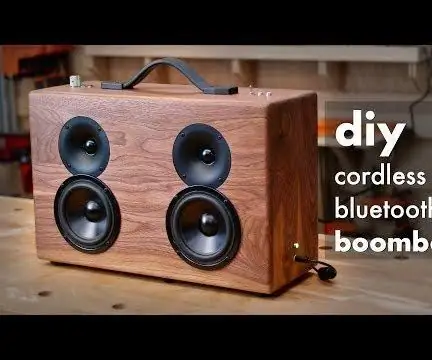
Spisu treści:
- Krok 1: Narzędzia i materiały
- Krok 2: Frezowanie
- Krok 3: Ponowne piłowanie
- Krok 4: orientowanie tablic
- Krok 5: Klej i frezuj
- Krok 6: Otwory głośnikowe
- Krok 7: Routing
- Krok 8: Rozdzielacz środkowy
- Krok 9: Ostateczne kształtowanie
- Krok 10: Lutowanie
- Krok 11: Wiercenie
- Krok 12: Porty
- Krok 13: Wykończenie
- Krok 14: Ostatnie kroki
2025 Autor: John Day | [email protected]. Ostatnio zmodyfikowany: 2025-01-23 15:02
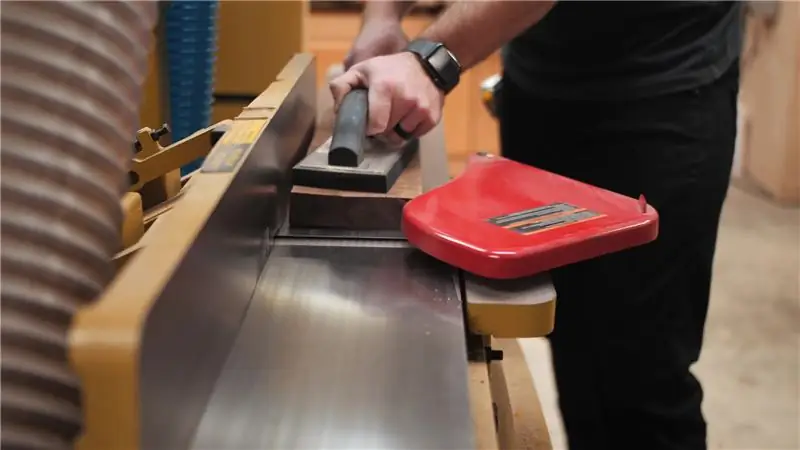
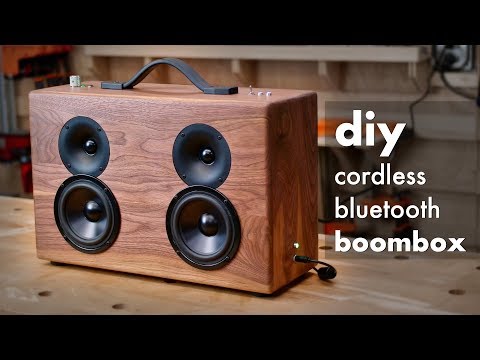
Zbudowałem ten przenośny, zasilany bateryjnie, przenośny głośnik typu boombox Bluetooth, używając zestawu głośnikowego Parts Express C-Note oraz płyty wzmacniacza KAB (linki do wszystkich części poniżej). To była moja pierwsza konstrukcja głośnika i jestem szczerze zdumiony, jak niesamowicie to brzmi.
Dzięki Kirby Meets Audio za pomoc w planowaniu, sprawdź jego kanał tutaj.
Ten boombox jest mocno inspirowany tym boomboxem The Hifi Case, jeśli chcesz kupić głośnik taki jak ten, sprawdź ich tutaj.
Kup gadżety „Zbuduj to sam”!
Krok 1: Narzędzia i materiały
Materiały:
- Zestaw głośników półkowych Parts Express C-Note
- Płyta wzmacniacza Dayton Audio KAB-250v3
- Pakiet kabli funkcyjnych Dayton Audio KAB-FC
- Moduł rozszerzenia baterii Dayton Audio KAB-BE 18650
- Dayton Audio KAB-PMV3 Panel Mount (nie było to dostępne, gdy budowałem mojego boomboxa, uprościłoby to)
- Pianka akustyczna Sonic Barrier 1/2 (potrzebne 2 arkusze)
- Biała perforowana deska crossover
- Czarne śruby
- Gniazdo DC do montażu na panelu 2,5 mm
- Pokrętło głośności
- 18650 baterii
- Zasilacz
- Gumowe nóżki
- Zaciskane terminale
- Uchwyt
- Poliuretan do wycierania
Narzędzia:
- Ukośnica Festool Kapex
- Wiertarko-wkrętarka akumulatorowa Festool CXS
- Wiertarko-wkrętarka akumulatorowa Festool PDC 18/4
- Szlifierka Festool ETS EC 150/5
- Frezarka górnowrzecionowa Festool OF 1400
- Strugarka Powermatic 15HH
- Łącznik Powermatic PJ-882HH
- Wynalazki X-Carve
- Wiertło do zaokrąglania promieni 3/8"
- Bit przycinania wpuszczanego
- Zaciski równoległe
- Pogłębiacz stożkowy
- Piła taśmowa
- Piła stołowa z piór
- Cyfrowy miernik kąta
Krok 2: Frezowanie
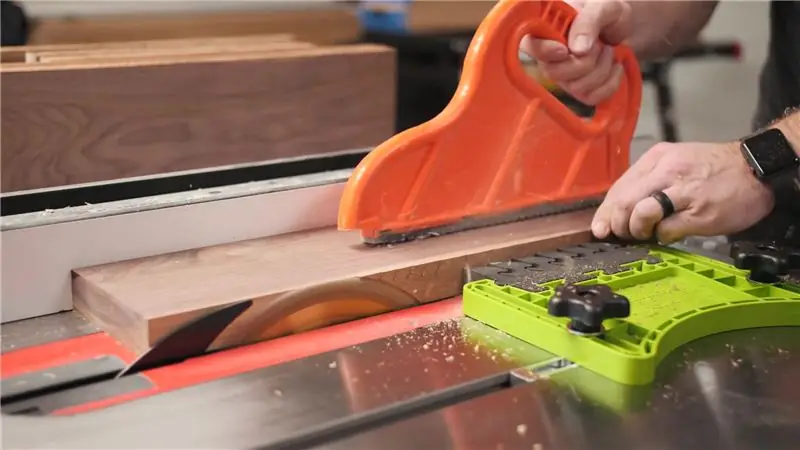
Zbudowałem ten boombox z litego orzecha włoskiego, więc zacząłem od rozbicia mojego szorstkiego drewna na poszczególne kawałki. Jeśli chcesz uprościć tę konstrukcję, możesz użyć materiałów arkuszowych, takich jak sklejka lub MDF, lub po prostu kupić wstępnie wyfrezowaną tarcicę.
Po przycięciu desek na zgrubną długość za pomocą piły ukośnej, wyrównałem je na wyrówniarce, strugarce i piły stołowej.
Kupiłem orzech o grubości 6/4 lub 1 ½” do tej konfiguracji i chciałem uzyskać końcową grubość ½” na tych deskach, więc następnie musiałem ponownie przeciąć wszystkie moje deski, zasadniczo dzieląc je na pół.
Krok 3: Ponowne piłowanie
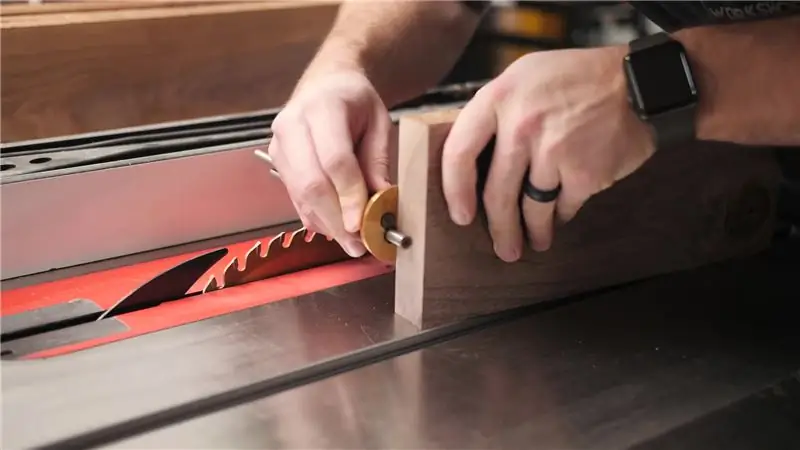
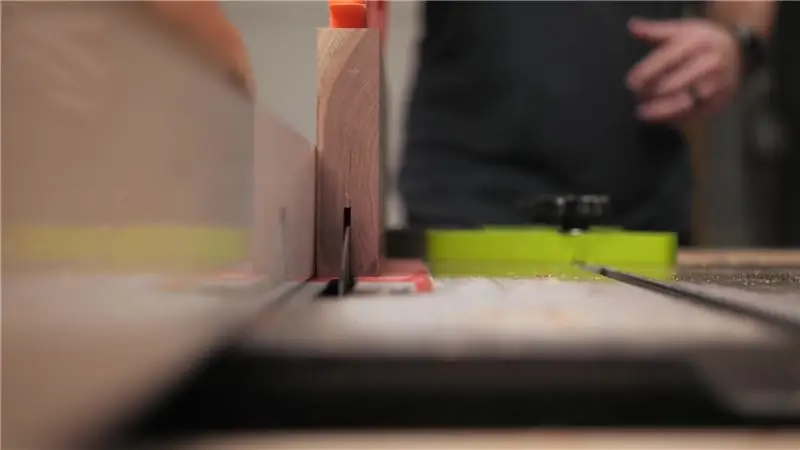
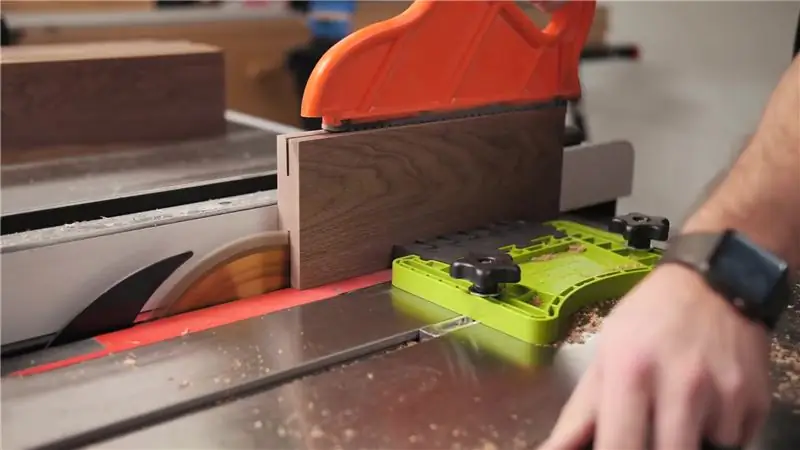
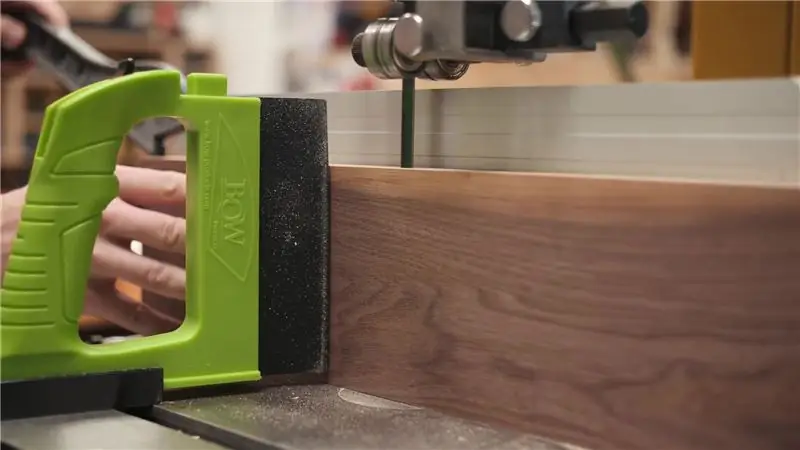
Brzeszczot mojej piły taśmowej był bardzo tępy, więc postanowiłem wykonać większość pracy piłą stołową. Aby to zrobić, najpierw zaznaczyłem środek deski za pomocą znacznika, a następnie ustawiłem płot tak, aby ostrze przechodziło przez środek deski. Dodałem również pióropusz, aby utrzymać deskę dociśniętą do ogrodzenia.
Chciałem wykonać to cięcie w wielu przejściach, więc zacząłem od ostrza około cala wokół stołu i wykonałem pierwsze przejście. Następnie obróciłem deskę jednym końcem, upewniając się, że ta sama ściana była przy ogrodzeniu, a następnie wykonałem podanie po drugiej stronie deski.
Powtórzyłem ten proces dla wszystkich desek, a następnie podniosłem ostrze na tyle wysoko, aby około ¾” materiału pozostało na środku desek. Nie chciałem przecinać całej piły stołowej, po prostu usunąć większość odpadów. Powtórzyłem kroki z wyższym ostrzem, a następnie podszedłem do piły taśmowej.
Ustawiłem kolejną deskę z piór przy piły taśmowej, aby pomóc utrzymać nacisk na deski, a następnie ponownie przepiłowałem wszystkie deski, całkowicie je rozłupując.
W końcu przy strugarce mogłem całkowicie wyrównać deski i usunąć mały grzbiet pozostawiony na środku desek.
Przed sklejeniem paneli musiałem przyciąć niektóre deski i usunąć niektóre obszary, które mi się nie podobały estetycznie, takie jak obszary bielu.
Krok 4: orientowanie tablic
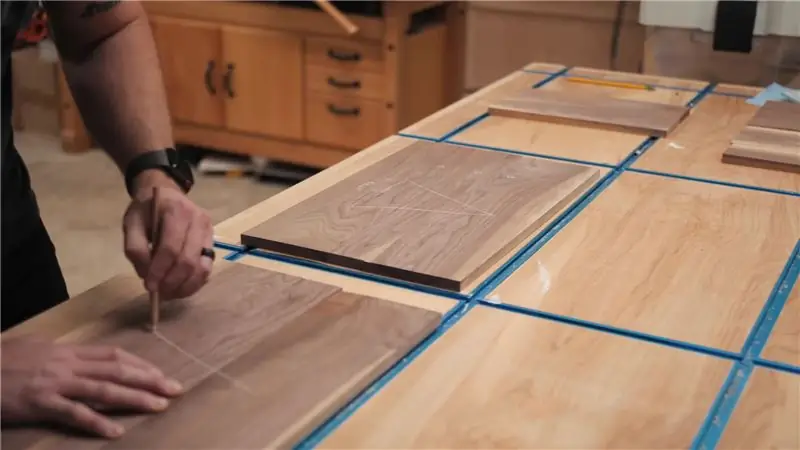
Gdy wszystkie deski zostały przycięte na wymiar, ułożyłem je w orientacji, którą uważałem za najlepszą, a następnie oznaczyłem je, aby nie pomylić ich podczas klejenia.
Ostatnim krokiem przed nałożeniem kleju było połączenie każdej krawędzi, aby upewnić się, że mam idealne linie kleju. Użyłem tej małej sztuczki, którą nauczyłem się od mojego kumpla Jaya Batesa, w którym łączysz dwie pasujące deski z przeciwną powierzchnią każdej deski do ogrodzenia wyrówniarki.
Widać, że skierowałem moją linię ołówkową w kierunku ogrodzenia na pierwszej desce, a następnie oddaliłem się od ogrodzenia na drugiej desce. To skutecznie zanegowało każdy najmniejszy błąd w prostopadłości mojego ogrodzenia i zapewniło, że skończyłem z płaskim panelem.
Krok 5: Klej i frezuj
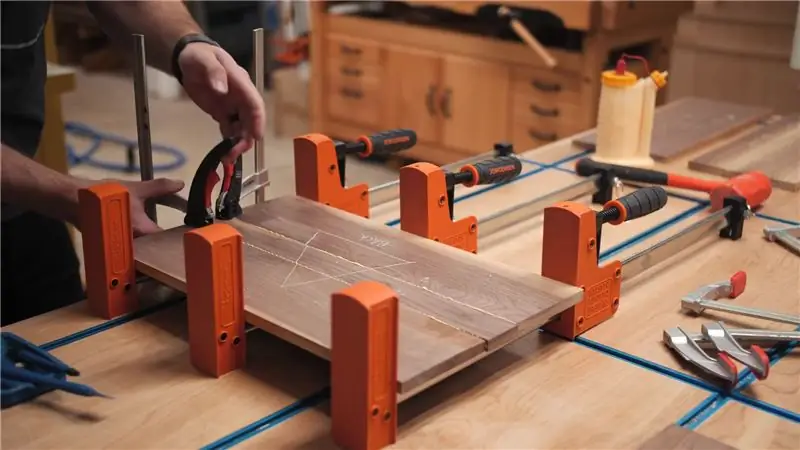
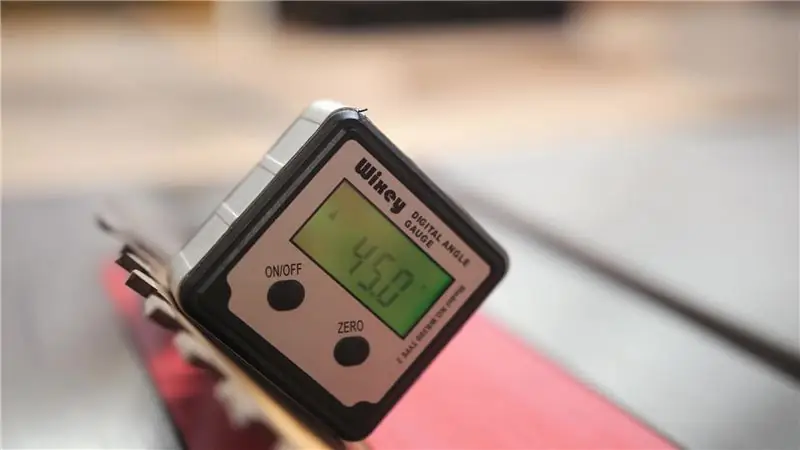
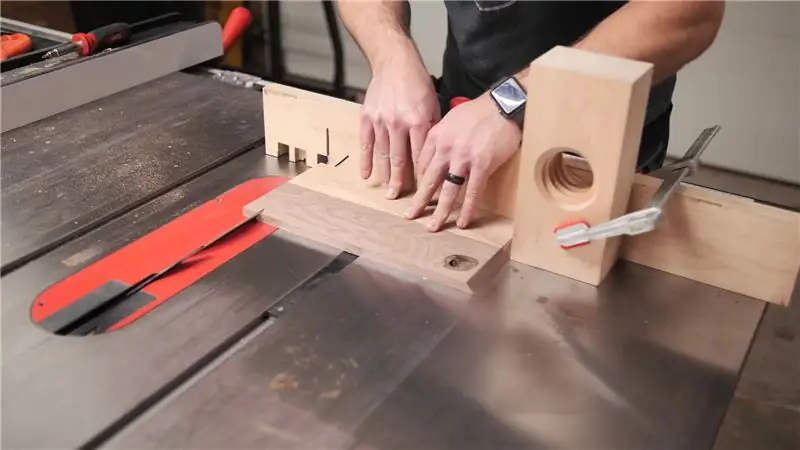
Wreszcie mogłem skleić panele. Nie użyłem niczego do wyrównania na tych deskach, głównie dlatego, że było ich tak wiele, i upewniłem się, że dodałem zaciski na końcach szwów, aby utrzymać je w linii.
Po pozostawieniu desek na kilka godzin w zaciskach, zeskrobałem klej, a następnie przepuściłem je przez strugarkę, aby je wyczyścić.
Po oczyszczeniu desek mogłem rozerwać górne, dolne i boczne panele do ostatecznej szerokości na piły stołowej, ponownie używając deski z piór, aby utrzymać stały nacisk na ogrodzenie.
Następnie ustawiłem ostrze na 45 stopni i zacząłem ciąć ukosy. Najpierw przyciąłem ukośną końcówkę każdej z desek tworzących ramę pudełka.
Z jednym końcem przyciętym pod kątem 45 stopni, ustawiłem blok oporowy na moim mierniku ukośnym, aby przyciąć ukos na drugim końcu desek. Dzięki temu moje panele górne i dolne wraz z panelami bocznymi miały dokładnie taką samą długość.
W końcu mogłem skleić pudełko i użyłem do tego kombinacji zacisków na pasek i zacisków narożnych. Skończyło się na idealnie kwadratowym pudełku i ukośnikach bez szczelin, co zawsze jest miłe.
Po przyklejeniu ramy pudełka mogłem przyciąć przedni i tylny panel do ostatecznego rozmiaru w oparciu o ostateczny rozmiar ramy, i zrobiłem to na piły ukośnej.
Krok 6: Otwory głośnikowe
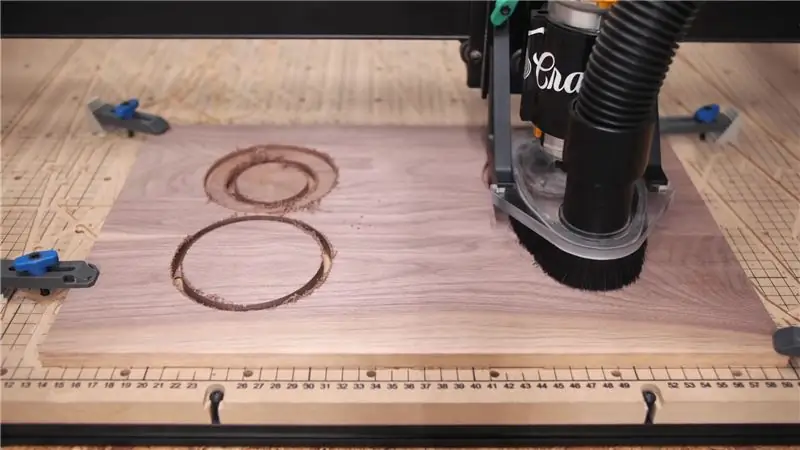
Następnie musiałem wyciąć otwory na głośniki w przednim panelu. Zestaw głośnikowy, którego użyłem, zestaw C-Note firmy Parts Express, jest dostarczany z obudowami MDF i można łatwo użyć płaskiego wykończenia i użyć tych obudów jako szablonów do wycięcia tych otworów, ale pomyślałem, że pozwolę X-Carve wykonaj dla mnie pracę.
Stworzyłem szybki projekt w Easel, darmowym oprogramowaniu CAM Inventables, i wykonałem cięcie testowe na kawałku sklejki ½”, aby upewnić się, że wszystko będzie pasować. Kiedy już wszystko pasowało, wykonałem ostateczne cięcie na panelu orzecha włoskiego. Cała ta operacja zajęła tylko około 13 minut, super szybka z bitem ¼”.
Po zakończeniu X-Carve wyciąłem zakładki utrzymujące resztki na miejscu, a następnie wyczyściłem wszystko za pomocą golenia i papieru ściernego.
Krok 7: Routing
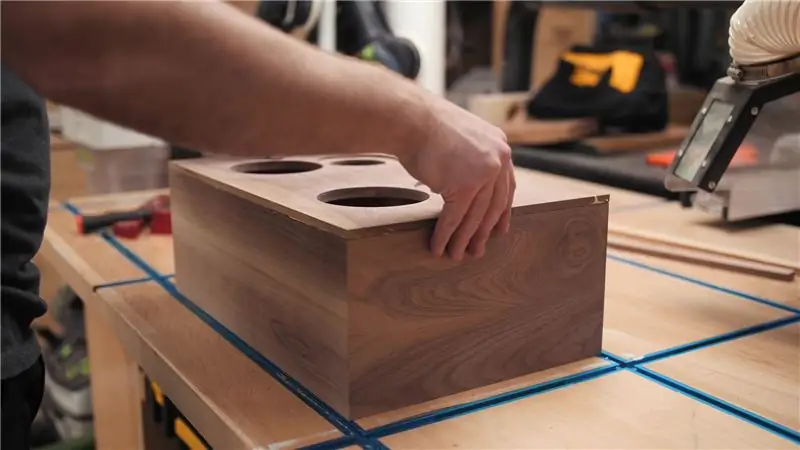
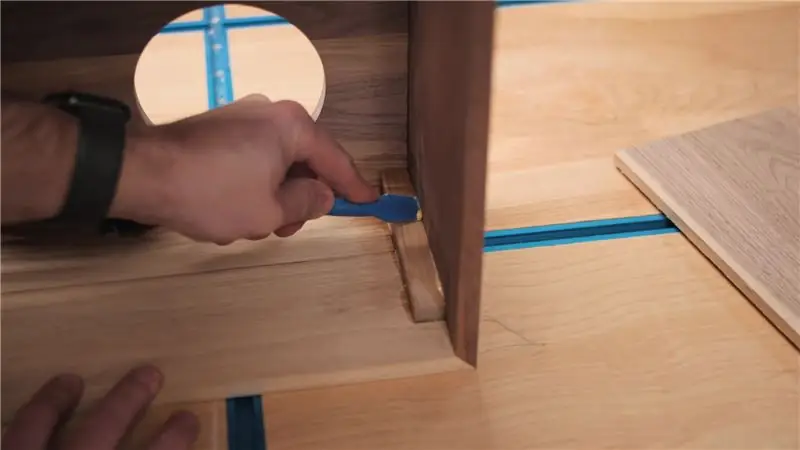
Chciałem nieco zagłębić przednie i tylne panele w ramie, aby zapewnić panelom bezpieczniejszy zestaw, więc następnie ustawiłem stół routera tak, aby wyciąć wręg o szerokości 1/2 cala i głębokości 3/4 cala. Przyciąłem te wręgi na wszystkich czterech krawędziach przedniego i tylnego panelu, upewniając się, że najpierw przyciąłem wręgi na długich krawędziach, aby zapobiec rozerwaniu końcowego słojów.
Następnie przykleiłem przedni panel do ramy i upewniłem się, że użyłem do tego dużej ilości kleju i zacisków. Potrzebujesz hermetycznej uszczelki na głośnikach, więc naprawdę nie możesz przesadzić z zaciskami.
Wiedziałem, że chcę ciężkiego zaokrąglenia na wszystkich krawędziach tego głośnika, a to oznaczałoby usunięcie dużej ilości materiału z rogów. Z tego powodu chciałem wzmocnić rogi i po prostu użyłem do tego kilku klocków po wewnętrznej stronie głośnika.
Do mocowania bloków użyłem kombinacji kleju CA i kleju do drewna, a klej CA zasadniczo utrzymywał bloki na miejscu, gdy klej do drewna wysychał.
Musiałem też dodać trochę więcej klocków po wewnętrznej stronie górnego i dolnego panelu i tam połączą się śruby mocujące tylny panel, który chciałem zdemontować.
Krok 8: Rozdzielacz środkowy
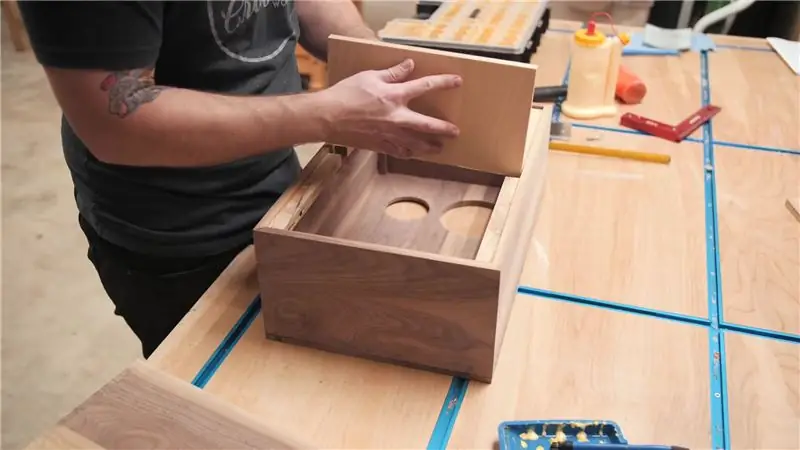

Ostatnim elementem dodanym do głośnika była środkowa przegroda, o której szczerze zapomniałem. Widać, że musiałem wyciąć klocki na górze i na dole, aby zrobić miejsce na przegrodę, którą wyciąłem ze sklejki ½” Baltic Birch. Ponownie upewniłem się, że użyłem tutaj dużej ilości kleju, ponieważ chciałem szczelnego zamknięcia.
Musiałem również dodać kolejny felc na środku tylnego panelu, aby nie kolidował z środkową przegrodą, i przeciąłem go na piłce stołowej.
Zacisnąłem tylny panel na miejscu, wstępnie wywierciłem i pogłębiłem otwory, a następnie dodałem 1 calowe śruby, aby utrzymać tylny panel na miejscu.
Krok 9: Ostateczne kształtowanie
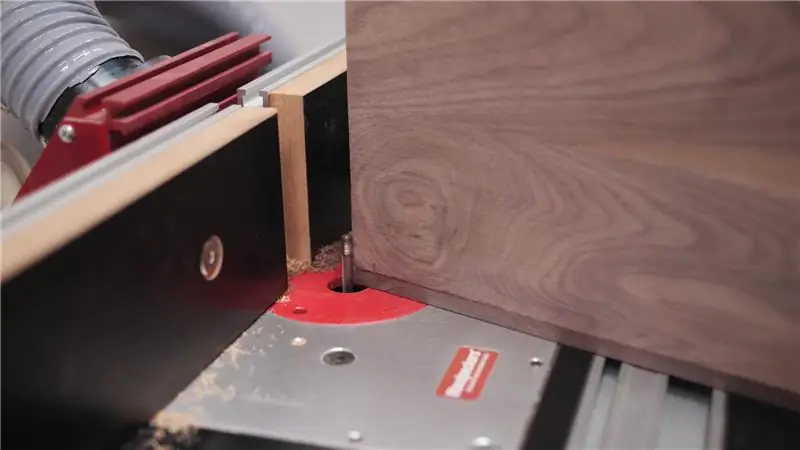
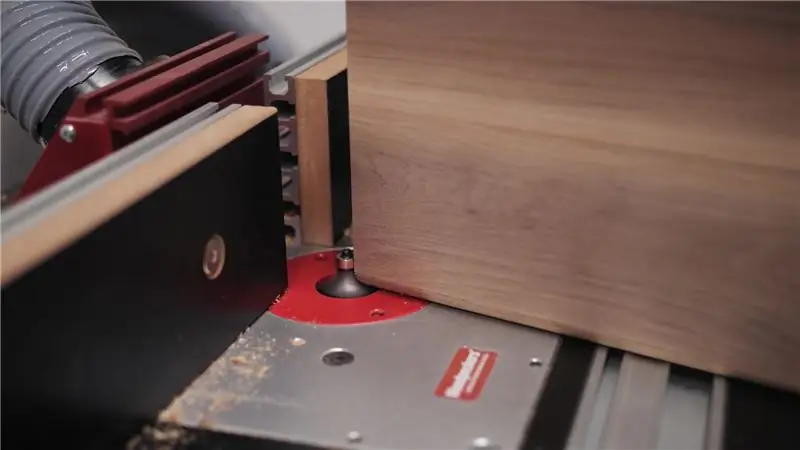
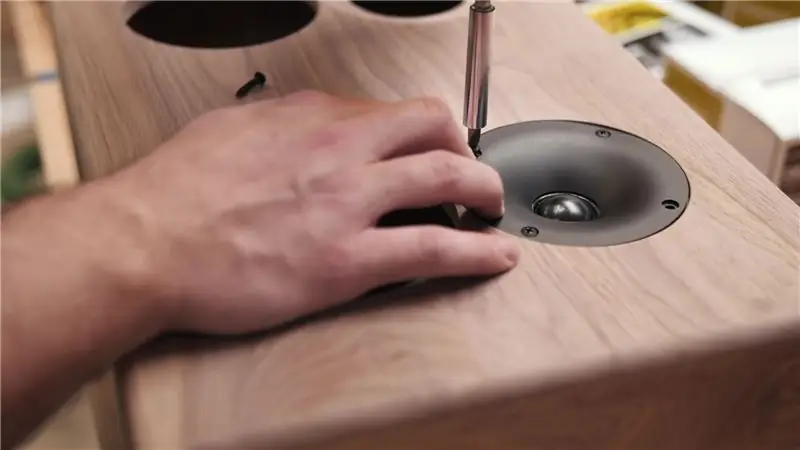
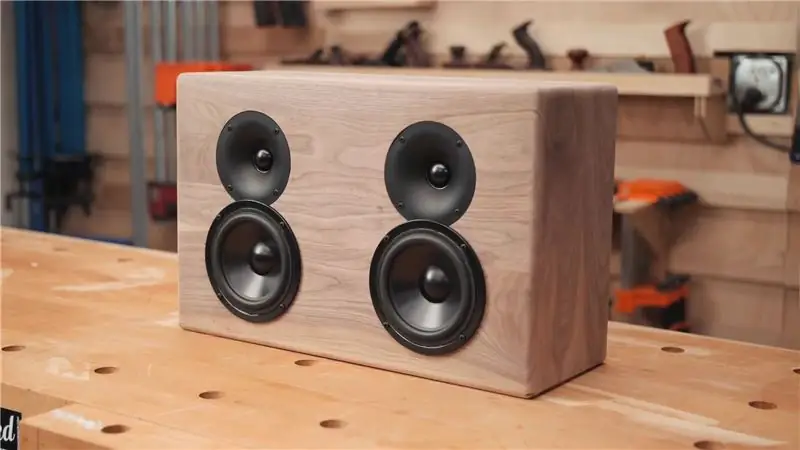
Po zbudowaniu pudełka mogłem przejść do sprzątania. Najpierw użyłem płaskiego wiertła do przycinania na stole routera, aby wyczyścić wszelkie zwisające obszary na przednim i tylnym panelu, które przyciąłem nieco za duże.
Gdy krawędzie zostały wyrównane, zamieniłem się na bit zaokrąglenia o promieniu ⅜” i dodałem zaokrąglenie do wszystkich krawędzi pudełka. Zawsze jestem zdumiony, jak wielką różnicę robi taki ciężki profil krawędzi, i naprawdę myślę, że ta zaokrąglona opona sprawiła, że wygląd głośnika.
Wreszcie mogłem zainstalować głośniki, co było proste. Po prostu upewniłem się, że otwory na śruby są prostopadłe do obudowy i użyłem samocentrującego wiertła do wstępnego nawiercenia otworów. Następnie użyłem czarnych śrub ¾” do zamocowania głośników i mogłem zrobić zdjęcie piękna dla moich mediów społecznościowych.
Krok 10: Lutowanie
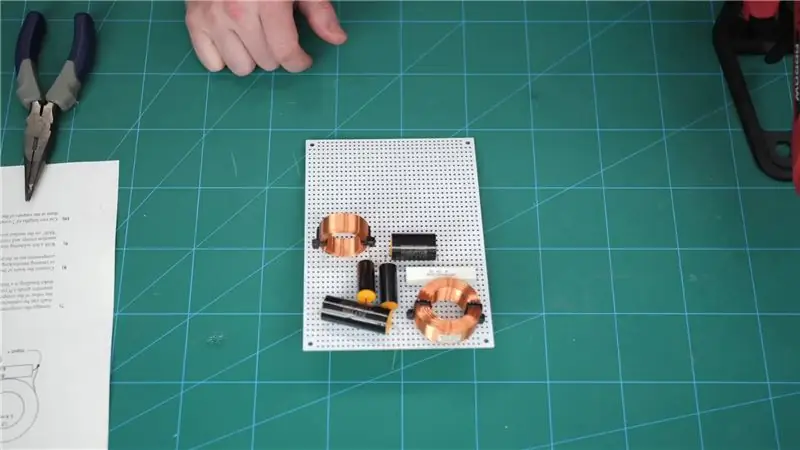
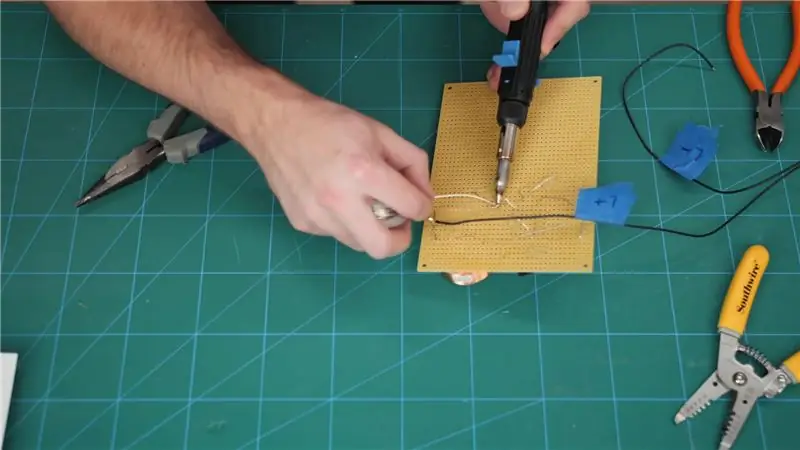
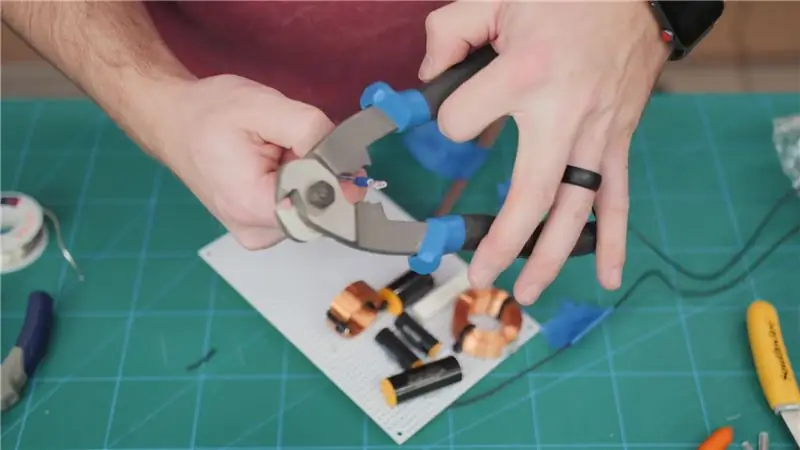
Następna w kompilacji była ta część, którą trochę się denerwowałem, budowanie zwrotnic. To było moje pierwsze lutowanie i było tu mnóstwo połączeń do lutowania. Jeśli nie wiesz, zwrotnice dzielą sygnał audio między głośnik niskotonowy i wysokotonowy, wysyłając wyższe częstotliwości do głośników wysokotonowych i niższe częstotliwości do głośników niskotonowych.
Znowu te zwrotnice były częścią zestawu głośnikowego C-Note, którego użyłem do tego projektu, i istnieją bardzo szczegółowe instrukcje dotyczące okablowania zwrotnic dołączone do tego zestawu. Zasadniczo musiałem połączyć różne komponenty samej zwrotnicy, a także dodać okablowanie, aby podłączyć zwrotnice do głośników oraz do wzmacniacza.
Podczas lutowania porozmawiajmy o sponsorze tego tygodnia, Bernzomatic.
W tym projekcie użyłem zarówno bezprzewodowej lutownicy Bernzomatic ST500, jak i palnika szczegółowego ST2200T, które doskonale nadają się do lutowania. Obie latarki są zasilane butanem, co oznacza, że są bezprzewodowe i całkowicie przenośne, idealne, jeśli potrzebujesz lutować coś z dala od gniazdka.
Do tego projektu użyłem również lutu elektrycznego Bernzomatic z rdzeniem kalafonii, który był niezwykle prosty w użyciu, nie wymagał topnika. Niezależnie od tego, czy jesteś profesjonalnym rzemieślnikiem, majsterkowiczem, rzemieślnikiem, rzemieślnikiem czy szefem kuchni, Bernzomatic ma odpowiedni produkt do niezliczonych projektów. Aby dowiedzieć się więcej o palnikach lutowniczych, lutownicach i innych produktach Bernzomatic, sprawdź link w opisie filmu poniżej i jeszcze raz dziękuję Bernzomatic za sponsorowanie filmu w tym tygodniu.
Po przylutowaniu gniazda zasilania do wyprowadzeń z płytki wzmacniacza, mogłem rozebrać końce przewodu głośnikowego i dodać te zaciskane końcówki, aby łatwo podłączyć przewód głośnikowy do głośników.
Krok 11: Wiercenie
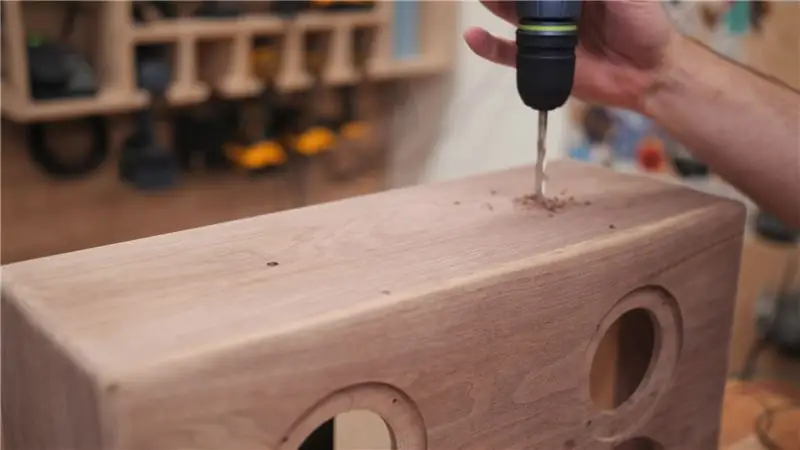
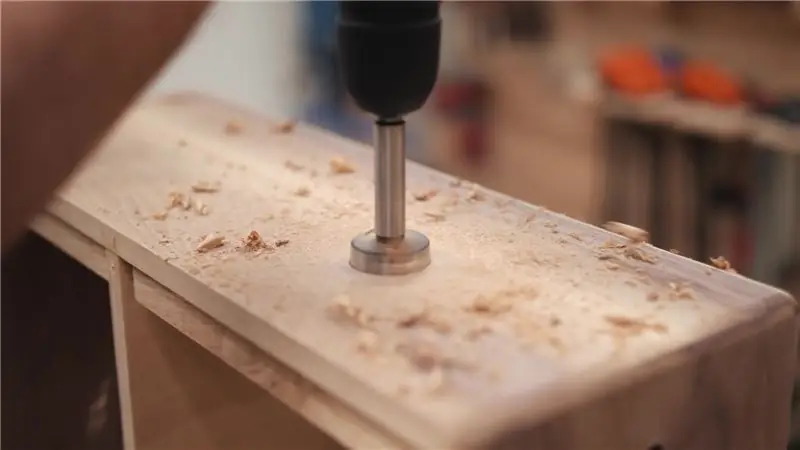
Po ukończeniu całego okablowania mogłem przejść do dodawania otworów na różne porty, diody LED, przełączniki i uchwyt do przenoszenia. Była to jedna z bardziej uciążliwych części konstrukcji, ponieważ wiele z tych elementów miało słupki o różnych rozmiarach, więc musiałem użyć suwmiarki, aby znaleźć odpowiedni rozmiar wiertła do wstępnego nawiercenia otworów.
Musiałem również użyć wiertła Forstner po wewnętrznej stronie szafki, aby umożliwić przejście komponentów. Większość z tych części miała tylko gwintowany obszar o długości około ¼”, więc musiałem zagłębić te otwory, aby umożliwić gwintowanym obszarom wystawanie przez obudowę.
Dodałem również gumowe nóżki na spodzie obudowy głośnika, aby nie grzechotał podczas odtwarzania muzyki.
Krok 12: Porty
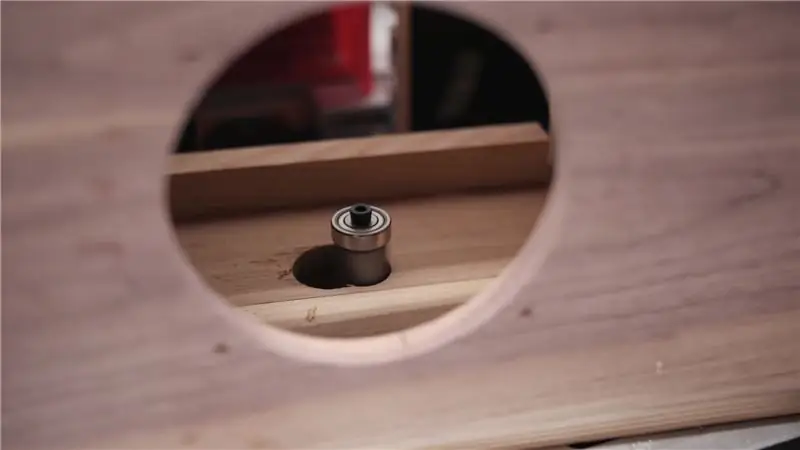
Ostatnie otwory, które musiałem wywiercić, dotyczyły portów na spodzie szafki. Te porty miały średnicę 1”, a ja nie posiadam wiertła 1”, więc musiałem tu trochę kreatywności.
Najpierw wywierciłem wiertłem Forstner otwór 1 ¼”, najbliższym rozmiarem wiertła, jaki miałem pod ręką, a następnie użyłem X-Carve do wycięcia szablonu. Następnie zamontowałem w stole frezarskim wpuszczany frez, przymocowałem szablon do dolnej części szafki za pomocą taśmy dwustronnie klejącej i wyprowadziłem otwór.
Oczywiście można było po prostu kupić odpowiedni rozmiar wiertła Forstnera, ale nie mogłem go znaleźć lokalnie, dzięki temu zaoszczędziłem dwadzieścia dolców i pomyślałem, że to sprytne rozwiązanie.
Krok 13: Wykończenie
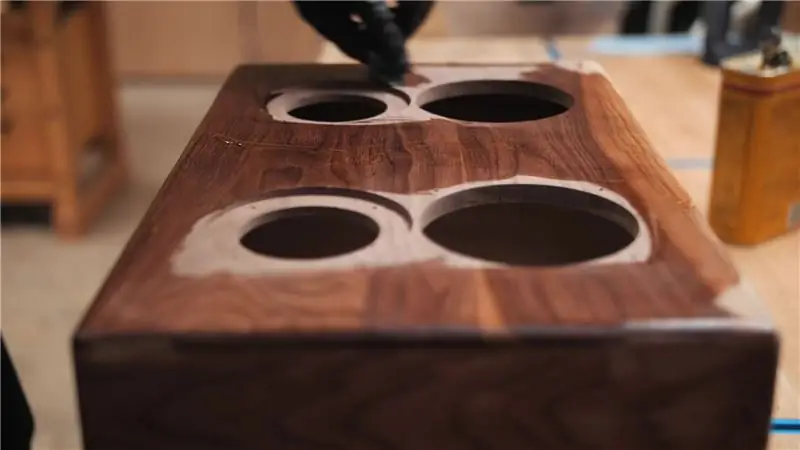
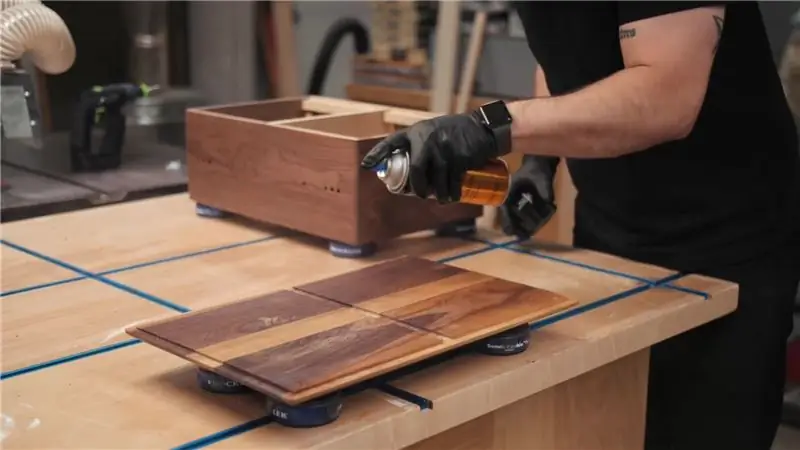
Po wywierceniu wszystkich otworów w obudowie głośnika wszystko, co pozostało do zrobienia, to przeszlifować wszystko do ziarna o ziarnistości 180 i przygotować do wykończenia.
Na koniec poszedłem z ściereczką na poliuretanie, głównie dlatego, że w puszce zostało mi akurat tyle, by zużyć ją w tym projekcie. Wytarłem trzy warstwy, pozostawiając wykończenie do wyschnięcia około 6 godzin między warstwami. Po prostu uwielbiam sposób, w jaki wykończenie wystrzeliło ziarno tego orzecha włoskiego, piękne.
Uszczelniłem również wnętrze szafki poliuretanem w sprayu, co nie byłoby konieczne, gdybym użył płyty MDF lub sklejki do wykonania pudełka, ale pomyślałem, że pomoże to zmniejszyć sezonowe rozszerzanie i kurczenie.
Po wyschnięciu mogłem przystąpić do końcowego montażu szafki. Najpierw chciałem się upewnić, że tylny panel ma hermetyczne uszczelnienie obudowy. Znalazłem tę piankową izolację w centrum domu, która okazała się idealna do tej konstrukcji. Można go obrać i przykleić, a ja po prostu upewniłem się, że poprowadzę go wzdłuż wszystkich obszarów z wpustami na tylnym panelu.
Gdy panel jest montowany za pomocą wkrętów, pianka ściska się i tworzy doskonałe uszczelnienie.
Krok 14: Ostatnie kroki
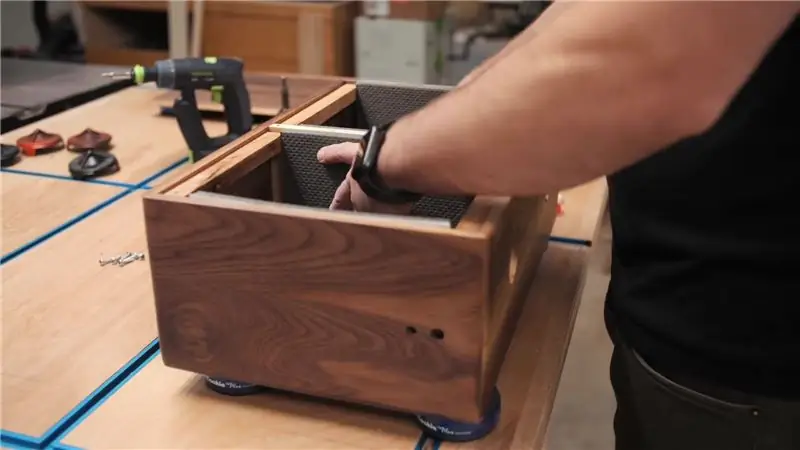
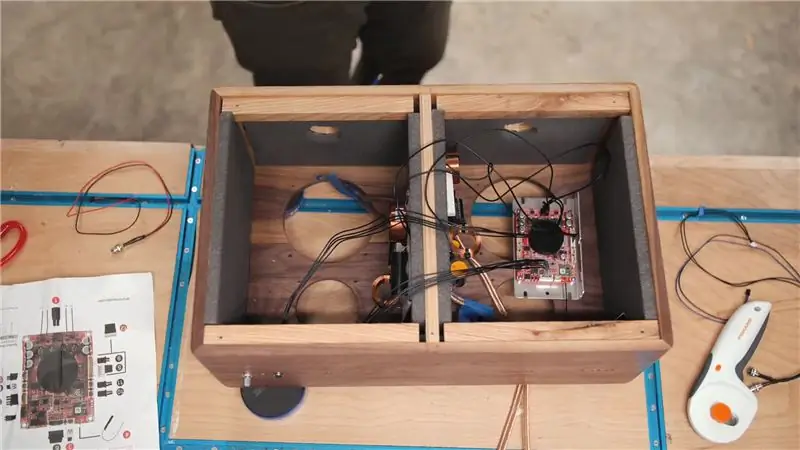
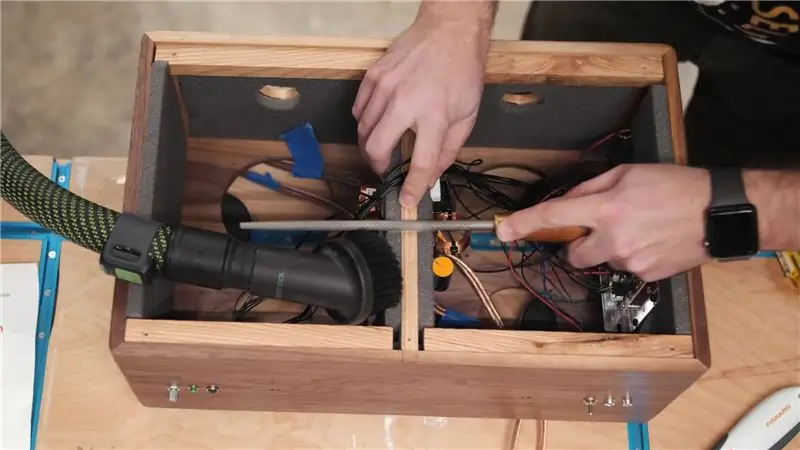
Następnie dodałem tę piankę tłumiącą dźwięk 1/2” do wszystkich wewnętrznych powierzchni obudowy, z wyjątkiem przedniej ścianki. Pianka ma podkład typu peel and stick i po prostu przycinam ją nożyczkami, upewniając się, że wycięłam wszystkie otwory, które wcześniej wywierciłam.
Mogłem też zamontować zwrotnice i płytkę wzmacniacza po wewnętrznej stronie obudowy. Użyłem do tego śrub i po prostu wkręciłem je w środkową przegrodę.
Musiałem dodać rowek do środkowej przegrody, aby kable mogły przejść z jednej strony szafki na drugą, i po prostu użyłem okrągłego tarnika, aby wyciąć rowek.
Wreszcie mogłem zainstalować wszystkie przełączniki, diody LED, gumowe nóżki, uchwyt i porty, przymocować tylny panel, a następnie włożyć głośniki.
Po zainstalowaniu głośników Boombox był gotowy i pozostało tylko go wypróbować!
Zalecana:
Zasilany bateryjnie czujnik poziomu kolektora wody: 7 kroków (ze zdjęciami)
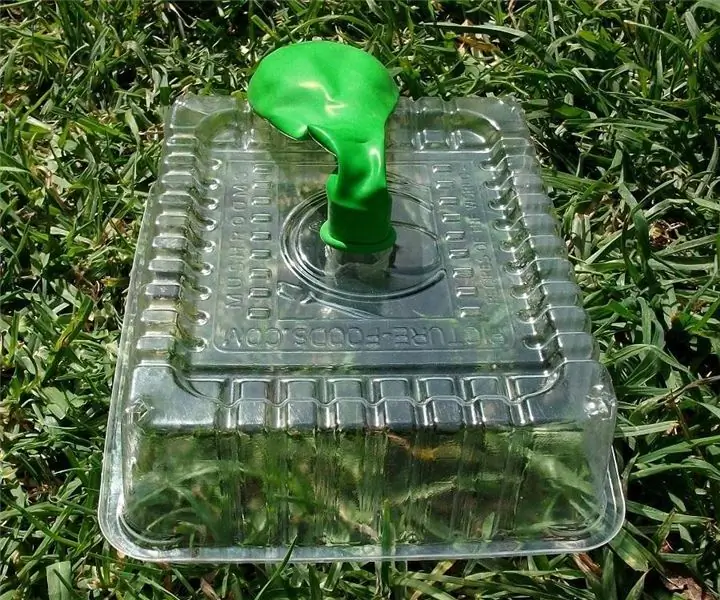
Zasilany bateryjnie czujnik poziomu kolektora wody: Nasz dom ma zbiornik na wodę zasilany z deszczu padającego na dach i używany do toalety, pralki i podlewania roślin w ogrodzie. Przez ostatnie trzy lata lata były bardzo suche, więc obserwowaliśmy poziom wody w zbiorniku. S
Zasilany bateryjnie inteligentny przycisk Wi-Fi do sterowania światłami HUE: 5 kroków (ze zdjęciami)
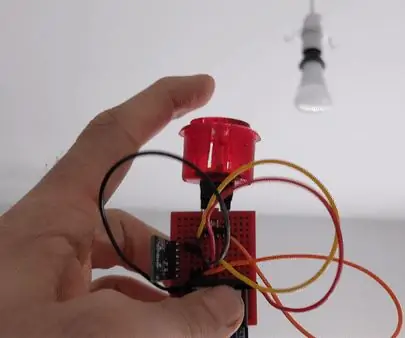
Zasilany bateryjnie inteligentny przycisk Wi-Fi do sterowania światłami HUE: Ten projekt pokazuje, jak zbudować zasilany bateryjnie przycisk Wi-Fi IoT w mniej niż 10 minut. Przycisk kontroluje światła HUE nad IFTTT.Dzisiaj możesz budować urządzenia elektroniczne i łączyć je z innymi urządzeniami inteligentnego domu dosłownie w kilka minut. Co to jest
Czujnik wilgotności kwiatów IOT WiFi (zasilany bateryjnie): 8 kroków (ze zdjęciami)
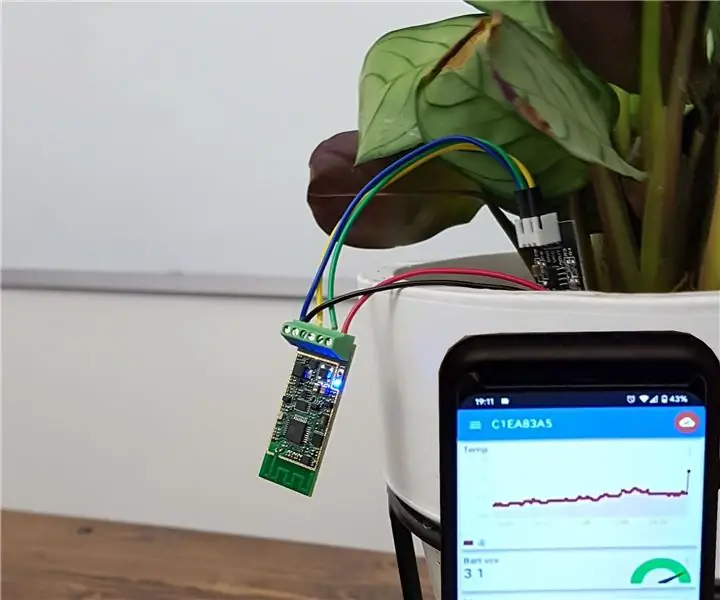
IOT WiFi Flower Moisture Sensor (zasilany bateryjnie): W tej instrukcji przedstawiamy, jak zbudować WiFi czujnik wilgoci / wody z monitorem poziomu baterii w mniej niż 30 minut. Urządzenie monitoruje poziom wilgoci i przesyła dane do smartfona przez internet (MQTT) z wybranym interwałem czasowym. U
Dowiedz się, jak zrobić przenośny monitor zasilany bateryjnie, który może również zasilać Raspberry Pi: 8 kroków (ze zdjęciami)
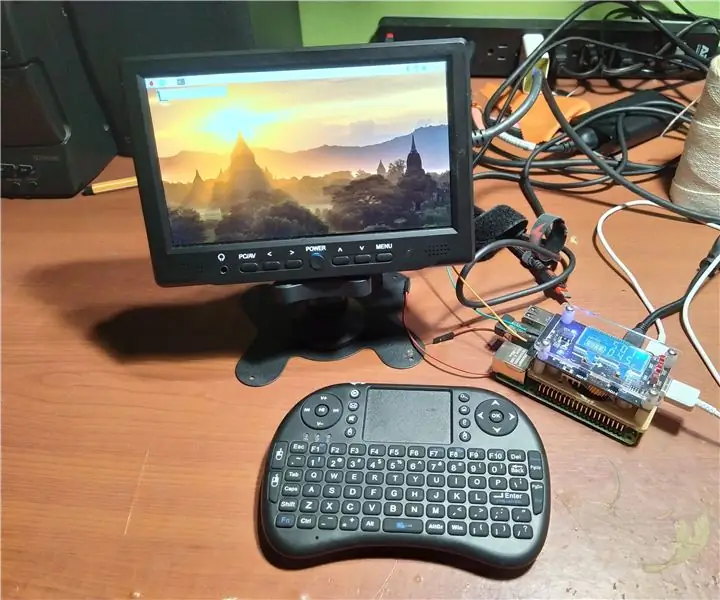
Dowiedz się, jak zrobić przenośny monitor zasilany bateryjnie, który może również zasilać Raspberry Pi: Czy kiedykolwiek chciałeś kodować pythona lub mieć wyjście wyświetlacza dla robota Raspberry Pi, w podróży lub potrzebujesz przenośnego dodatkowego wyświetlacza do laptopa czy aparat? W tym projekcie będziemy konstruować przenośny monitor zasilany bateryjnie i
Zasilany bateryjnie czujnik drzwiowy z integracją automatyki domowej, WiFi i ESP-NOW: 5 kroków (ze zdjęciami)
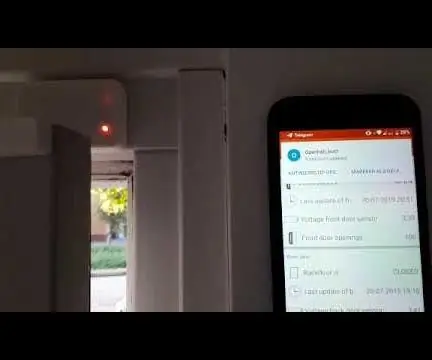
Czujnik drzwi zasilany bateryjnie z integracją automatyki domowej, Wi-Fi i ESP-NOW: W tej instrukcji pokazuję, jak zrobiłem czujnik drzwi zasilany bateryjnie z integracją automatyki domowej. Widziałem inne fajne czujniki i systemy alarmowe, ale sam chciałem taki zrobić. Moje cele: Czujnik, który wykrywa i zgłasza zdar