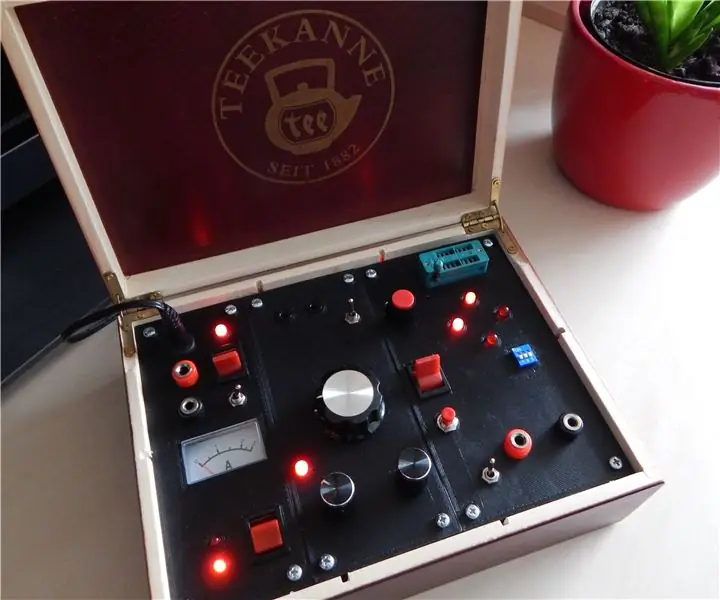
Spisu treści:
- Krok 1: Teoria sterowania prądem stałym i krokowym
- Krok 2: Schemat obwodu
- Krok 3: Schematy
- Krok 4: Niezbędne komponenty i narzędzia
- Krok 5: Projekt panelu przedniego
- Krok 6: Drukowanie 3D i malowanie natryskowe
- Krok 7: Okablowanie panelu
- Krok 8: Złącza panelu-płyty
- Krok 9: PCB
- Krok 10: Arduino
- Krok 11: Montaż i testowanie
- Krok 12: Koniec
2025 Autor: John Day | [email protected]. Ostatnio zmodyfikowany: 2025-06-01 06:10

Kilka miesięcy temu mój przyjaciel dał mi kilka porzuconych drukarek atramentowych i kserokopiarek. Byłem zainteresowany zebraniem ich jednostek zasilających, kabli, czujników, a zwłaszcza silników. Uratowałem, co mogłem i chciałem przetestować wszystkie części, aby upewnić się, że są sprawne. Niektóre silniki były oceniane na 12 V, niektóre na 5 V, niektóre były krokowe, a inne były silnikami prądu stałego. Gdybym tylko miał urządzenie, do którego mógłbym po prostu podłączyć silnik, ustawić częstotliwość, cykl pracy i wybrać metodę krokową do przetestowania.
Postanowiłem zbudować go bez użycia cyfrowego procesora sygnałowego czy mikrokontrolera. Skromny 555 lub tl741 jako oscylator, licznik 4017 i wiele bramek logicznych dla trybów silnika krokowego. Na początku świetnie się bawiłem przy projektowaniu układu, a także przy projektowaniu panelu przedniego urządzenia. Znalazłem porządne drewniane pudełko na herbatę, aby wszystko włożyć do środka. Podzieliłem obwód na cztery części i zacząłem testować go na płytce prototypowej. Wkrótce pojawiły się pierwsze oznaki frustracji. To był bałagan. Dużo bramek, dużo układów scalonych, przewodów. Nie działał poprawnie i myślałem między dwiema opcjami: Żeby było to bardzo proste - tylko dla silników prądu stałego, albo odłóż to na bok i dokończ czasami później… wybrałem drugą opcję.
Krok 1: Teoria sterowania prądem stałym i krokowym
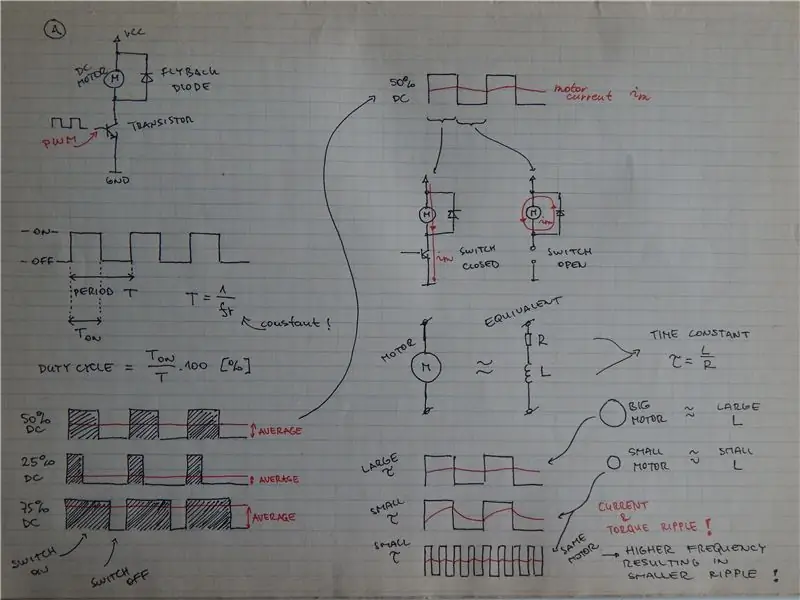
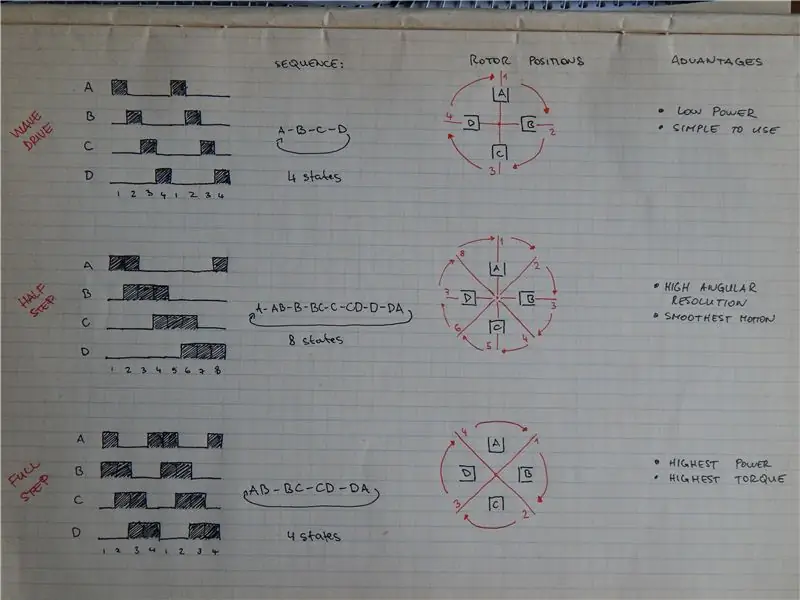
Silnik prądu stałego
Najpopularniejszym sposobem sterowania silnikiem prądu stałego jest tak zwana modulacja szerokości impulsu (PWM). PWM jest stosowany do określonego przełącznika i włącza i wyłącza silnik. Na rysunku widać wskazany okres przełączania i jego związek z częstotliwością, wskazany jest również czas przełączania. Cykl pracy jest definiowany jako czas przełączania podzielony przez całkowity okres. Jeśli utrzymamy stałą częstotliwość, jedynym sposobem na zmianę cyklu pracy jest zmiana na czas. Zwiększając cykl pracy, wzrasta również średnia wartość napięcia przyłożonego do silnika. Ze względu na wyższe napięcie przez silnik prądu stałego przepływa wyższy prąd, a wirnik obraca się szybciej.
Ale jaką częstotliwość wybrać? Aby odpowiedzieć na to pytanie, przyjrzyjmy się bliżej, czym właściwie jest silnik prądu stałego. Równoważnie można go opisać jako filtr RL (pomijając tylko na chwilę EMF). Jeśli do silnika zostanie przyłożone napięcie (filtr RL), prąd wzrasta ze stałą czasową tau równą L / R. W przypadku sterowania PWM, gdy przełącznik jest zamknięty, prąd płynący przez silnik wzrasta i zmniejsza się w czasie, gdy przełącznik jest wyłączony. W tym momencie prąd ma ten sam kierunek co poprzednio i przepływa przez diodę flyback. Silniki o większej mocy mają wyższą indukcyjność, a tym samym wyższą stałą czasową niż mniejsze silniki. Jeśli częstotliwość jest niska, gdy mały silnik jest zasilany, następuje gwałtowny spadek prądu w czasie wyłączania, a następnie duży wzrost w czasie włączania. To tętnienie prądu powoduje również tętnienie momentu obrotowego silnika. Nie chcemy tego. Dlatego przy zasilaniu mniejszych silników częstotliwość PWM powinna być wyższa. Wiedzę tę wykorzystamy przy projektowaniu w kolejnych krokach.
Silnik krokowy
Jeśli chcemy sterować jednobiegunowym silnikiem krokowym, stosowanym w elektronice hobbystycznej, mamy do wyboru 3 podstawowe opcje sterowania (tryby) - Wave drive (WD), Half Step (HS) i Full Step (FS). Kolejność poszczególnych trybów oraz położenie wirnika jest wskazane na rysunku (dla uproszczenia wskazałem silnik z dwiema parami biegunów). W tym przypadku Wave Drive i Full Step powodują obrót wirnika o 90 stopni i można to osiągnąć powtarzając 4 stany. W trybie Half Step potrzebujemy sekwencji 8 stanów.
Wybór trybu zależy od wymagań systemu - jeśli potrzebujemy dużego momentu obrotowego, najlepszym wyborem jest Full Step, jeśli wystarczy niższy moment obrotowy i może zasilamy nasz układ z akumulatora preferowany jest tryb wave drive. W zastosowaniach, w których zależy nam na osiągnięciu najwyższej rozdzielczości kątowej i płynnym ruchu, tryb Half Drive jest idealnym wyborem. Moment obrotowy w tym trybie jest o około 30% niższy niż w trybie Full Drive.
Krok 2: Schemat obwodu
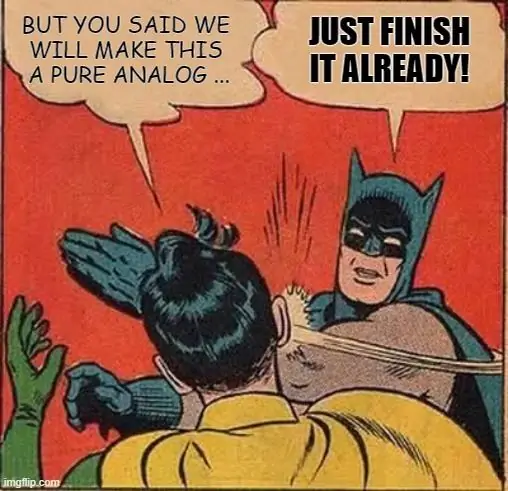
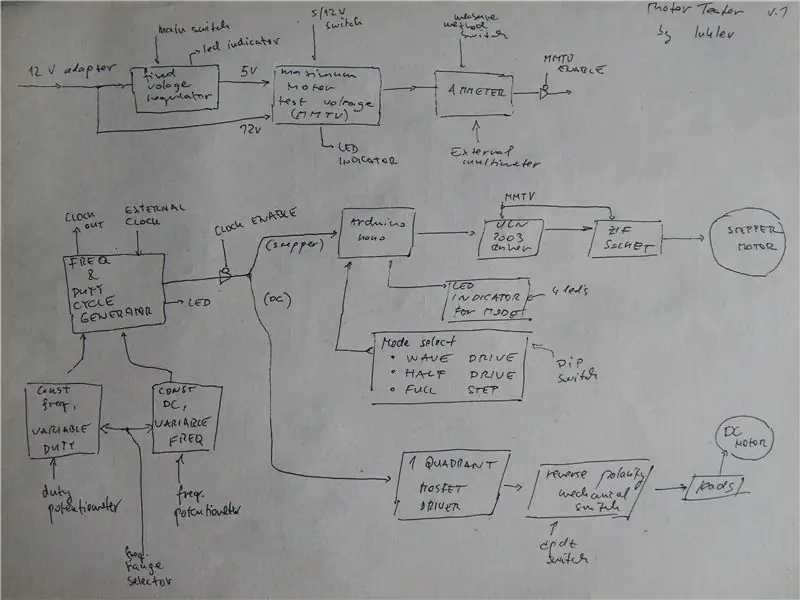
Ten prosty mem trafnie opisuje mój proces myślenia podczas projektowania.
Górna część schematu opisuje zasilacz - adapter 12 woltów, który jest redukowany do 5 woltów za pomocą regulatora liniowego. Chciałem mieć możliwość wyboru maksymalnego napięcia testowego silnika (MMTV) - 12 lub 5 woltów. Wbudowany amperomierz omija obwody sterujące i mierzy tylko prąd silnika. Wygodna byłaby również możliwość przełączania między wewnętrznym i zewnętrznym pomiarem prądu za pomocą multimetru.
Oscylator będzie działał w dwóch trybach: pierwszy to stała częstotliwość i zmienny cykl pracy, a drugi to zmienna częstotliwość. Oba te parametry będzie można ustawić za pomocą potencjometrów, a jeden przełącznik obrotowy będzie przełączał tryby i zakresy. W systemie znajdzie się również przełącznik między zegarem wewnętrznym a zewnętrznym poprzez złącze jack 3,5 mm. Zegar wewnętrzny zostanie również podłączony do panelu za pomocą złącza jack 3,5 mm. Jeden przełącznik i przycisk do włączania/wyłączania zegara. Sterownik silnika prądu stałego będzie pojedynczym kwadrantowym N-kanałowym sterownikiem mosfet. Kierunek zostanie zmieniony za pomocą mechanicznego przełącznika dpdt. Przewody silnika zostaną podłączone przez gniazda bananowe.
Sekwencja silnika krokowego będzie kontrolowana przez arduino, które również rozpozna 3 tryby sterowania określone przez przełącznik DIP. Sterownik silnika krokowego będzie uln2003. Arduino będzie również sterować 4 diodami LED, które będą reprezentować animację zasilanych uzwojeń silnika w tych trybach. Silnik krokowy zostanie podłączony do testera poprzez gniazdo ZIF.
Krok 3: Schematy
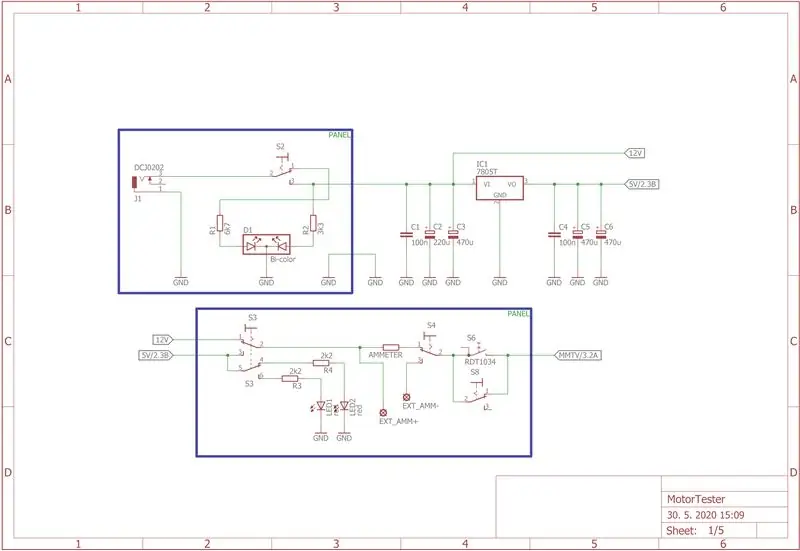
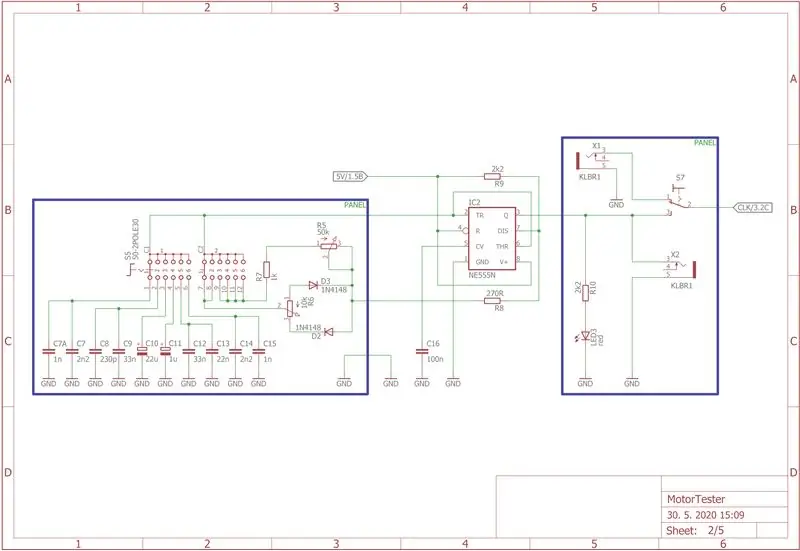
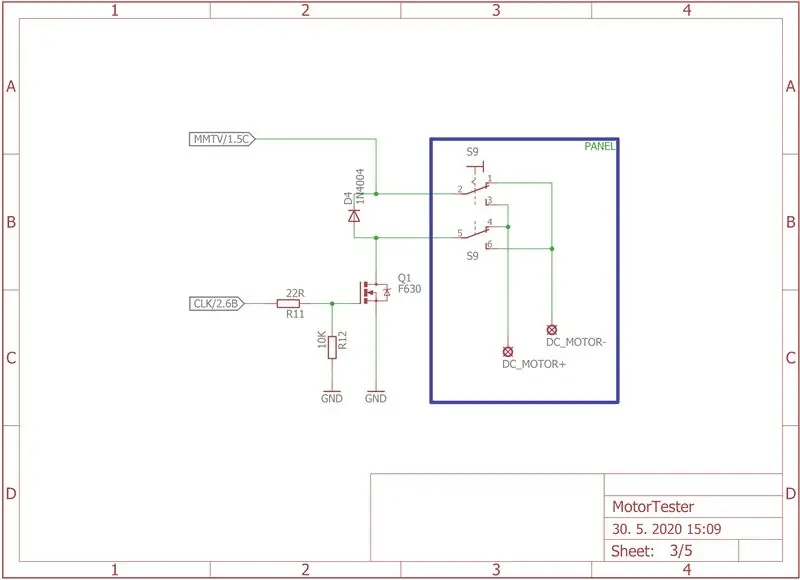
Schematy podzielone są na pięć części. Obwody obramowane niebieskimi ramkami reprezentują komponenty, które znajdą się na panelu.
- Zasilacz
- Oscylator
- Sterownik prądu stałego
- Sterownik krokowy Arduino
- Sterownik krokowy bramek logicznych
Arkusz nr. 5 to powód, dla którego zostawiłem ten projekt kłamliwy. Obwody te tworzą sekwencje dla wcześniej wspomnianych trybów sterowania - WD, HS i FS. Ta część jest zastąpiona przez arduino w całości w arkuszu nr. 4. Załączony jest również kompletny schemat Eagle.
Krok 4: Niezbędne komponenty i narzędzia

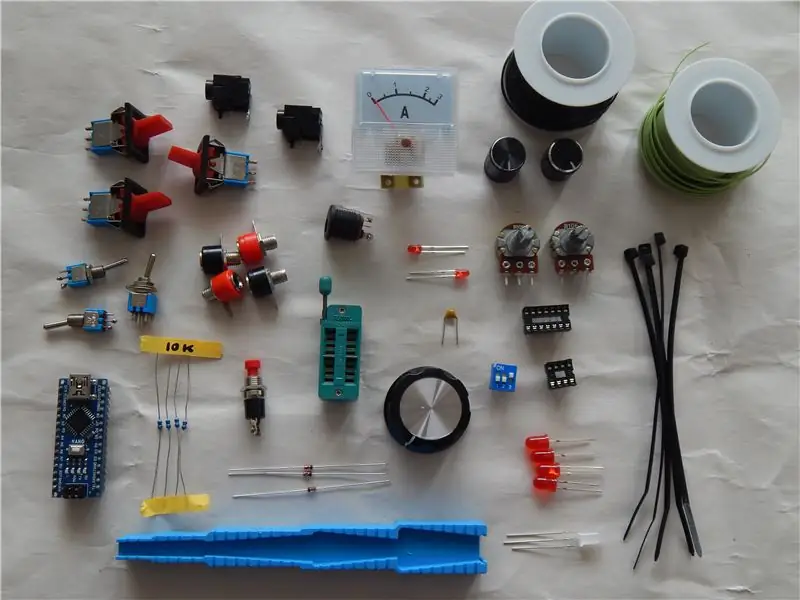
Niezbędne komponenty i narzędzia:
- Multimetr
- Suwmiarka
- Gilotyna do tektury
- Znacznik
- Pinceta
- Szczypce drobne
- Szczypce do cięcia
- Szczypce do ściągania izolacji
- Lutownica
- Lutować
- Kolofonia
- Przewody (24 awg)
- 4x przełącznik spdt
- 2x przełącznik dpdt
- 4x wtyk bananowy
- Naciśnij przycisk
- Gniazdo ZIF
- 2x gniazdo 3,5 mm
- Złącze prądu stałego
- Arduino nano
- 3-biegunowy przełącznik DIP
- 2x 3mm LED
- 5x 5mm LED
- Dwukolorowa dioda LED
- Pokrętła potencjometrów
- Gniazda DIP
- Uniwersalna płytka drukowana
- Złącza dupontowe
- Plastikowe opaski kablowe
I
- Potencjometry
- Rezystory
- Kondensatory
z wybranymi wartościami, odpowiadającymi zakresom częstotliwości i jasności diod LED.
Krok 5: Projekt panelu przedniego
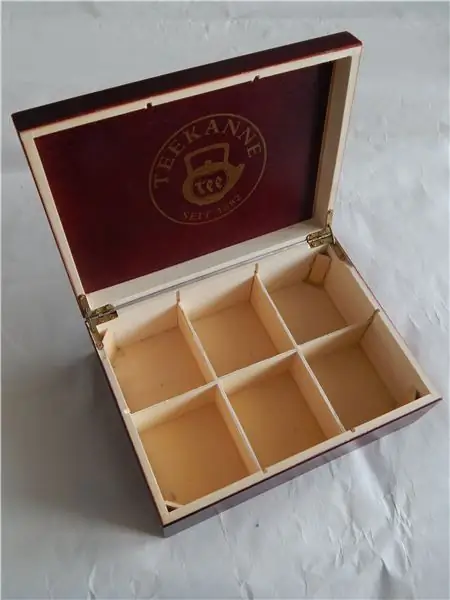
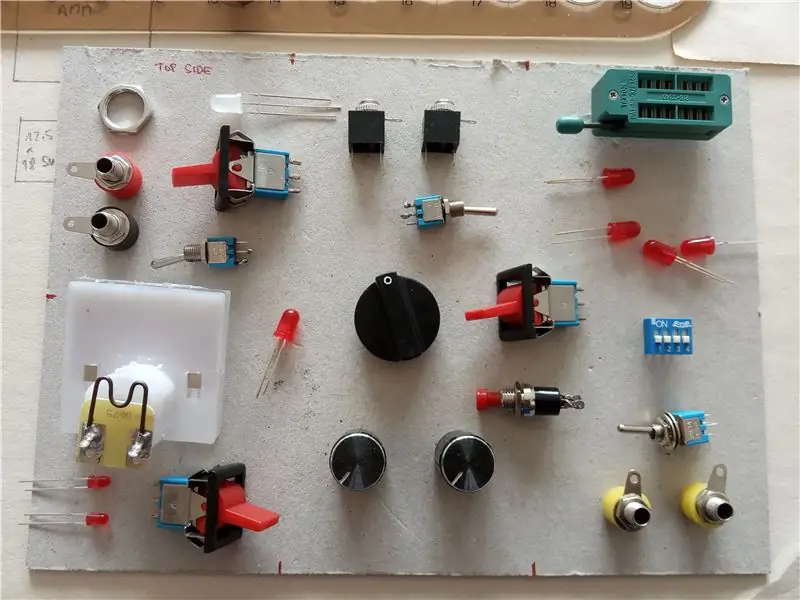
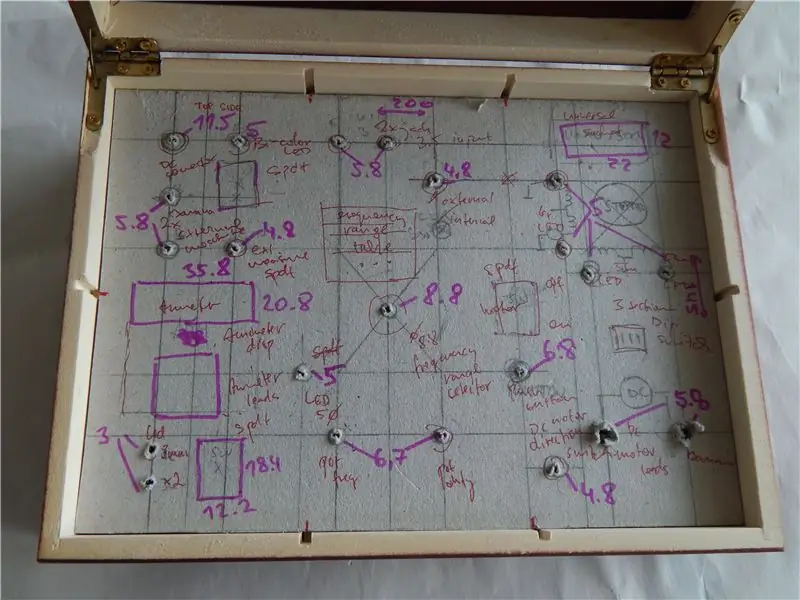
Tester został umieszczony w starym drewnianym pudełku po herbacie. Najpierw zmierzyłem wymiary wewnętrzne, a następnie z twardego kartonu wyciąłem prostokąt, który posłużył jako szablon do rozmieszczenia elementów. Kiedy byłem zadowolony z rozmieszczenia części, ponownie zmierzyłem każdą pozycję i stworzyłem projekt panelu w Fusion360. Panel podzieliłem na 3 mniejsze części, dla uproszczenia w druku 3D. Zaprojektowałem również uchwyt w kształcie litery L do mocowania paneli po wewnętrznej stronie pudełka.
Krok 6: Drukowanie 3D i malowanie natryskowe
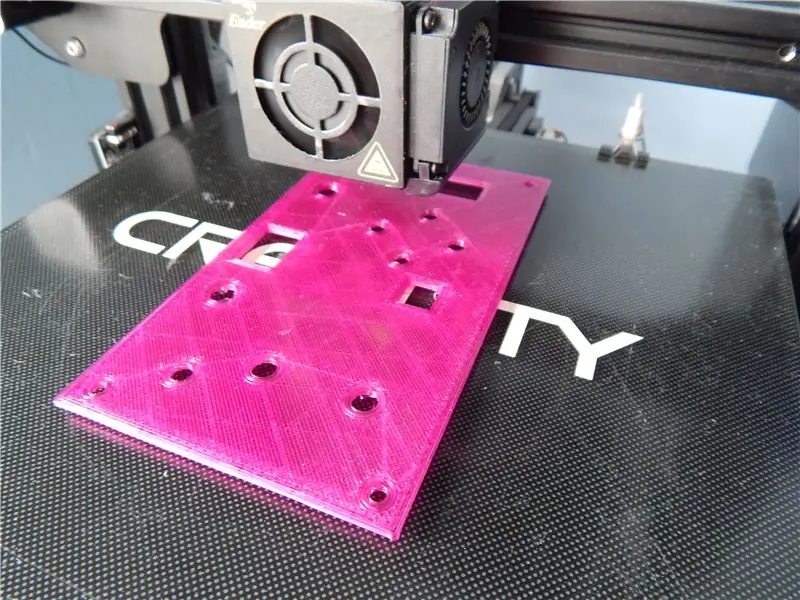
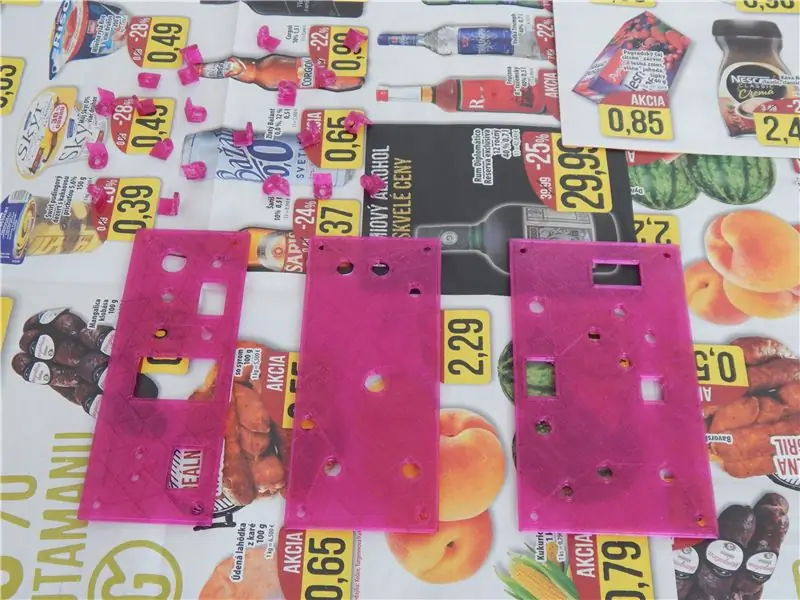
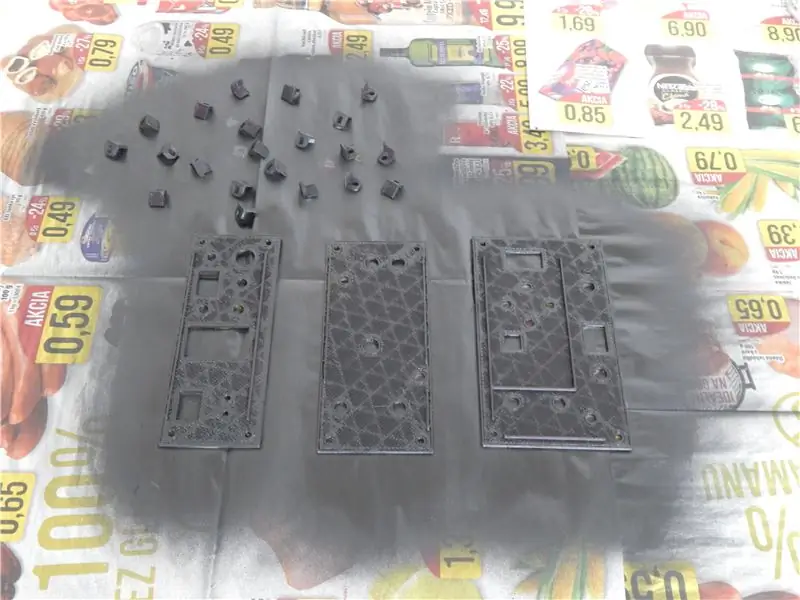
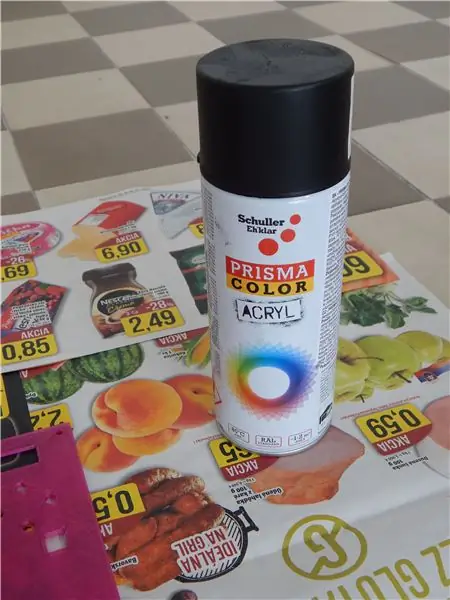
Panele wydrukowano na drukarce Ender-3, z resztek materiału, który miałem w domu. Był to przezroczysty różowy petg. Po wydrukowaniu spryskałem panele i uchwyty matową czarną farbą akrylową. Aby uzyskać pełne krycie, nałożyłam 3 warstwy, położyłam je na kilka godzin na zewnątrz do wyschnięcia i przewietrzenia przez około pół dnia. Uważaj, opary farby mogą być szkodliwe. Zawsze używaj ich tylko w wentylowanym pomieszczeniu.
Krok 7: Okablowanie panelu
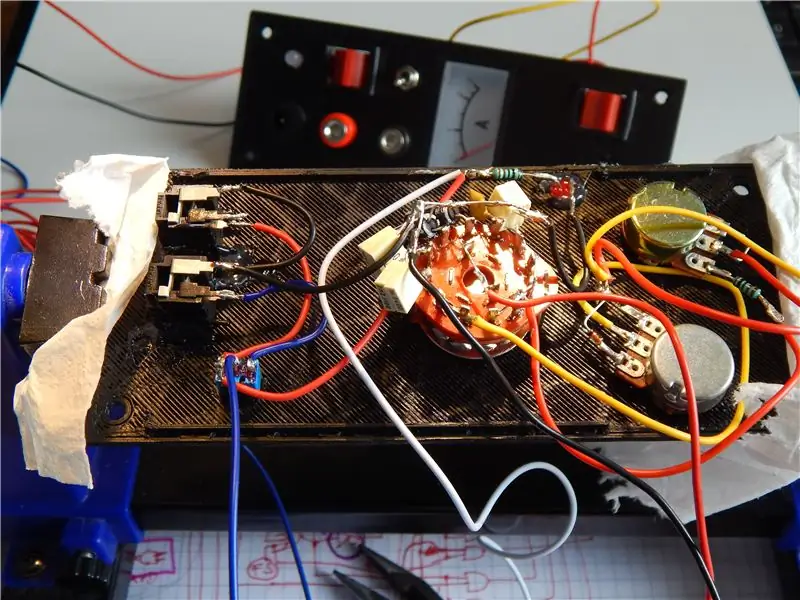
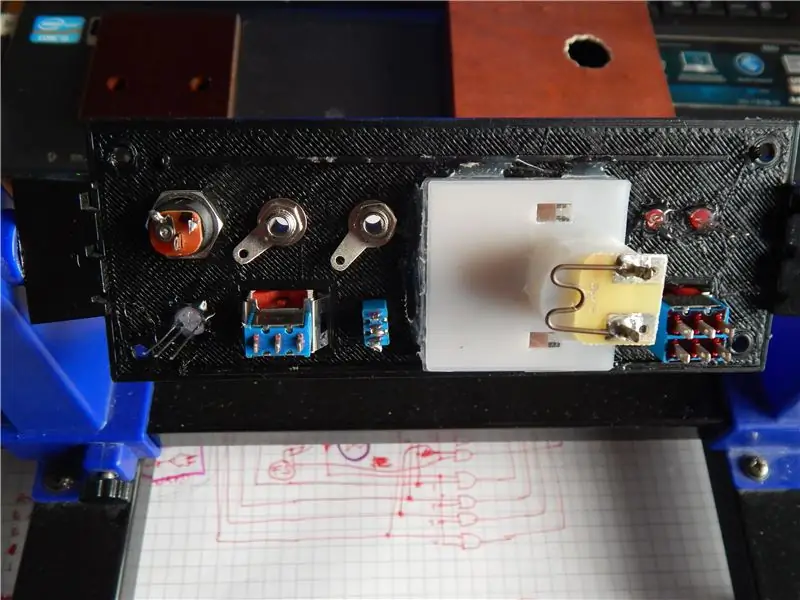
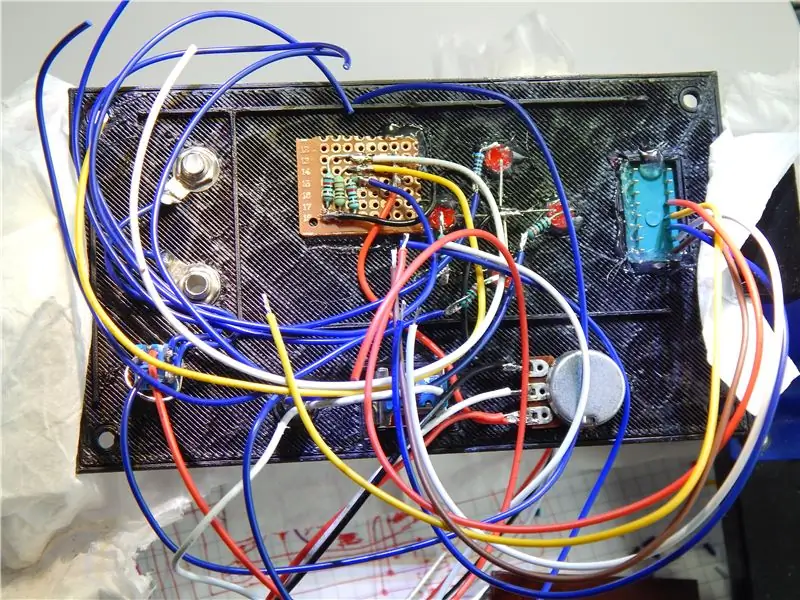
Osobiście moja ulubiona, ale najbardziej czasochłonna część (z góry przepraszam za niekorzystanie z rurek termokurczliwych, byłam w załamaniu czasu - inaczej na pewno bym z nich skorzystała).
Regulowane wsporniki bardzo pomagają podczas montażu i obsługi paneli. Możliwe jest również użycie tzw. trzeciej ręki, ale wolę uchwyt. Jej uchwyty pokryłem ściereczką tekstylną, aby panel nie został porysowany podczas pracy.
Do panelu włożyłem i przykręciłem wszystkie przełączniki i potencjometry, diody LED i inne złącza. Następnie oszacowałem długość przewodów, które połączą elementy na panelu, a także te, które będą używane do połączenia z płytką. Są one zazwyczaj nieco dłuższe i dobrze jest je nieco wydłużyć.
Do lutowania złączy prawie zawsze używam ciekłego topnika lutowniczego. Nakładam niewielką ilość na szpilkę a następnie cynę i podłączam do przewodu. Topnik usuwa z powierzchni wszelkie utlenione metale, co znacznie ułatwia lutowanie złącza.
Krok 8: Złącza panelu-płyty
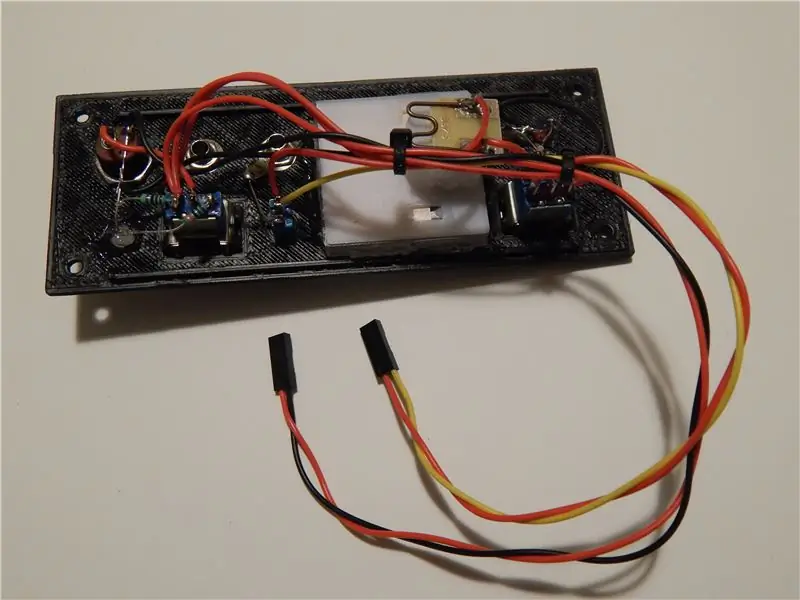
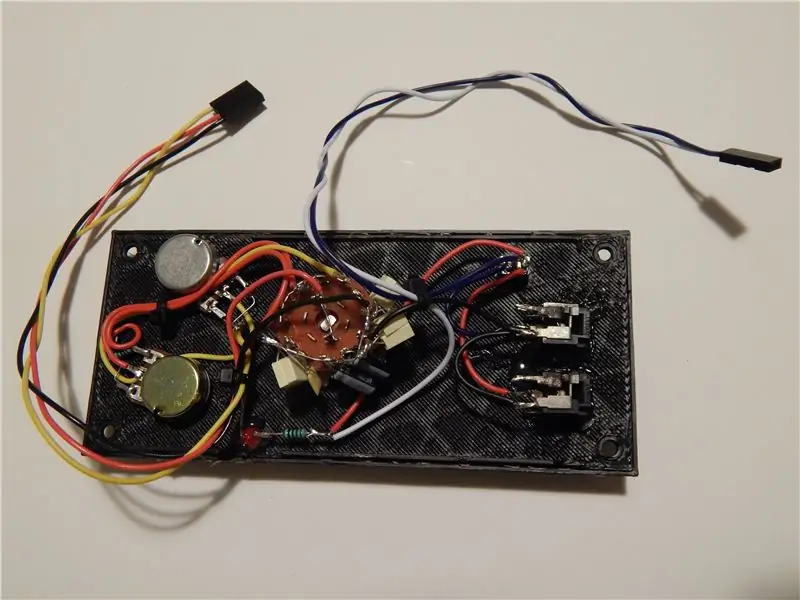
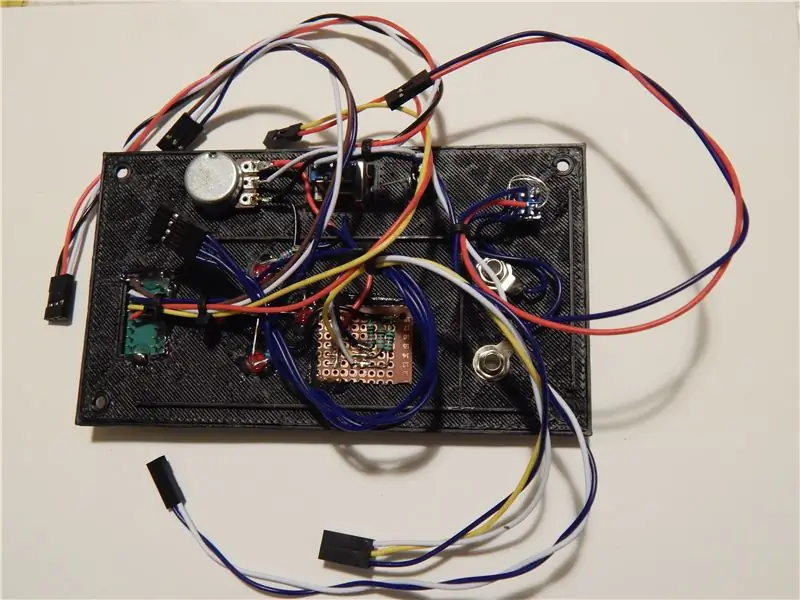
Do podłączenia panelu do płytki wykorzystałem złącza typu dupont. Są ogólnodostępne, tanie i co najważniejsze na tyle małe, by wygodnie zmieścić się w wybranym pudełku. Kable ułożone są według schematu, parami, trojaczkami lub czworokątami. Są one oznaczone kolorami, aby można je było łatwo zidentyfikować i podłączyć. Jednocześnie warto, aby przyszłość nie gubiła się w jednolitej plątaninie przewodów. Na koniec są zabezpieczone mechanicznie plastikowymi opaskami kablowymi.
Krok 9: PCB
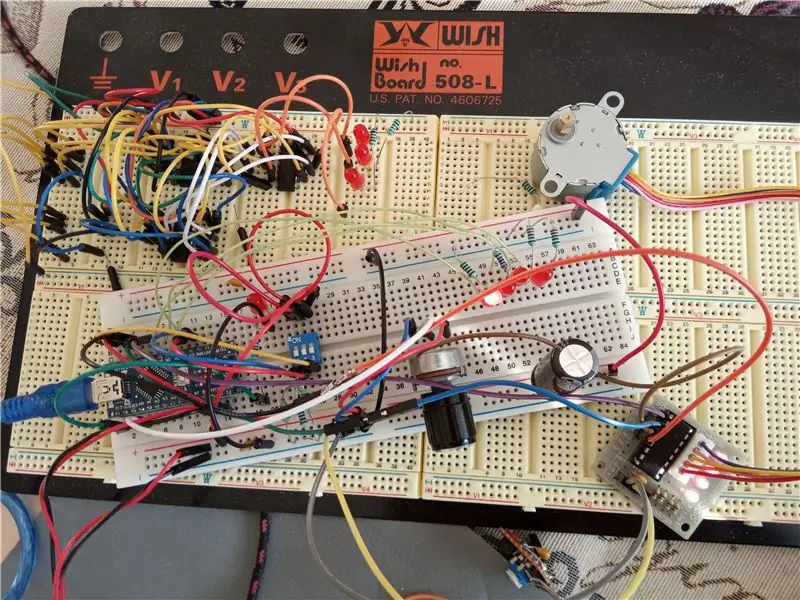
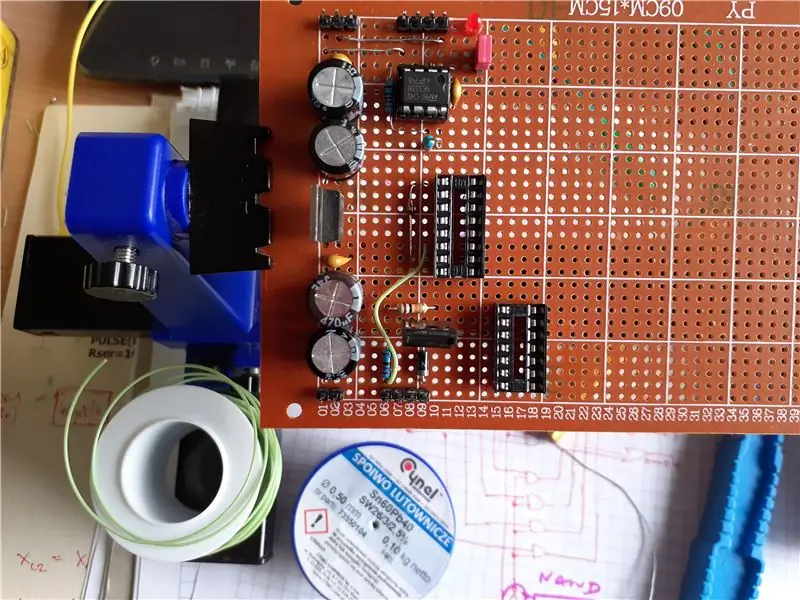
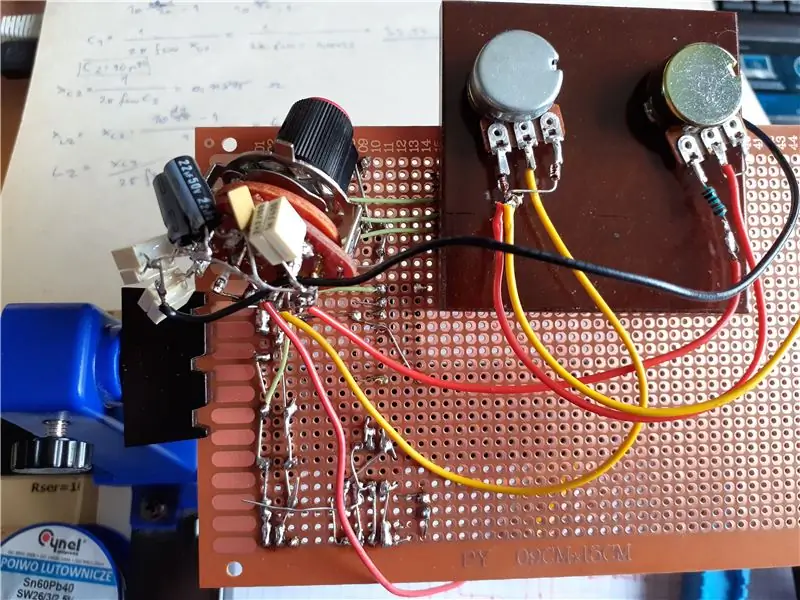
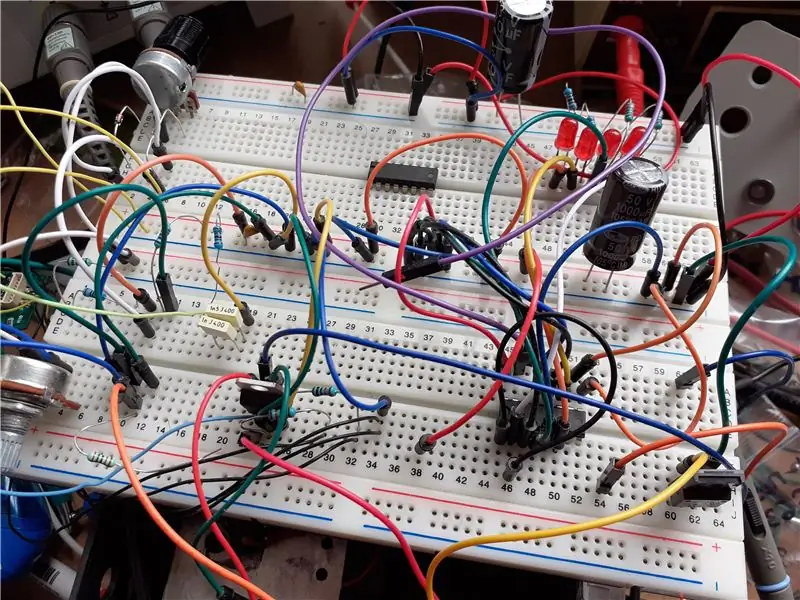
Ponieważ część schematu znajdująca się poza panelem nie jest obszerna, postanowiłem wykonać obwód na uniwersalnej płytce drukowanej. Użyłem zwykłej płytki o wymiarach 9x15 cm. Kondensatory wejściowe wraz z liniowym regulatorem i radiatorem umieściłem po lewej stronie. Następnie zainstalowałem podstawki pod licznik IC 555, 4017 oraz sterownik ULN2003. Gniazdo licznika 4017 pozostanie puste, ponieważ jego funkcję przejmuje arduino. W dolnej części znajduje się sterownik do N-kanałowego mosfeta F630.
Krok 10: Arduino
Połączenie systemu z arduino udokumentowane jest w arkuszu schematów nr. 4. Zastosowano następujący układ kołków:
- 3 wejścia cyfrowe dla przełączników DIP - D2, D3, D12
- 4 wyjścia cyfrowe dla wskaźników LED - D4, D5, D6, D7
- 4 wyjścia cyfrowe dla sterownika krokowego - D8, D9, D10, D11
- Jedno wejście analogowe dla potencjometru - A0
Wskaźniki LED reprezentujące poszczególne uzwojenia silnika zapalają się powoli, gdy uzwojenia są faktycznie zasilane. Gdyby prędkość migania diod LED odpowiadała uzwojeniom silnika, zobaczylibyśmy to jako ciągłe oświetlenie ich wszystkich. Chciałem uzyskać przejrzystą, prostą reprezentację i różnice między poszczególnymi trybami. Dlatego wskaźniki LED są sterowane niezależnie w odstępach 400 ms.
Funkcje sterowania silnikiem krokowym stworzył autor Cornelius na swoim blogu.
Krok 11: Montaż i testowanie
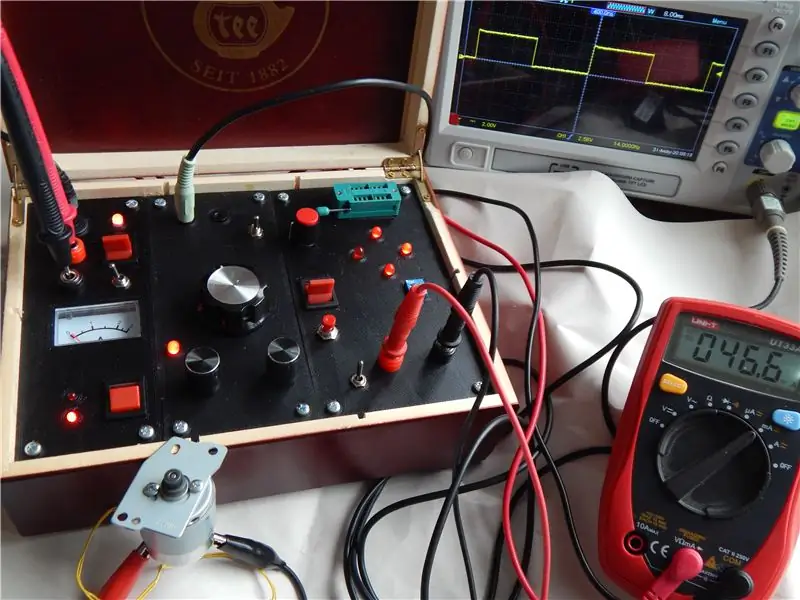
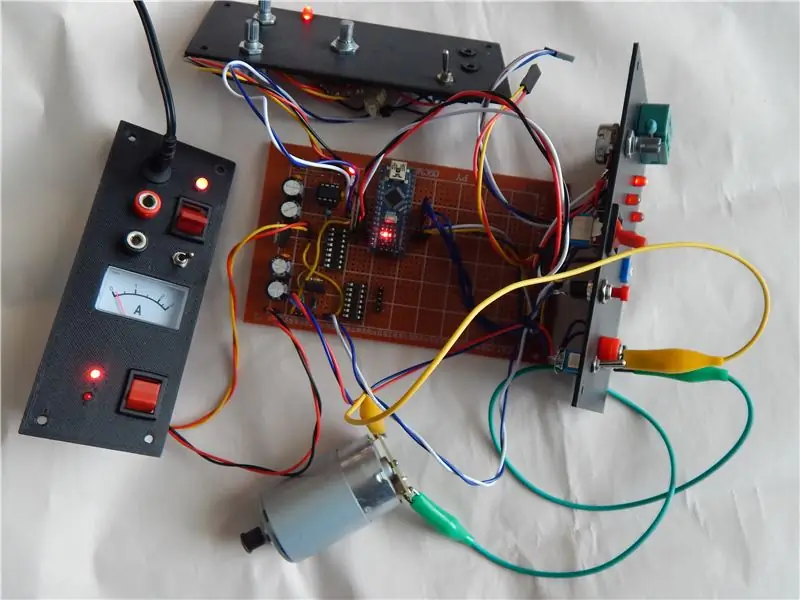
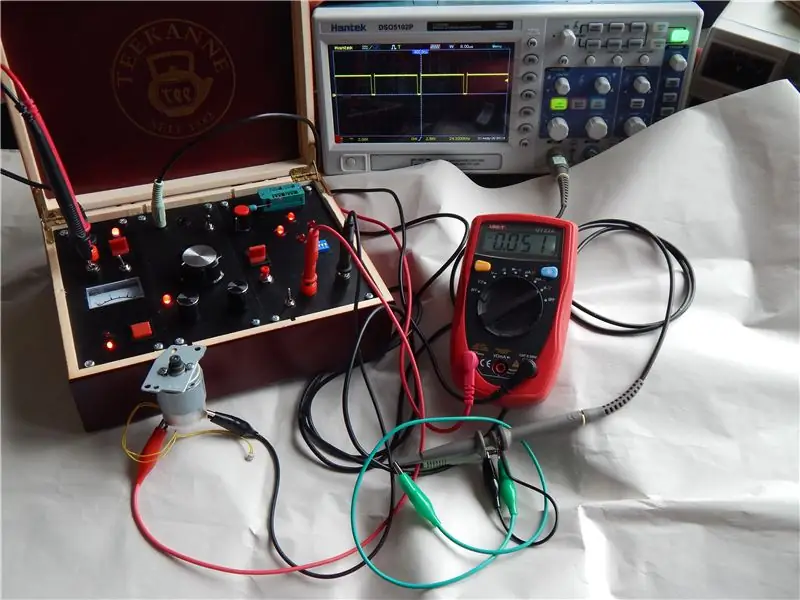
W końcu podłączyłem wszystkie panele do płytki i zacząłem testować tester. Zmierzyłem oscylator i jego zakresy za pomocą oscyloskopu, a także kontrolę częstotliwości i współczynnika wypełnienia. Nie miałem większych problemów, jedyną zmianą, jaką wprowadziłem, było dodanie kondensatorów ceramicznych równolegle do wejściowych kondensatorów elektrolitycznych. Dodany kondensator zapewnia tłumienie zakłóceń o wysokiej częstotliwości wprowadzanych do systemu przez pasożytnicze elementy kabla zasilacza DC. Wszystkie funkcje testera działają zgodnie z wymaganiami.
Krok 12: Koniec
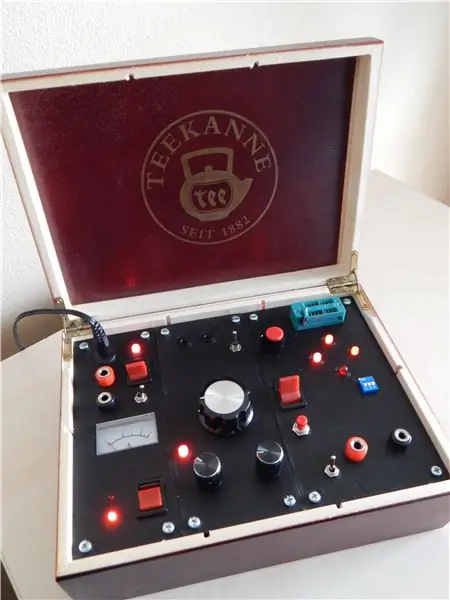
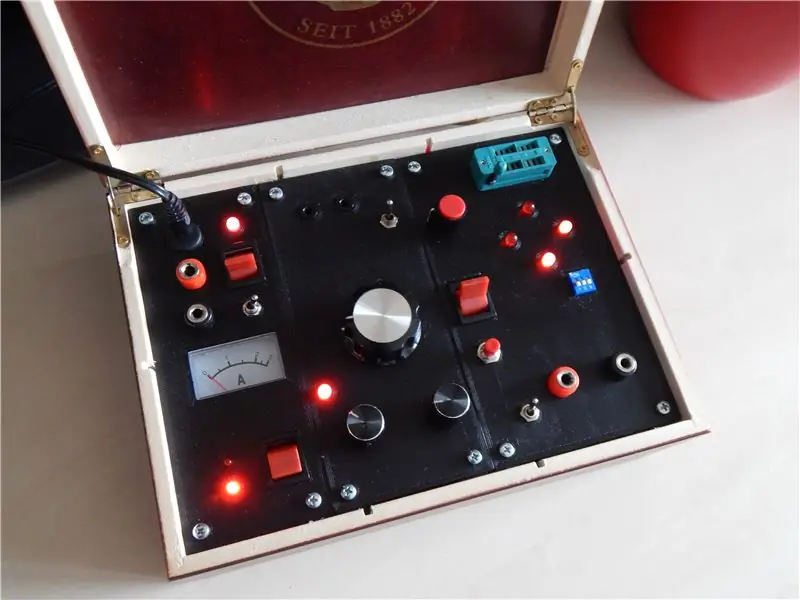
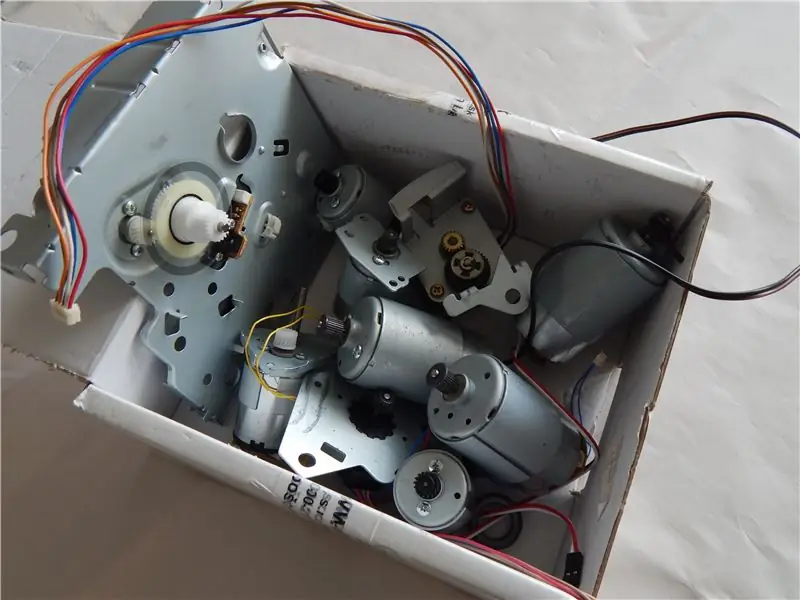
Teraz mogę w końcu po prostu przetestować wszystkie silniki, które udało mi się uratować przez lata.
Jeśli jesteś zainteresowany teorią, schematem lub czymkolwiek na temat testera, nie wahaj się ze mną skontaktować.
Dziękuję za przeczytanie i poświęcony czas. Bądź zdrowy i bezpieczny.
Zalecana:
Korzystanie z więcej niż 4 silników - układanie wielu osłon silnika: 3 kroki
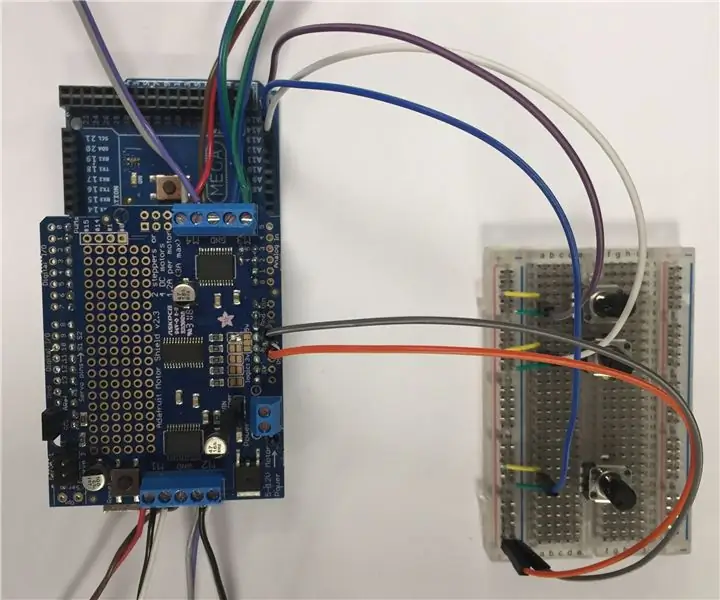
Korzystanie z więcej niż 4 silników - układanie wielu osłon silnikowych: instruktażowe urządzenie do wibrodotykowej substytucji i wzmacniania sensorycznego wkład w bodźce wibracyjne. Te bodźce wibracyjne są p
Prowadzenie małych silników za pomocą TB6612FNG: 8 kroków
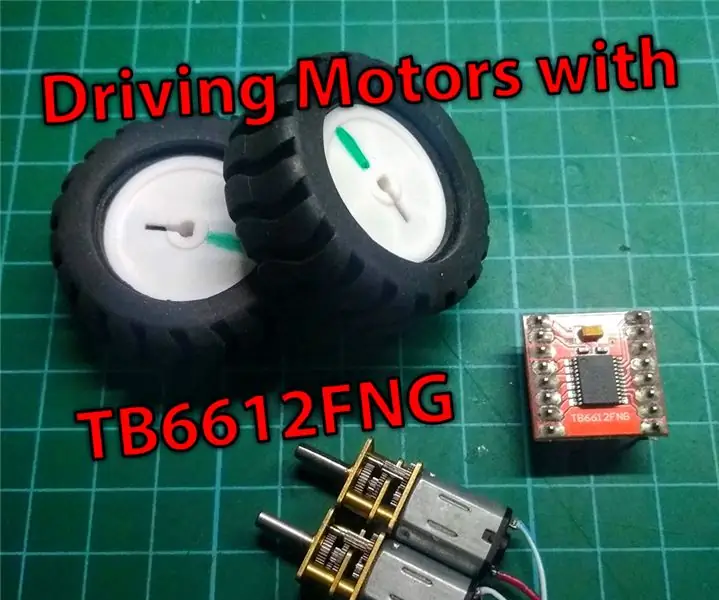
Napędzanie małych silników za pomocą TB6612FNG: TB6612FNG to układ scalony sterownika podwójnego silnika firmy Toshiba. Istnieje wiele tablic zaciskowych i jest to jeden z najpopularniejszych wyborów do napędzania małych silników. Istnieje wiele zasobów online, jak zacząć korzystać z TB6612FNG b
Co zrobić z losowymi kolekcjami silników: Projekt 2: Wirujące światła (model UFO): 12 kroków (ze zdjęciami)
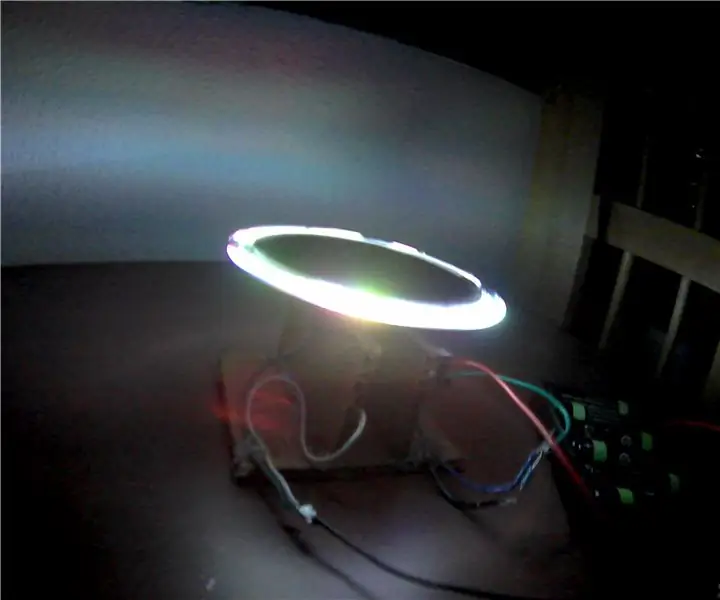
Co zrobić z kolekcjami losowych silników: Projekt 2: Wirujące światła (model UFO): Więc nadal mam kolekcję losowych silników… Co mam zrobić? Cóż, pomyślmy. Co powiesz na spinner LED? (Nie trzymane w ręku, przepraszam miłośników fidget spinner.) Wygląda trochę jak UFO, brzmi jak mieszanka chwastów i blendera
Korzystanie z silników z układem scalonym L293D: 6 kroków (ze zdjęciami)
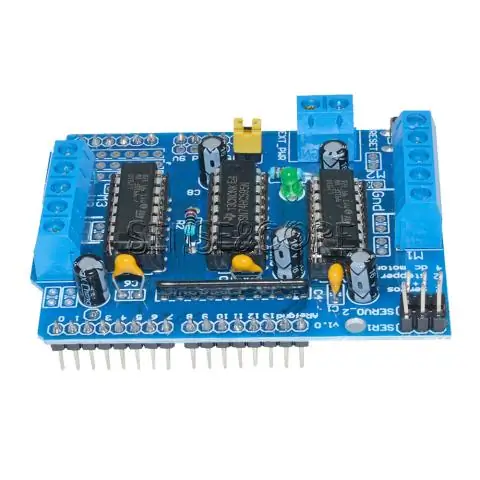
Używanie silników z układem scalonym L293D: Jest to krótki przewodnik z kilkoma dodatkowymi informacjami (konfiguracje pinów itp.), których nauczyłem się po drodze, jak używać L293D z Arduino, pokazując, że możemy: A) Używać dodatkowe źródło zasilania do zasilania silnika prądu stałego.B) Użyj L293D c
Tester pojemności akumulatora litowo-jonowego (tester mocy litowej): 5 kroków
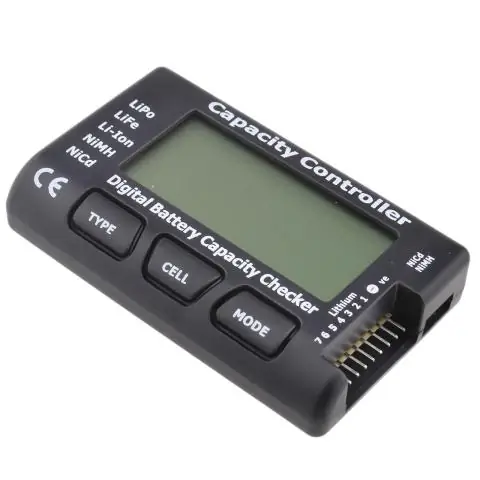
Tester pojemności akumulatora litowo-jonowego (tester mocy litu): =========== OSTRZEŻENIE & ZASTRZEŻENIE ==========Baterie litowo-jonowe są bardzo niebezpieczne, jeśli nie są obsługiwane prawidłowo. NIE NALEŻY PRZEŁADOWAĆ/PALIĆ/OTWIERAĆ Baterie litowo-jonoweWszystko, co robisz z tymi informacjami, to Twoje własne ryzyko====== ======================================