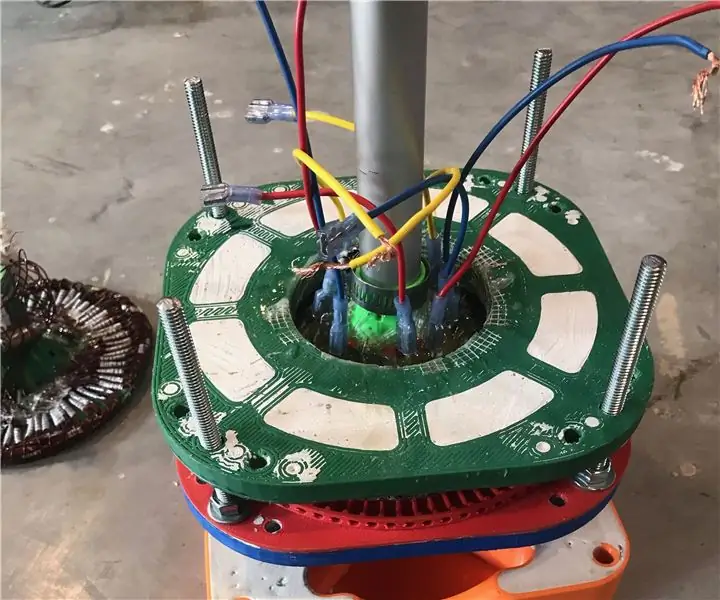
Spisu treści:
2025 Autor: John Day | [email protected]. Ostatnio zmodyfikowany: 2025-01-23 15:03
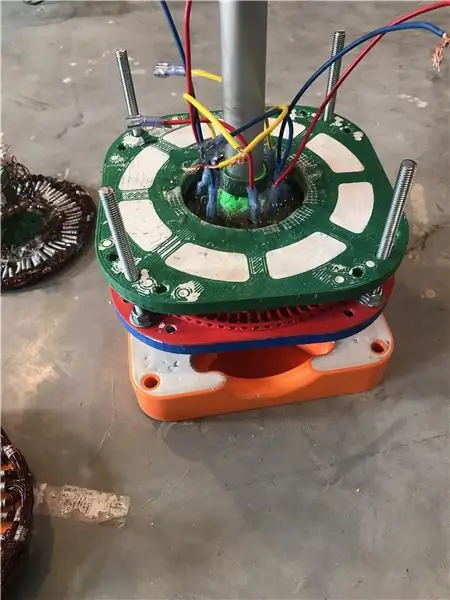
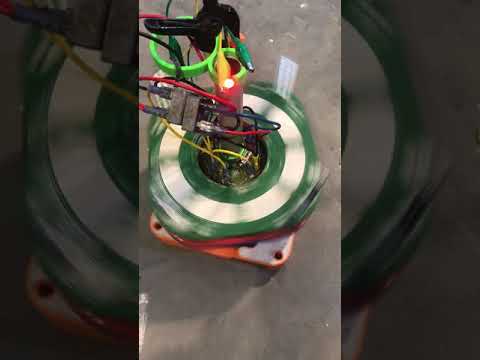
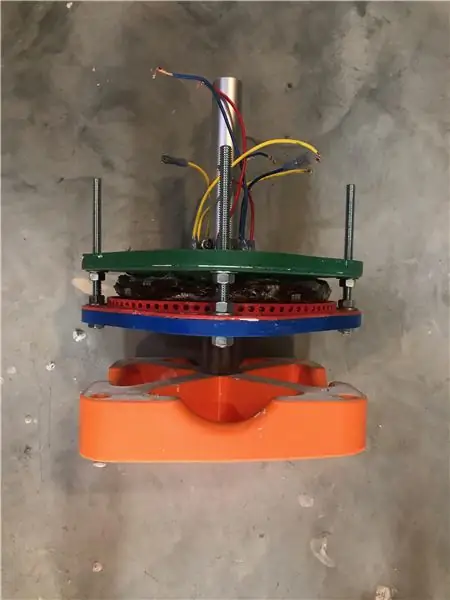
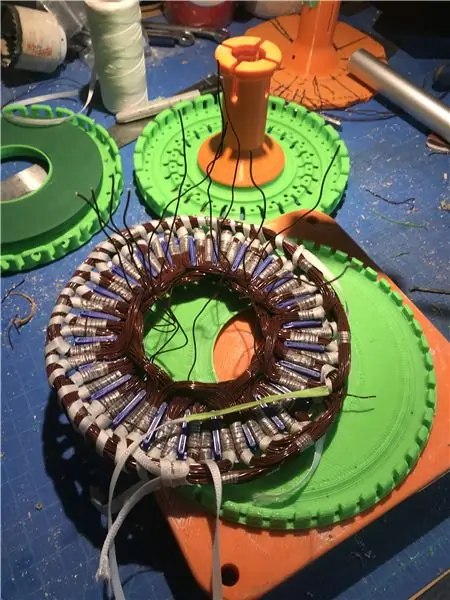
ZATRZYMAĆ!! PRZECZYTAJ NAJPIERW!!! To jest zapis projektu, który wciąż jest w fazie rozwoju, prosimy o oferowanie wsparcia.
Moim ostatecznym celem jest to, aby ten typ silnika/alternatora mógł stać się sparametryzowanym projektem open source. Użytkownik powinien być w stanie wprowadzić niektóre parametry, takie jak moment obrotowy, prędkość, prąd, wolty/obr./min, rozmiary magnesów wspólnych i być może dostępne miejsce, a także powinna zostać wygenerowana seria plików.stl i.dxf do druku 3D.
To, co zrobiłem, to stworzenie platformy, która może zweryfikować symulowany projekt, który następnie może być ewoluowany do bardziej optymalnego urządzenia przez społeczność.
Po części jest to jeden z powodów, dla których ustawiłem to za pomocą dynamometru. Dynamometr mierzy moment obrotowy i prędkość, aby umożliwić pomiar KM lub watów wału. W tym przypadku zbudowałem alternator z przelotowym, nieruchomym wałem, co ułatwia ustawienie systemu dynamometru, a więc może być skonfigurowany do napędzania silnika przez RC ESC (mam nadzieję) i zmierzony moment obrotowy na wyjściu, a także prędkość, V i Amps, co pozwala określić sprawność silnika.
Na moje potrzeby może być napędzany przez silnik o zmiennej prędkości (nadwyżka z wiertarki akumulatorowej, z przekładnią obniżającą) i mierzonym wejściowym momentem obrotowym wału, a także V i amperami, co pozwala na generowanie rzeczywistej wydajności i spodziewanych obciążeń turbiny do symulacji.
W tym trybie mam nadzieję użyć RC ESC zdolnego do hamowania regeneracyjnego i być może Arduino do kontrolowania obciążenia, które mój VAWT przenosi, aby osiągnąć MPPT (Multi Power Point Tracking).
MPPT jest używany do sterowania turbinami słonecznymi i wiatrowymi, ale w przypadku wiatru jest to nieco inne. W przypadku energii wiatrowej dużym problemem jest to, że gdy prędkość wiatru podwaja się z 10 km/h do 20 km/h, energia dostępna z wiatru wzrasta o sześcian, a więc 8-krotnie. Jeśli 10 W było dostępne przy 10 km/h, to 80 W jest dostępne przy 20 km/h. Wspaniale jest mieć więcej energii, ale moc alternatorów podwaja się tylko wtedy, gdy podwaja się prędkość. Więc jeśli masz idealny alternator na wiatr z prędkością 20 km/h, jego obciążenie może być tak duże, że przy 10 km/h nawet się nie uruchomi.
To, co robi MPPT, to użycie wytrzymałego przełącznika półprzewodnikowego, aby bardzo szybko odłączyć, a następnie ponownie podłączyć alternator. Pozwala dostosować obciążenie alternatora, a Multi MPPT oznacza, że można ustawić różne obciążenia dla różnych prędkości.
Jest to bardzo przydatne, ponieważ wszystkie typy turbin gromadzą maksymalną energię, gdy obciążenie jest dopasowane do dostępnej energii lub prędkości wiatru.
WIĘC
To nie jest przepis, chociaż wierzę, że można go skopiować z tego, co opublikowałem, i chętnie udzielę dalszych informacji, ale sugeruję, że najlepszą opcją byłoby zasugerowanie mi ulepszeń przed zakończeniem konkursu Obwody i czujniki, abym mógł rozważyć, odpowiedzieć i być może ulepszyć tę instrukcję.
Będę nadal aktualizował, poprawiał i dodawał informacje, więc jeśli teraz jest to interesujące, może zechcesz zajrzeć ponownie za chwilę, ale mam nadzieję, że zdążysz trochę zrobić, zanim konkurs Sensors zakończy się 29/19 lipca.
Poza tym nie jestem szczególnie towarzyską bestią, ale od czasu do czasu lubię klepać się po plecach i to jest jeden z powodów, dla których tu jestem:-) Powiedz mi, czy podoba ci się oglądanie mojej pracy i chcesz zobaczyć więcej proszę:-)
Ten projekt powstał, ponieważ chciałem kontrolować obciążenie do testowania moich projektów turbin i chciałem, aby było ono łatwe do odtworzenia, aby inni również mogli z niego korzystać. W tym celu ograniczyłem się do zaprojektowania czegoś, co dałoby się zbudować tylko za pomocą drukarki FDM, bez żadnych innych obrabiarek. Wydaje się, że nie ma wielu produktów komercyjnych, które zaspokajałyby zapotrzebowanie na alternator o wysokim momencie obrotowym i niskiej prędkości, nie zazębiający się, chociaż jest ich kilka z Chin. Generalnie nie ma dużego popytu, ponieważ systemy przekładni są tak tanie, a energia elektryczna tak tania.
Chciałem czegoś, co dałoby około 12 V przy 40-120 obr/min i około 600-750 W przy 120-200 obr/min. Chciałem również, aby był kompatybilny z niedrogimi 3-fazowymi kontrolerami PMA ze świata RC (Elektroniczne Kontrolery Prędkości ESC). Ostatnim wymaganiem było to, aby była to prowadnica zewnętrzna (obudowa lub osłona z magnesami obraca się, podczas gdy wał ze stojanem jest nieruchomy), z wałem przechodzącym przez całą obudowę i stojanem, który zaciska się na wale.
Ta instrukcja jest w toku i publikuję ją, aby ludzie mogli zobaczyć proces, a nie dlatego, że myślę, że powinni to skopiować. Kluczową rzeczą, którą chciałbym zmienić, jest to, że zbudowana przeze mnie podkładka z drutu nie jest wystarczająco mocna, aby właściwie skierować pola magnetyczne wokół pierścienia, więc duża część strumienia magnetycznego zapłaconego w tych magnesach jest marnowana z tyłu. Kiedy przerobię projekt, co zrobię wkrótce, prawdopodobnie zrobię to z magnetycznymi płytami podkładowymi jako ze stali wycinanej cnc. Stal byłaby dość tania, znacznie mocniejsza i uprościłaby większość tej konfiguracji. Interesujące było zrobienie kompozytów FDM/drutu/plastiku, jak to tutaj zilustrowałem, a z PLA obciążonym żelazem również byłoby inaczej. Postanowiłem jednak, że chcę czegoś, co naprawdę wytrzyma, a więc stalowych płyt.
Poczyniłem spore postępy w tej wersji, której użyję do testowania tego VAWT. Nie jestem jeszcze na miejscu, jeśli chodzi o wydajność na niskim napięciu. Myślę, że moja moc/moment obrotowy jest na właściwym poziomie, będę aktualizować w miarę postępów, ale w tym momencie to, co mam, ma duże szanse na kontrolowanie obciążenia, którego potrzebuję. Po zwarciu wydaje się, że jest w stanie zapewnić całkiem spory opór momentu obrotowego, więcej niż wystarczający do przetestowania turbiny. Muszę tylko założyć kontrolowany bank oporu, a mam przyjaciela, który mi w tym pomaga.
Jedną rzeczą, o której powiem pokrótce, jest to, że podobnie jak wielu ludzi, od kilku lat mam drukarkę 3D (używającą PLA) 3D, z której czerpałem 20-30 kg przyjemności. Często uważam to za frustrujące, ponieważ części o dowolnym rozmiarze/wytrzymałości są albo drogie i bardzo powolne w druku, albo tanie, szybkie i marne.
Wiem, ile tysięcy tych drukarek 3D jest na rynku, często nic nie robiąc, ponieważ wykonanie użytecznych części zajmuje zbyt dużo czasu lub kosztuje zbyt dużo. Wymyśliłem ciekawe rozwiązanie na mocniejsze szybsze części z tej samej drukarki i PLA.
Nazywam to „strukturą wylewaną”, w której drukowany obiekt (składający się z 1 lub więcej drukowanych części, a czasem łożysk i wałków) jest wykonany z pustymi przestrzeniami przeznaczonymi do wylania pełnego utwardzającego płynnego wypełniacza. Oczywiście niektóre z oczywistych wyborów do wylewanych wypełnień to coś w rodzaju żywicy epoksydowej wypełnionej krótkimi włóknami ciętymi włóknami szklanymi, które można stosować do elementów o wysokiej wytrzymałości i niskiej wadze. Wypróbowuję też jakiś tańszy, bardziej ekologiczny pomysł. Drugą stroną tego zespołu „wylewanej struktury” jest to, że wnęka lub pustka, którą zamierzasz wypełnić, może mieć elementy o małej średnicy o dużej wytrzymałości na rozciąganie, wstępnie napięte na wydrukowanej „formie/korku”, co tworzy wynikową strukturę kompozyt w materiałach i strukturze, częściowo Stressed Skin (powłoka PLA), ale z rdzeniem o wysokiej wytrzymałości na ściskanie, który zawiera również elementy o wysokiej wytrzymałości na rozciąganie. Zrobię drugi instruktaż z tym, więc porozmawiam o tym tutaj, tylko po to, aby omówić, w jaki sposób odnosi się to do tej kompilacji.
Krok 1: Lista materiałów i proces
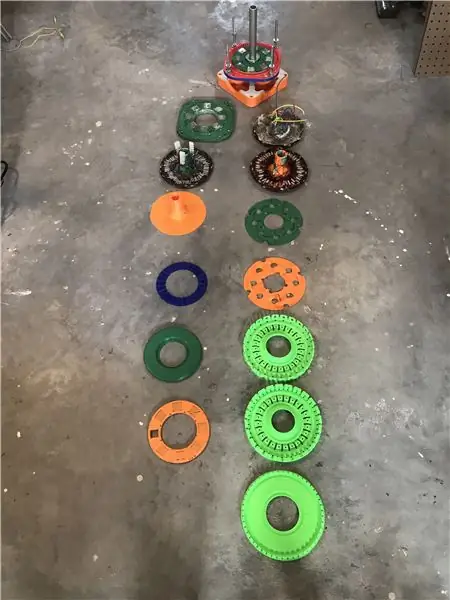
PMA składa się z 3 zespołów, z których każdy zawiera lub wykorzystuje różne części i materiały.
Od góry (strona łożyska) do dołu (strona stojana), 1. Nośnik łożyska i górna tablica łożyskowa
2. Stojan
3. Dolna tablica magnesów
1. Nośnik łożyska i górna tablica magnetyczna
Do tego użyłem części drukowanych 3D wymienionych powyżej
- 150mm8pole górny magazynek i wspornik łożyska CV5.stl,
- płyta wewnętrzna od strony łożyska
- płyta zewnętrzna od strony łożyska
- Łożysko samonastawne 1" ID (jak w standardowych poduszkach + dodaj łącze internetowe),
- 25 'z drutu stalowego ocynkowanego 24g
- 15 'z drutu stalowego ocynkowanego 10g
- 2 rolki grubej wełny stalowej
Opcjonalnie ciężki drut stalowy i wełnę stalową można zastąpić stalowymi płytami nośnymi, cięciem laserowym / strumieniem wody lub drukowaną magnetyczną płytą nośną 3D (ale ciężki drut stalowy jest nadal dobrym pomysłem, ponieważ będzie odporny na odkształcenia plastyczne czas). Próbowałem odlać płytę nośną z żywicy epoksydowej obciążonej proszkiem tlenku żelaza i odniosłem pewien sukces. Poprawienie bocznego sprzężenia strumienia pomiędzy magnesami w szyku za pomocą bardziej efektywnej płyty podkładowej powinno zwiększyć napięcie przy niższych obrotach. Warto również pamiętać, że jest to główny element konstrukcyjny, a płyta tylna przenosi siły z magnesów na słupki podnoszące. Siły magnetyczne przyciągające płyty do siebie mogą wynosić setki funtów, a siły rosną wykładniczo (w sześcianie do trzeciej potęgi), gdy płyty zbliżają się do siebie. Może to być bardzo niebezpieczne i należy uważać na narzędzia i inne przedmioty, które mogą być przyciągane do zmontowanej płyty lub jej pleców!
Użyłem około 300 stóp 24g powlekanego drutu magnetycznego w uzwojeniach, które omówię szczegółowo później.
Krok 2: Wykonanie płyt magnetycznych
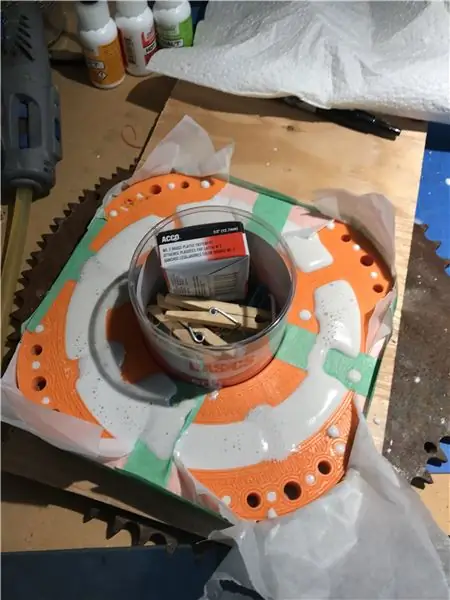
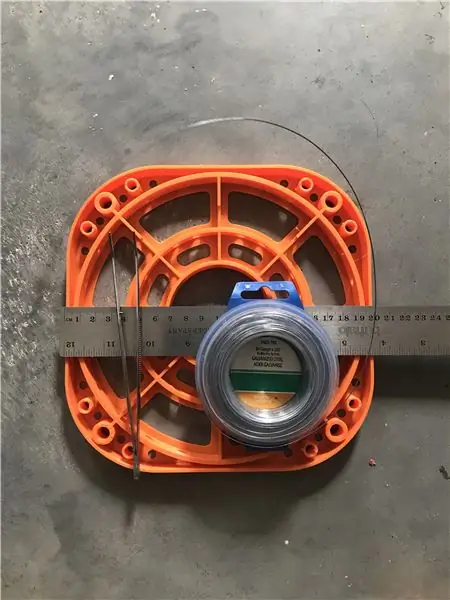
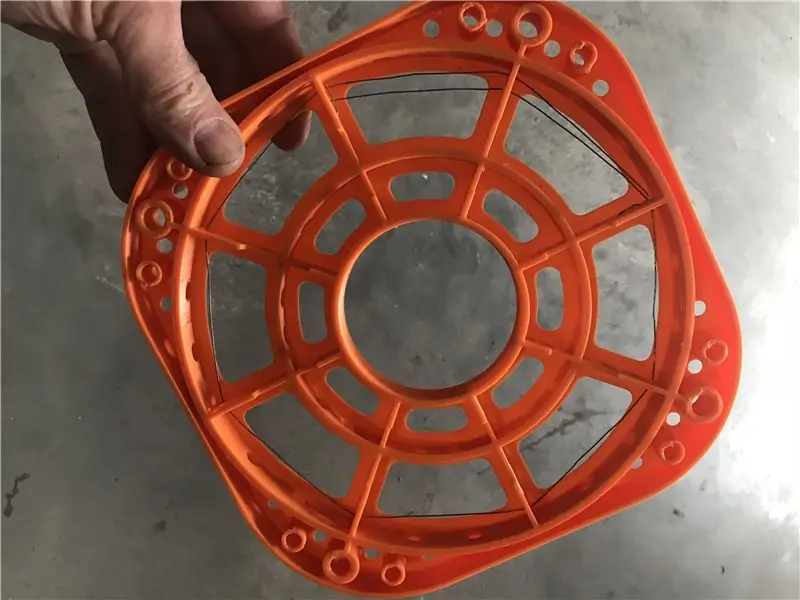
W tym alternatorze o strumieniu osiowym, aby zminimalizować zazębienie i zmaksymalizować moc wyjściową, używam dwóch tablic magnetycznych, po jednym po każdej stronie cewek stojana. Oznacza to, że do przeciągnięcia pola magnetycznego przez miedziane uzwojenia nie jest potrzebny rdzeń magnetyczny, jak to ma miejsce w przypadku większości geometrii silnika/wymiany. Istnieje kilka projektów ze strumieniem osiowym, które wykorzystują rdzenie żelazne i być może w przyszłości spróbuję kilku eksperymentów w ten sposób. Chciałbym wypróbować materiał do druku w 3D z żelazkiem.
W tym przypadku wybrałem 8-biegunowy układ magnesów w okręgu około 150 mm, używając magnesów ziem rzadkich o wymiarach 1 "x 1" x 0,25". Ten rozmiar miał zapewnić, że wszystkie części zmieszczą się na stole drukującym o wymiarach 210 mm x 210 mm. Ogólnie rzecz biorąc, najpierw zwymiarowałem ten alternator, rozumiejąc, że im większa średnica, tym lepsza pod względem woltów na obr./min, więc zrobiłem go tak duży, jak wygodnie zmieściłby się na moim stole roboczym. FYI, jest więcej niż jeden powód, dla którego większy jest lepszy: więcej miejsca na magnesy, im dalej magnesy są od środka, tym szybciej się poruszają, a także jest więcej miejsca na miedź! Wszystko to może się szybko sumować! Jednak wniosek, do którego doszedłem, jest taki, że w tym zakresie rozmiarów, konwencjonalny system strumieniowy może być lepszą konstrukcją domową. Małe wirniki nie mają dużo miejsca, a rzeczy mogą być dość ciasne, zwłaszcza jeśli robisz wałek przelotowy, tak jak to zrobiłem w tym projekcie. Również jeśli twój magnes (długość promieniowa) jest mały w stosunku do średnicy twojego wirnika, tak jak w tym, (około 6" średnicy do 1" magnesu), to windi ng robi się trochę dziwny, gdy wewnętrzne uzwojenie końca jest tylko około 1/2 długości zewnętrznego.
Wróćmy do instruktażu! Sposób, w jaki zmontowałem płytki magnetyczne tego alternatora, polega na przyklejeniu najpierw płytki magnetycznej (zielonej) do czerwonego kołnierza/płyty nośnej. Następnie umieściłem płytkę magnesu na kilku cienkich warstwach sklejki (o grubości około 0,75 cala) i umieściłem obie na ciężkiej stalowej płycie, aby magnesy mogły zacisnąć zespół na miejscu. Następnie nawinąłem stalowy drut na z tyłu płytek magnetycznych. Nie poszło tak, jak się spodziewałem. Silne pole magnetyczne pociągnęło drut w kierunku środka magnesów i nie udało mi się zgiąć każdego rzędu drutu, aby idealnie pasował do następnego miejsca, bez popychania pierwszego owinięcia. Miałem nadzieję, że uda mi się nawinąć drut, a strumień magnetyczny go zablokuje. Następnie próbowałem przecinać pierścienie drutu i tak było lepiej, ale wciąż daleko od tego, co bym miałem nadzieję, że uzyskamy ładną, spójną płytę nośną z drutu. Możliwe są bardziej złożone sposoby wykonania tego i mogą być warte przyszłych eksperymentów. Próbowałem również użyć wełny stalowej, zagęszczonej w polu magnetycznym, jako płyty tylnej lub strumienia droga powrotna. Wydawało się, że to działa, ale rzeczywista gęstość żelaza nie wydawała się być bardzo wysoka, więc nie Nie testuj jego skuteczności, po części dlatego, że uważałem, że struktura drutu jest ważna dla obciążeń mechanicznych na płytach magnetycznych. Wełna stalowa również może być warta zbadania w przyszłości, jednak płyty stalowe cięte strumieniem wody są prawdopodobnie następną opcją, którą wypróbuję.
Następnie wziąłem pomarańczową część wydrukowaną w 3D i nawinąłem drut wokół niej, wzdłuż kierunku, który wydawał mi się być kierunkami największego obciążenia, śruba do śruby i śruba do środka kilka razy w każdym rogu. Owinąłem go również wokół otworów na śruby, w których cały pręt gwintowany przechodzi jako słupki podnoszące, aby utrzymać i regulować odstępy między płytami.
Po upewnieniu się, że płyta magnetyczna i kołnierz są wystarczająco dobre, a pomarańczowa płytka nośna została prawidłowo nawleczona drutem wzmacniającym, połączyłem je za pomocą kleju. Należy zachować ostrożność, ponieważ to połączenie klejowe będzie musiało być wodoszczelne lub zamknięte. Miałem przecieki dwa pierwsze razy i jest bałagan, marnuję dużo gipsu i jest więcej stresu niż potrzebujesz. Zalecam trzymanie niebieskiej tasiemki lub innej gumy balonowej, takiej jak nietrwały klej, aby szybko załatać wycieki. Po połączeniu części wypełnij wybranym materiałem wzmacniającym. Użyłem twardego gipsu, modyfikowanego klejem PVA. Gips powinien osiągać ściskanie 10 000 psi, ale naprężenie niewielkie (stąd drut). Chciałbym spróbować żywicy epoksydowej z posiekanym szkłem i kabosilem lub betonem i domieszkami.
Przydatną rzeczą w przypadku tynku jest to, że gdy się go kopnie, masz sporo czasu, gdy jest twardy, ale kruche i przeciekające lub plamy można łatwo zeskrobać lub zrzucić.
W tym projekcie znajdują się dwie płytki magnetyczne. Jedno ma łożysko, standardową jednostkę samonastawną 1 bloku poduszkowego. Wcześnie wcisnąłem moje w układ magnesów. Do zastosowania, do którego je zaprojektowałem, drugie łożysko będzie znajdować się w turbinie nad alternatorem, więc ja używał tylko jednego samonastawnego łożyska. W końcu było to trochę uciążliwe. Te części można również zmontować z każdą płytką magnesu mającą łożysko, jeśli przewody wyjściowe ze stojana były prowadzone wewnętrznie przez zamontowany wał. pozwalają na zamontowanie przeciwbieżnych śmigieł do wspólnego, nie obracającego się wału/rury.
Krok 3: Tworzenie stojana

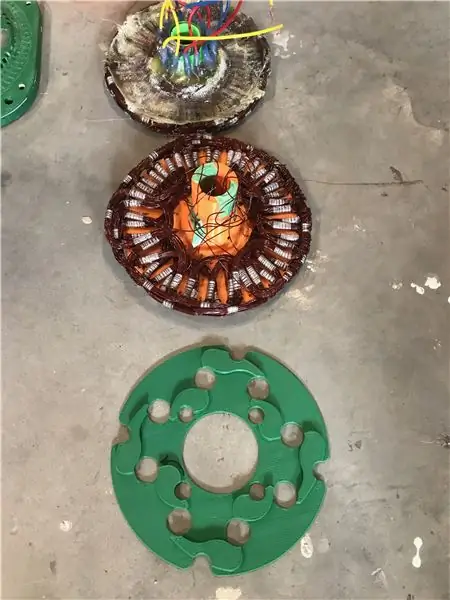
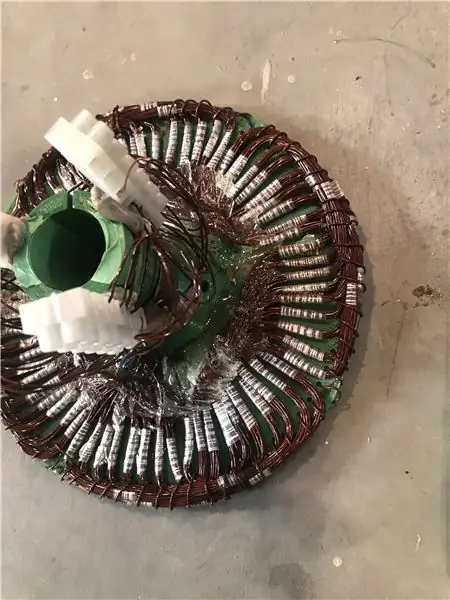
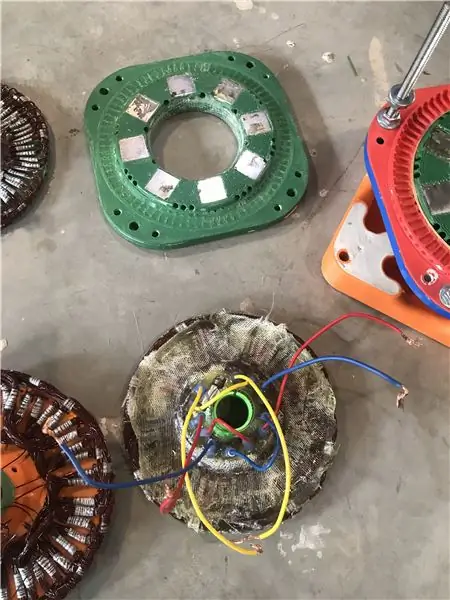
Zgodnie z moim motywem próby wyjaśnienia tego, co zrobiłem i dlaczego w tamtym czasie wydawało się to dobrym pomysłem, stojan będzie wymagał nieco więcej miejsca.
W PMA na ogół uzwojenia są nieruchome, podczas gdy zespoły magnetyczne obracają się. Nie zawsze tak jest, ale prawie zawsze. W zespole osiowym, ze zrozumieniem podstawowej „zasady prawej ręki”, rozumie się, że każdy przewodnik napotykający wirujące pole magnetyczne będzie miał prąd i napięcie generowane między końcami drutu, przy czym ilość użytecznego prądu jest proporcjonalna w kierunku pola. Jeśli pole porusza się równolegle do drutu (np. po okręgu wokół osi obrotu), nie będzie generowany żaden użyteczny prąd, ale generowane będą znaczne prądy wirowe, opierając się ruchowi magnesów. Jeśli przewód biegnie prostopadle, wówczas zostanie osiągnięte najwyższe napięcie i prąd wyjściowy.
Innym uogólnieniem jest to, że przestrzeń w stojanie, przez którą przepływa strumień magnetyczny podczas obrotu, dla maksymalnej mocy wyjściowej, powinna być wypełniona jak największą ilością miedzi, ułożoną promieniście. Jest to problem w przypadku systemów ze strumieniem osiowym o małej średnicy, ponieważ w tym przypadku powierzchnia dostępna dla miedzi w pobliżu wału stanowi ułamek powierzchni na krawędzi zewnętrznej. Możliwe jest uzyskanie 100% miedzi w najbardziej wewnętrznym obszarze napotkanym przez pole magnetyczne, ale w tej geometrii, która daje tylko 50% na zewnętrznej krawędzi. Jest to jeden z najsilniejszych powodów, dla których warto trzymać się z dala od zbyt małych projektów o strumieniu osiowym.
Jak powiedziałem wcześniej, ta instrukcja nie dotyczy tego, jak zrobiłbym to ponownie, a raczej wskazuje kierunki, które wydają się obiecujące, i pokazują niektóre dziury, do których można dotrzeć na tej ścieżce.
Projektując stojan chciałem, aby był jak najbardziej elastyczny pod względem napięcia wyjściowego na minutę i chciałem, aby był 3-fazowy. Aby uzyskać maksymalną wydajność, poprzez minimalizację generowanych prądów wirowych, każda „noga” (każda strona cewki powinna być traktowana jako „noga”) powinna napotykać tylko jeden magnes na raz. Jeśli magnesy znajdują się blisko siebie lub stykają się, jak w przypadku wielu wysokowydajnych silników rc, podczas gdy „noga” przechodzi przez odwrócenie strumienia magnetycznego, powstaną znaczne prądy wirowe. W zastosowaniach silnikowych nie ma to aż takiego znaczenia, ponieważ cewka jest zasilana przez sterownik, gdy znajduje się we właściwych miejscach.
Zwymiarowałem tablicę magnesów, mając na uwadze te koncepcje. Każdy z ośmiu magnesów w tablicy ma średnicę 1 cala, a odstęp między nimi wynosi 1/2 cala. Oznacza to, że segment magnetyczny ma długość 1,5" i jest w nim miejsce na 3 x 1/2" "nóżki". Każda „noga” jest fazą, więc w dowolnym momencie jedna noga widzi strumień neutralny, podczas gdy pozostałe dwie widzą strumień narastający i malejący. Idealne wyjście 3-fazowe, chociaż dając punktowi neutralnemu tak dużo miejsca (aby zminimalizować prądy wirowe) i używając magnesów kwadratowych (lub w kształcie koła), strumień prawie wcześnie osiąga szczyt, pozostaje wysoki, a następnie szybko spada do zera. Myślę, że ten typ wyjścia nazywa się trapezoidalnym i może być trudny dla niektórych kontrolerów, które rozumiem. Okrągłe magnesy o średnicy 1 cala w tym samym aparacie dałyby więcej prawdziwej fali sinusoidalnej.
Ogólnie rzecz biorąc, alternatory budowane w domu zostały zbudowane przy użyciu „cewek”, wiązek drutu w kształcie pierścienia, gdzie każda strona pierścienia jest „nogą”, a kilka cewek można połączyć ze sobą, szeregowo lub równolegle. Pączki są ułożone w okrąg, a ich środki są wyrównane ze środkiem ścieżki magnesu. To działa, ale są pewne problemy. Jedną z kwestii jest to, że ponieważ przewodniki nie są promieniowe, znaczna część przewodnika nie przechodzi pod kątem 90 stopni do pola magnetycznego, więc generowane są prądy wirowe, które pojawiają się jako ciepło w cewce i opór obrotu w układzie magnesów.. Inną kwestią jest to, że ponieważ przewodniki nie są radialne, nie układają się tak ładnie. Moc wyjściowa jest wprost proporcjonalna do ilości drutu, który można zmieścić w tej przestrzeni, więc moc wyjściowa jest redukowana przez niepromieniste „nogi”. Chociaż byłoby to możliwe i jest to czasami wykonywane w projektach komercyjnych, nawijanie cewki z promieniowymi „nogami, połączonymi u góry i na dole, wymaga 2 razy więcej nawijania końcowego niż uzwojenie serpentynowe, w którym górna część jednej nogi jest połączona z górną częścią następną odpowiednią nogę, a następnie spód tej nogi łączy się z następną odpowiednią nogą i tak dalej.
Innym ważnym czynnikiem w tego typu alternatorach Axial flux (wirujące magnesy nad i pod stojanem) jest szczelina między płytami. Jest to zależność sześcienna, ponieważ zmniejszasz odległość między płytami o 1/2, indukcja magnetyczna wzrasta 8x. Im cieńszy możesz zrobić swój stojan, tym lepiej!
Mając to na uwadze, wykonałem 4-płatkowy przyrząd do nawijania, przygotowałem system do odmierzania około 50 stóp splotek drutu i owinąłem przyrząd 6 razy, tworząc wiązki drutu o średnicy około 6 mm. Te pasuję do niebieskiego pierścienia dystansowego, przywiązując je przez otwory, aby końce drutu wychodziły z tyłu. To nie było łatwe. Trochę pomogło mi staranne zaklejenie wiązek taśmą, aby nie były luźne, oraz poświęcenie czasu i użycie gładkiego drewnianego narzędzia do formowania, aby wepchnąć druty na miejsce. Gdy wszystkie zostały przywiązane, niebieski pierścień dystansowy został umieszczony w największym z jasnozielonych pojemników formujących, a za pomocą ciemnozielonego narzędzia do formowania pączków, po drugiej stronie jasnozielonego pojemnika, dokładnie sprasowany na płasko za pomocą imadło ławkowe. Ta wanna formująca ma rowek, w którym można skręcić drut wiązałkowy. Wymaga to czasu i cierpliwości, ponieważ ostrożnie obracasz o około 1/5 obrotu, naciskasz, obracasz i kontynuujesz pracę. Dzięki temu dysk jest płaski i cienki, jednocześnie umożliwiając uzwojenie końcowe. Możesz zauważyć, że moje 4-płatkowe uzwojenie ma proste „nogi”, ale połączenia wewnętrzne i zewnętrzne nie są okrągłe. Miało to ułatwić im układanie w stosy. Nie wyszło tak dobrze. Gdybym robił to jeszcze raz, sprawiłbym, że wewnętrzne i zewnętrzne uzwojenia końcowe poruszałyby się po okrągłych ścieżkach.
Po spłaszczeniu i spłaszczeniu krawędzi, owinąłem płaską wstążkę wokół krawędzi, aby ją zagęścić, a następnie kolejną w górę, w dół i wokół każdej nogi, a następnie również do tej obok niej. Po wykonaniu tej czynności możesz usunąć druty wiązałkowe i przełączyć się na mniejszą wannę prasującą, a następnie wrócić do imadła i docisnąć je tak cienko i płasko, jak to możliwe. Gdy jest płaski, wyjmij z wanny prasy. Zamiast skomplikowanego procesu ostrożnego woskowania i powlekania form środkami antyadhezyjnymi, zazwyczaj używam tylko kilku warstw folii stretch (z kuchni). Ułóż kilka warstw na dnie formy i połóż włókno szklane na folii stretch. Następnie dodaj rurkę montażową stojana, która pasuje do górnej części jasnozielonego wanny formującej, ale ma między sobą warstwę folii stretch i włókna szklanego. Następnie dodaj uzwojenie stojana z powrotem na miejsce, aby wcisnąć zarówno folię rozciągliwą, jak i włókno szklane i zablokować rurkę montażową stojana na miejscu. Następnie wróć do imadła i ponownie naciśnij płasko. Po dopasowaniu do wanny, z włożoną folią stretch i włóknem szklanym, dodaje się tkaninę z włókna szklanego (z otworem w środku na rurkę montażową stojana).
Teraz jest gotowy do wylania materiału wiążącego, powszechnie używa się żywicy epoksydowej lub poliestrowej. Zanim to nastąpi, staranne przygotowanie jest ważne, ponieważ po rozpoczęciu tego procesu nie można go zatrzymać. Użyłem drukowanej w 3D płyty bazowej, którą wcześniej wykonałem, z otworem 1" w środku i płaską płytą wokół niej. Użyłem 16" kawałka 1" aluminiowej rury, do której pasowałaby rura montażowa stojana i była trzymane prostopadle do płaskiej płyty. Zielona wanna formująca, uzwojenie stojana i rurka montażowa stojana zostały zsunięte, aby usiąść na płaskiej płycie. Przed zmieszaniem żywicy epoksydowej najpierw przygotowałem 4 kawałki folii termokurczliwej i ostrożnie umieściłem piąty kawałek na ciemnozielony formujący pączek, żeby miał jak najmniej zmarszczek na twarzy względem uzwojenia stojana. Po wymieszaniu żywicy epoksydowej i wylaniu jej na tkaninę z włókna szklanego, następnie ostrożnie rozłożyłem folię stretch wokół 1" rurki i umieściłem zielony tworząc pierścień na nim. Przygotowałem też kilka starych tarcz hamulcowych, które dawały trochę wagi i ładnie usiadłem na zielonym pączku. Następnie postawiłem odwrócony garnek na tarcze hamulcowe, a na wierzch garnka ułożyłem około 100 funtów materiału. Zostawiłem to na 12 godzin i wyszedł około 4-6mm grubości.
Krok 4: Testowanie i czujniki
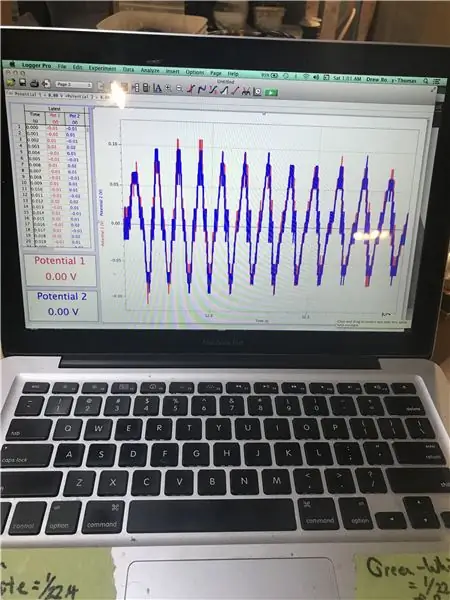
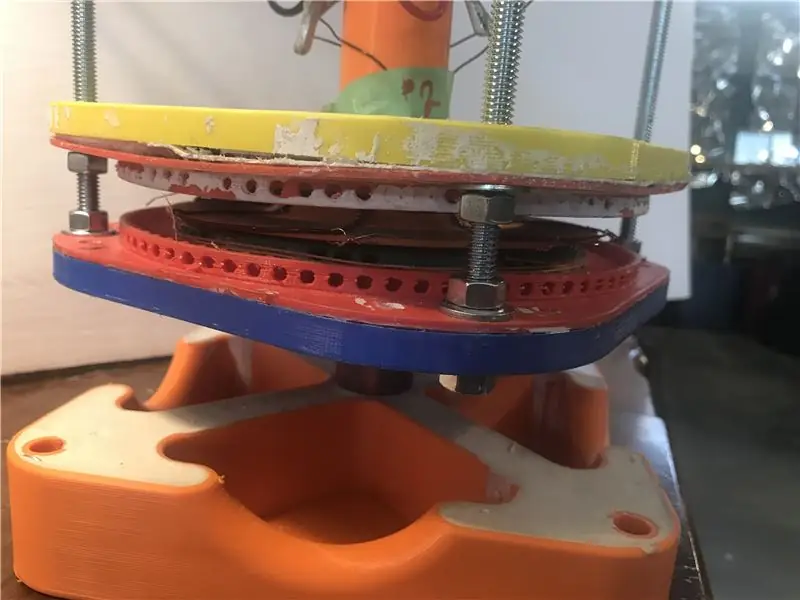
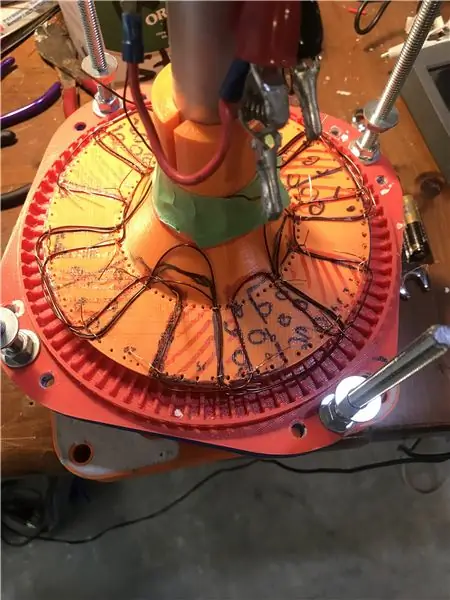
Istnieje wiele mierzalnych wejść i wyjść z alternatora, a pomiar ich wszystkich jednocześnie nie jest łatwy. Mam szczęście, że mam kilka narzędzi od Verniera, które znacznie to ułatwiają. Vernier tworzy produkty na poziomie edukacyjnym, nie certyfikowane do użytku przemysłowego, ale bardzo pomocne dla eksperymentatorów takich jak ja. Używam rejestratora danych Verniera z różnymi czujnikami typu plug and play. W tym projekcie używam sond prądowych i napięciowych opartych na technologii Halla do pomiaru mocy alternatora, czujnika optycznego do określania prędkości alternatora oraz ogniwa obciążnikowego do pomiaru wejściowego momentu obrotowego. Wszystkie te instrumenty są próbkowane około 1000 razy na sekundę i rejestrowane na moim laptopie przy użyciu rejestratora Verniera jako urządzenia przekazującego AD. Na moim laptopie powiązane oprogramowanie może wykonywać obliczenia w czasie rzeczywistym na podstawie danych wejściowych, łącząc dane dotyczące momentu obrotowego i prędkości, aby uzyskać moc wejściową wału w czasie rzeczywistym w watach oraz dane wyjściowe w czasie rzeczywistym w watach elektrycznych. Nie skończyłem z tymi testami, a informacje od kogoś, kto ma lepsze zrozumienie, byłyby pomocne.
Problem, który mam, polega na tym, że ten alternator jest tak naprawdę projektem pobocznym, więc nie chcę poświęcać mu zbyt wiele czasu. W obecnej sytuacji myślę, że mogę go użyć do kontrolowanego obciążenia w moich badaniach nad VAWT, ale ostatecznie chciałbym pracować z ludźmi, aby go dopracować, aby był wydajnym dopasowaniem do mojej turbiny.
Kiedy zacząłem badać VAWT około 15 lat temu, zdałem sobie sprawę, że testowanie VAWT i innych sił napędowych jest bardziej złożone, niż większość ludzi zdaje sobie sprawę.
Podstawowym problemem jest to, że energia reprezentowana w poruszającym się płynie jest wykładnicza do szybkości jego ruchu. Oznacza to, że gdy podwoisz prędkość przepływu, energia zawarta w przepływie wzrasta 8x (jest sześcienna). Jest to problem, ponieważ alternatory są bardziej liniowe i ogólnie, jeśli podwoisz obroty alternatora, uzyskasz około 2x więcej watów.
Ta fundamentalna rozbieżność między turbiną (urządzeniem gromadzącym energię) a alternatorem (moc na wale do użytecznej mocy elektrycznej) utrudnia wybór alternatora dla turbiny wiatrowej. Jeśli wybierzesz pasujący alternator do swojej turbiny wiatrowej, który będzie generował największą moc przy wietrze o prędkości 20 km/h, prawdopodobnie nie zacznie się obracać nawet do 20-25 km/h, ponieważ obciążenie turbiny z alternatora będzie zbyt duże. Przy takim dopasowaniu z alternatorem, gdy wiatr przekroczy 20 km, turbina nie tylko przechwyci tylko część energii dostępnej w wietrze o wyższej prędkości, ale turbina może przekroczyć prędkość i ulec uszkodzeniu, ponieważ obciążenie zapewniane przez alternator nie jest duże wystarczająco.
W ostatniej dekadzie rozwiązanie stało się bardziej ekonomiczne ze względu na spadek cen elektroniki sterującej. Zamiast próbować dopasować zakres prędkości, projektant oblicza maksymalną prędkość, z jaką urządzenie ma działać, i wybiera alternator na podstawie ilości energii i idealnej prędkości dla turbiny przy tej lub nieco wyższej prędkości.. Ten alternator, jeśli jest podłączony do jego obciążenia, normalnie zapewniałby zbyt duży moment obrotowy przy niskich obrotach, a przeciążona turbina nie przechwyci całej energii, jaką mogłaby mieć, gdyby była odpowiednio obciążona. Aby wytworzyć właściwe obciążenie, dodawany jest sterownik, który na chwilę odłącza alternator od obciążenia elektrycznego, umożliwiając turbinie rozpędzanie się do odpowiedniej prędkości, a alternator i obciążenie zostają ponownie połączone. Nazywa się to MPPT (Multi Power Point Tracking). Sterownik jest zaprogramowany w taki sposób, że wraz ze zmianą prędkości turbiny (lub wzrostem napięcia alternatora), alternator jest podłączany lub odłączany mniej więcej tysiąc razy na sekundę, aby dopasować obciążenie zaprogramowane dla tej prędkości lub napięcia.
Zalecana:
Interfejs 3-osiowego czujnika żyroskopowego BMG160 z Arduino Nano: 5 kroków
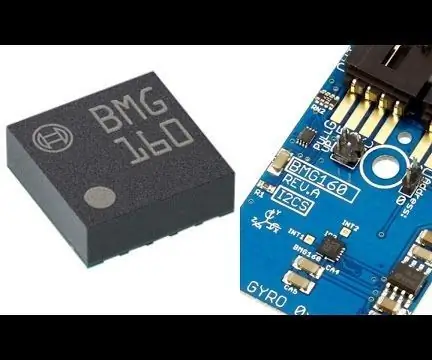
Interfejs 3-osiowego czujnika żyroskopowego BMG160 z Arduino Nano: w dzisiejszym świecie ponad połowa młodzieży i dzieci lubi gry, a wszyscy ci, którzy to lubią, zafascynowani technicznymi aspektami gier, wiedzą, jak ważne jest wykrywanie ruchu w tej dziedzinie. Byliśmy również zdumieni tym samym
Przeważnie drukowany w 3D przełącznik kołyskowy: 4 kroki (ze zdjęciami)
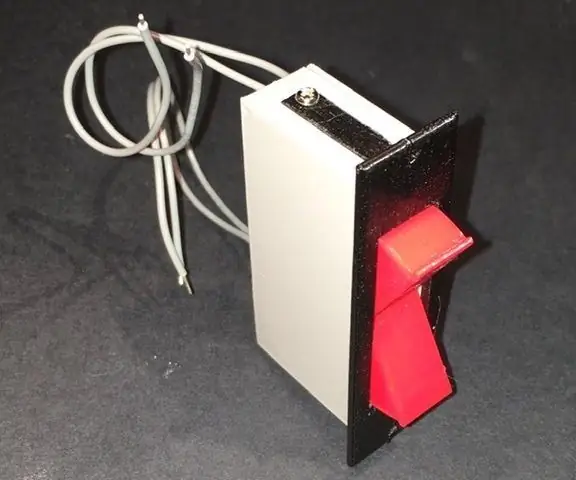
Przeważnie drukowany w 3D przełącznik kołyskowy: Instruktaż to kolejna eksploracja tego, co można osiągnąć za pomocą skromnego magnetycznego kontaktronu i kilku magnesów neodymowych. Do tej pory za pomocą kontaktronów i magnesów zaprojektowałem: Przełącznik obrotowy Przełącznik suwakowy Przełącznik Push Bu
Przeważnie drukowany w 3D enkoder binarny: 4 kroki (ze zdjęciami)
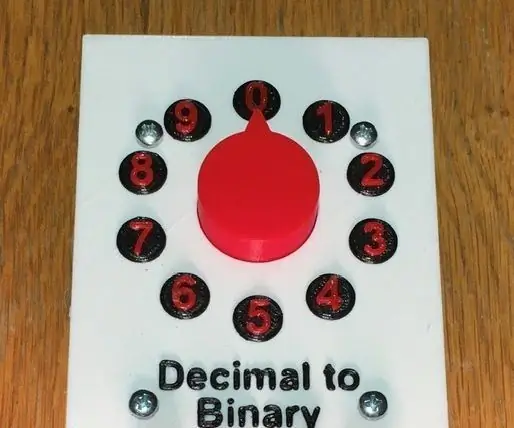
Przeważnie drukowany w 3D koder binarny: Koder konwertuje informacje z jednego formatu lub kodu na inny. Urządzenie przedstawione w tej instrukcji konwertuje tylko liczby dziesiętne od 0 do 9 na ich odpowiedniki binarne. Przedstawione tu koncepcje można jednak wykorzystać do tworzenia
Konfigurowanie strumienia Twitch.: 7 kroków
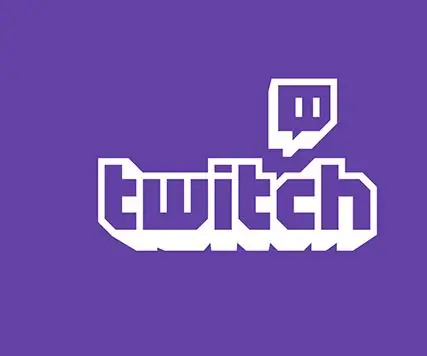
Konfigurowanie strumienia Twitch.: Dzisiaj pokażę, jak rozpocząć transmisję na twitch.tv za pomocą oprogramowania Open Broadcasting. Jest to wykorzystywane do projektu pisania technicznego. Mam nadzieję, że to pomoże Ci skonfigurować transmisję.***O czym należy pamiętać: nie można streamować
Uproszczony, drukowany w 3D mechanizm podwójnego oka Animatronic: 4 kroki (ze zdjęciami)
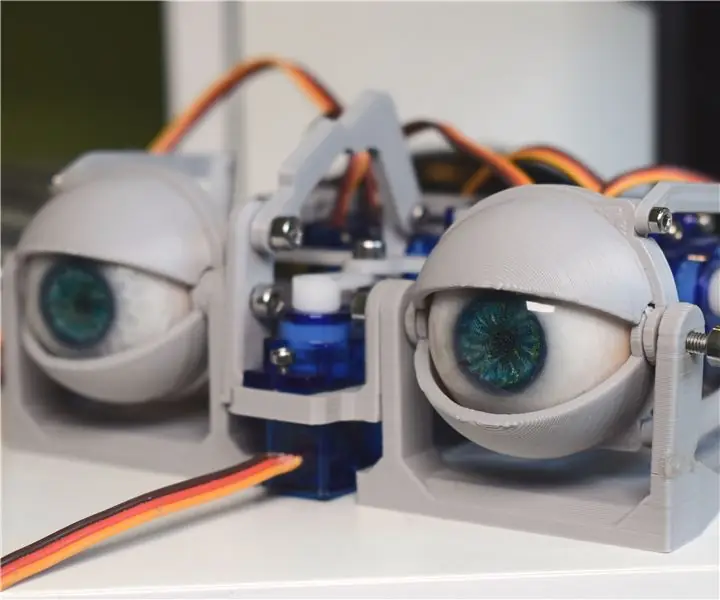
Uproszczony, drukowany w 3D, animatroniczny mechanizm podwójnego oka: Po zbudowaniu w przeszłości prostego mechanizmu z jednym okiem, chciałem ulepszyć projekt, a także uczynić go bardziej dostępnym dla społeczności twórców. Zaktualizowany montaż wykorzystuje części, które można łatwo kupić online, a prawie wszystkie komponenty mogą