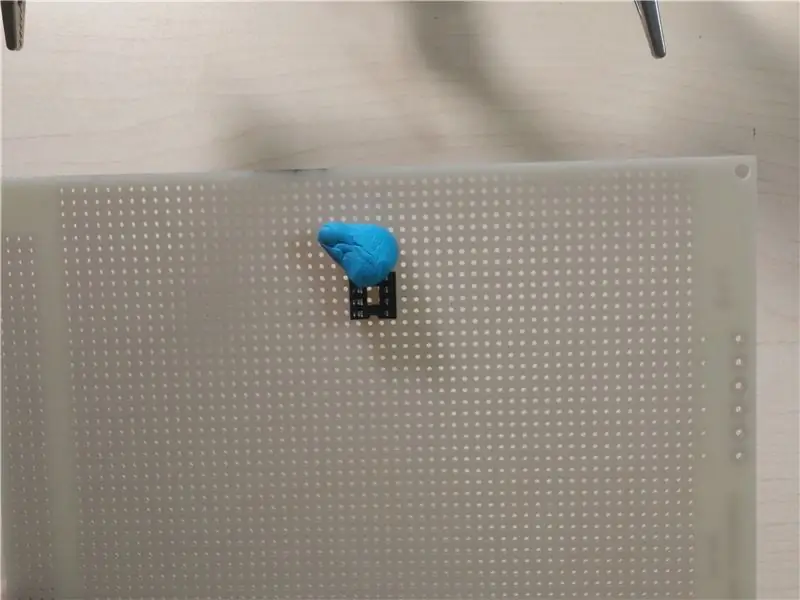
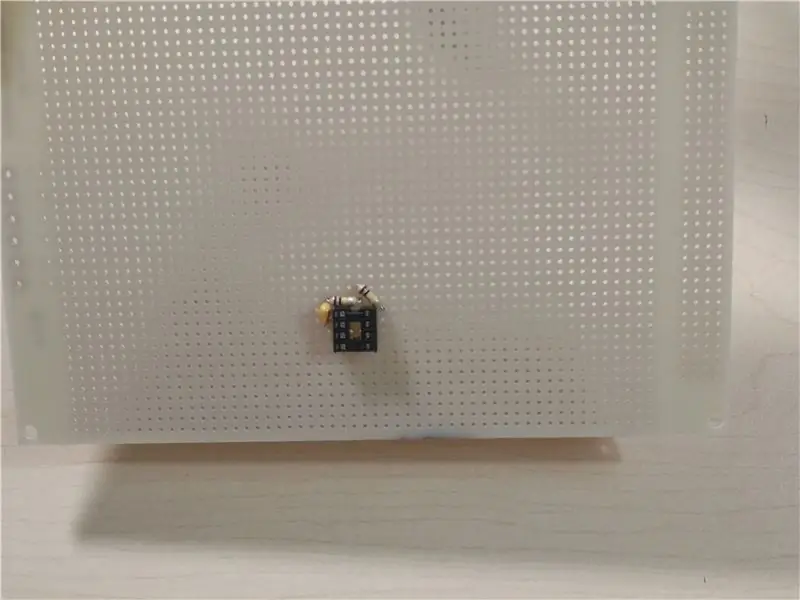
W tym kroku rozpoczniemy lutowanie płyty perforowanej gniazda IC DIP.
Schemat pokazuje jak będą okablowane wszystkie części, pin sterujący mosfet to etykieta "PWM" bo właśnie podpiąłem je bezpośrednio do pinu na arduino, jak mogłem zmienić co każdy pin sterowany z kodu.
Zacząłem od umieszczenia gniazda DIP z jednej strony deski, blisko środka deski.
WSKAZÓWKA: lepka przyczepność pomaga utrzymać części na miejscu podczas lutowania.
Następnie dodałem kondensator 100nF na pinach 1 i 2, a następnie użyłem dwóch rezystorów 100k OHM do podłączenia do pinu 8. Następnie użyłem 4 kondensatorów równolegle i dodałem 100nF na pin 6. Następnie dodano męski kabel audio i podłączono do Kondensator 10nF. Uziemienie z kabla audio było przywiązane do ziemi.
Dołączyłem obraz tylnej strony płyty perforowanej, dodałem również etykiety na spodzie, aby łatwiej było zrozumieć, gdzie części zostały okablowane.
Krok 4: Dodawanie mosfetów
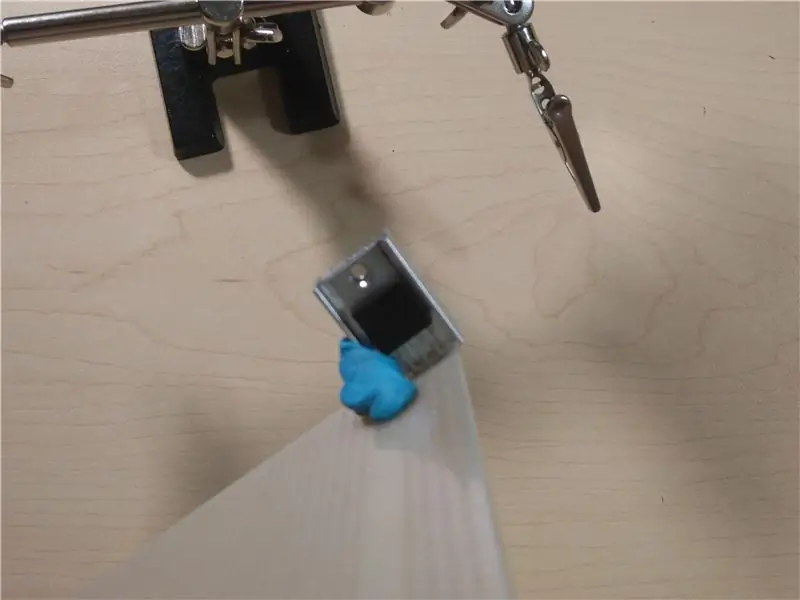
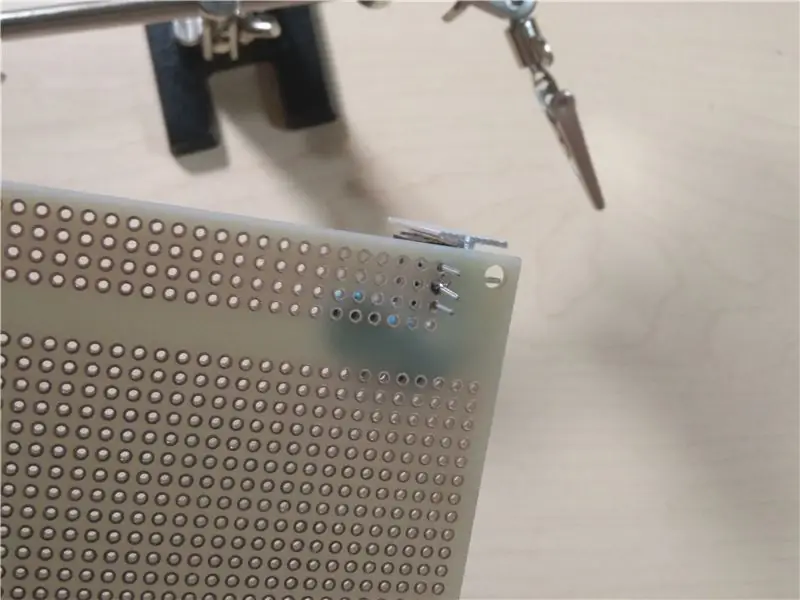
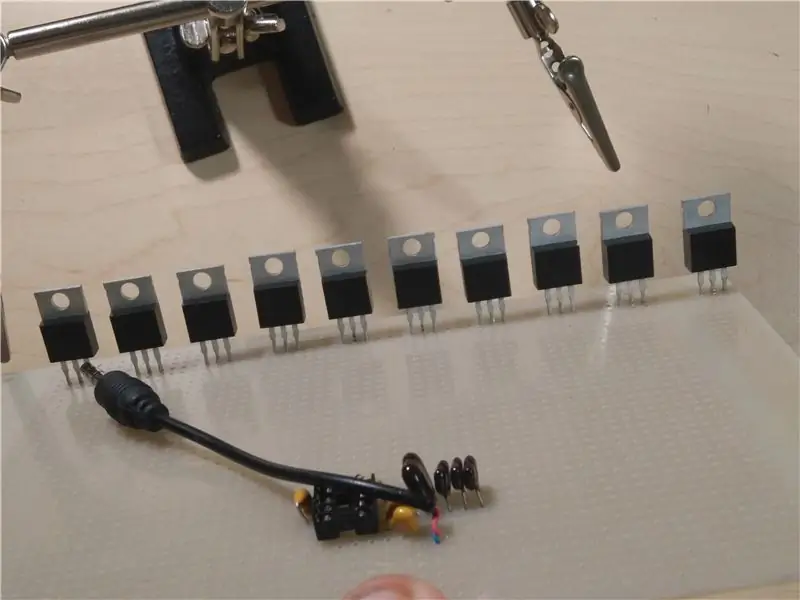
Kolejnym krokiem było dodanie mosfetów, ponieważ dodawałem mosfety, do ustawienia wysokości używałem radiatorów, później okazało się, że nie nagrzewają się na tyle, aby wymagały dodania radiatorów.
Zacząłbym od przyłożenia lutu do środkowego pinu, pozwalając na regulacje.
Po umieszczeniu mosfetów zacząłem dodawać rezystory ściągające 10k OHM, użyłem nóg rezystora do mostkowania między niezbędnymi pinami.
Krok 5: Umieszczenie diod i rezystorów 5W
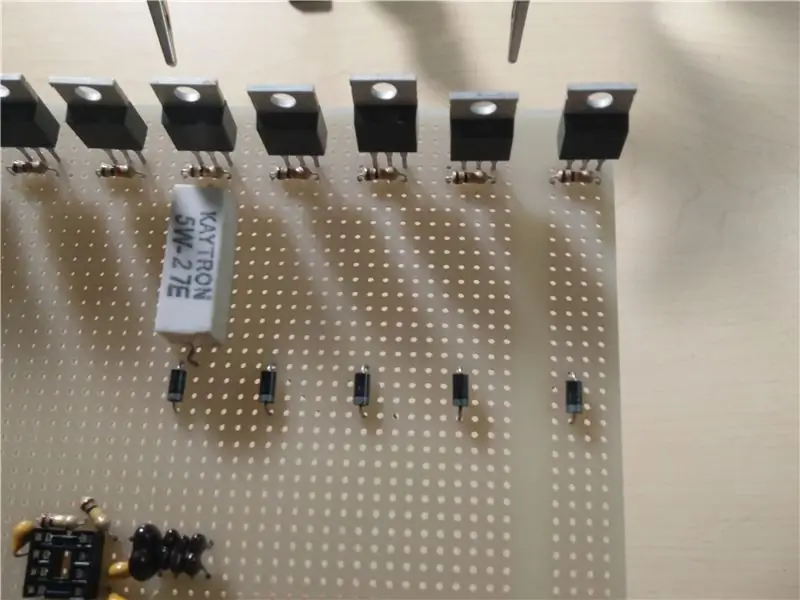
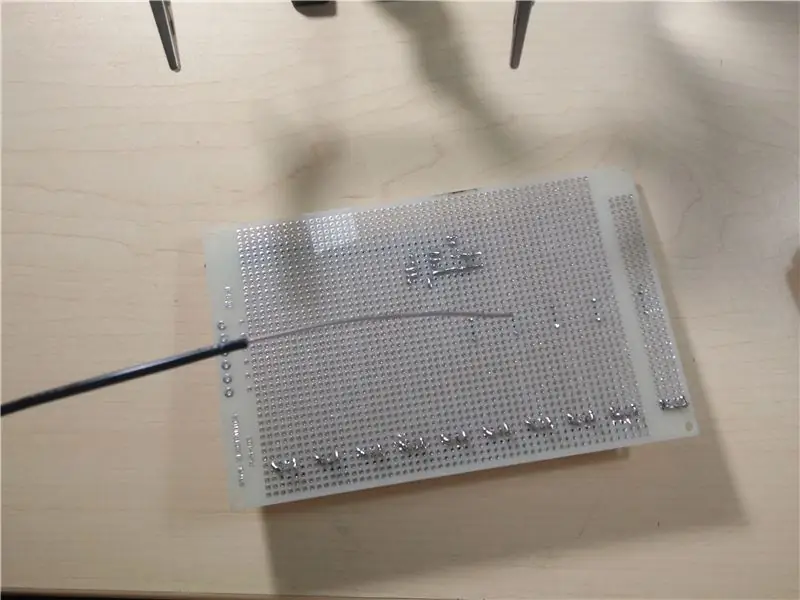
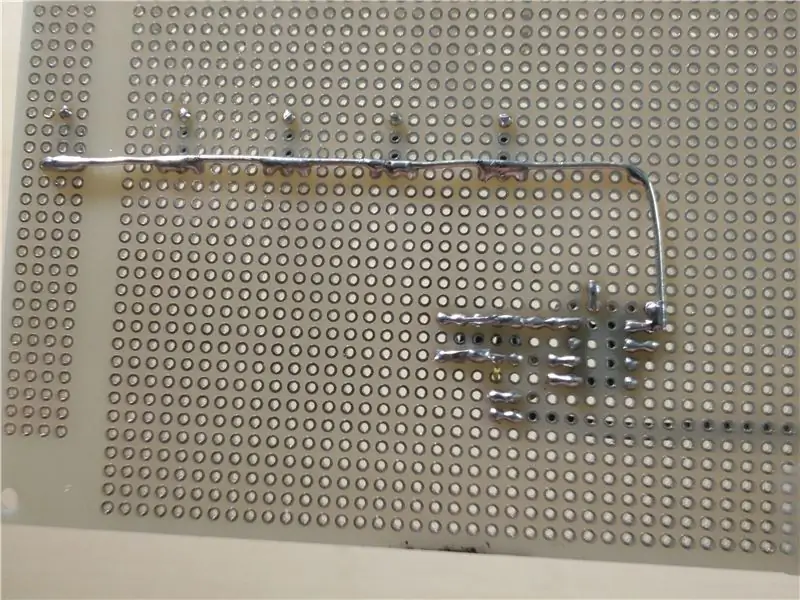
W momencie wykonywania tego kroku wciąż czekałem na dostawę rezystorów 5W, więc uratowałem rezystor z poprzedniej wersji głośników wodnych, aby zapewnić odstępy wymagane do umieszczenia diod.
Po umieszczeniu diod zacząłem zdejmować solidny drut 18AWG, aby działał jako dodatnie i ujemne szyny zbiorcze
Solidny drut AWG został umieszczony po dodatniej stronie diod, a następnie poprowadzony do pinu 1 w gnieździe IC.
inny element został użyty do przejścia od ujemnej strony kondensatora 33pF i pętli wokół mosfetów. Kolejny mniejszy kawałek został zapętlony od ujemnego kondensatora 33pF do pinu 2 w gnieździe IC.
Krok 6: Dodanie gniazda panelu, Bluetooth i potencjometrów
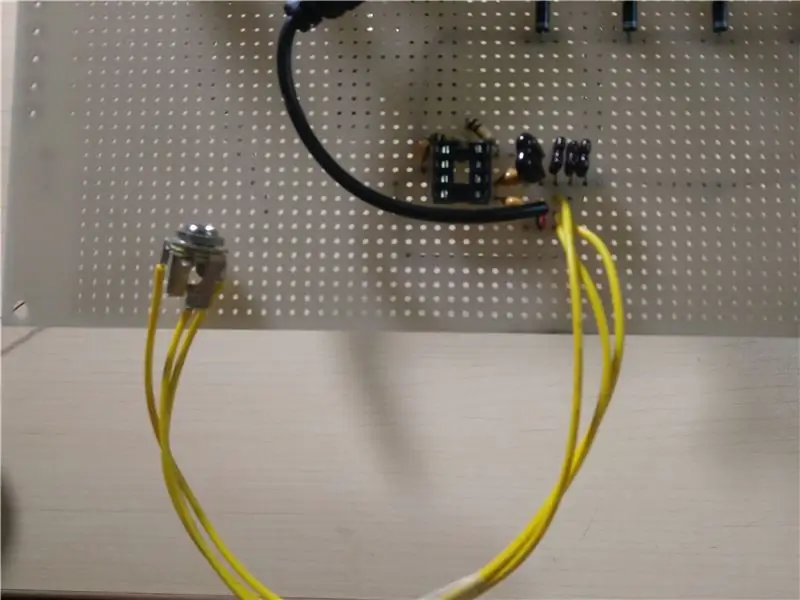
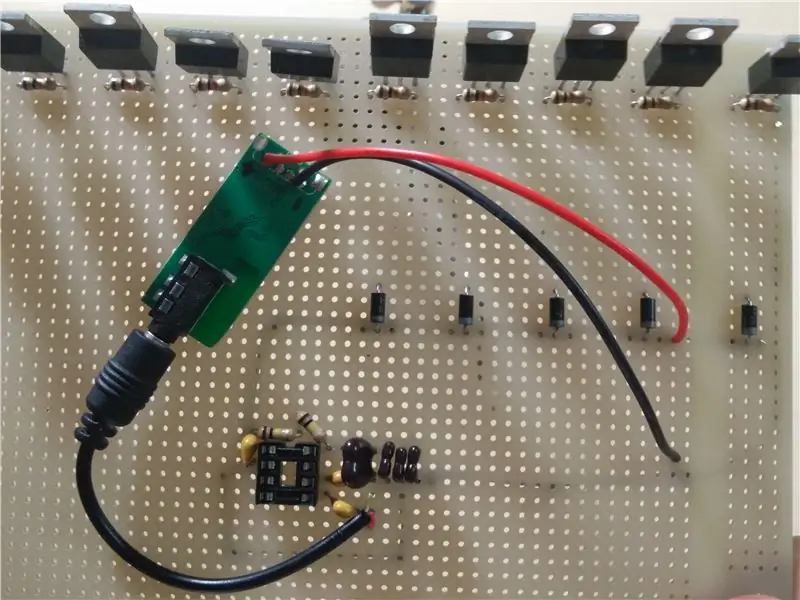
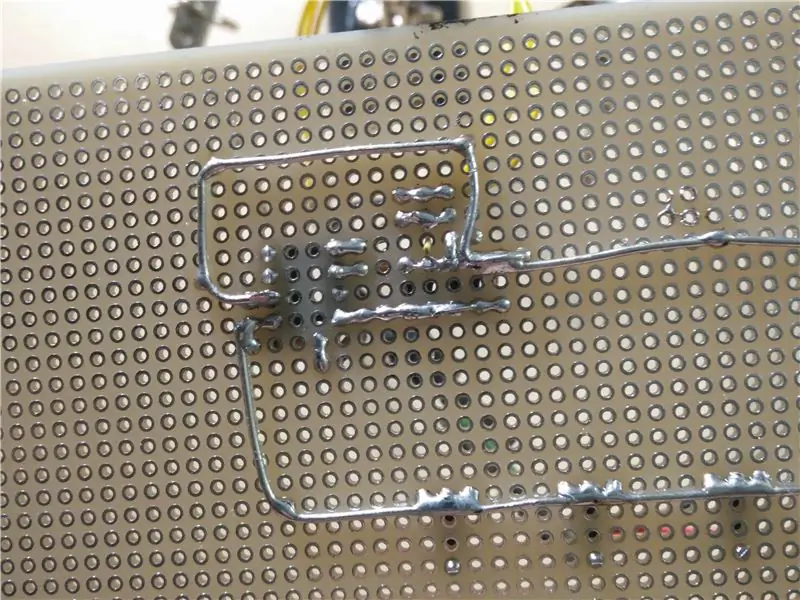
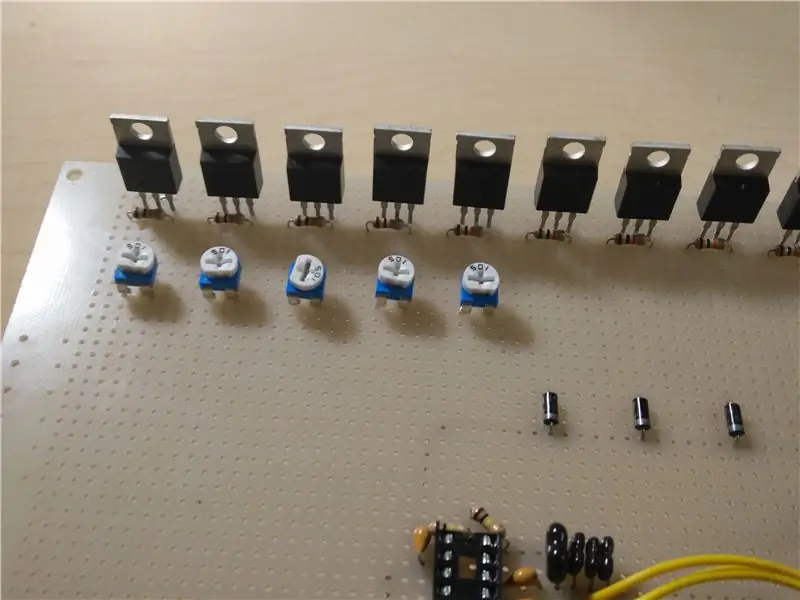
Używając linki połączeniowej 20AWG, aby podłączyć gniazdo panelu do tych samych połączeń, co męski kabel audio. Następnie dodałem przewody do zasilania i uziemienia dla adaptera Bluetooth, używając solidnej szyny AWG na spodzie.
Następnie dodałem potencjometry 500 OHM, które pozwalają na dodatkową kontrolę jasności LED (są one konieczne, ale uważam, że niektóre kolory LED mogą przytłaczać inne, więc dodałem je, aby dostosować ich jasność)
Użyłem nadmiaru metalu z przyciętych przewodów kondensatora, aby zniwelować odległość od potencjometru do środkowego pinu mosfetów
Krok 7: Przygotowanie głośników wodnych
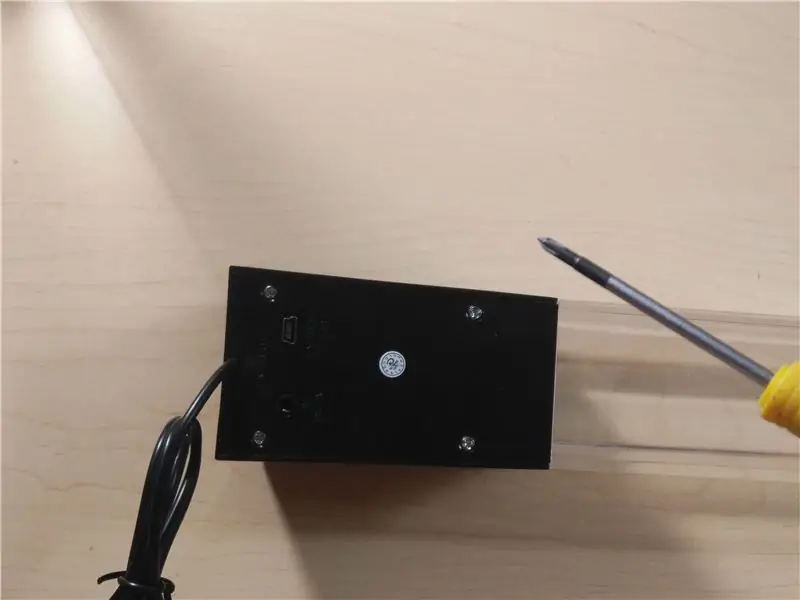
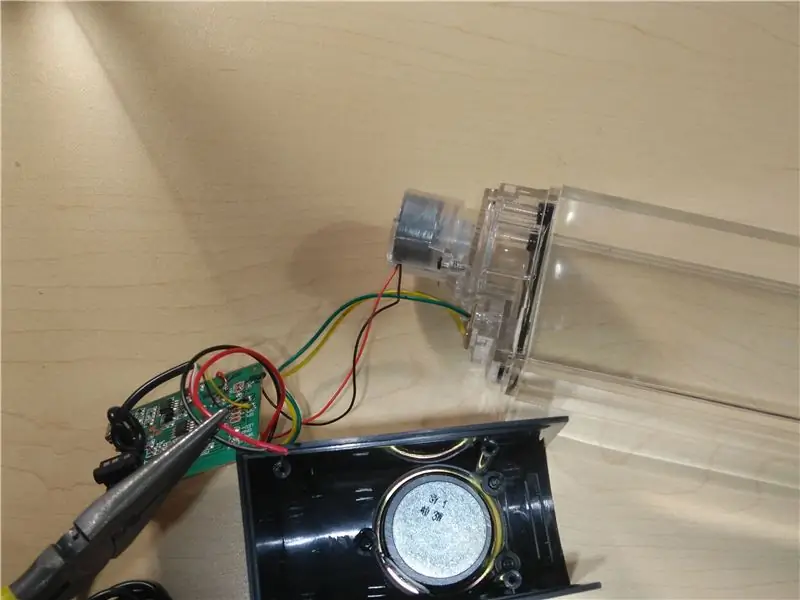
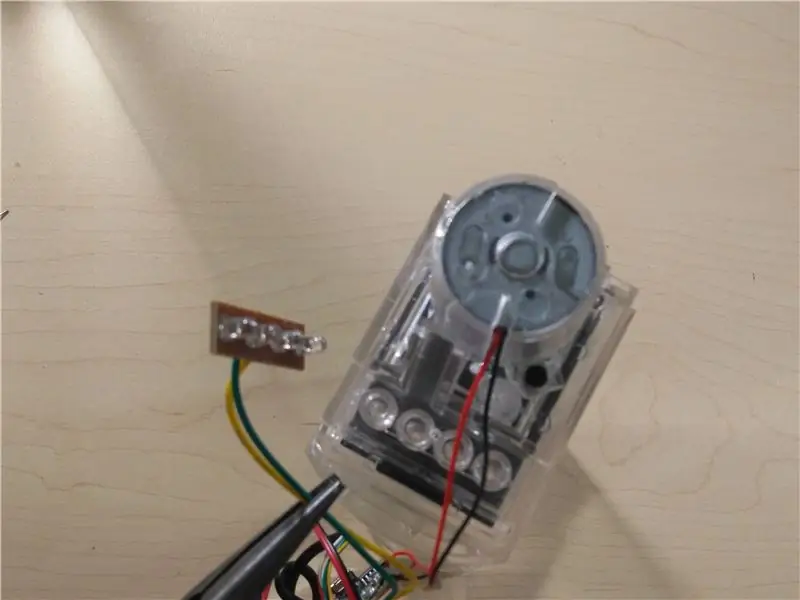
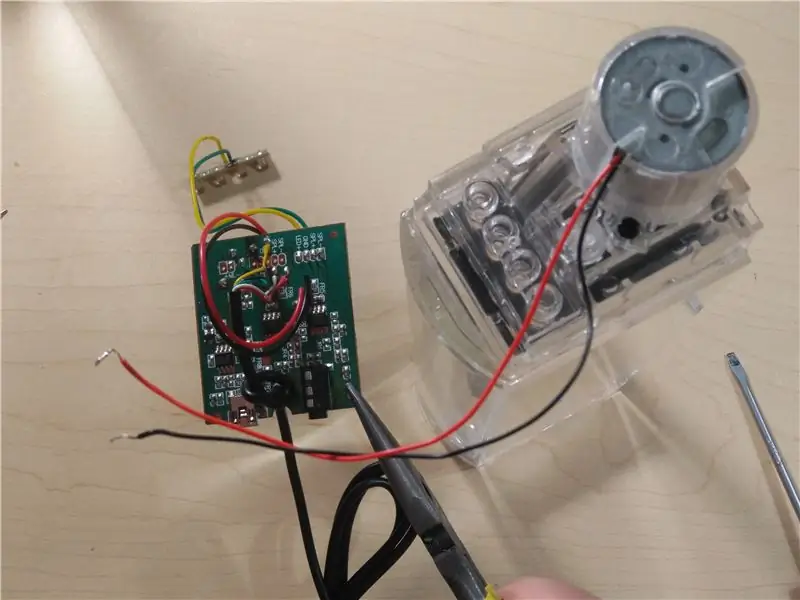
Zacząłem od odkręcenia małym śrubokrętem małych śrubek z tyłu obudowy głośnika wodnego, po wyjęciu płytki drukowanej zlokalizowałem przewody do silnika. używając frezów do przepłukiwania, wycinałem je jak najbliżej płytki drukowanej.
UWAGA: przewody na silnikach nie nadają się do serwisowania, popełnianie zbyt wielu błędów podczas cięcia i ściągania końcówek może zniszczyć silnik/przewody
Następnie użyłem małych szczypiec, aby usunąć płytkę drukowaną z diodami LED. Wybieram jeden kolor na obudowę z wodą w porównaniu z 4 kolorami, które są używane z produktu w sklepie.
Następnie zginam dodatnie przewody LED prawie równo, tak że krzyżują się ze sobą, zaczynam od wygięcia zewnętrznych diod LED, aby diody LED poziomu rozciągały się od końca do końca. Używanie kleju samoprzylepnego do trzymania diod LED na miejscu; Następnie zginam dwie wewnętrzne diody LED, ale przycinam ich przewody, ponieważ nie muszą być tak długie. Z diodami trzymanymi przez lepką przyczepność nie mogę lutować razem dodatnich wyprowadzeń.
Mogę teraz przyciąć ujemne przewody diod LED i przyciąć również rezystory. (Zdecydowałem się ustawić diody LED tak, aby ich kolorowe paski były skierowane w tym samym kierunku; było to czysto kosmetyczne) Używając wyprowadzeń rezystorów, zginałem je w taki sam sposób, jak w przypadku dodatnich wyprowadzeń diod LED.
Do unieruchomienia diod LED użyłem gorącego kleju. Następnie dołączony 3-przewodowy łącznik. Silnik i diody LED mają wspólny pozytyw. pasujące złącza są następnie podłączane do płytki perforowanej, dodatnie po jednej stronie diody i ujemne silnika po drugiej stronie diody. Negatyw diod LED jest podłączony do nogi na potencjometrze.
Czerwone i żółte diody LED miały na sobie rezystor 150 omów
Białe, zielone i niebieskie diody LED miały na sobie rezystor 100 omów
Te wartości rezystorów powinny pozwolić każdej LED działać przy 20mA
Krok 8: Dodawanie przewodów Arduino
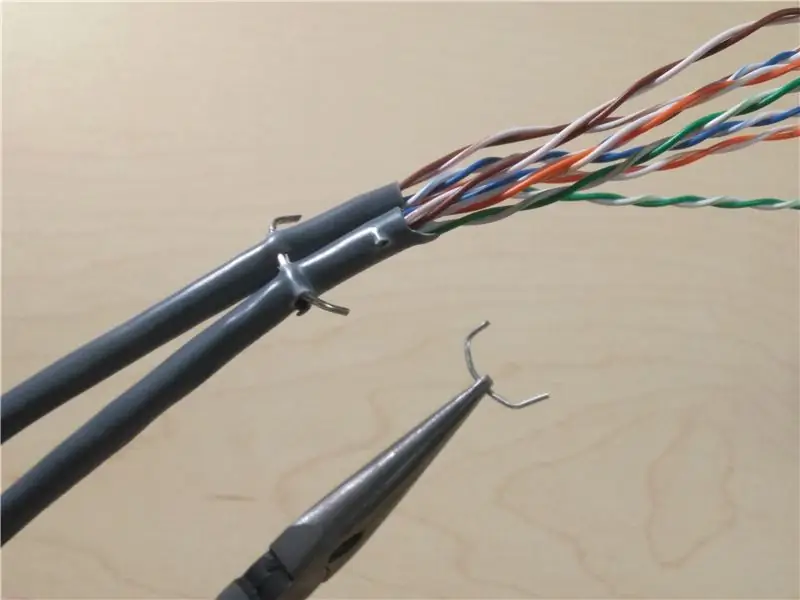
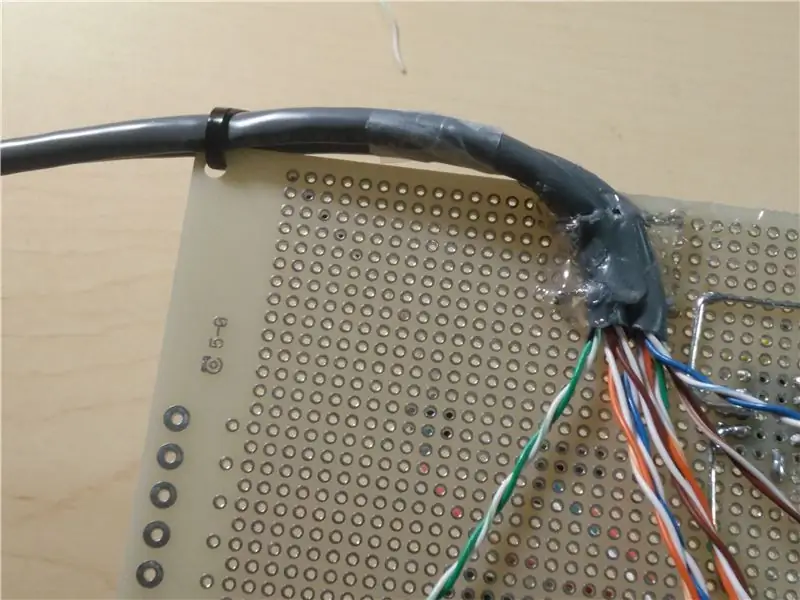
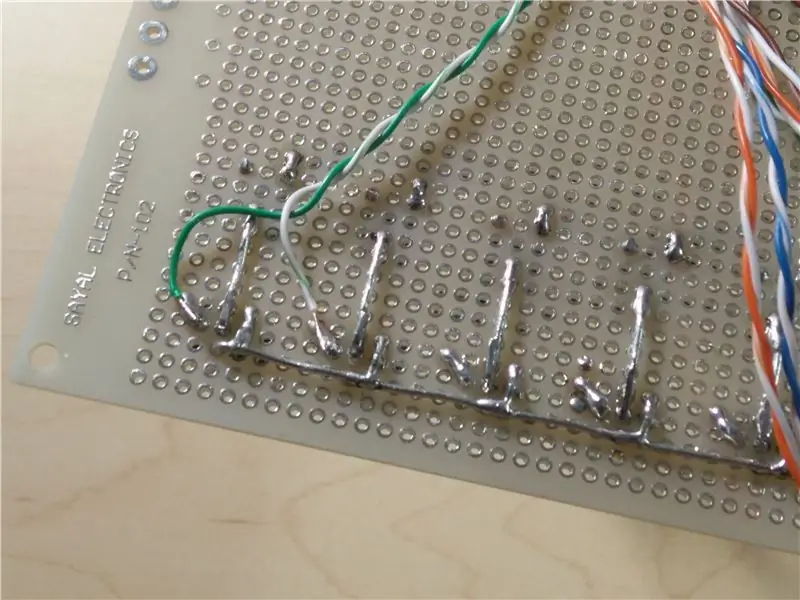
Użyłem dwóch odcinków kabla Ethernet, około 12 cali kabla (x 2) Użyłem łącznie 15 przewodów (1 zapasowy)
Użyłem części drutu z litego rdzenia, aby pomóc w zabezpieczeniu kabla do płyty perforowanej, skończyło się na tym, że potrzebowałem gorącego kleju, aby utrzymać go na miejscu. Zapięcie na suwak w rogu pomogło skierować przewód do arduino, które po umieszczeniu w futerale znajdowałoby się obok płyty perforowanej.
Przewody były rozmieszczone losowo, ale upewniłem się, że mogą dotrzeć do miejsca, w którym potrzebują, niektóre były dłuższe niż inne, te, które były zbyt długie, zostały przycięte na wymiar. Za pomocą nagłówków udało mi się przylutować pozostałe końce drutu do pinów, co pozwala mi na demontaż arduino, jeśli zajdzie taka potrzeba. Skończyło się na dodaniu gorącego kleju później, aby przewody nie zerwały pinów, ale robię to po przetestowaniu wszystkich funkcji.
Dodałem przewody do sterowania IC i przewód zarówno do 5v+, jak i do masy.
Po wykonaniu tej czynności wykonałem test, aby sprawdzić, czy światła i układ scalony będą działały poprawnie, ponieważ wciąż czekałem na rezystory 5W w mailu.
Krok 9: Rezystory silnika i potencjometry
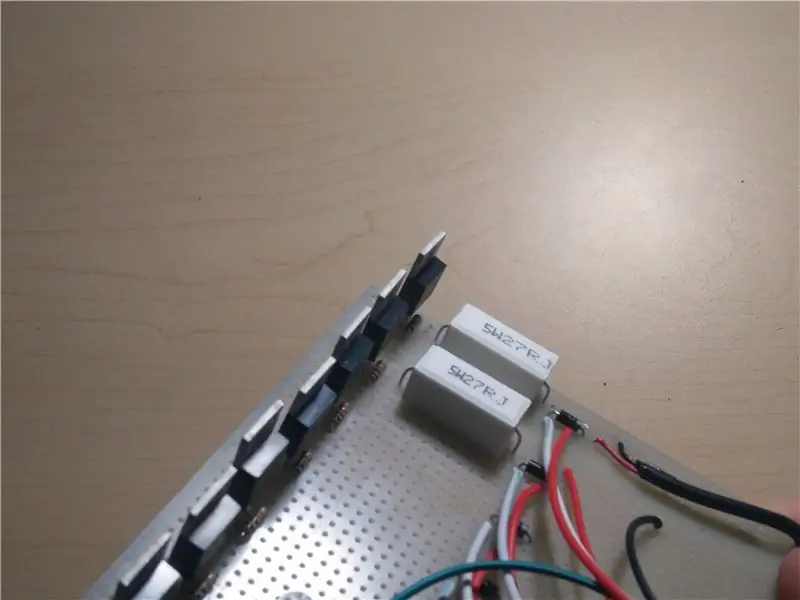
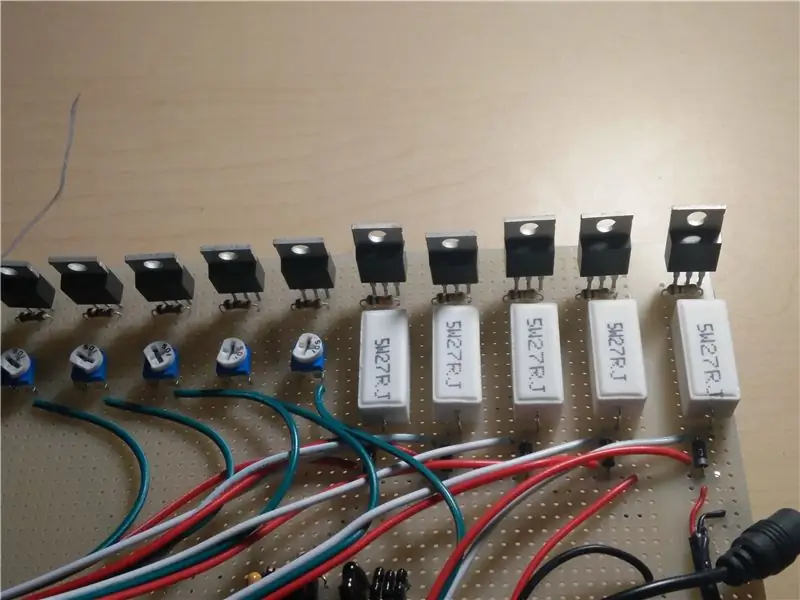
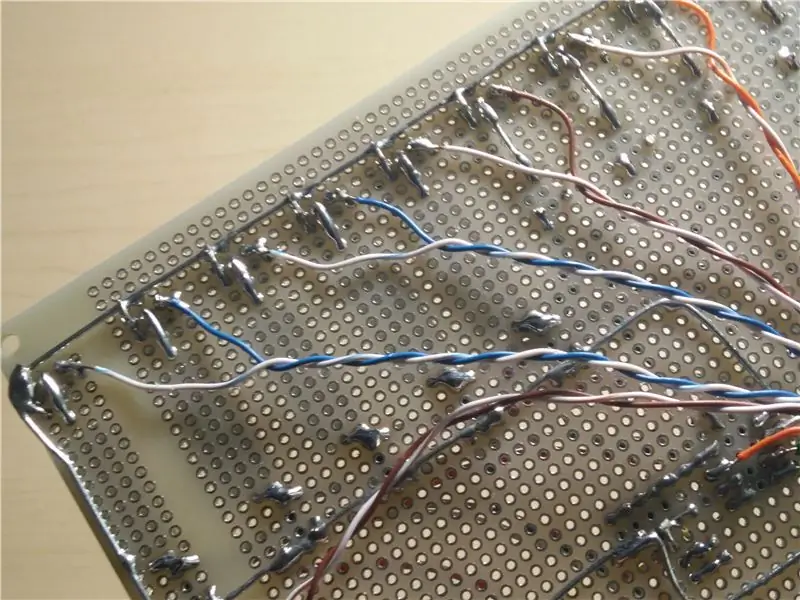
Dodałem rezystory 5W między diodą a środkowym pinem mosfeta. Używam wyprowadzeń rezystora, aby zniwelować lukę.
Uważam, że silniki są bardziej wrażliwe na impulsy i są uruchamiane szybko, gdy woda już powoli płynie. Tutaj do gry wkracza potencjometr 2k. Potencjometr jest podłączony za pomocą przewodu połączeniowego 20 AWG do rezystora 5 W (nie podłączaj tego przewodu przed rezystorem 5 W, ponieważ potencjometr nie może obsłużyć mocy silnika)
Druga noga potencjometru jest wygięta i za pomocą kolejnego kawałka solidnego drutu 18AWG mogę podłączyć jeden pin wszystkich potencjometrów do masy.
UWAGA: Początkowo próbowałem nie używać potencjometrów, ale odkryłem, że używanie PWM w tych silnikach powoduje straszne sprzężenie zwrotne wysokiej częstotliwości, które powoduje zakłócenia w układzie scalonym
Krok 10: Drukowanie 3D
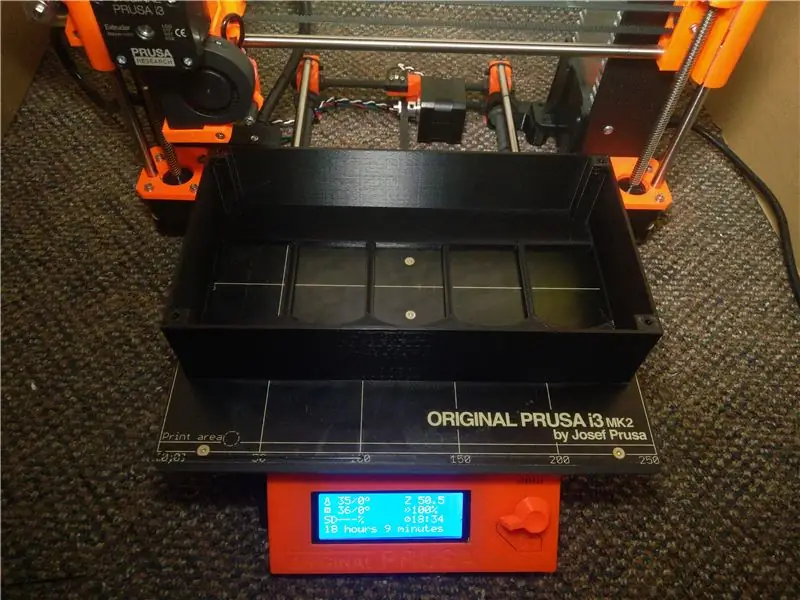
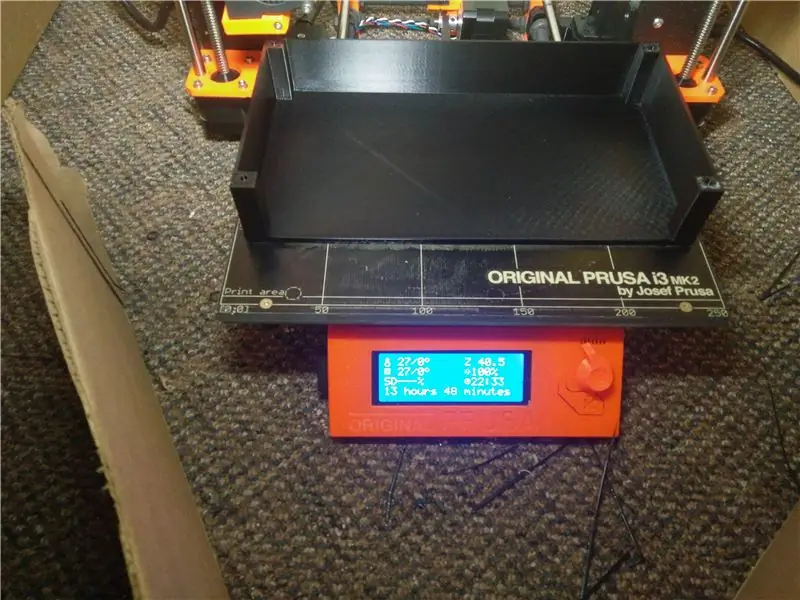
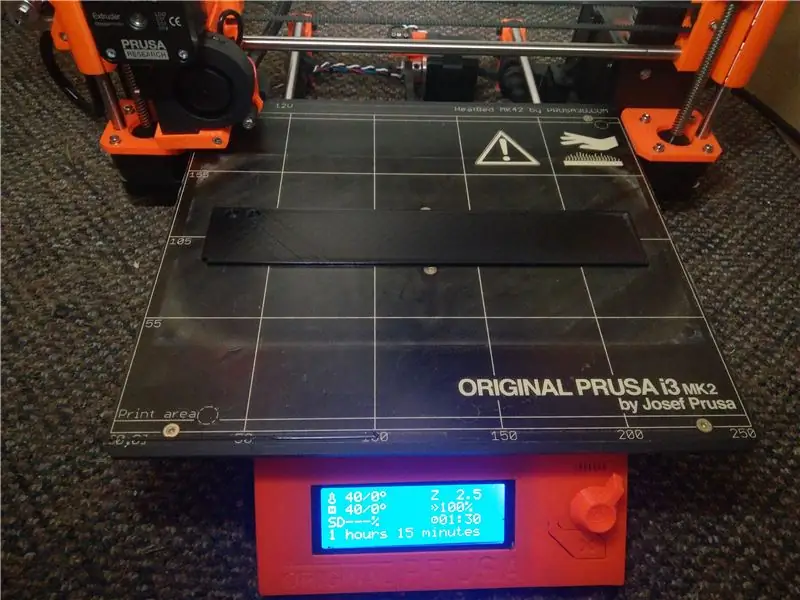
Wydrukowałem w sumie 3 części, górny, dolny i tylny panel. Jednak pliki STL, które dodałem, to tylko dwie części (góra i dół), co ułatwi komuś śledzenie. Zrobiłem to, ponieważ stwierdziłem, że próba dodania panelu po fakcie nie wygląda tak dobrze. Robię głównie tylny panel, ponieważ nie byłem pewien, co chcę z tyłu. W moim przypadku postanowiłem dodać włącznik/wyłącznik.
W sumie patrzysz na 36 godzin drukowania 3D. Używam ABS w mojej drukarce, ponieważ bardzo łatwo maluję i szlifuję. Dodatkowo, kiedy tworzę zespoły, mogę używać acetonu do spawania części.
Pierwsza część, którą polecam wydrukować, to plik testowy pomiaru 3D, jest to mały 15-minutowy kawałek, który pozwala upewnić się, że głośnik wodny będzie pasował. Przeszedłem przez około 8 iteracji, aż uzyskałem odpowiedni profil, aby dopasować głośnik. Dzięki temu oszczędzam marnowanie 18-godzinnego wydruku. góra ma szczeliny na 1/8 "x 1 1/2", musiałem użyć małego pliku, ponieważ mostkowanie na mojej drukarce 3D jest trochę ciasne.
Krok 11: Montaż
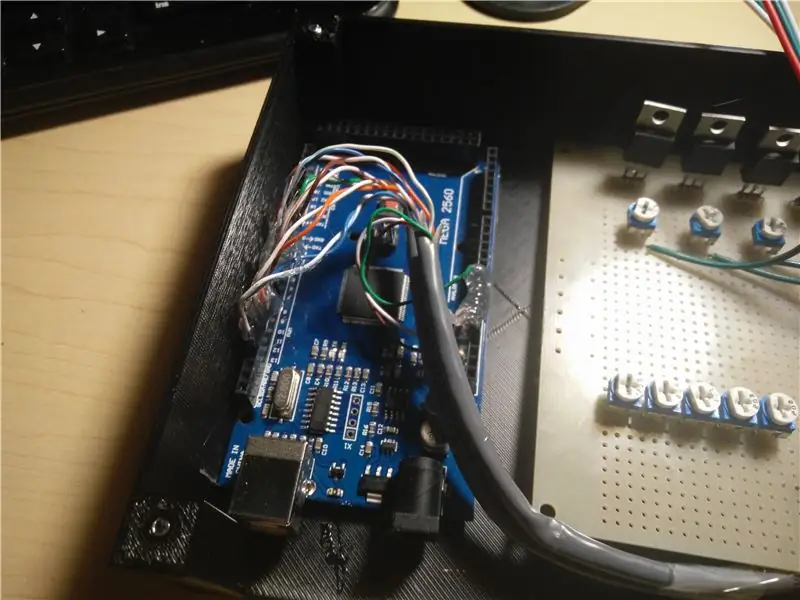
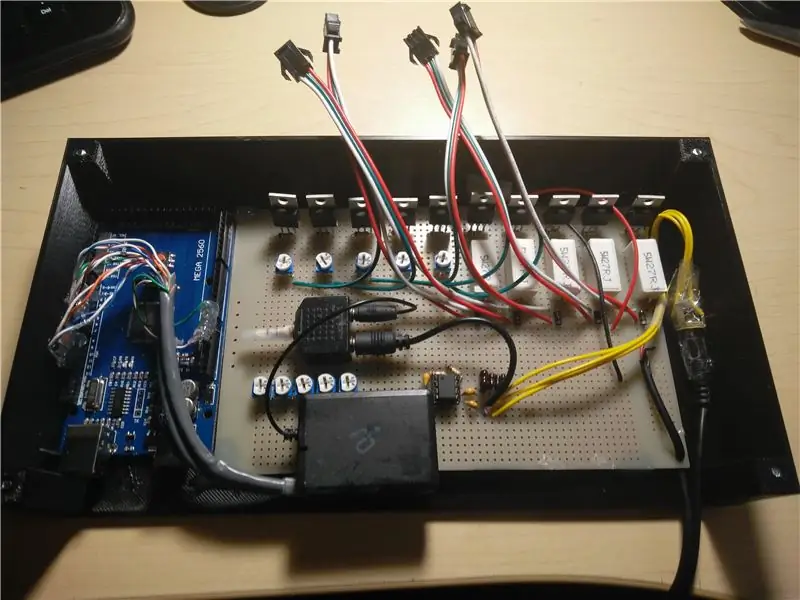
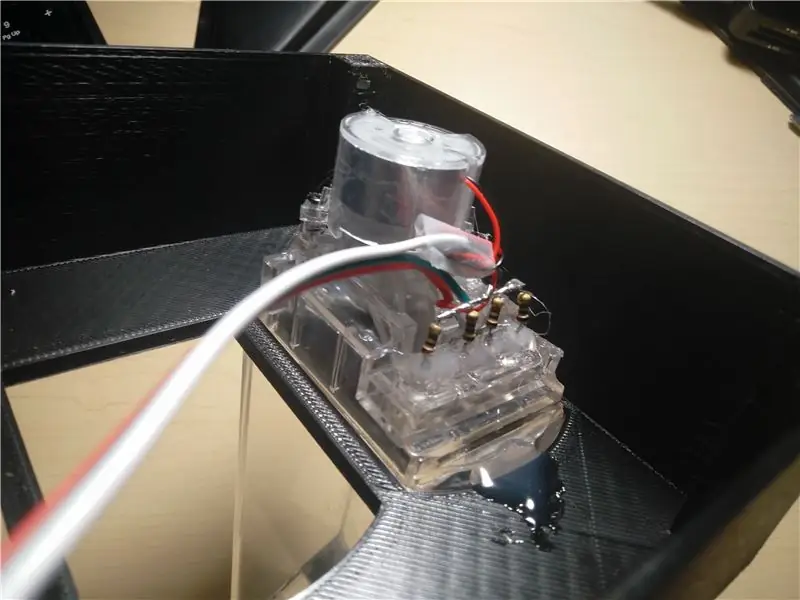
Zacząłem od użycia gorącego kleju na główkach do przewodów, aby upewnić się, że się nie złamią. Gorący klej dodałem po upewnieniu się, że silniki działają z programowaniem. Użyłem niewielkiej ilości gorącego kleju w dwóch rogach arduino, aby można było go później usunąć w razie potrzeby. alternatywnie w druku 3D można zaprojektować elementy dystansowe i wkładki gwintowane.
Jak widać na zdjęciu mam dołączony inny moduł Bluetooth, korzystałem z tego modułu podczas oczekiwania na nowy w mailu. Głównym problemem fałszywego wyzwalania głośników nie jest wyłącznie wina modułów Bluetooth, silniki wydają się nie lubić pracować na PWM.
Do górnego elementu dodałem wieże ciśnień i zabezpieczyłem go gorącym klejem. Zużyłem niewielką ilość, ponieważ planuję później zdemontować głośniki i przeszlifować, a następnie pokryć bezbarwnym plastikiem, ale jest za zimno, aby natryskiwać farbę w miejscu, w którym teraz jestem. Gniazdo panelu i przełącznik zostały następnie dodane do tylnego panelu, właściwie dodałem kabel zasilający USB wcześniej, ale teraz, gdy wydruk 3D jest jednym elementem, kabel musi zostać poprowadzony przez obudowę, a następnie podłączony na miejscu, możesz zobaczyć, gdzie podpięty USB na zdjęciu, przebija się przez płytkę perforowaną i przylutowany do solidnej szyny z drutu AWG, Jedyna różnica od zdjęcia polega na tym, że przy przełączniku dodatni najpierw przejdzie do przełącznika, a następnie do płytki perforowanej.
Krok 12: Kodeks
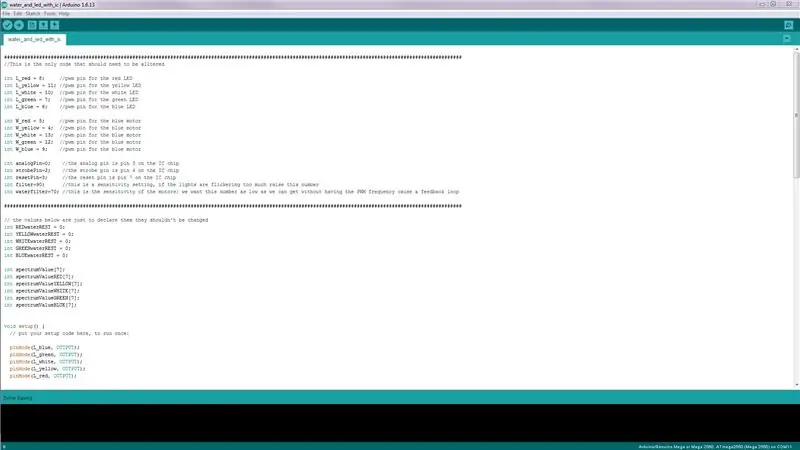
Dodany przeze mnie kod jest w większości prosty. Kod powinien działać bez zmian.
Jedyną rzeczą, którą należałoby zmienić, są zmienne na górze kodu. Są wyraźnie oznaczone komentarzami.
NOTATKA:
W oparciu o wskazówkę poświęciłem czas na naukę i próbę dostosowania częstotliwości PWM na arduino mega. Chociaż zmiana częstotliwości pomogła usunąć hałas silnika, który powodował pętlę sprzężenia zwrotnego, wymagała jednak zmiany wielu innych części kodu, trzeba było zmienić taktowanie, trzeba było zwiększyć czułość.
Problem ze zmianą utworzonej częstotliwości PWM polegał na tym, że trzeba było zwiększyć taktowanie, aby zrównoważyć fałszywe wyzwalanie, które zaczęło się pojawiać, a wartości musiały zostać zmienione, co zmniejszyło czułość głośników. Uważam, że najlepszą rzeczą w tym momencie byłoby wypróbowanie sterownika silnika z mojej poprzedniej iteracji tego projektu, o którym mówi się więcej w ostatnim kroku.
Krok 13: Produkt końcowy
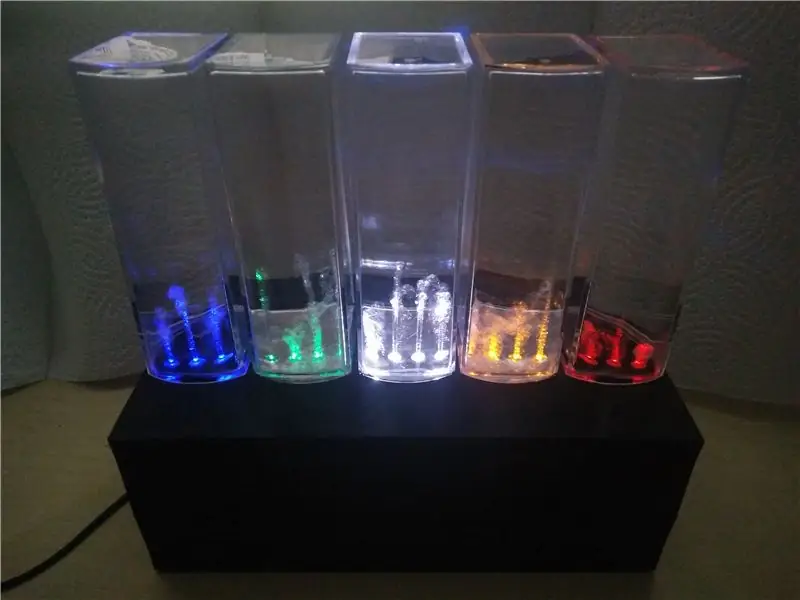
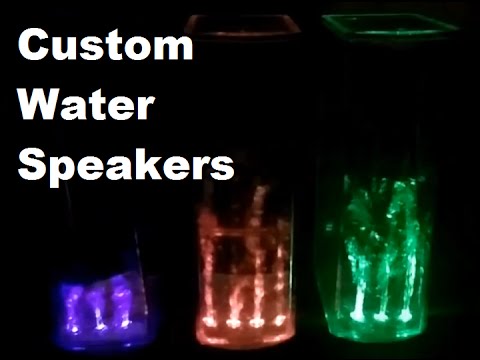
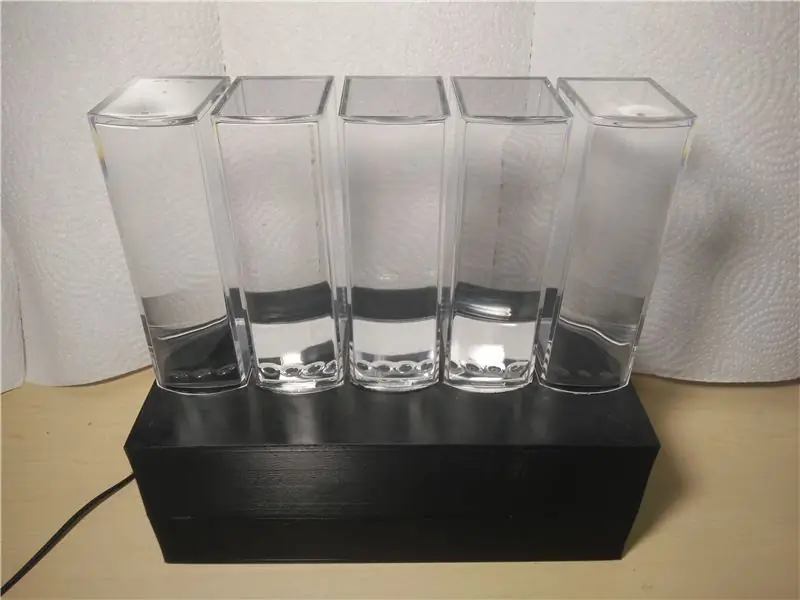
Ostatni element jest naprawdę intrygujący do obejrzenia. Ten element najlepiej oglądać w słabym lub ciemnym oświetleniu pokoju. Niestety mój obecny aparat nie jest w stanie nagrywać w warunkach słabego oświetlenia. To dlatego, że mógłbym użyć dobrego aparatu do pokazania moich projektów, które zgłosiłem po raz pierwszy w konkursie autorskim, mam nadzieję, że ludziom spodobał się ten projekt i zdecydują się na mnie głosować.
Dodałem wideo z oryginalnej wersji głośników, aby z grubsza zobaczyć, jak wyglądają.
Następne kroki
Chciałbym spróbować użyć oryginalnego obwodu sterownika silnika, który stworzyłem w wersji 1, który używa tranzystorów i fotokomórek, aby sprawdzić, czy pozwoli to silnikom działać lepiej, powinno to wyeliminować problemy, które miałem z szumami częstotliwości silniki dzięki wykorzystaniu sygnału sterującego PWM. Mogę też dodać kilka głośników z boku obudowy wraz z własną regulacją głośności.
Możesz również zauważyć, że wnętrze wież ciśnień ma różne kolory, oryginalne głośniki, które miałem, są chome, których nie mogłem znaleźć lokalnie, więc zdecydowałem się na czarny na nowe (dostępne w różnych kolorach) Mogę ulepszyć do wszystkich w jednym kolorze, ale sprzedają za 40 dolarów za parę.
Zalecana:
Konwersja starego głośnika na Bluetooth Boombox: 8 kroków (ze zdjęciami)
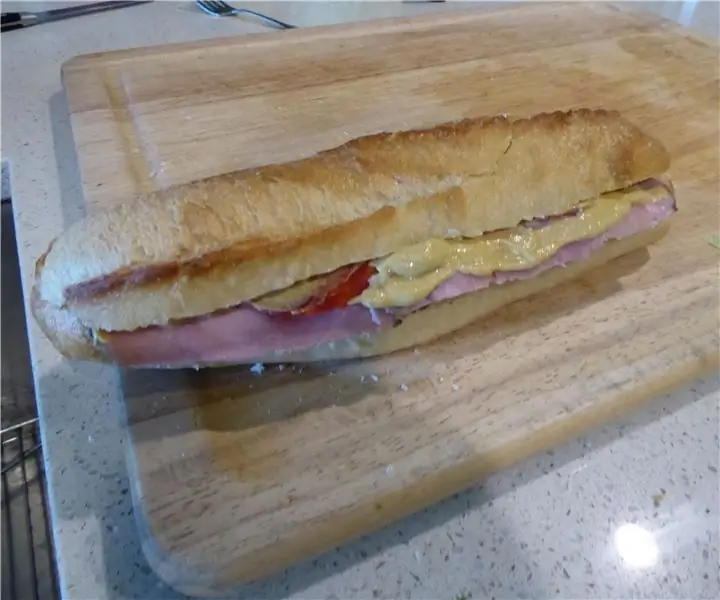
Konwersja starego głośnika na Bluetooth Boombox: Cześć wszystkim! Dziękuję bardzo za dostrojenie się do tej wersji! Zanim przejdziemy do szczegółów, zastanów się, czy zagłosować na tę instrukcję w konkursie na samym dole. Wsparcie jest bardzo cenione! Od kilku lat minęło
Płytka PCB głośnika bezprzewodowego: 5 kroków (ze zdjęciami)
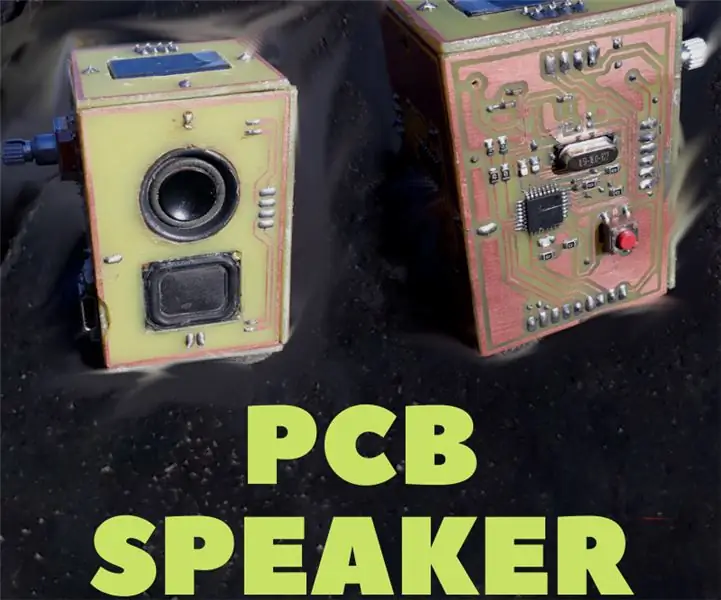
Wireless Speaker PCB: Uwielbiam tworzyć własne PCB, sprawia mi to dużo przyjemności i jeszcze bardziej lubię słuchać muzyki (moim ulubionym gatunkiem jest rap:)). Na moim biurku zawsze brakuje miejsca na narzędzia czy elementy elektroniczne, dlatego stworzyłem prototyp ti
Przeróbka głośnika audio: DIY (Made in Fusion 360): 18 kroków (ze zdjęciami)
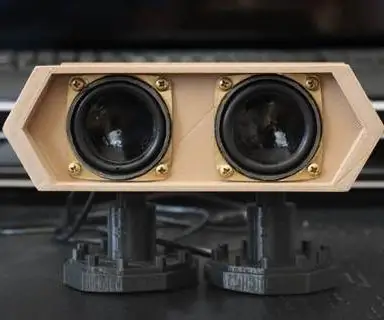
Przeróbka głośników audio: DIY (Made in Fusion 360): Mam parę głośników, które zrobiłem 2 i pół roku temu. Ale pudła głośników są niezorganizowane i zajmują dużo miejsca. Dlatego chciałbym przerobić mój głośnik audio, wykonując pudełko lub etui w druku 3D. Głośnik nadaje się tylko do komputera
Instrukcje budowania przenośnego tunelu wodnego: 18 kroków
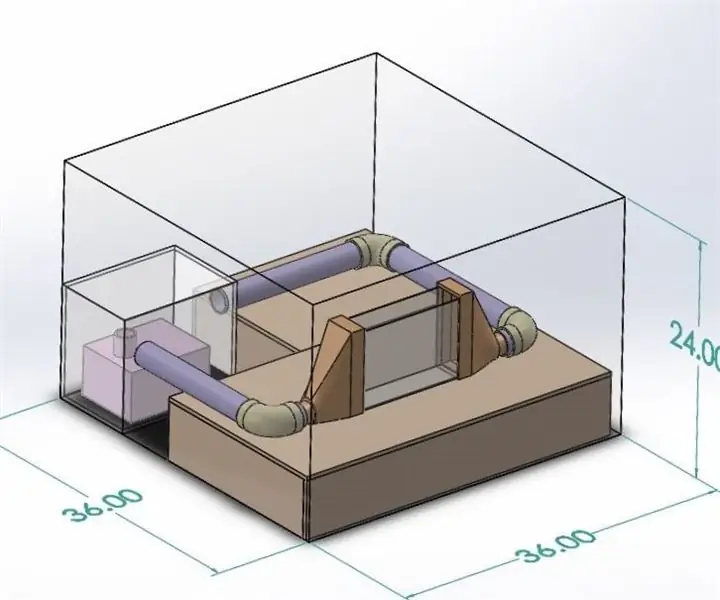
Instrukcje budowania przenośnego tunelu wodnego: Służy jako zestaw instrukcji dotyczących prawidłowego budowania tunelu wodnego do zastosowań PIV. Cechy tunelu wodnego obejmują: Widoczny odcinek testowy Stabilny przepływ wody, który można regulować za pomocą regulatora Prostownica przepływu Projekt
Instrukcja obsługi tunelu wodnego: 5 kroków
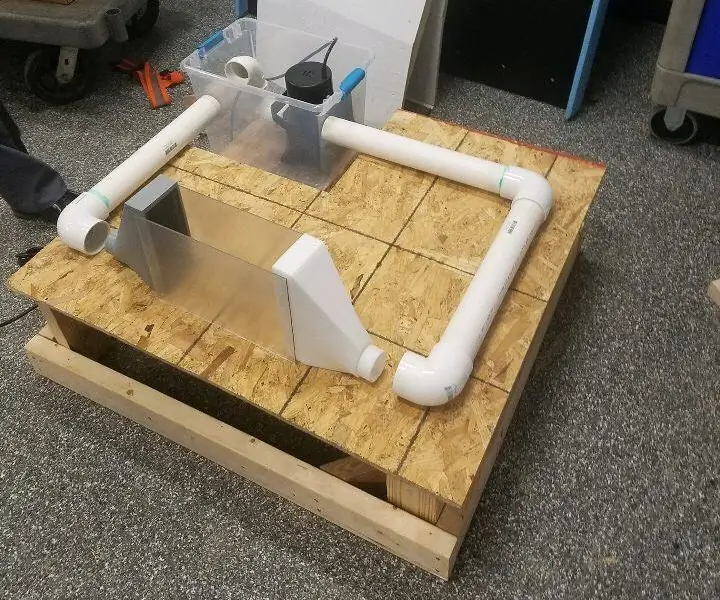
Instrukcja obsługi tunelu wodnego: Służy jako zestaw instrukcji obsługi tunelu wodnego Aquatic Solution. Wymienione instrukcje dotyczą nominalnej i najbezpieczniejszej wydajności