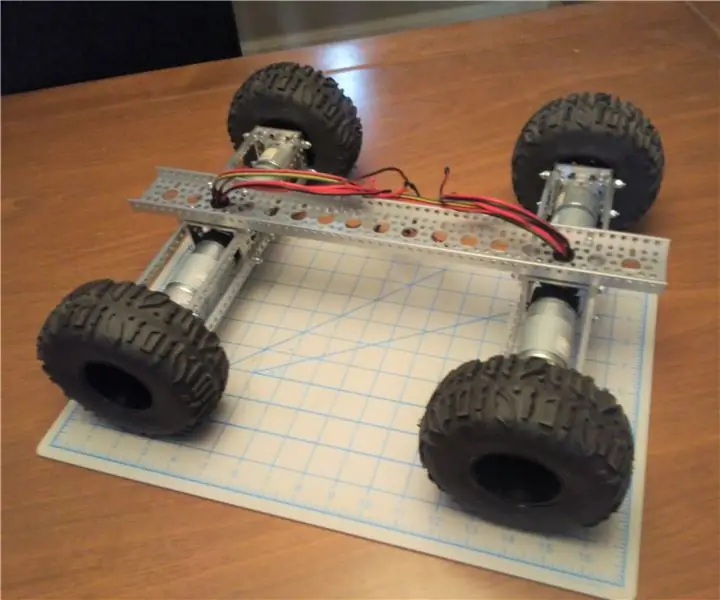
Spisu treści:
- Kieszonkowe dzieci
- Krok 1: Podstawowy zestaw narzędzi
- Krok 2: Zbuduj klatki silnika
- Krok 3: Dodaj kręgosłup
- Krok 4: Dodaj mocowania silnika do silników
- Krok 5: Podłącz silniki
- Krok 6: Przymocuj piastę koła do wału silnika
- Krok 7: Złóż koła
- Krok 8: Śruba na kołach
- Krok 9: Opcje dla ciała
- Krok 10: Dodawanie elektroniki
2025 Autor: John Day | [email protected]. Ostatnio zmodyfikowany: 2025-06-01 06:10
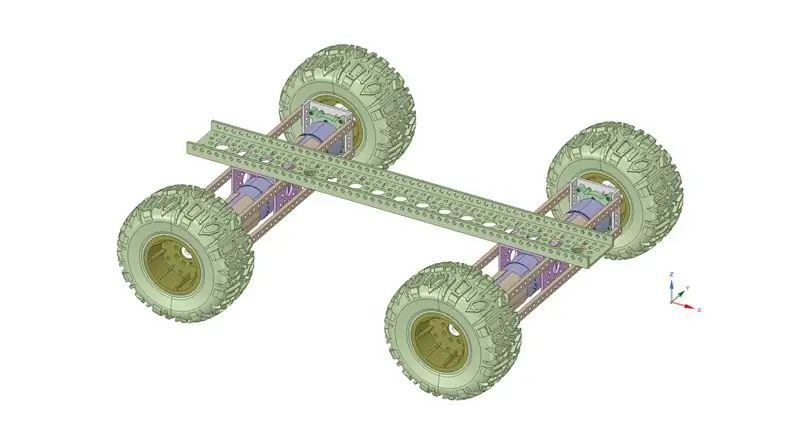
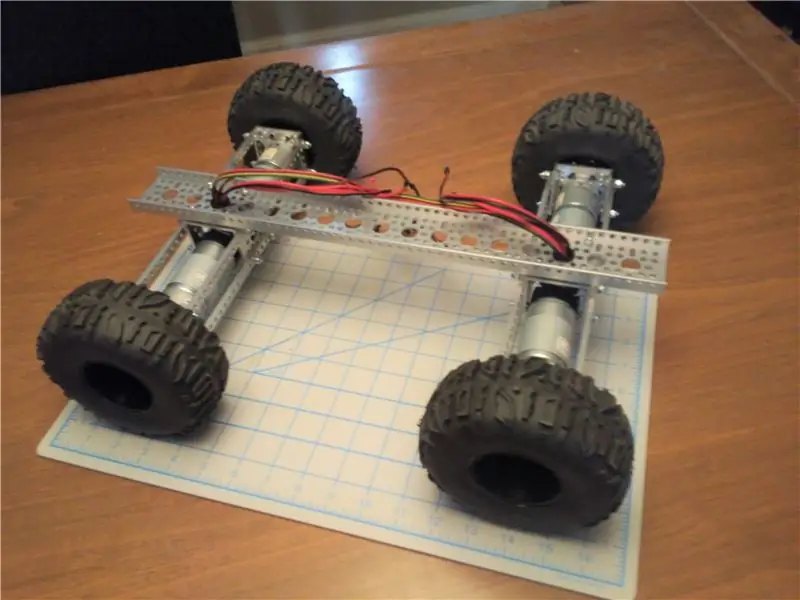
Pokażę wam, jak zbudowałem podwozie RC lub autonomicznego łazika przy użyciu komponentów goBILDA. Dodam tutaj, że nie mam żadnego związku z goBILDA poza tym, że jestem w większości zadowolonym klientem.
Poniżej zamieściłem pełną listę części w sekcji Materiały eksploatacyjne, ale na każdym kroku wymienię dokładnie to, czego potrzebujesz.
Na koniec pokażę kilka sposobów na dodanie struktury do szkieletu i dodam kilka ogólnych komentarzy na temat elektroniki napędu silnika.
Kieszonkowe dzieci
Możesz kupić te części na
Rama
- 1 x 1121 kanał typu U z dolnym bokiem (17 otworów, długość 432 mm)
- Płaska belka z serii 4 × 1102 (29 otworów, długość 232 mm) - 2 sztuki
- Kanał U 2 × 1120 (1 otwór, długość 48 mm)
- 4 × 1121 kanał typu U z dolnym bokiem (1 otwór, długość 48 mm)
Pociąg napędowy
- Seria 4 × 5201, stosunek 53:1, silnik z przekładnią czołową 105 obr./min z enkoderem
- Mocowanie silnika z gwintem czołowym 4 × 1701 (16-3)
- 4 × 1310 Series Hyper Hub (6 mm otwór D)
- 2 × 3605 Obręcze Hurricane - 2 sztuki
- 2 × 3609 Series Cougar Tire - 2 szt.
Sprzęt komputerowy
- Klucz płasko-oczkowy 1 × 7mm
- Klucz sześciokątny 1 × 3 mm;
- Klucz sześciokątny 1 × 2,5 mm
- 1 × Wkręt z łbem kulistym ze stali ocynkowanej serii 2802 (M4 x 0,7 mm, długość 8 mm) - 25 szt.
- 2 × wkręty z łbem kulistym ze stali ocynkowanej serii 2802 (M4 x 0,7 mm, długość 14 mm) - 25 szt.
- Podkładka ze stali ocynkowanej 2 × 2801 (4 mm ID x 8 mm OD) - 25 szt.
- 2× Nakrętka zabezpieczająca ze stali ocynkowanej serii 2812 z wkładką nylonową (M4 x 0,7 mm, sześciokąt 7 mm) - opakowanie 25 szt.
- Wkręt z łbem gniazdowym ze stali ocynkowanej 1 × 2800 (M4 x 0,7 mm, długość 12 mm) - 25 szt.
- 1 × Podkładka dzielona ze stali ocynkowanej serii 2809 (4mm ID x 7mm OD) - 25 sztuk
- 1 × nakrętka sześciokątna ze stali ocynkowanej serii 2811 (M4 x 0,7 mm, sześciokąt 7 mm) - 25 szt.
- 1 × plastikowa przelotka (14-1) - 12 szt.
- 1 × gumowa przelotka (14-2) - 12 paczek
Krok 1: Podstawowy zestaw narzędzi
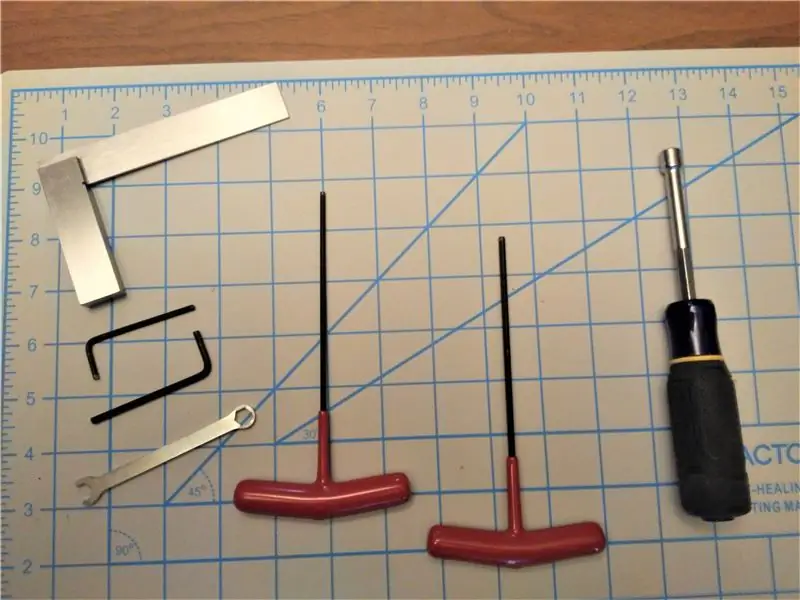
To jedyne narzędzia, których naprawdę potrzebujesz.
- Plac. Dobrze jest mieć kwadrat maszynisty, ale tak naprawdę każdy kwadrat, nawet plastikowy, jest lepszy niż brak kwadratu.
- Klucze imbusowe 2,5 i 3 mm oraz klucz 7 mm od goBILDA. Znajdują się one na liście części. Jeśli masz już zestaw metrycznych kluczy szesnastkowych, nie potrzebujesz ich. Ale nawet jeśli masz fajny zestaw metrycznych kluczy płasko-oczkowych, kup ten cienki od goBILDA.
- Uchwyty sześciokątne 2,5 i 3 mm. Uchwyt w kształcie litery T może się obracać lub obracać w sposób, w jaki żaden śrubokręt nigdy tego nie zrobi. Może również zastosować dodatkowy moment obrotowy, którego potrzebujesz do niektórych części, takich jak piasty zaciskowe, których używamy do kół.
- Klucz nasadowy 7mm. Uzyskaj rodzaj, którego używają profesjonaliści, jak pokazano. Potrzebujesz tego samego momentu obrotowego, co oni.
Prawdopodobnie można by to wszystko złożyć razem z trzema narzędziami goBILDA, ale nie byłoby to zbyt zabawne. Generalnie używamy klucza imbusowego do przytrzymywania śruby maszynowej podczas dokręcania nakrętki kluczem do nakrętek, a klucza do przytrzymywania nakrętki podczas dokręcania śruby za pomocą uchwytu T.
Krok 2: Zbuduj klatki silnika
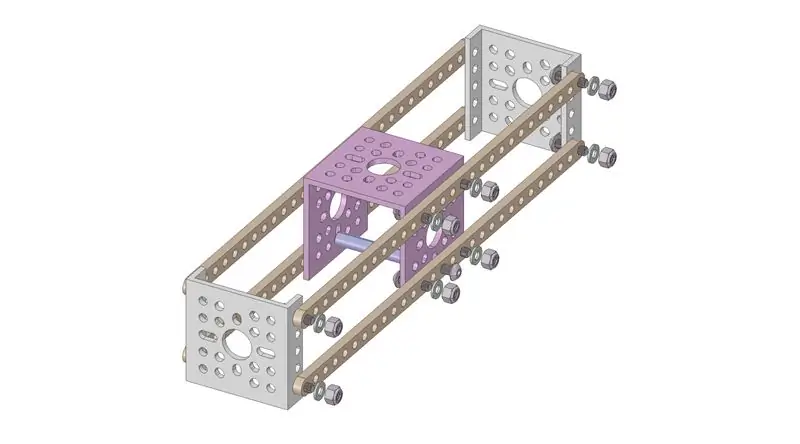
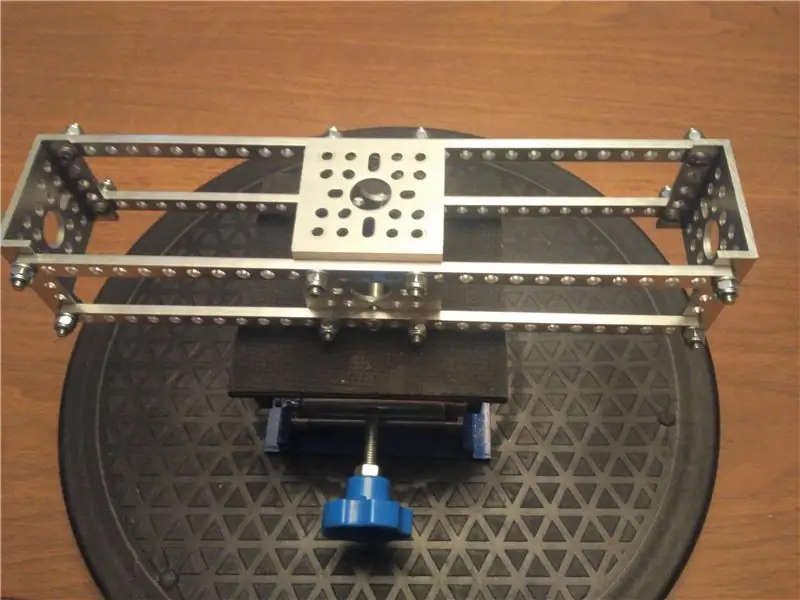
Zacznijmy. Skręcić ze sobą dwie klatki silnika. Oto, czego potrzebujesz dla każdego z nich:
- Jeden kanał dla centrum.
- Dwa dolne kanały na końcach.
- Cztery belki płaskie.
- Po 16 śrub z łbem kulistym M4 x 14 mm, podkładek płaskich i nakrętek nylok.
Rysunek przedstawia element dystansowy 43 mm na otwartym końcu kanału, ale jest to opcjonalne.
Zbuduj klatki silnika na martwej płaskiej powierzchni w następujący sposób:
- Przykręć każdą belkę do kanału środkowego za pomocą dwóch śrub z łbem kulistym 14 mm, płaskich podkładek i nakrętek nylok.
- Wyrównaj wszystko.
- Dodaj niski kanał boczny na każdym końcu za pomocą większej liczby śrub z łbem kulistym 14 mm, płaskich podkładek i nakrętek nylok.
- Wyrównaj wszystko.
- Dokręć wszystko.
I to jest najtrudniejsza część. Teraz wystarczy dodać szkielet, aby skompletować ramę.
Krok 3: Dodaj kręgosłup
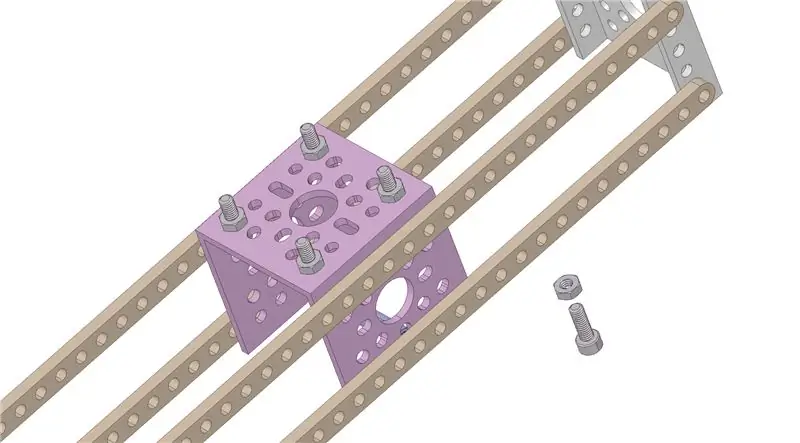
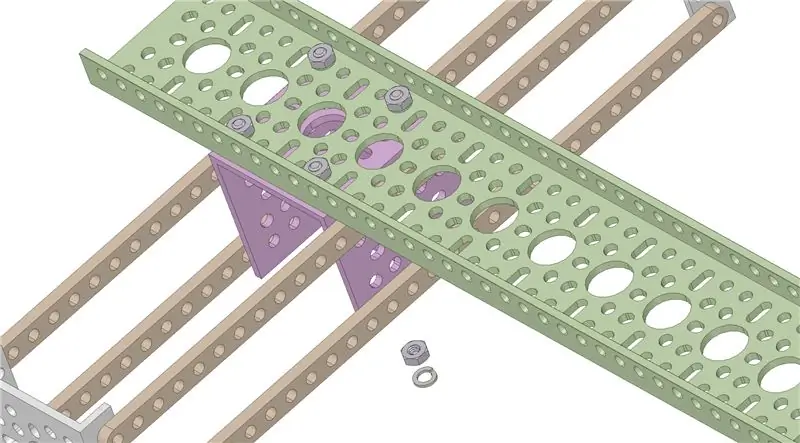
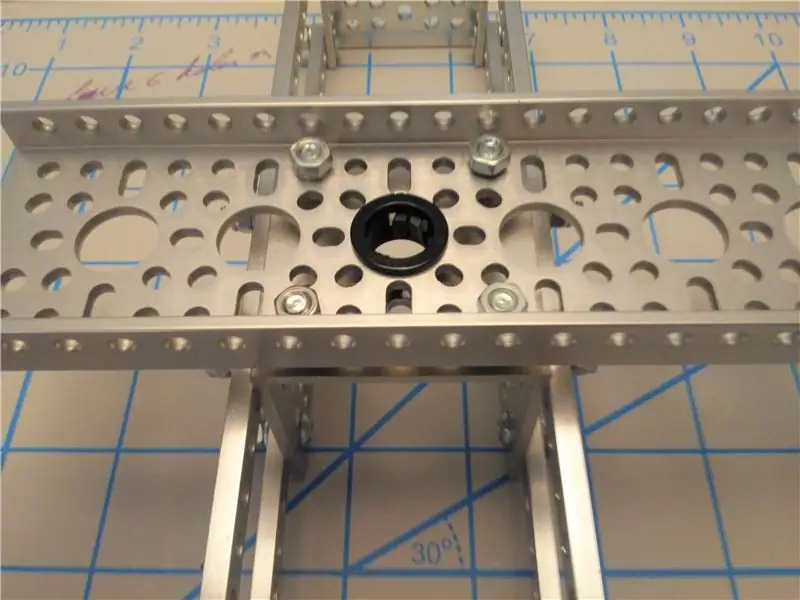
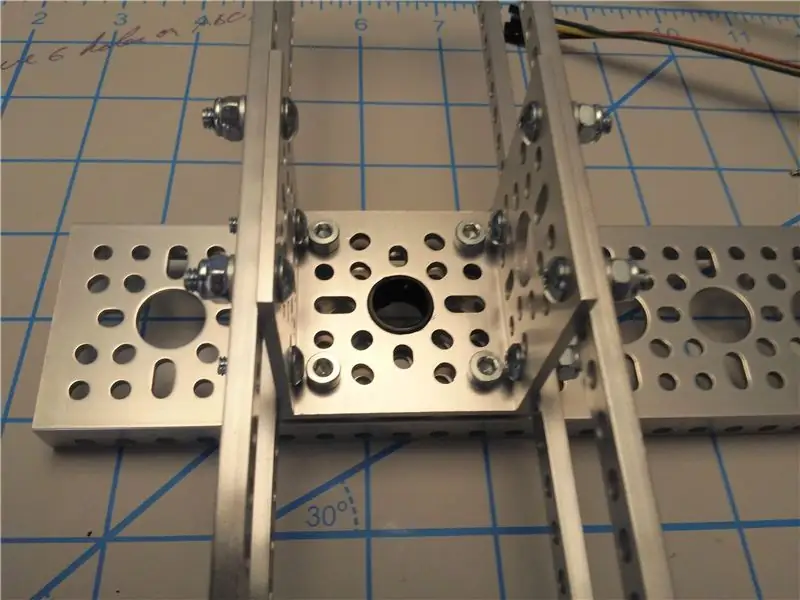
Teraz jesteśmy gotowi do związania dwóch klatek silnika razem z kręgosłupem. Oto, czego potrzebujesz.
- Jeden kanał szkieletowy z dolnego boku.
- Osiem wkrętów z łbem walcowym M4 x 12 mm i dzielonych podkładek zabezpieczających
- 16 zwykłych nakrętek sześciokątnych
Każda klatka silnika jest przymocowana do szkieletu za pomocą czterech śrub z łbem walcowym. Najpierw zainstalujemy śruby mocujące na klatkach silnika za pomocą zwykłych nakrętek sześciokątnych. Dzięki temu można później zdjąć szkielet, po włożeniu silników, bez utraty śrub. Oto jak to robimy:
- Przełóż śruby mocujące przez środkowy kanał klatki silnika i nakręć na każdy z nich nakrętkę sześciokątną, dokręcając palcem.
- Wyrównaj trzeci duży otwór kanału szkieletowego z dużym otworem w środkowym kanale klatki silnika i dociśnij go do śrub mocujących.
- Wyrównaj wszystko.
- Teraz sięgnij tym cienkim kluczem i przytrzymaj każdą nakrętkę podczas dokręcania śruby za pomocą 3 mm uchwytu T.
- Wyrównaj wszystko.
- Dodaj dzieloną podkładkę zabezpieczającą i nakrętkę sześciokątną na każdą śrubę nad kręgosłupem i dokręć śrubokrętem nasadowym 7 mm.
- Zainstaluj twarde plastikowe przelotki, jak pokazano na zdjęciach. Powinny wystawać na około mm w głąb klatki silnika.
I to wszystko. Rama jest kompletna. Teraz jesteśmy gotowi do dodania silników.
Krok 4: Dodaj mocowania silnika do silników
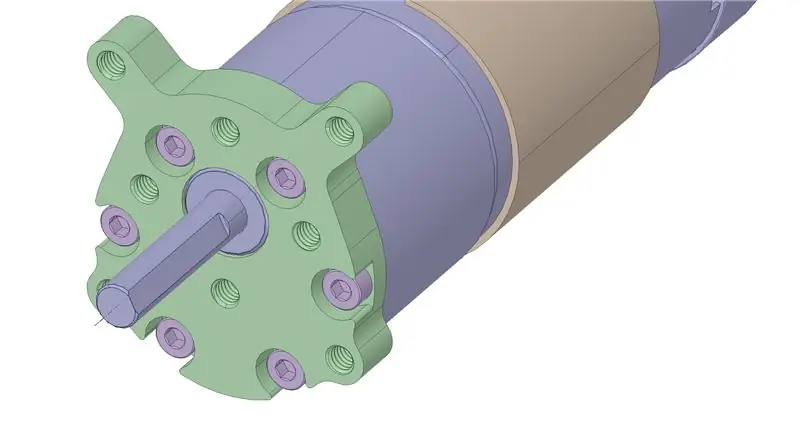
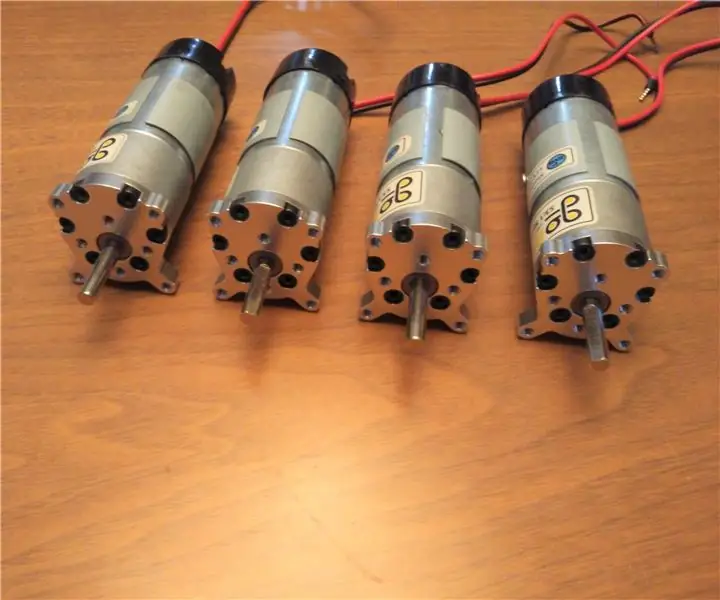
W końcu włączymy silniki. Ale najpierw musimy przymocować mocowania silników do silników. Mocowania silnika to tak naprawdę nic innego jak adaptery rozmieszczenia otworów: pozwalają nam przykręcić element o jednym wzorze i/lub rozmiarze otworów do elementu o zupełnie innym rozmieszczeniu.
Przykręć mocowanie silnika do silnika za pomocą sześciu dołączonych śrub M3. Pójdzie tylko w jedną stronę.
Moje mocowania były dostarczane z dość nieoptymalnymi śrubami napędowymi Phillips. Mimo że rysunek części z goBUILDA ma śruby mocujące, jak pokazano na powyższym rysunku.
Wymieniłem złe śruby na śruby z łbem gniazdowym M3 x 6mm, jak pokazano na zdjęciu.
Teraz możemy przymocować zespoły silników do ramy.
Krok 5: Podłącz silniki
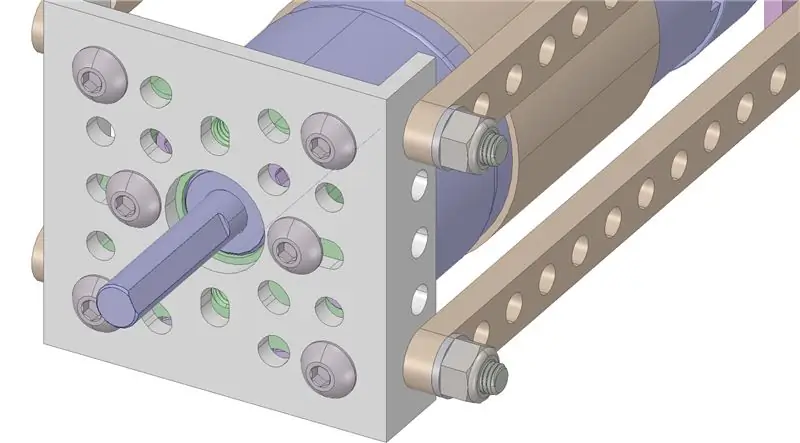
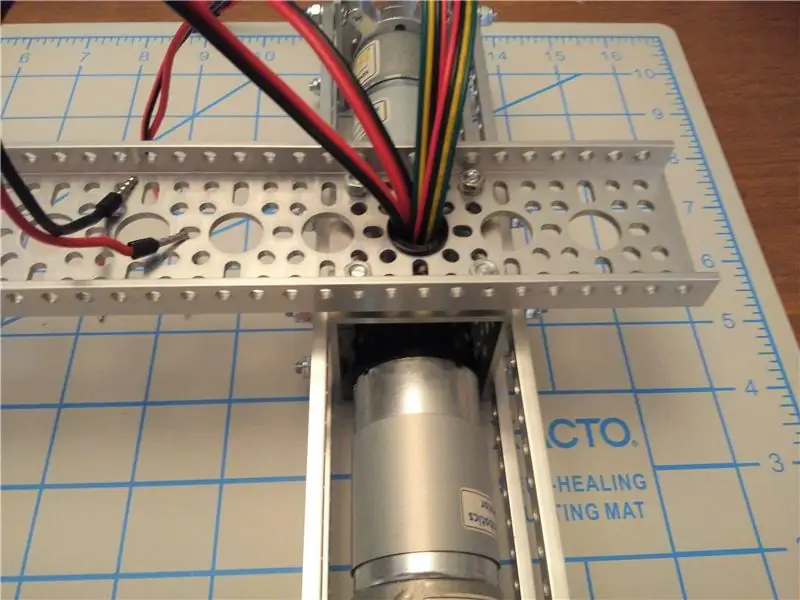
Ilustracja pokazuje wszystko właściwą stroną do góry, ale w tym celu chcesz odwrócić ramkę do góry nogami. Jedna uwaga: jeśli zamierzasz dodać kable enkodera do silników, teraz byłby to dobry moment, aby to zrobić. OK, ruszajmy. Dla każdego silnika:
- Przeprowadź przewody przez plastikową przelotkę.
- Ustaw silnik na miejscu i dokończ przeciąganie przewodów.
- Przykręć mocowanie silnika do kanału końcowego klatki silnika za pomocą śrub z łbem kulistym M4 x 8 mm. Pójdzie tylko w jedną stronę.
Do mocowania silnika można użyć od czterech do ośmiu śrub. Sześć wydaje się w porządku. Osiem wydaje się przesadne i niepotrzebne. Użyłem ośmiu.
I jesteśmy prawie na miejscu. Musimy tylko założyć piasty na wałki silnika i możemy przykręcić koła.
Krok 6: Przymocuj piastę koła do wału silnika
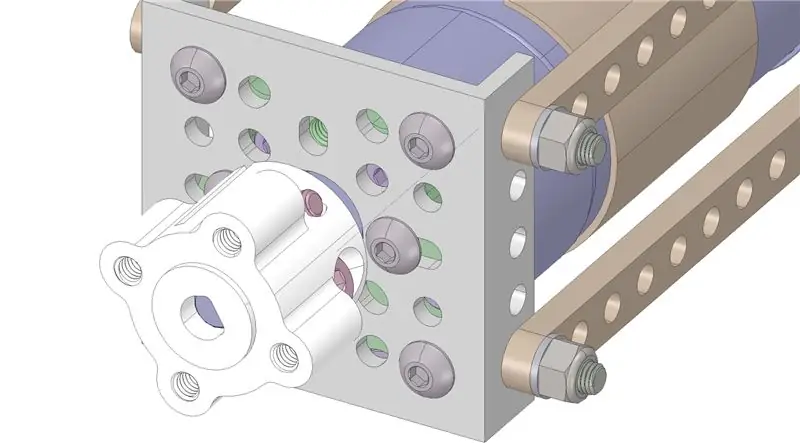
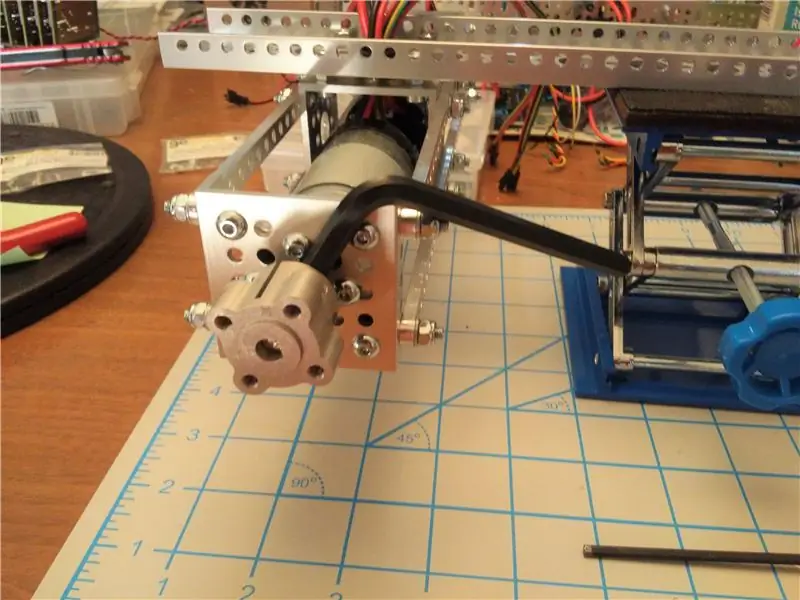
Dla każdego silnika:
Umieść piastę na wale silnika. Użyj podkładki dystansowej, aby upewnić się, że wszystkie cztery piasty znajdują się w tej samej odległości na zewnątrz. Używam klucza sześciokątnego 6 mm, ale wszystko o szerokości 6 mm wystarczy. Po umieszczeniu elementu dystansowego dokręć na przemian dwie śruby zaciskowe, aż zaczną harmonijnie krzyczeć.
I prawie skończyłeś. Czas złożyć koła i nazwać to dniem.
Krok 7: Złóż koła
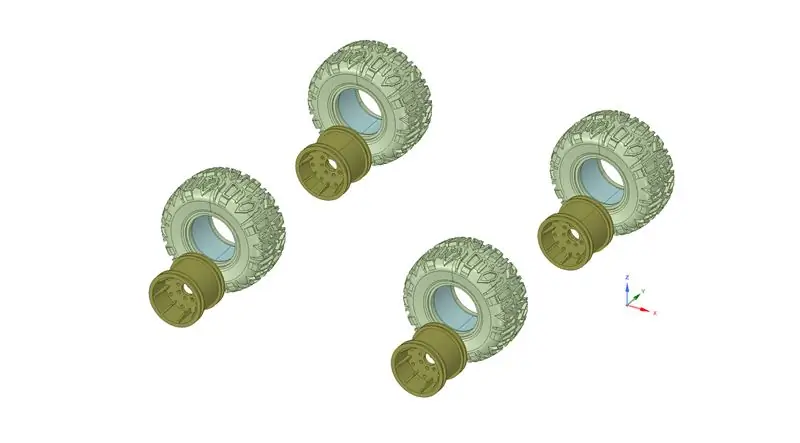
Opony wyposażone są w piankowe wstawki. Uważam, że najlepszym sposobem na umieszczenie wkładek w oponach jest złożenie ich na pół i po prostu wciśnięcie. Masuj je trochę, aż cała opona będzie równo wypchana.
Teraz zamontujemy opony na felgach, aby dokończyć montaż koła.
Opony są kierunkowe, a felgi niesymetryczne. Oto jak tego nie schrzanić:
- Ułóż cztery obrzeża w kwadrat, jak pokazano powyżej, ze wszystkimi płytszymi zagłębieniami środkowymi skierowanymi do wewnątrz w kierunku przeciwnego obrzeża.
- Ułóż opony obok felg tak, aby wszystkie bieżniki opon były skierowane w ten sam sposób.
- Chwyć każdą obręcz i oponę i wciśnij oponę na obręcz bez obracania czegokolwiek.
- Przesuwaj oponę kciukami, aż obie stopki zostaną całkowicie osadzone w swoich szczelinach w obręczy.
- W razie potrzeby przyklej i pozostaw na noc.
Nie przykleiłem mojego i wydawało się, że to wszystko dobrze radzi sobie z narzędziami wokół kortu tenisowego (korty tenisowe mają zazwyczaj dobrą przyczepność, więc nie ma zbyt dużego poślizgu). Opony odpadły jednak podczas późniejszych dość rygorystycznych testów na stanowisku. Potem je skleiłem.
Wydaje się, że ludzie silnie odczuwają klej do opon, prawdopodobnie proporcjonalnie do tego, ile na niego wydali. Miałem szczęście z MG Chemicals AC. Jeśli chodzi o to, jak je skleić, istnieje wiele filmów na ten właśnie temat.
Teraz możemy przykręcić koła.
Krok 8: Śruba na kołach
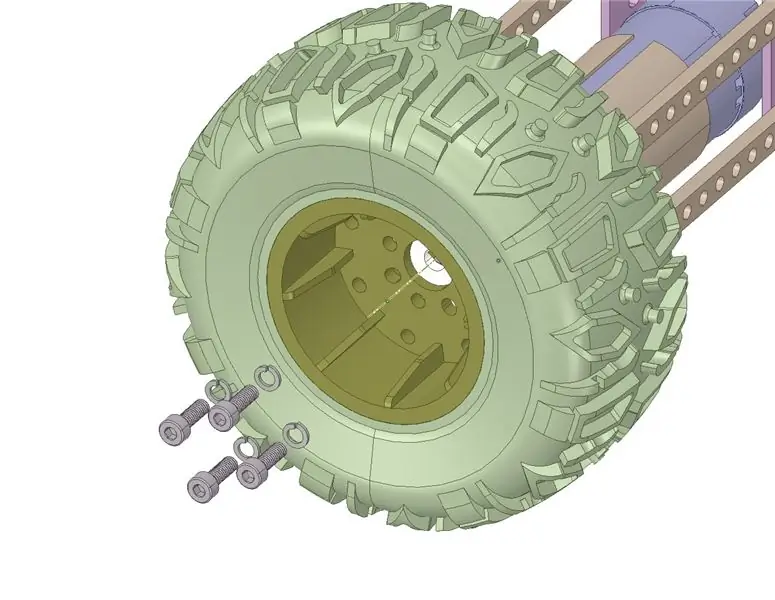
Ułóż cztery koła wokół ramy, tak aby wszystkie płytsze zagłębienia środkowe były skierowane do wewnątrz, a bieżniki opon były skierowane w ten sam sposób.
Na koniec przykręć każde koło do piasty za pomocą czterech śrub z łbem walcowym M4 x 12 mm i dzielonych podkładek zabezpieczających, jak pokazano powyżej.
I to kończy podstawowy montaż.
Wszystko, czego teraz potrzebujesz, to podstawowa elektronika i możesz iść.
Krok 9: Opcje dla ciała
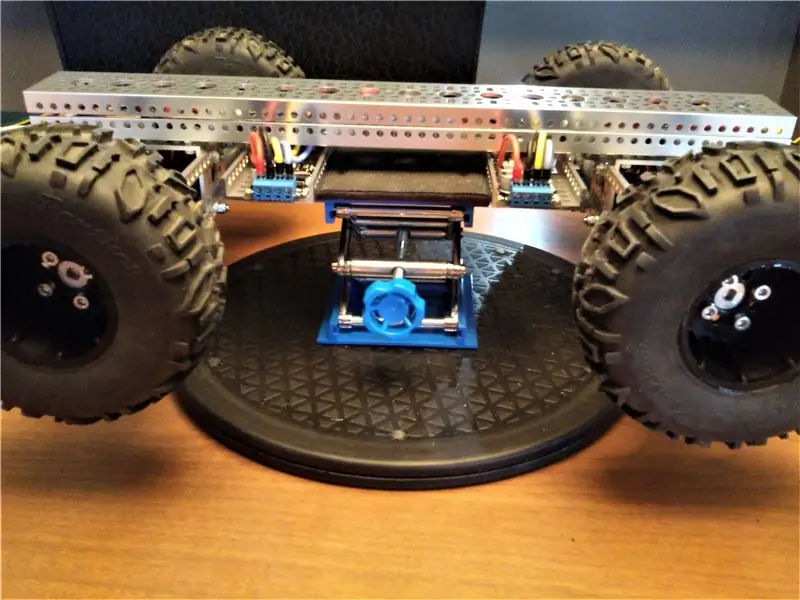
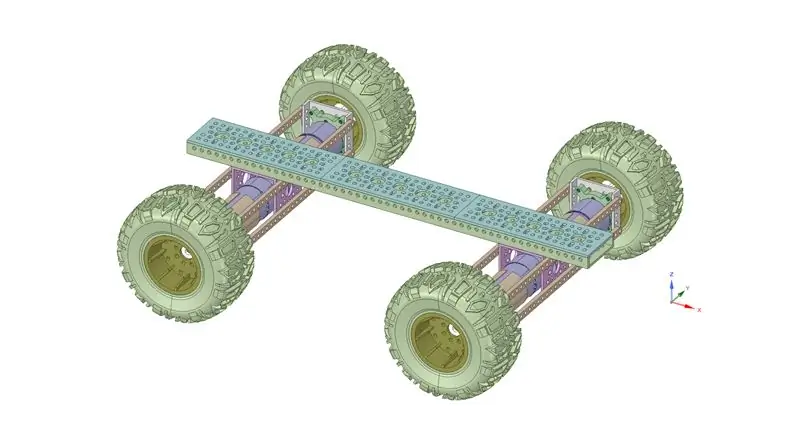
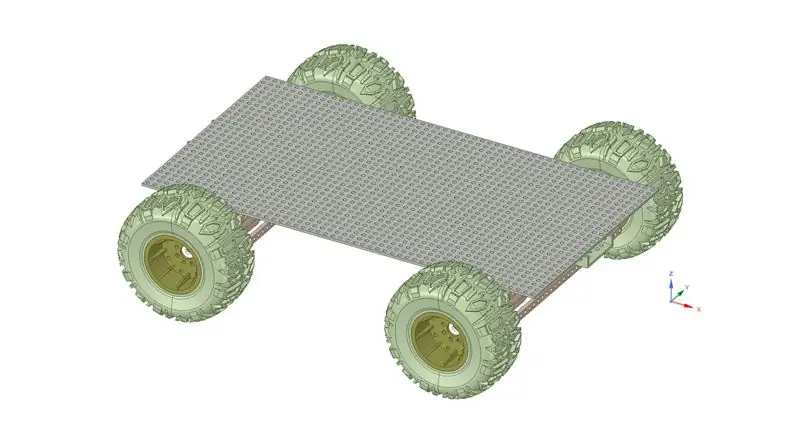
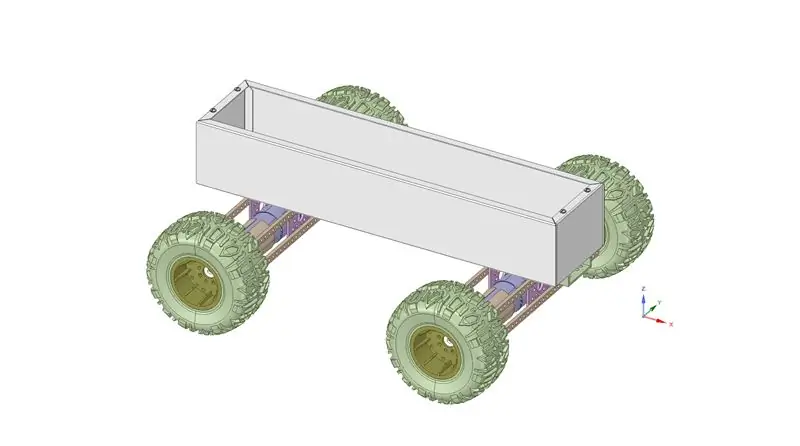
Oto kilka dodatkowych pomysłów na ciało. Szkielet można przykryć maksymalnie trzema płytami z układem 5 otworów, maksymalnie trzema pięciootworowymi kanałami bocznymi dolnymi, jednym długim kanałem bocznym dolnym, jedną lub kilkoma płytami rastrowymi lub czymś innym. Pokazane pudełko to aluminiowa obudowa Hammonda, tylko 2 mm krótsza niż szkielet.
Krok 10: Dodawanie elektroniki
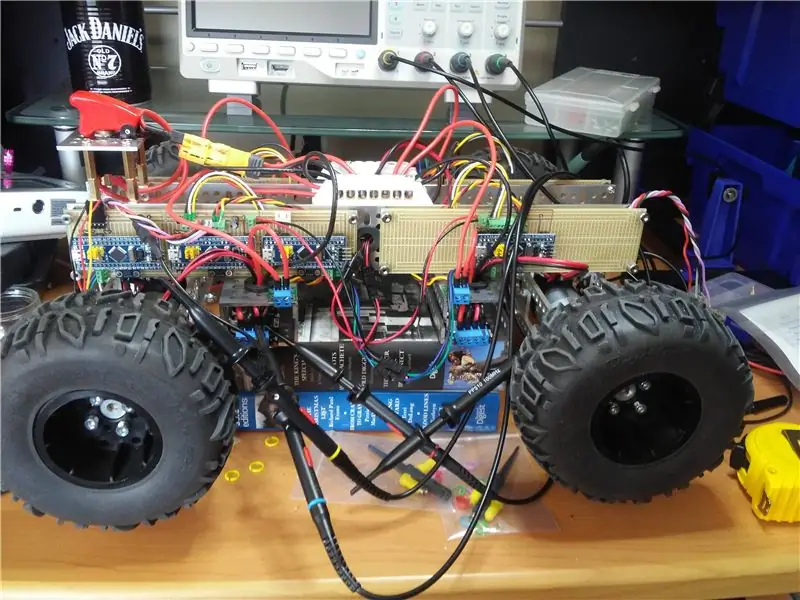
Istnieją sterowniki silników i sterowniki silników. Sterowniki silników działają na wyższym poziomie w schemacie rzeczy, które sterowniki silników. Zazwyczaj mówimy do sterowników silników z impulsami serwo z odbiornika radiowego RC lub z komunikacją szeregową z pewnego rodzaju procesora. Sterowniki silników są dostępne w jednym lub dwóch kanałach.
Z drugiej strony kierowcy motorów działają na bardziej podstawowym poziomie. Rozmawiamy ze sterownikami silników z sygnałem PWM z procesora.
Jeśli budujesz pojazd stricte RC, to dwukanałowy sterownik silnika może być dla Ciebie. Wystarczy podłączyć równolegle oba silniki z każdej strony, podłączyć kanały przepustnicy i sterowania z odbiornika RC, dodać akumulator i gotowe. Do tego pojazdu potrzebujesz kontrolera, który może obsłużyć około 15 A na bok.
Kiedy jednak dodamy do tego procesor, robi się ciekawiej. Teraz odczytujemy dane z odbiornika za pomocą procesora. Obecnie można to zwykle zrobić za pomocą prostego łącza szeregowego. Następnie możemy przesłać dane dotyczące przepustnicy i sterowania do sterownika silnika przez drugie łącze szeregowe.
Lub możemy użyć prostych sterowników silników i sterować nimi bezpośrednio za pomocą PWM. Nie musimy łączyć ze sobą silników z każdej strony. Każdy silnik może mieć swój własny kanał sterownika. Sterowniki silników są dostępne w jednym, dwóch lub czterech kanałach, o których wiem. W przypadku tego pojazdu jeden dwukanałowy sterownik na każdym końcu wydaje się najrozsądniejszym układem. Używam czterech jednokanałowych sterowników.
Sterowniki, których używam, kosztują około dziesięciu dolców każdy. Obsługują 13 A w sposób ciągły bez radiatora. Wykonują PWM z blokowaną antyfazą lub PWM z dwoma przewodami i uziemieniem. Jedynym minusem jest to, że nie mają wyjścia prądowego. Nazywają się Cytron MD13S.
Zalecana:
Tanie akrylowe podwozie czołgu robota dla Arduino SN7300 Sinoning: 6 kroków
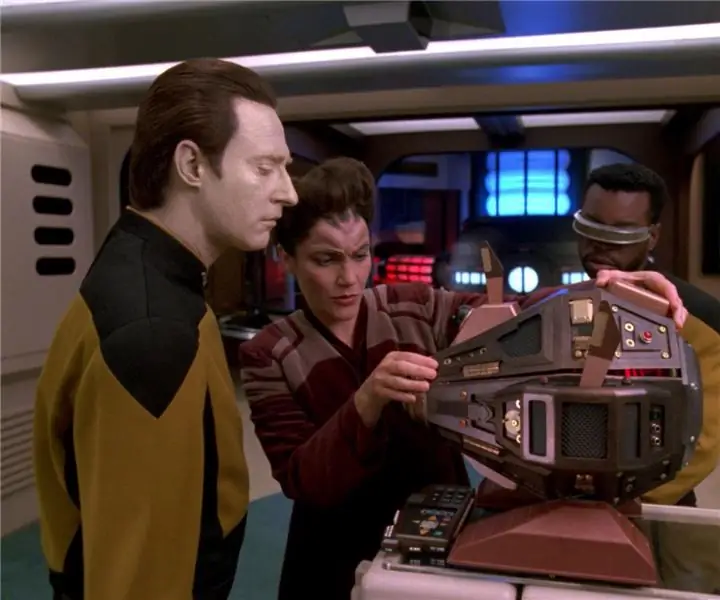
Tanie akrylowe podwozie zbiornika robota dla Arduino SN7300 Sinoning: Tanie akrylowe podwozie zbiornika dla Arduino SN7000 Sinoningkup od: SINONING ROBOT TANK
Pług śnieżny do łazika FPV: 8 kroków (ze zdjęciami)
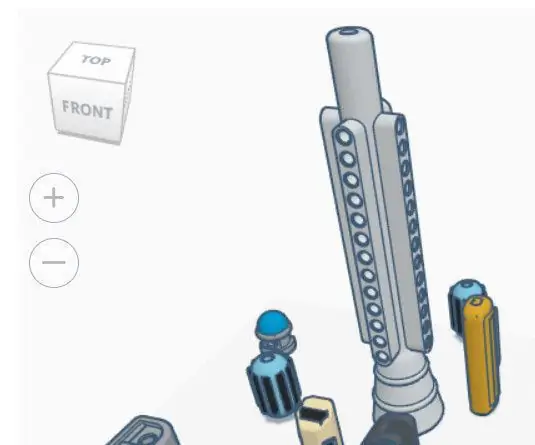
Pług śnieżny do łazika FPV: nadchodzi zima. Tak więc łazik FPV potrzebuje pługa śnieżnego, aby zapewnić czysty chodnik. Linki do RoverInstructables: https://www.instructables.com/id/FPV-Rover-V20/ Thingiverse: https://www.thingiverse.com/thing : 2952852Obserwuj mnie na Instagramie za późno
Podwozie robota HUNIE do prac domowych na zewnątrz: 6 kroków
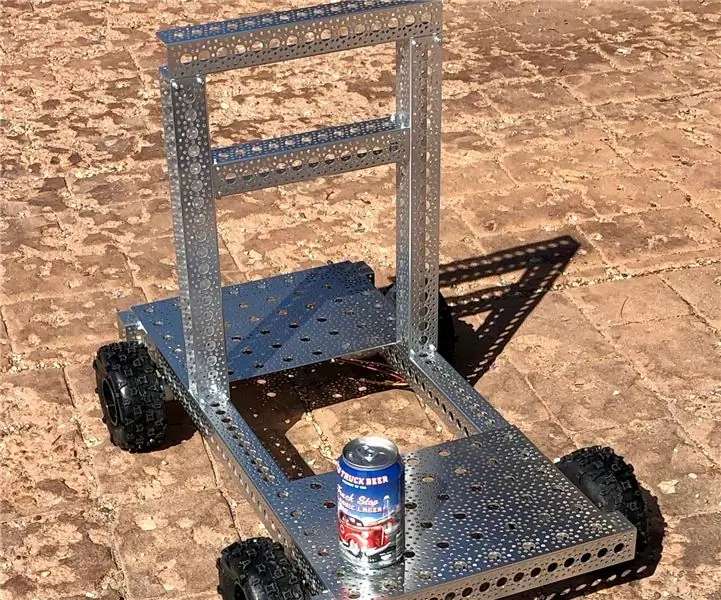
HUNIE-Robot Chassis do prac domowych na zewnątrz: Powyżej przedstawiam moją pierwszą konstrukcję robota. Jestem całkiem zręczny z elektroniką, programowałem trochę komputery trzy dekady temu i szukałem nowego hobby, ponieważ RC Airplanes nie pasuje już do mojego stylu życia (za daleko w terenie). buduję
Podwozie robota DIY: 8 kroków (ze zdjęciami)
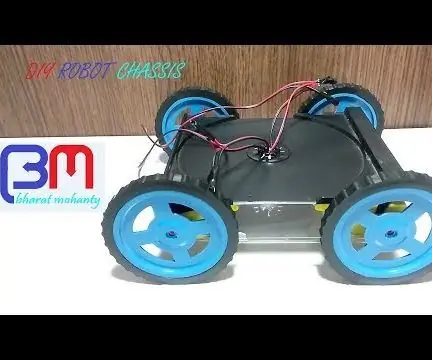
Diy Robot Chassis: jest to najłatwiejsze podwozie robota, jakie możesz zrobić w domu. Możesz oglądać tworzenie wideo na moim KANALE. Możesz bezpośrednio SUBSKRYBOWAĆ MÓJ KANAŁ KLIKNIJ TUTAJ
Podwozie robota Monka 6x4: 10 kroków
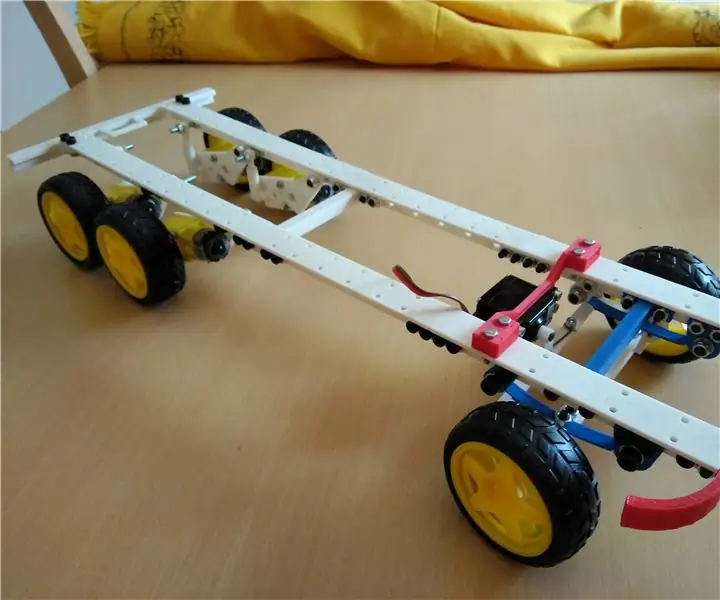
Robot Monka 6x4 Podwozie: części 3D do pobrania: https://www.thingiverse.com/thing:3006384nakrętki: M3,M4,M5 podkładki zwykłe i samozabezpieczające: M3x10mm, M3x16mm, M3x25mm,M4x16mm, M4x27mm, M5x20mm.inne części :4x silnik TT, 6x koło, Servo S3003, 2x łożysko 625, mała sprężyna