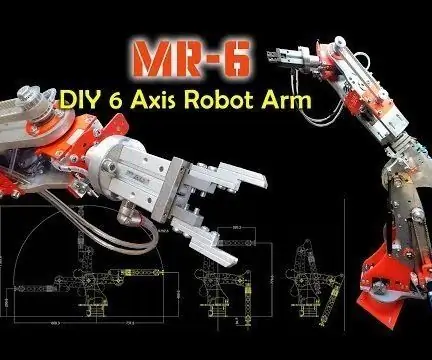
Spisu treści:
2025 Autor: John Day | [email protected]. Ostatnio zmodyfikowany: 2025-01-23 15:03
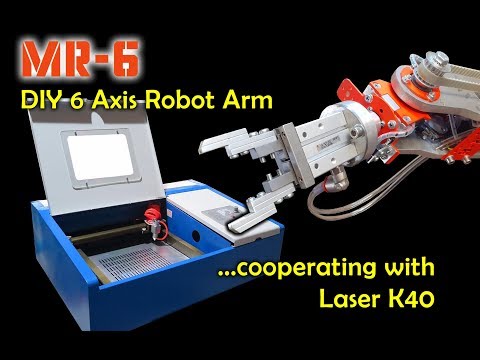
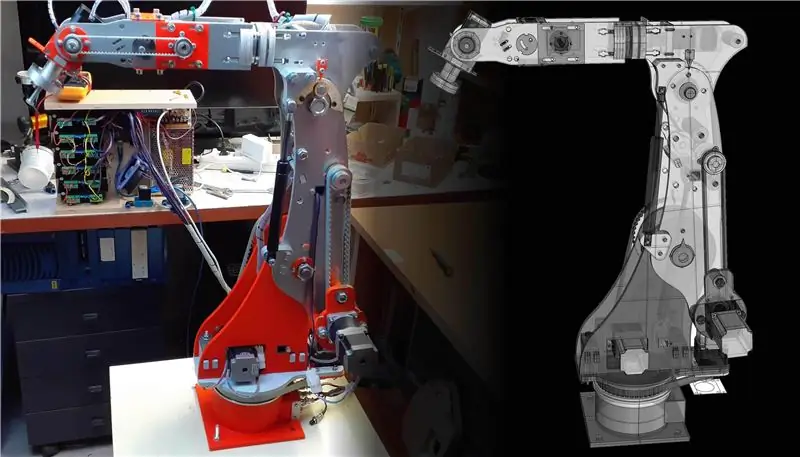
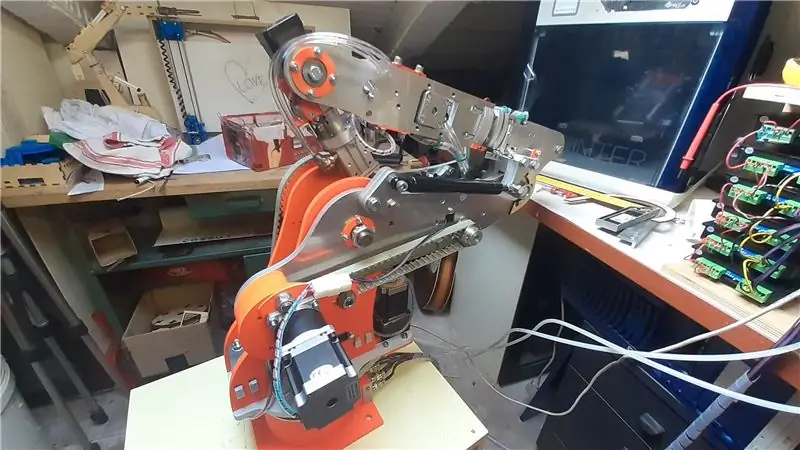
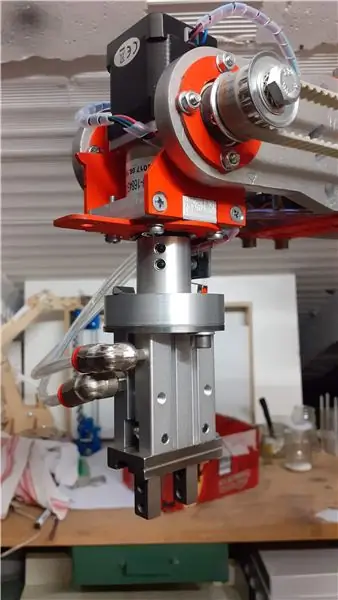
Po ponad rocznych badaniach, prototypach i różnych awariach udało mi się zbudować robota żelazno/aluminiowego o 6 stopniach swobody sterowanego silnikami krokowymi.
Najtrudniejszą częścią był projekt, ponieważ chciałem osiągnąć 3 podstawowe cele:
- Niski koszt realizacji
- Łatwy montaż nawet przy niewielkim sprzęcie
- Dobra precyzja podczas ruchu
Model 3D projektowałem z Rhino kilka razy, aż (moim zdaniem) udało się uzyskać dobry kompromis spełniający 3 wymagania.
Nie jestem inżynierem, a przed tym projektem nie miałem żadnego doświadczenia w robotyce, więc osoba bardziej doświadczona ode mnie mogła znaleźć błędy projektowe w tym, co zrobiłem, ale nadal mogę powiedzieć, że jestem zadowolony z końcowego rezultatu, który osiągnąłem.
Kieszonkowe dzieci
aby uzyskać więcej informacji odwiedź mój osobisty blog
Krok 1: Projektowanie CAD
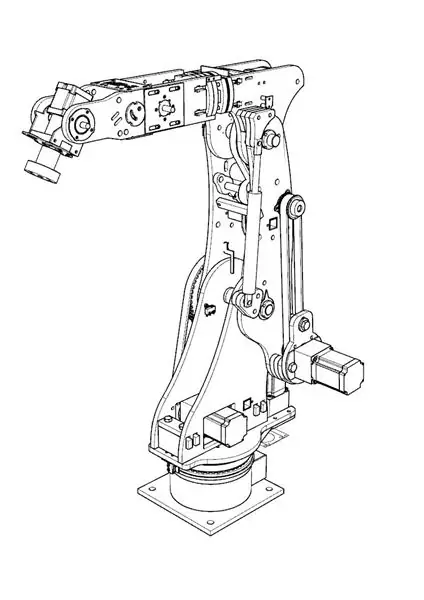
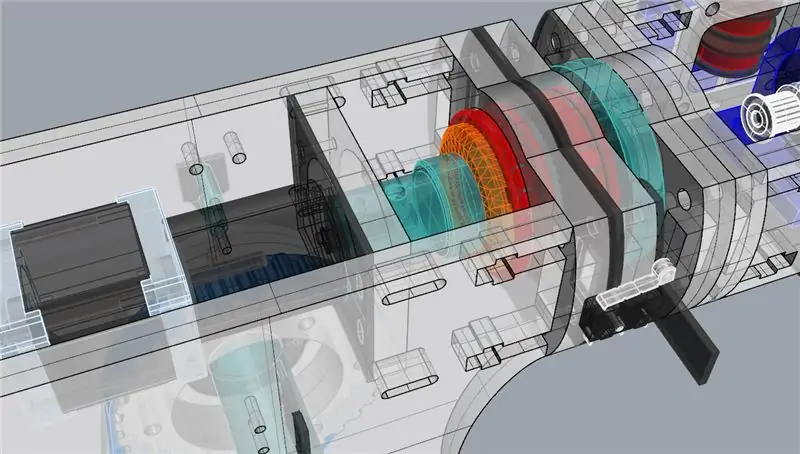
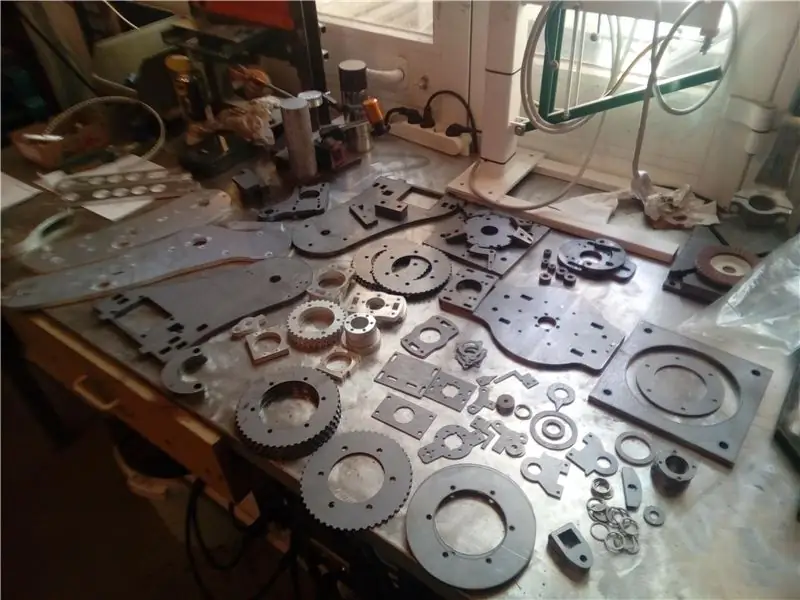
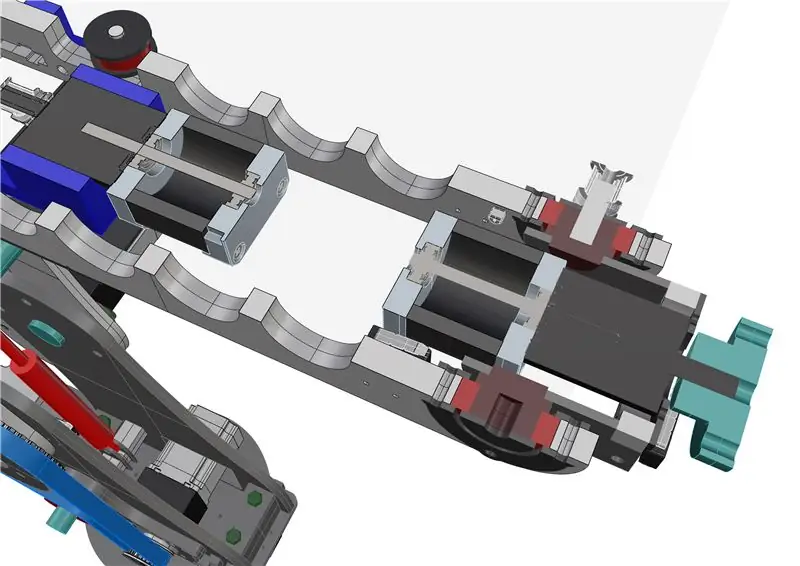
Przed dojściem do ostatecznego modelu zaprojektowałem co najmniej 8 różnych prototypów z różnymi systemami przekładni, ale żaden nie spełniał 3 wymagań opisanych powyżej.
Zestawiając rozwiązania mechaniczne wszystkich wykonanych prototypów (a także akceptując pewne kompromisy) powstał model finalny. Nie liczyłem godzin spędzonych przed CAD, ale zapewniam, że było ich naprawdę dużo.
Jednym z aspektów, o którym należy pamiętać na etapie projektowania, jest to, że nawet jeden gram dodany na końcu nadgarstka robota jest mnożony kosztem oporu momentu obrotowego silników u podstawy, a zatem zwiększa się wagę i tym więcej silników należy obliczyć, aby wytrzymać wysiłek.
Aby "pomóc" silnikom wytrzymać naprężenia zastosowałem tłoki gazowe 250N i 150N.
Pomyślałem o obniżeniu kosztów poprzez stworzenie robota z wycinanych laserowo płyt żelaznych (C40) i aluminium o grubościach od 2, 3, 5, 10 mm; cięcie laserowe jest znacznie tańsze niż frezowanie metalu 3D.
Po zaprojektowaniu każdego poszczególnego elementu wykonałem kształty elementów w formacie.dxf i wysłałem je do centrum cięcia. Wszystkie pozostałe elementy wykonałem samodzielnie na tokarce.
Krok 2: Przygotowanie i montaż
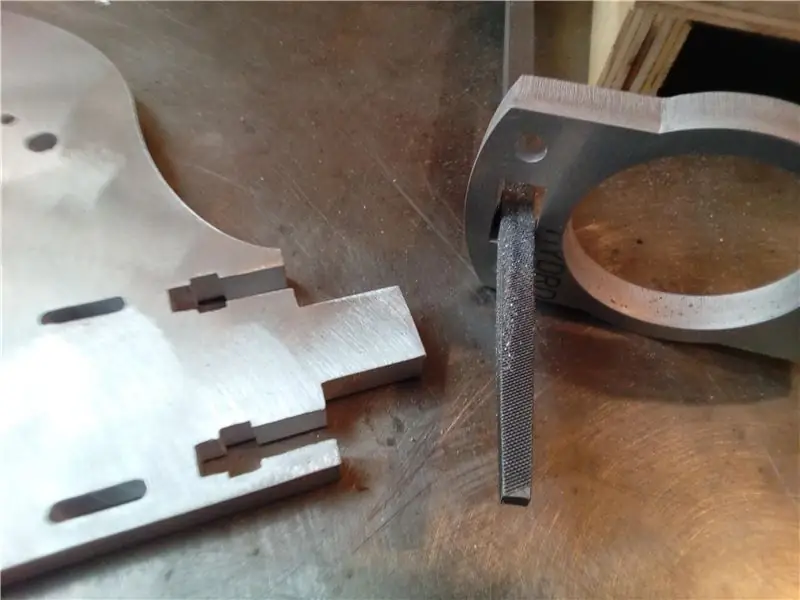
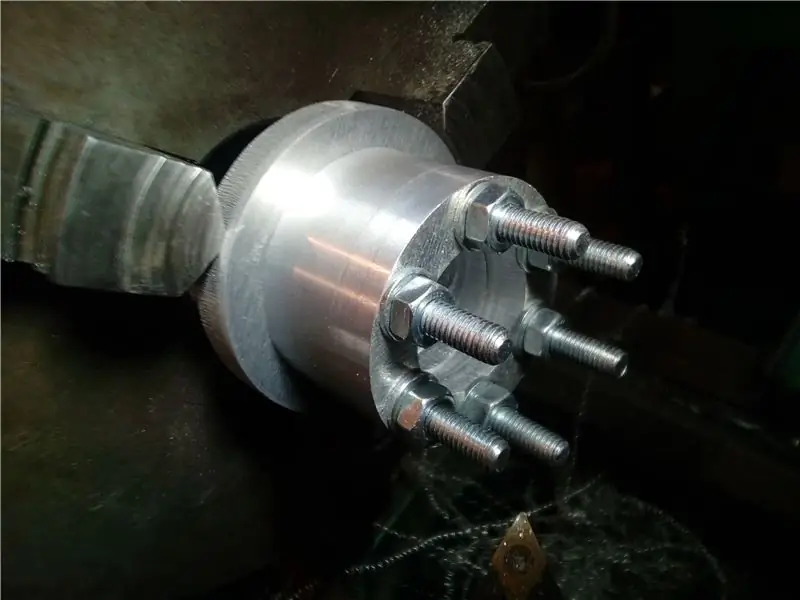
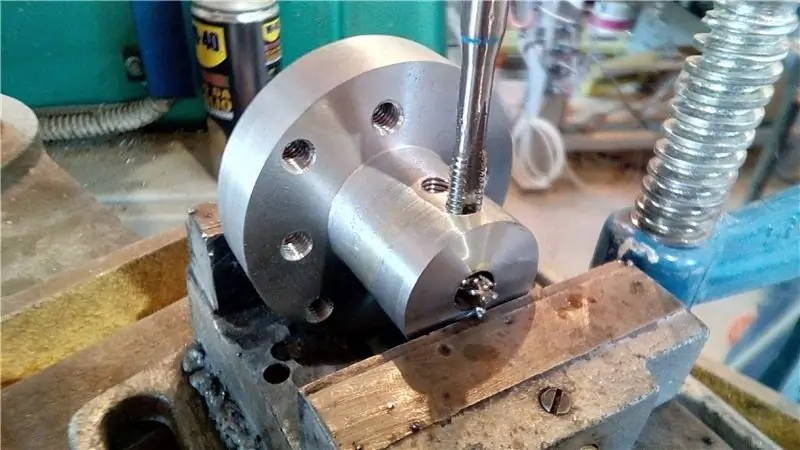
Wreszcie czas ubrudzić sobie ręce (to robię najlepiej)…
Faza budowy zabrała wiele godzin pracy na przygotowanie elementów, ręczne piłowanie otworów, połączeń, gwintów i obracanie piast. Fakt, że zaprojektowałem każdy element tak, aby móc pracować z zaledwie kilkoma narzędziami roboczymi, sprawił, że nie miałem żadnych większych niespodzianek ani problemów mechanicznych.
Najważniejsze, żeby nie spieszyć się z zakończeniem, ale być skrupulatnym i podążać za każdą linijką projektu, improwizacja na tym etapie nigdy nie prowadzi do dobrych rezultatów.
Uświadomienie sobie gniazd łożyskowych jest niezwykle ważne, ponieważ każdy przegub opiera się na nich i nawet niewielki kilkuprocentowy luz może zaszkodzić powodzeniu projektu.
Musiałem przerobić szpilki, ponieważ za pomocą tokarki usunąłem około 5 centów mniej niż otwór łożyska, a kiedy próbowałem go zamontować, gra była potwornie oczywista.
Narzędzia, których użyłem do przygotowania wszystkich kawałków to:
- wiertarka pionowa
- młynek / dremel
- kamień szlifierski
- plik ręczny
- tokarka
- angielskie klawisze
Rozumiem, że nie każdy może mieć tokarkę w domu i w takim przypadku konieczne będzie zlecanie detali do specjalistycznego centrum.
Zaprojektowałem elementy do cięcia laserowego z nieco bardziej obfitymi spoinami, aby móc je doskonalić ręcznie, ponieważ laser, jakkolwiek precyzyjny, generuje stożkowe cięcie i należy to wziąć pod uwagę.
Ręczna praca z pilnikiem każdego połączenia, które wykonałem, aby wygenerować bardzo precyzyjne połączenie między częściami.
Nawet otwory w gniazdach łożyskowych zmniejszyłem, a następnie rozwierciłem ręcznie za pomocą dremela i dużo (ale naprawdę dużo) cierpliwości.
Wszystkie gwinty wykonałem ręcznie na wiertarce, ponieważ uzyskuje się maksymalną prostopadłość między instrumentem a elementem. Po przygotowaniu każdego elementu nadeszła długo oczekiwana chwila prawdy, montaż całego robota. Zaskoczyło mnie, że każdy element dokładnie pasuje do drugiego z odpowiednimi tolerancjami.
Robot jest już zmontowany
Zanim zrobię cokolwiek innego, wolałem zrobić kilka testów ruchowych, aby upewnić się, że silniki zostały poprawnie zaprojektowane, jeśli znajdę jakieś problemy z silnikami, zwłaszcza momentem dokręcania, będę zmuszony przerobić sporą część projektu.
Po zamontowaniu 6 silników zabrałem więc ciężkiego robota do laboratorium na poddaszu, aby poddać go pierwszym testom.
Krok 3: Pierwsze testy ruchu
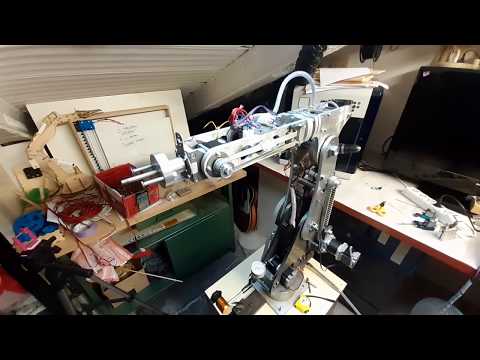
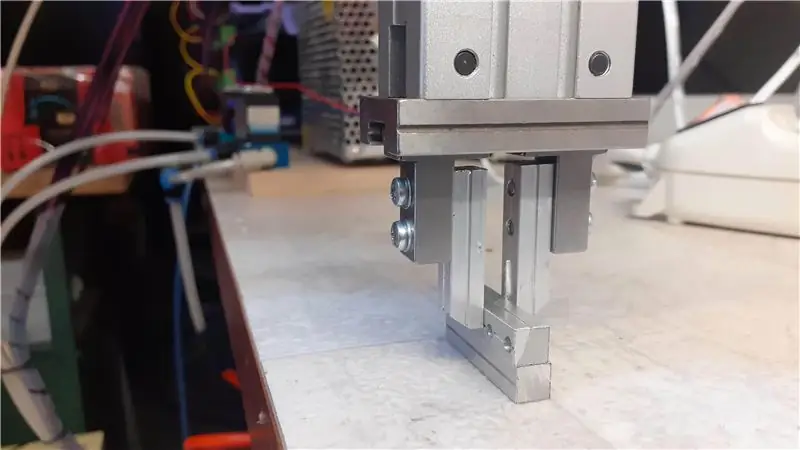
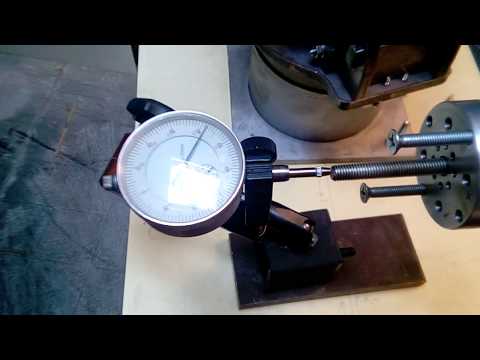
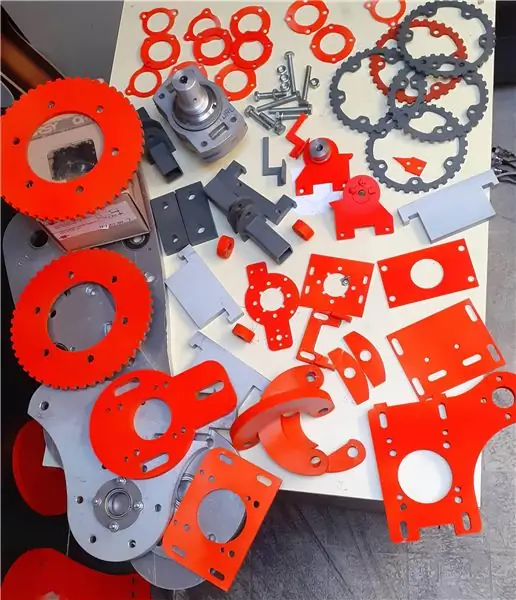
Po skompletowaniu części mechanicznej robota szybko zmontowałem elektronikę i podłączyłem tylko kable 6 silników. Wyniki testów były bardzo pozytywne, złącza poruszają się dobrze i we wcześniej ustalonych kątach odkryłem kilka łatwych do rozwiązania problemów.
Pierwszy problem dotyczy połączenia nr. 3, które przy maksymalnym rozciągnięciu nadmiernie obciążały pas i czasami powodowały utratę kroków. Rozwiązanie tego problemu doprowadziło mnie do różnych argumentów, które zobaczymy w następnym kroku.
Drugi problem dotyczy wspólnego nr. 4, rozwiązanie skręcania pasa nie było zbyt niezawodne i powodowało problemy. W międzyczasie z żelaznych części robota zaczęły powstawać małe punkty rdzy, więc mając okazję rozwiązać problemy, skorzystałem również z okazji, aby go pomalować.
Krok 4: Malowanie i składanie
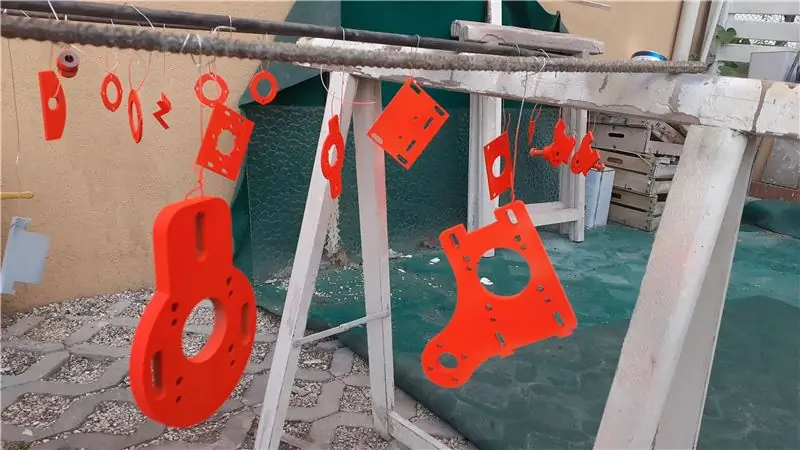
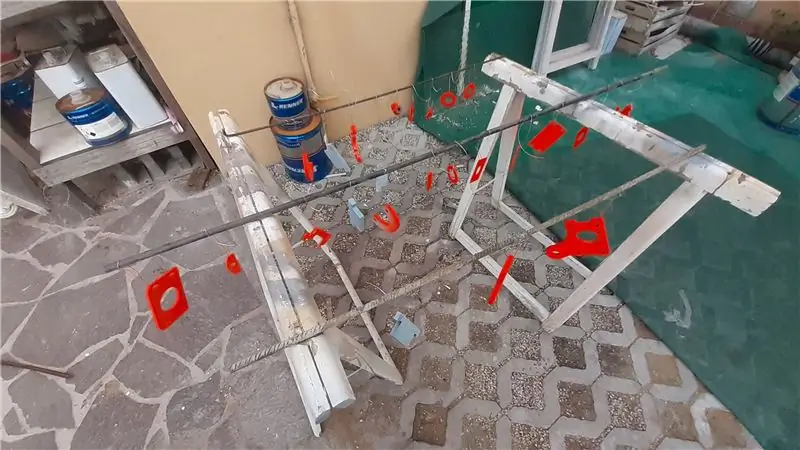
Niespecjalnie lubię fazę malowania, ale w tym przypadku jestem do tego zobowiązana, bo kocham ją jeszcze mniej.
Na żelazko najpierw nakładam podkład, który służy jako tło dla czerwonej farby fluo.
Krok 5: Poprawka N.1
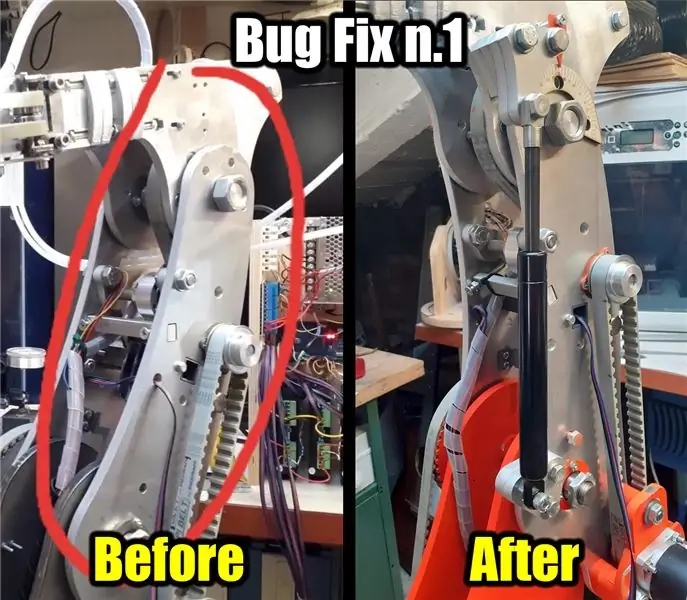
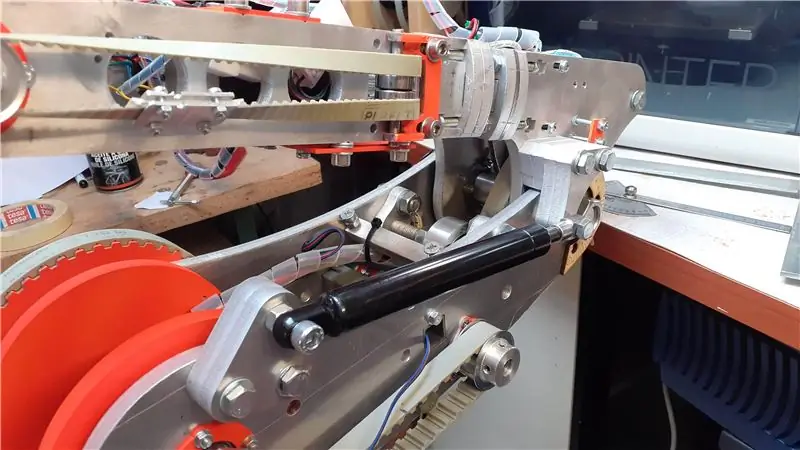
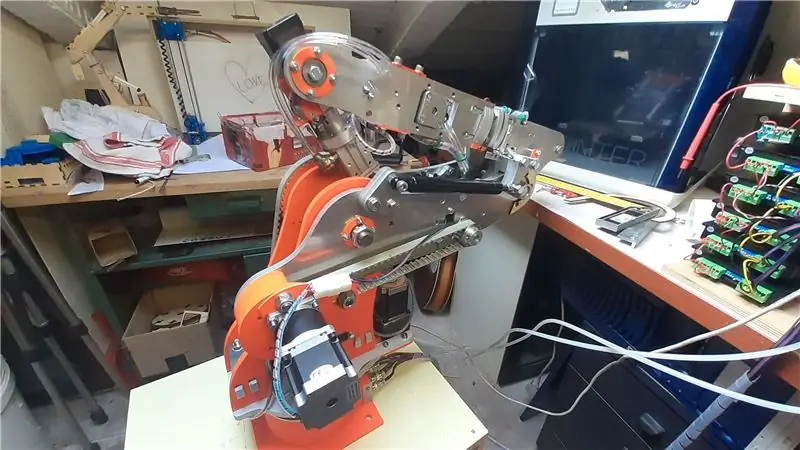
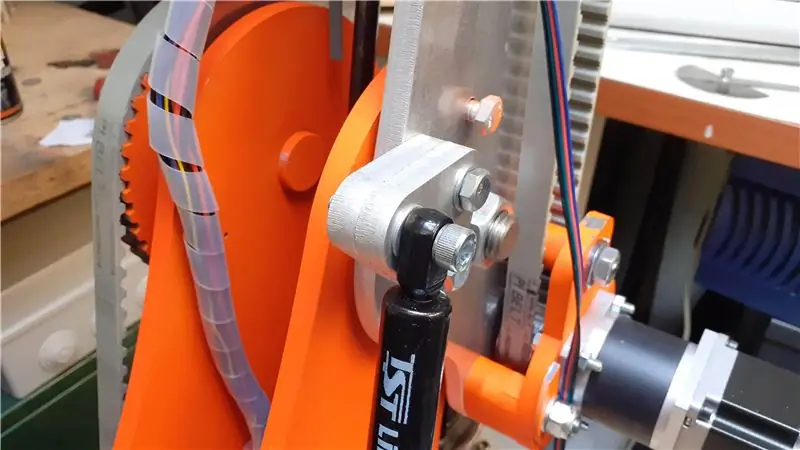
Po wynikach testów musiałem dokonać pewnych zmian w celu poprawy dokładności robota. Pierwsza modyfikacja dotyczy przegubu nr 3 w szczególności gdy był w najbardziej niekorzystnym stanie wywierał nadmierną przyczepność paska i w konsekwencji silnik był zawsze pod napięciem naprężenie. Rozwiązaniem było pomóc poprzez przyłożenie siły przeciwnej do kierunku obrotu.
Spędziłem całe noce zastanawiając się, co może być najlepszym rozwiązaniem, bez konieczności robienia wszystkiego od nowa. Początkowo myślałem o zastosowaniu dużej sprężyny skrętnej, ale patrząc w Internecie nie znalazłem nic satysfakcjonującego, więc zdecydowałem się na tłok gazowy (jak już zaprojektowałem dla przegubu nr 2), ale nadal musiałem zdecydować, gdzie go umieścić, ponieważ nie miał wystarczająco dużo miejsca.
Rezygnując nieco z estetyki uznałem, że najlepszym miejscem na umieszczenie tłoka jest bok.
Wykonałem obliczenia potrzebnej mocy tłoka biorąc pod uwagę punkt, w którym musiał wywierać siłę, a następnie zamówiłem na eBayu tłok 150 N o długości 340 mm, a następnie zaprojektowałem nowe wsporniki, aby móc go naprawić.
Krok 6: Poprawka N.2

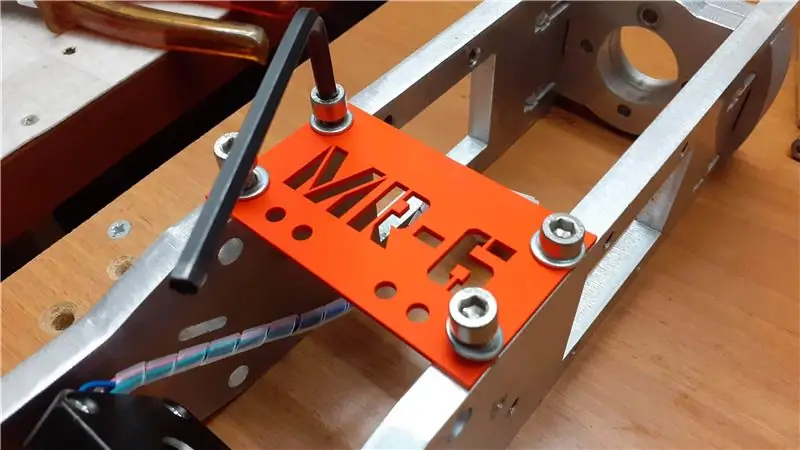
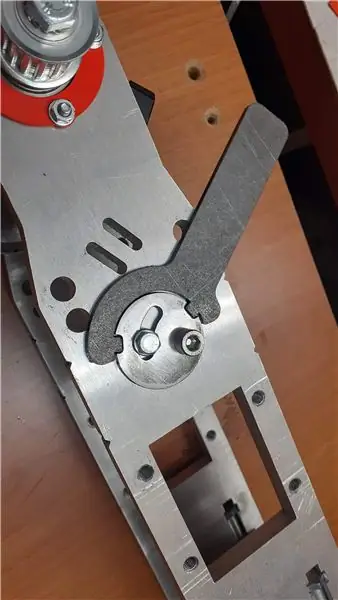
Druga zmiana dotyczy wspólnego nr. 4, gdzie początkowo planowałem transmisję ze skręconym paskiem, ale zdałem sobie sprawę, że przestrzenie się zmniejszyły, a pasek nie działał tak dobrze, jak się spodziewałem.
Postanowiłem całkowicie przerobić całe połączenie, projektując ramiona tak, aby otrzymać silnik w kierunku równoległym do nich. Dzięki tej nowej modyfikacji pasek działa teraz poprawnie, a także łatwiej go napinać, ponieważ zaprojektowałem system kluczyków, aby łatwo napinać pasek.
Krok 7: Elektronika
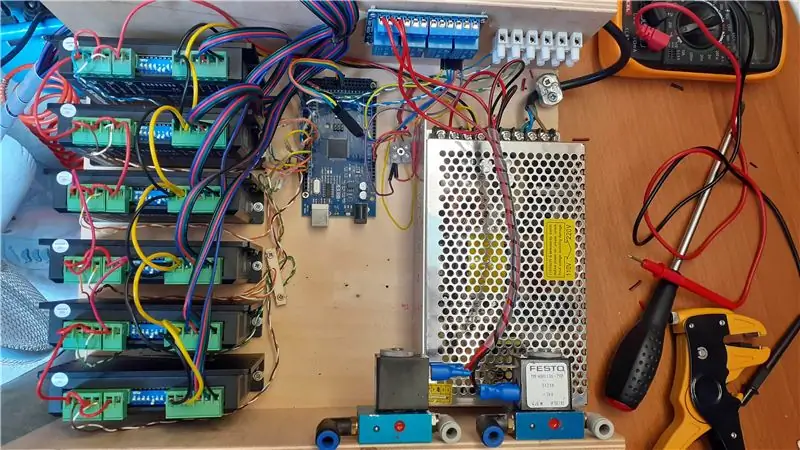
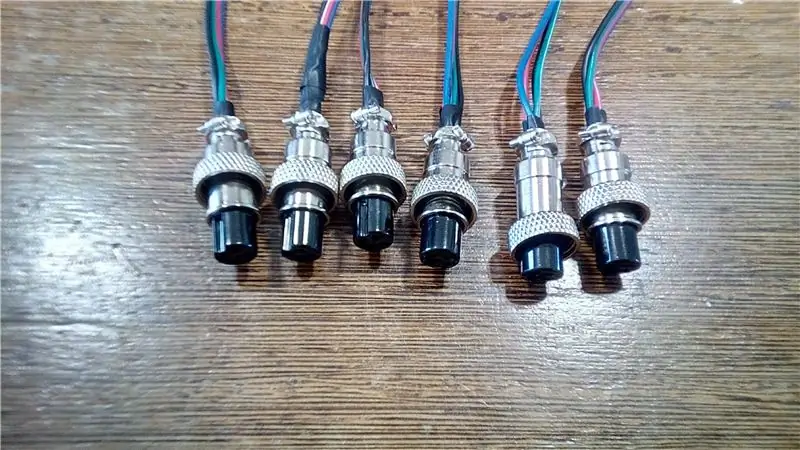
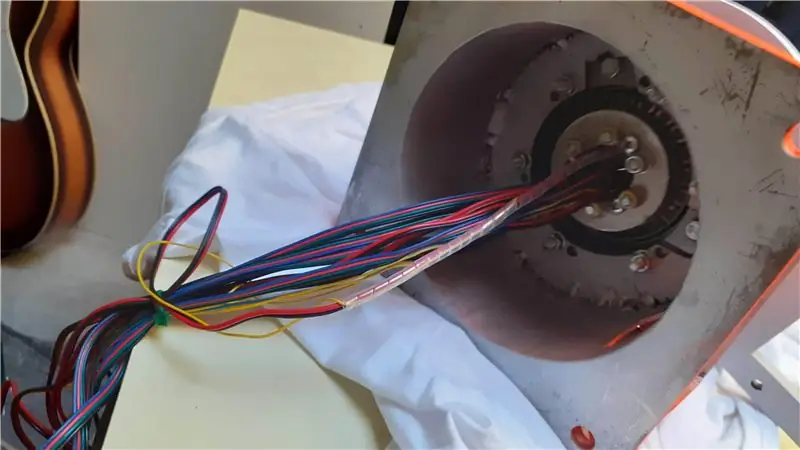
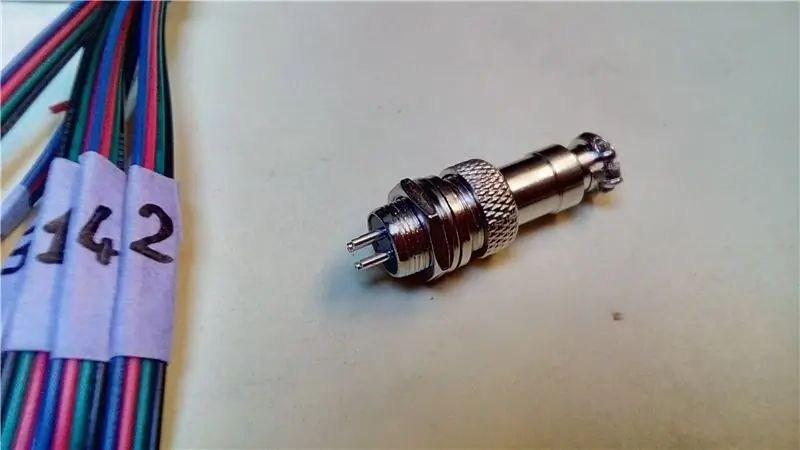
Elektronika sterowania silnikiem jest taka sama, jaka jest używana w klasycznym 3-osiowym CNC, z tą różnicą, że do zarządzania są 3 więcej sterowników i 3 więcej silników. Wszystkie logiki sterowania osiami są obliczane przez aplikację, elektronika ma jedyne zadanie otrzymywania instrukcji o tym, o ile stopni silniki będą musiały się obrócić, aby złącze nie osiągnęło pożądanej pozycji.
Części składające się na elektronikę to:
- Arduino Mega
- n. 6 sterowników DM542T
- n. 4 Rele
- n. 1 zasilacz 24 V
- n. 2 zawory elektromagnetyczne (do docisku pneumatycznego)
Na Arduino załadowałem szkic, który zajmuje się jednoczesnym zarządzaniem ruchami silników, takimi jak przyspieszanie, zwalnianie, prędkość, kroki i maksymalne limity i jest zaprogramowany do odbierania poleceń do wykonania przez port szeregowy (USB).
W porównaniu do profesjonalnych kontrolerów ruchu, które mogą kosztować nawet kilka tysięcy euro, Arduino na swój drobny sposób broni się zbyt ewidentnie zbyt skomplikowanymi operacjami, którymi nie jest w stanie zarządzać np. wielowątkowość przydatna zwłaszcza, gdy trzeba zarządzać wieloma silnikami jednocześnie.
Krok 8: Uwagi dotyczące oprogramowania
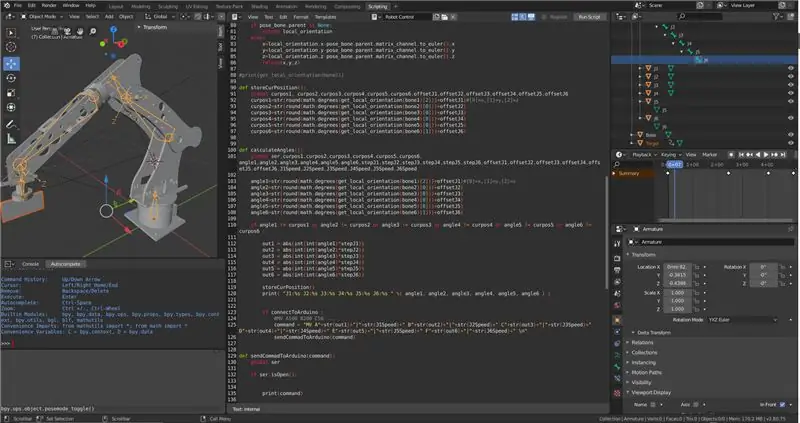
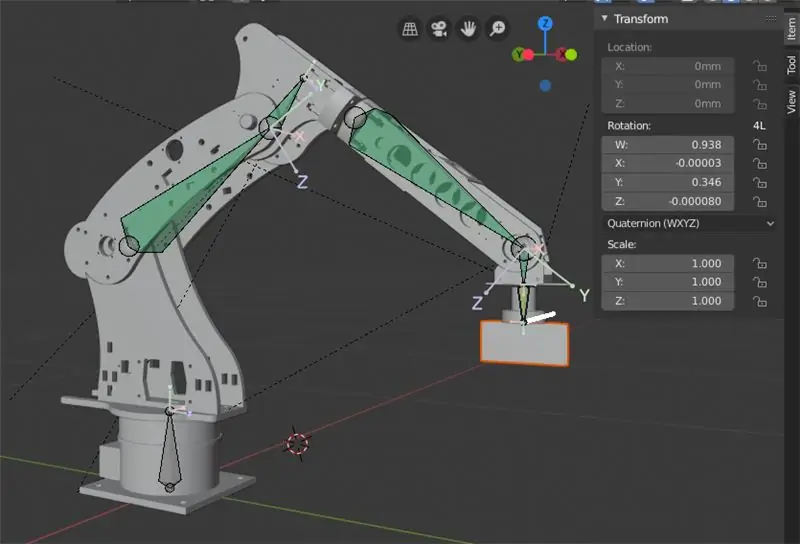
Każdy robot ma swój własny kształt i różne kąty ruchu, a kinematyka jest dla każdego z nich inna. W tej chwili do testów używam oprogramowania Chrisa Annina (www.anninrobotics.com), ale matematyka napisana dla jego robota nie pasuje idealnie do moich w rzeczywistości niektórych obszarów obszaru pracy, do których nie mogę dotrzeć je, ponieważ obliczenia narożników nie są kompletne.
Oprogramowanie Annin nadaje się teraz do eksperymentowania, ale będę musiał zacząć myśleć o napisaniu własnego oprogramowania, które w 100% pasuje do fizyki mojego robota. Zacząłem już robić testy używając Blendera i pisać Pythonową część kontrolera ruchu i wydaje się, że jest to dobre rozwiązanie, jest kilka aspektów do opracowania, ale ta kombinacja (Blender + Ptyhon) jest bardzo łatwa do zaimplementowania, szczególnie jest łatwa planować i symulować ruchy bez konieczności posiadania robota przed sobą.
Krok 9: Zacisk pneumatyczny

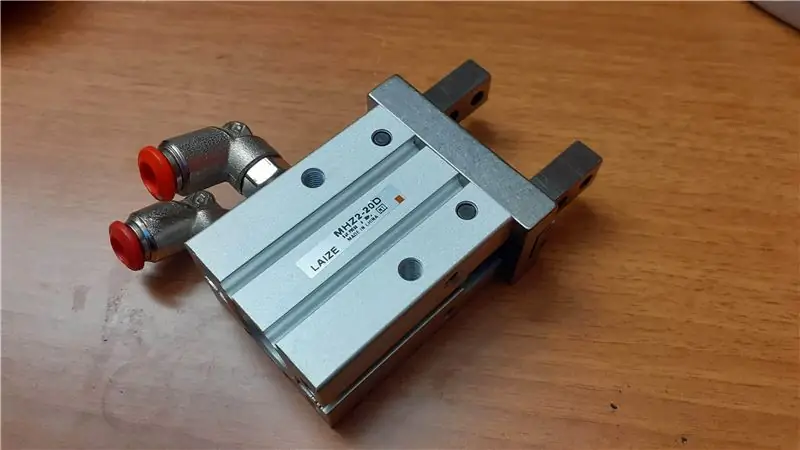
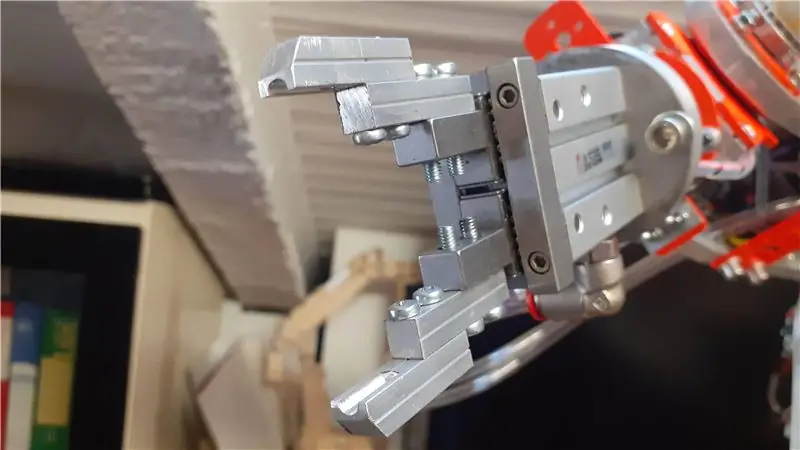
Aby móc przenosić przedmioty do robota wyposażyłem go w docisk pneumatyczny.
Osobiście nie lubię szczypiec z serwomechanizmami, nie dają mi dużej pewności co do uszczelki więc pomyślałem, że pneumatyczna szczypce specjalnie regulująca docisk może zaspokoić wszystkie potrzeby.
Za pomocą kwadratowych profili aluminiowych zmodyfikowałem zacisk tak, aby mieścił zarówno małe przedmioty, jak i duże przedmioty.
Później, gdy znajdę czas, zbierzę wszystkie informacje o projekcie, abym mógł go pobrać.
Mam nadzieję, że podobało ci się to pouczenie.
Zalecana:
Ramię robota 3D z silnikami krokowymi sterowanymi przez Bluetooth: 12 kroków
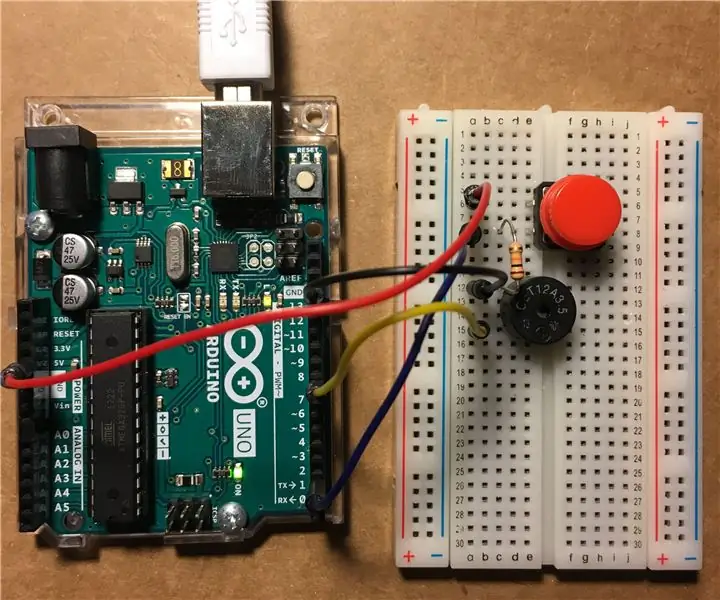
Ramię robota 3D z silnikami krokowymi sterowanymi przez Bluetooth: W tym samouczku zobaczymy, jak wykonać ramię robota 3D z silnikami krokowymi 28byj-48, serwomotorem i częściami drukowanymi w 3D. Płytka drukowana, kod źródłowy, schemat elektryczny, kod źródłowy i wiele informacji znajdują się na mojej stronie internetowej
Mecanum Omni Wheels Robot z silnikami krokowymi GRBL Arduino Shield: 4 kroki
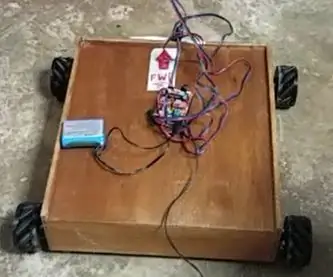
Mecanum Omni Wheels Robot z GRBL Stepper Motors Arduino Shield: Mecanum Robot - Projekt, który chciałem zbudować, odkąd zobaczyłem go na wspaniałym blogu mechatronicznym Dejana: howtomechatronics.com Dejan naprawdę wykonał dobrą robotę, obejmując wszystkie aspekty od sprzętu, drukowania 3D , elektronika, kod i aplikacja na Androida (MIT
Ramię robota ROS MoveIt, część 2: Kontroler robota: 6 kroków
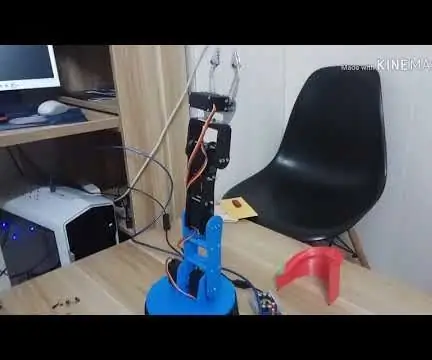
Ramię robota ROS MoveIt Część 2: Kontroler robota: https://github.com/AIWintermuteAI/ros-moveit-arm.gitW poprzedniej części artykułu stworzyliśmy pliki URDF i XACRO dla naszego ramienia robota i uruchomiliśmy RVIZ, aby kontrolować nasze ramię robota w symulowanym środowisku.Tym razem zrobimy to z p
JAK ZŁOŻYĆ IMPONUJĄCE DREWNIANE RAMIĘ ROBOTA (CZĘŚĆ 3: RAMIĘ ROBOTA) -- W OPARCIU O MIKRO: WĘDZIK: 8 kroków
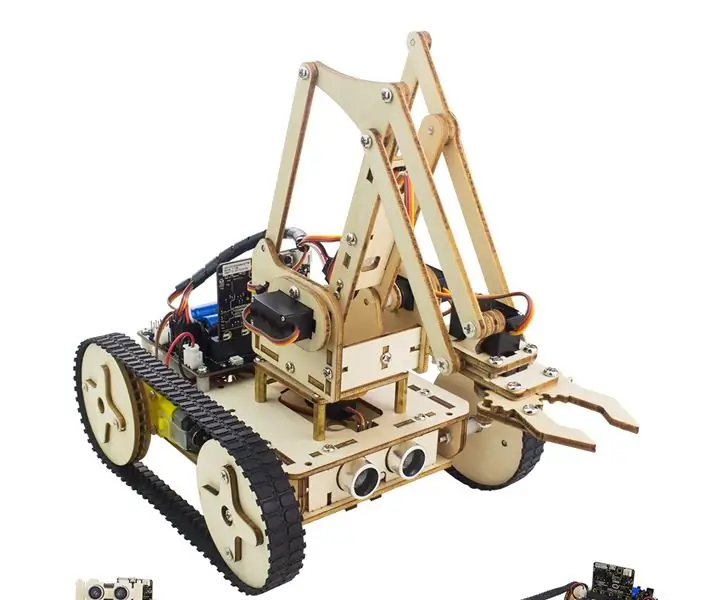
JAK ZŁOŻYĆ IMPONUJĄCE DREWNIANE RAMIĘ ROBOTA (CZĘŚĆ 3: RAMIĘ ROBOTA) -- W OPARCIU O MIKRO: BITN: Kolejny proces instalacji opiera się na zakończeniu trybu omijania przeszkód. Proces instalacji w poprzedniej sekcji jest taki sam, jak proces instalacji w trybie śledzenia linii. Następnie spójrzmy na ostateczną formę A
Robot FPV Rover sterowany przez Wi-Fi (z Arduino, ESP8266 i silnikami krokowymi): 11 kroków (ze zdjęciami)
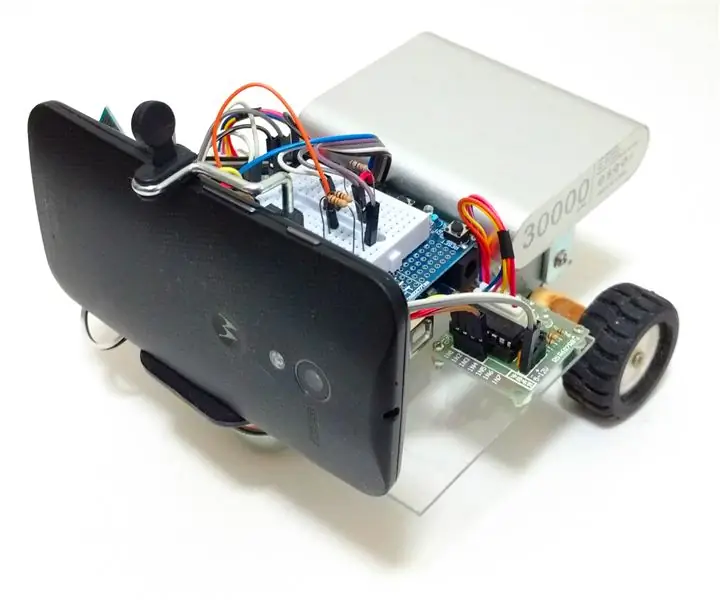
Robot łazik FPV sterowany przez Wi-Fi (z Arduino, ESP8266 i silnikami krokowymi): Ta instrukcja pokazuje, jak zaprojektować zdalnie sterowany dwukołowy robot łazik przez sieć Wi-Fi, używając Arduino Uno podłączonego do modułu Wi-Fi ESP8266 oraz dwa silniki krokowe. Robotem można sterować ze zwykłej przeglądarki internetowej