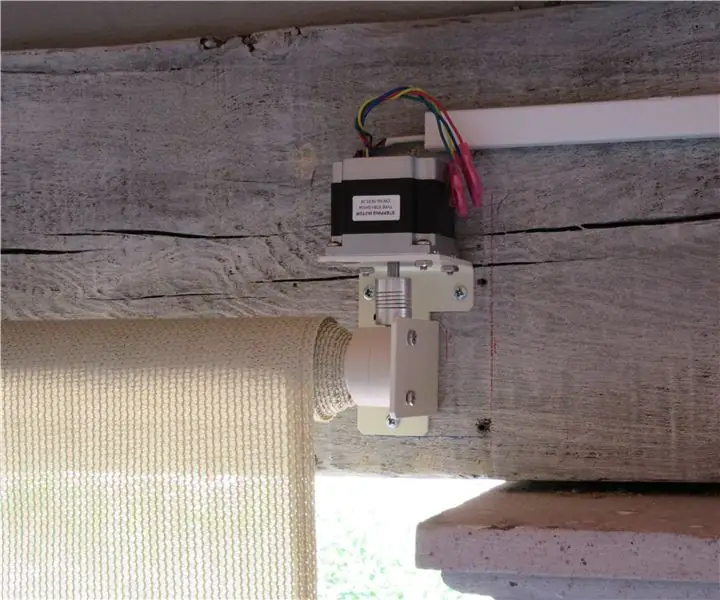
Spisu treści:
- Krok 1: Określ wymagania
- Krok 2: Zbuduj dynamometr
- Krok 3: Wybierz kandydatów na sterowniki silników krokowych
- Krok 4: Wybierz kandydujące silniki krokowe
- Krok 5: Zmierz moment obrotowy vs prędkość kandydatów
- Krok 6: Napęd o stałym napięciu 57BYGH207 Half Coil przy prądzie znamionowym
- Krok 7: Stały napęd prądowy 57BYGH207 Half Coil przy prądzie znamionowym
- Krok 8: Napęd prądu stałego pełnej cewki 57BYGH207 przy prądzie znamionowym
- Krok 9: Napęd prądu stałego 57BYGH104 pełna cewka przy ½ prądu znamionowego
- Krok 10: Napęd prądu stałego o pełnej cewce 57BYGH104 przy prądzie znamionowym 3/4
- Krok 11: Napęd prądu stałego 57BYGH104 pełna cewka przy prądzie znamionowym
- Krok 12: Dokonywanie ostatecznego wyboru
2025 Autor: John Day | [email protected]. Ostatnio zmodyfikowany: 2025-01-23 15:03
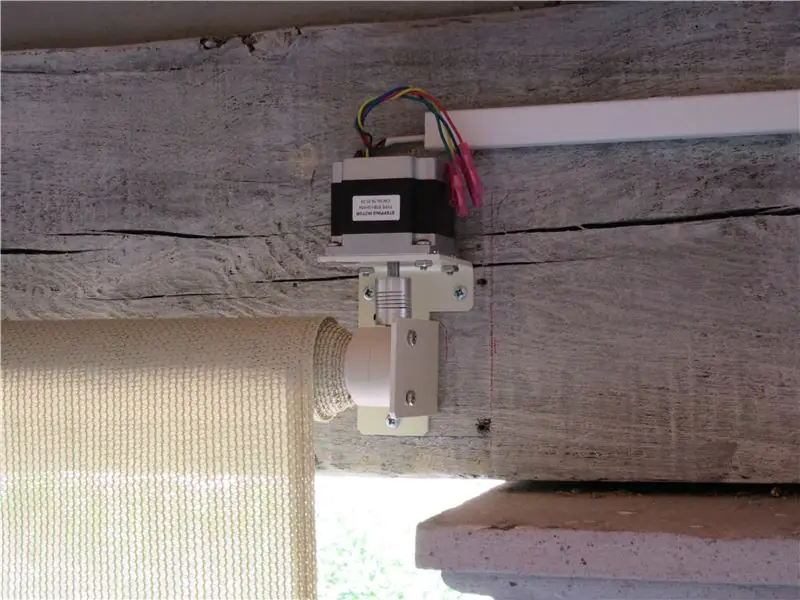
W tej instrukcji przejdę przez kroki, które podjąłem, aby wybrać silnik krokowy i sterownik do prototypowego projektu automatycznego ekranu cieniującego. Osłony przeciwsłoneczne to popularne i niedrogie modele z korbą ręczną Coolaroo. Chciałem zastąpić korby ręczne silnikami krokowymi i centralnym sterownikiem, który można zaprogramować do podnoszenia i opuszczania rolet na podstawie obliczonych czasów wschodu i zachodu słońca. Projekt ewoluował przez co najmniej pięć iteracji do produktu, który można znaleźć na Amazon.com lub AutoShade.mx, ale proces wyboru silnika krokowego i jego elektroniki sterującej powinien mieć zastosowanie w wielu innych projektach opartych na Arduino.
Początkową konfiguracją wybraną dla prototypowej elektroniki był procesor Arduino Uno (Rev 3) (Adafruit # 50) z płytkami do wyświetlania (Adafruit #399), taktowaniem zegara czasu rzeczywistego (Adafruit #1141) i sterownikami silników dwustopniowych (Adafruit #1438).). Wszystkie płyty komunikują się z procesorem za pomocą interfejsu szeregowego I2C. Dla wszystkich z nich dostępne są sterowniki programowe, co znacznie ułatwia tworzenie sterownika zacieniania ekranu.
Krok 1: Określ wymagania
Rolety powinny działać co najmniej tak szybko, jak przy ręcznym obracaniu. Stała prędkość ręczna może wynosić 1 korbę na sekundę. Większość silników krokowych ma wielkość kroku 1,8 stopnia, czyli 200 kroków na obrót. Tak więc minimalna prędkość kroku powinna wynosić około 200 kroków na sekundę. Dwa razy byłoby jeszcze lepiej.
Moment obrotowy służący do podnoszenia lub opuszczania cienia przez przekładnię ślimakową Coolaroo mierzono na 9 ekranach z cieniami na górze i na dole ich przesuwu za pomocą skalibrowanego śrubokręta dynamometrycznego (McMaster Carr #5699A11 o zakresie +/- 6 cali-funtów). To był moment „odrywający” i bardzo się różnił. Minimalna wartość wynosiła 0,25 cala na funt, a maksymalna 3,5 cala na funt. Właściwą metryczną jednostką miary momentu obrotowego jest N-m, a 3 cale-funty to 0,40 N-m, którą użyłem jako nominalny „moment tarcia”.
Z jakiegoś powodu sprzedawcy silników krokowych podają moment obrotowy silnika w jednostkach kg-cm. Powyższy minimalny moment obrotowy 0,4 N-m wynosi 4,03 Kg-cm. Aby uzyskać przyzwoity margines momentu obrotowego, chciałem silnik zdolny dostarczyć dwa razy więcej lub około 8 kg-cm. Przeglądając silniki krokowe wymienione w Circuit Specialists szybko wskazałem, że potrzebuję silnika o rozmiarze 23 ramy. Są one dostępne w krótkich, średnich i długich stosach oraz w różnych uzwojeniach.
Krok 2: Zbuduj dynamometr
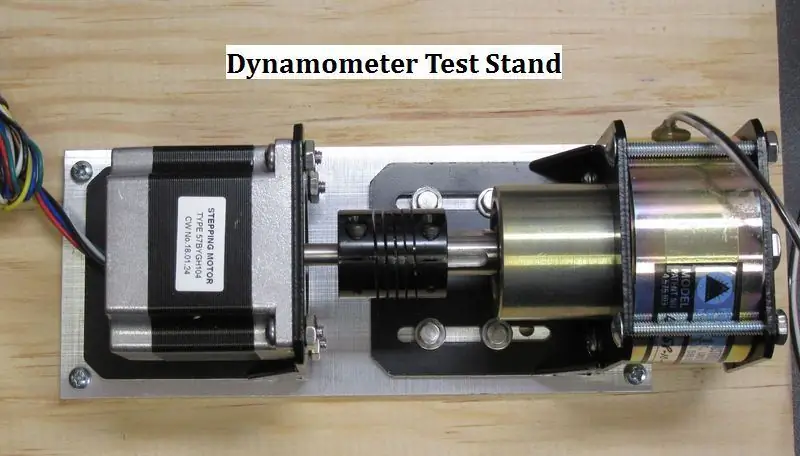
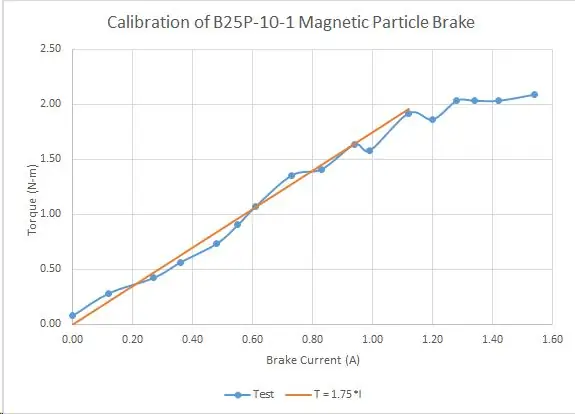
Silniki krokowe mają wyraźną charakterystykę momentu obrotowego w funkcji prędkości, która zależy od sposobu, w jaki napędzane są ich uzwojenia. Istnieją dwa powody, dla których moment obrotowy zmniejsza się wraz z prędkością. Po pierwsze, w uzwojeniach powstaje tylna siła elektromotoryczna (napięcie), która przeciwstawia się przyłożonemu napięciu. Po drugie, indukcyjność uzwojenia przeciwstawia się zmianie prądu, która występuje przy każdym kroku.
Osiągi silnika krokowego można przewidzieć za pomocą symulacji dynamicznej i zmierzyć za pomocą dynamometru. Zrobiłem jedno i drugie, ale nie będę omawiał symulacji, ponieważ dane testowe są tak naprawdę sprawdzeniem dokładności symulacji.
Dynamometr umożliwia pomiar zdolności momentu obrotowego silnika podczas pracy z kontrolowaną prędkością. Skalibrowany hamulec magnetyczno-proszkowy przykłada moment obciążenia do silnika. Nie ma potrzeby mierzenia prędkości, ponieważ będzie ona równa szybkości kroku silnika, dopóki moment obciążenia nie przekroczy możliwości silnika. Gdy tak się stanie, silnik traci synchronizację i wydaje głośny dźwięk. Procedura testowa polega na zadaniu stałej prędkości, powolnym zwiększaniu prądu płynącego przez hamulec i zanotowaniu jego wartości tuż przed utratą synchronizacji przez silnik. Jest to powtarzane przy różnych prędkościach i wykreślane jako moment obrotowy w funkcji prędkości.
Wybrany hamulec cząstek magnetycznych to model Placid Industries B25P-10-1 zakupiony w serwisie eBay. Model ten nie jest już wymieniony na stronie internetowej producenta, ale z numeru części wynika, że zapewnia szczytowy moment obrotowy 25 in-lb = 2,825 N-m, a cewka jest zaprojektowana na 10 VDC (maks.). Jest to idealne rozwiązanie do testowania rozważanych silników o rozmiarze 23, które są przystosowane do wytwarzania szczytowych momentów obrotowych około 1,6 Nm. Ponadto hamulec ten był wyposażony w otwór pilotażowy i otwory montażowe identyczne z tymi stosowanymi w silnikach NMEA 23, dzięki czemu można go było zamontować za pomocą wspornika montażowego o tym samym rozmiarze co silnik. Silniki mają wały ¼ cala, a hamulec był dostarczany z wałem ½ cala, więc w serwisie eBay zakupiono również elastyczny adapter sprzęgła z wałami o tym samym rozmiarze. Wszystko, co było potrzebne, to montaż na dwóch wspornikach do aluminiowej podstawy. Zdjęcie powyżej przedstawia stanowisko badawcze. Wsporniki montażowe są łatwo dostępne w Amazon i Ebay.
Moment hamowania hamulca magnetyczno-proszkowego jest proporcjonalny do prądu uzwojenia. Aby skalibrować hamulec, jeden z dwóch śrubokrętów do pomiaru momentu obrotowego został podłączony do wału po przeciwnej stronie hamulca jako silnik krokowy. Dwa użyte wkrętaki to McMaster Carr o numerach katalogowych 5699A11 i 5699A14. Pierwszy z nich ma maksymalny zakres momentu obrotowego 6 in-lb = 0,678 Nm, a drugi ma maksymalny zakres momentu obrotowego 25 in-lb = 2,825 N-m. Prąd dostarczany był ze zmiennego zasilacza prądu stałego CSI5003XE (50 V/3A). Powyższy wykres pokazuje zmierzony moment obrotowy w funkcji prądu.
Należy zauważyć, że w zakresie zainteresowania tych testów moment hamowania można ściśle przybliżyć za pomocą zależności liniowej Moment obrotowy (N-m) = 1,75 x Prąd hamowania (A).
Krok 3: Wybierz kandydatów na sterowniki silników krokowych
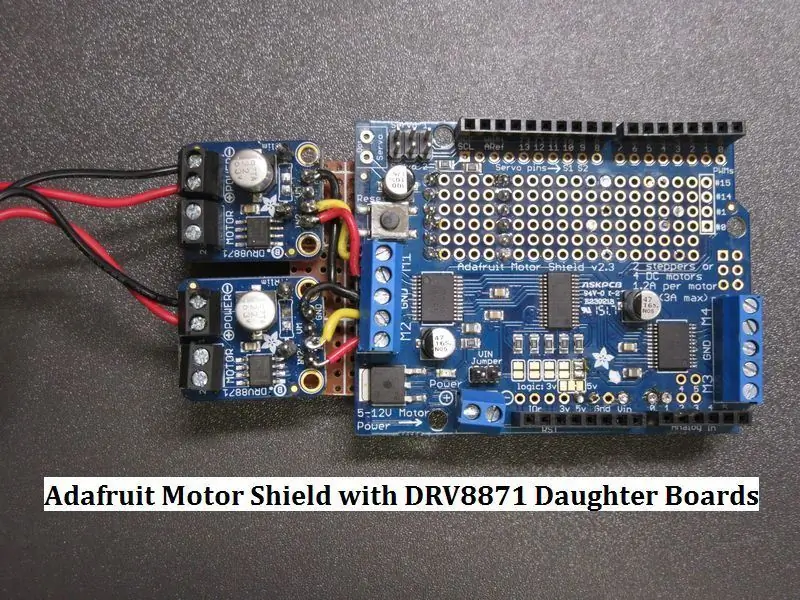
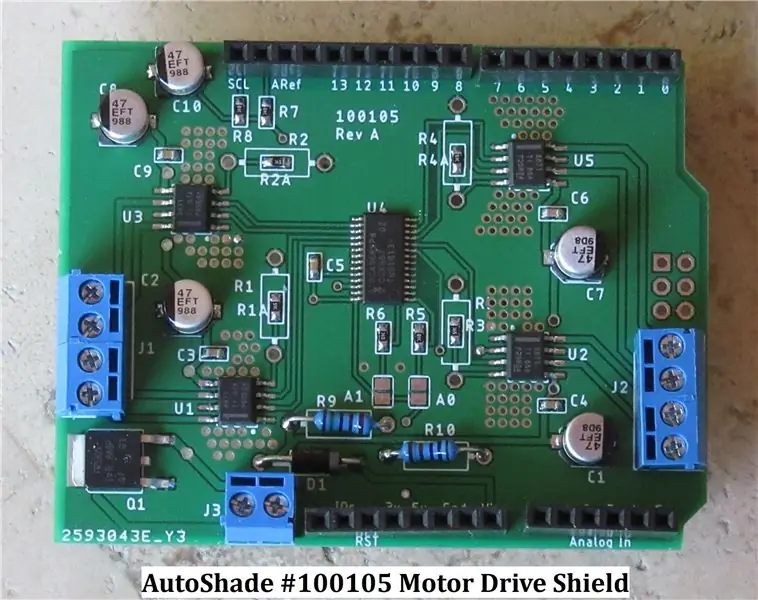
Silniki krokowe mogą być napędzane z jednym uzwojeniem w pełni aktywnym w czasie potocznie zwanym SINGLE stepping, z obydwoma uzwojeniami w pełni aktywnymi (DOUBLE stepping) lub z obydwoma uzwojeniami częściowo aktywnymi (MICROSTEPPING). W tej aplikacji interesuje nas maksymalny moment obrotowy, dlatego używany jest tylko PODWÓJNY krok.
Moment obrotowy jest proporcjonalny do prądu uzwojenia. Silnik krokowy może być napędzany stałym napięciem, jeśli rezystancja uzwojenia jest wystarczająco wysoka, aby ograniczyć prąd w stanie ustalonym do wartości znamionowej silnika. Adafruit #1438 Motorshield wykorzystuje sterowniki stałonapięciowe (TB6612FNG) o napięciu znamionowym 15 VDC, maksymalnie 1,2 ampera. Ten sterownik to większa płyta pokazana na pierwszym zdjęciu powyżej (bez dwóch płyt-córek po lewej).
Wydajność ze sterownikiem stałonapięciowym jest ograniczona, ponieważ prąd przy prędkości jest znacznie zmniejszony ze względu zarówno na indukcyjność uzwojenia, jak i tylną siłę elektromotoryczną. Alternatywnym podejściem jest dobór silnika o mniejszej rezystancji i uzwojeniu indukcyjnym oraz napędzanie go stałym prądem. Stały prąd jest wytwarzany przez modulację szerokości impulsu przyłożonego napięcia.
Świetnym urządzeniem służącym do zapewnienia napędu stałoprądowego jest DRV8871 firmy Texas Instruments. Ten mały układ scalony zawiera mostek H z wewnętrznym czujnikiem prądu. Zewnętrzny rezystor służy do ustawienia pożądanego prądu stałego (lub maksymalnego). Układ scalony automatycznie odłącza napięcie, gdy prąd przekroczy zaprogramowaną wartość i ponownie je przykłada, gdy spadnie poniżej pewnego progu.
DRV8871 ma napięcie znamionowe 45 VDC, maksymalnie 3,6 ampera. Zawiera wewnętrzny obwód wykrywający nadmierną temperaturę, który odłącza napięcie, gdy temperatura złącza osiągnie 175 stopni C. Układ scalony jest dostępny tylko w 8-pinowej obudowie HSOP, która ma podkładkę termiczną na spodzie. TI sprzedaje płytkę rozwojową, która zawiera jeden układ scalony (dwa są wymagane dla jednego silnika krokowego), ale jest bardzo droga. Adafruit i inni sprzedają małą płytkę prototypową (Adafruit #3190). Do testu dwa z nich zostały zamontowane na zewnątrz Adafruit Motorshield, jak pokazano na pierwszym zdjęciu powyżej.
Obecne możliwości napędu zarówno TB6612, jak i DRV8871 są w praktyce ograniczone przez wzrost temperatury wewnątrz części. Będzie to zależeć od ciepła części oraz temperatury otoczenia. W moich testach w temperaturze pokojowej, płyty-córki DRV8871 (Adafruit #3190) osiągnęły limity przegrzania w około 30 sekund przy 2 amperach, a silniki krokowe stają się bardzo niestabilne (pojedyncza faza z przerwami, gdy obwód przegrzania włącza się i wyłącza). Używanie DRV8871 jako płyt-córek i tak jest kłopotliwe, dlatego zaprojektowano nowy ekran (AutoShade #101005), który zawiera cztery sterowniki do obsługi silników dwustopniowych. Ta płytka została zaprojektowana z dużą ilością płaszczyzny uziemienia po obu stronach, aby odprowadzać ciepło do układów scalonych. Wykorzystuje ten sam interfejs szeregowy do Arduino, co Adafruit Motorshield, więc to samo oprogramowanie biblioteczne może być używane do sterowników. Drugie zdjęcie powyżej pokazuje tę płytkę drukowaną. Aby uzyskać więcej informacji na temat AutoShade #100105, zobacz listę na Amazon lub na stronie AutoShade.mx.
W mojej aplikacji do cieniowania podnoszenie lub opuszczanie każdego cienia zajmuje od 15 do 30 sekund, w zależności od ustawienia prędkości i odległości cienia. Dlatego prąd powinien być ograniczony w taki sposób, aby granica przegrzania nigdy nie została osiągnięta podczas pracy. Czas do osiągnięcia limitów przegrzania w 100105 jest dłuższy niż 6 minut przy limicie prądu 1,6 ampera i dłuższy niż 1 minuta przy limicie prądu 2,0 ampera.
Krok 4: Wybierz kandydujące silniki krokowe
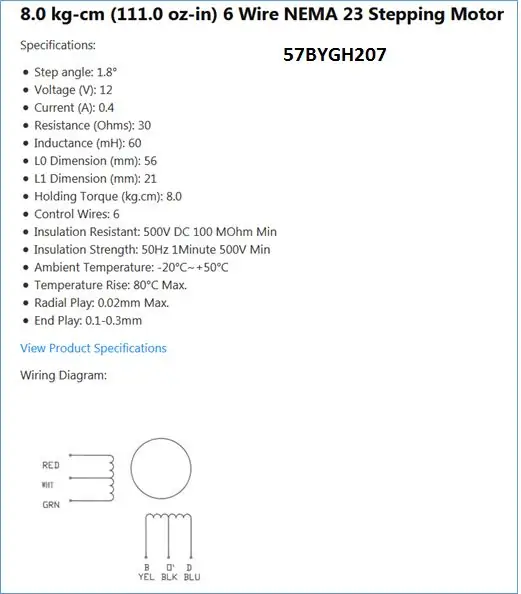
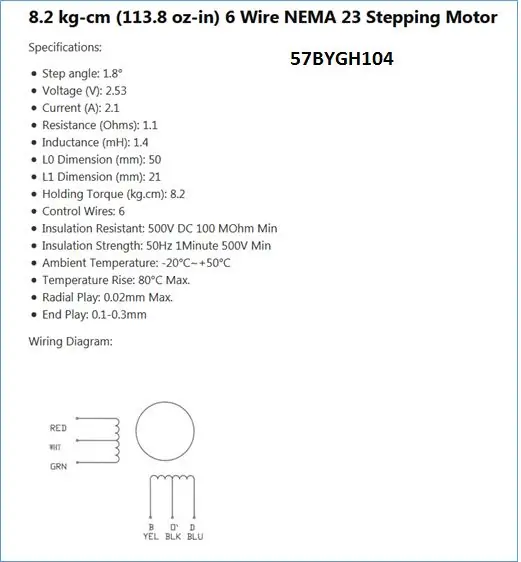
Circuit Specialists ma dwa silniki krokowe w rozmiarze 23, które zapewniają wymagany moment obrotowy 8 kg-cm. Oba mają uzwojenia dwufazowe z odczepami środkowymi, dzięki czemu można je połączyć w taki sposób, aby napędzane były pełne uzwojenia lub półuzwojenia. Specyfikacje tych silników są wymienione w dwóch powyższych tabelach. Oba silniki są prawie identyczne mechanicznie, ale elektrycznie silnik 104 ma znacznie niższą rezystancję i indukcyjność niż silnik 207. Nawiasem mówiąc, specyfikacje elektryczne dotyczą wzbudzenia w połowie cewki. Gdy używane jest całe uzwojenie, rezystancja podwaja się, a indukcyjność wzrasta czterokrotnie.
Krok 5: Zmierz moment obrotowy vs prędkość kandydatów
Za pomocą dynamometru (i symulacji) wyznaczono krzywe momentu obrotowego w funkcji prędkości dla wielu konfiguracji silnika/uzwojenia/prądu. Program (szkic) służący do uruchomienia dynamometru do tych testów można pobrać ze strony internetowej AutoShade.mx.
Krok 6: Napęd o stałym napięciu 57BYGH207 Half Coil przy prądzie znamionowym
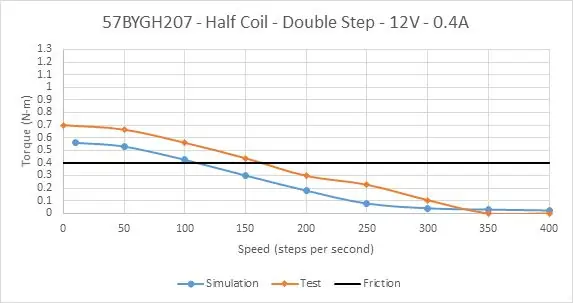
Silnik 57BYGH207 z półcewką zasilany napięciem 12V (tryb stałego napięcia) daje prąd 0,4 A i był oryginalną konfiguracją napędu. Ten silnik może być napędzany bezpośrednio z Adafruit #1434 Motorshield. Powyższy rysunek przedstawia symulowaną i zmierzoną charakterystykę prędkości momentu obrotowego wraz z najgorszym przypadkiem tarcia. Ta konstrukcja spada znacznie poniżej pożądanego momentu obrotowego wymaganego do działania przy 200 do 400 krokach na sekundę.
Krok 7: Stały napęd prądowy 57BYGH207 Half Coil przy prądzie znamionowym
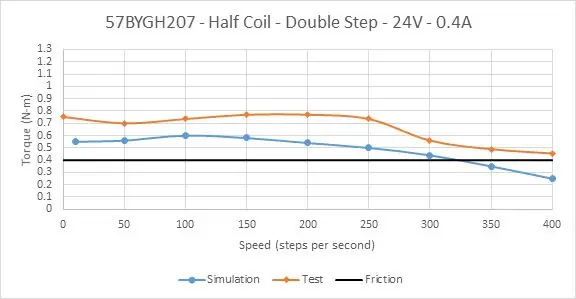
Podwojenie przyłożonego napięcia, ale użycie choppera w celu ograniczenia prądu do 0,4 A znacznie poprawia wydajność, jak pokazano powyżej. Dalsze zwiększenie przyłożonego napięcia poprawiłoby jeszcze bardziej wydajność. Jednak praca powyżej 12 VDC jest niepożądana z kilku powodów.
· DRV8871 ma napięcie ograniczone do 45 VDC
· Zasilacze ścienne o wyższym napięciu nie są tak powszechne i są droższe
· Regulatory napięcia używane do zasilania 5 VDC obwodów logicznych stosowanych w konstrukcji Arduino są ograniczone do maks. 15 VDC. Zatem eksploatacja silników przy napięciach wyższych niż to wymagałaby dwóch zasilaczy.
Krok 8: Napęd prądu stałego pełnej cewki 57BYGH207 przy prądzie znamionowym
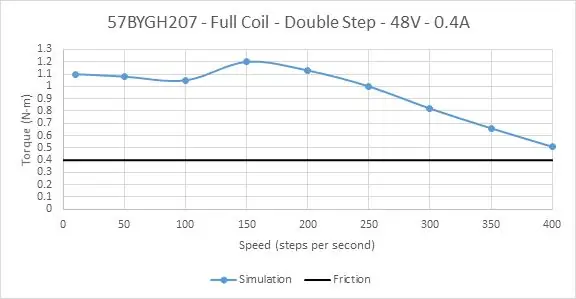
Przyjrzano się temu podczas symulacji, ale nie przetestowano, ponieważ nie miałem zasilacza 48 V. Moment obrotowy przy niskich prędkościach podwaja się, gdy pełna cewka jest napędzana prądem znamionowym, ale następnie spada szybciej wraz z prędkością.
Krok 9: Napęd prądu stałego 57BYGH104 pełna cewka przy ½ prądu znamionowego
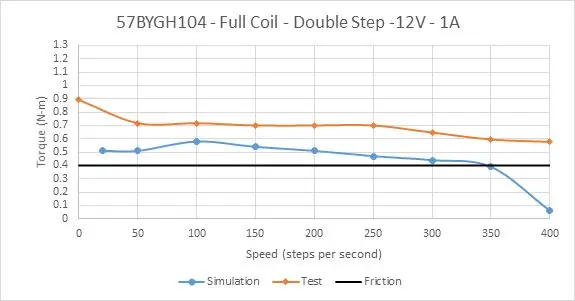
Przy 12 VDC i prądzie 1,0 A uzyskuje się pokazaną powyżej charakterystykę momentu obrotowego. Wyniki testu spełniają wymagania dotyczące działania przy 400 krokach na sekundę.
Krok 10: Napęd prądu stałego o pełnej cewce 57BYGH104 przy prądzie znamionowym 3/4
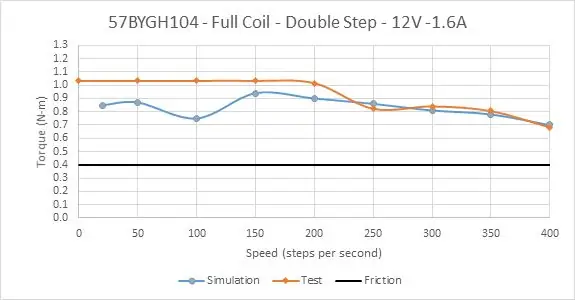
Zwiększenie prądów uzwojeń do 1,6 A znacząco zwiększa margines momentu obrotowego.
Krok 11: Napęd prądu stałego 57BYGH104 pełna cewka przy prądzie znamionowym
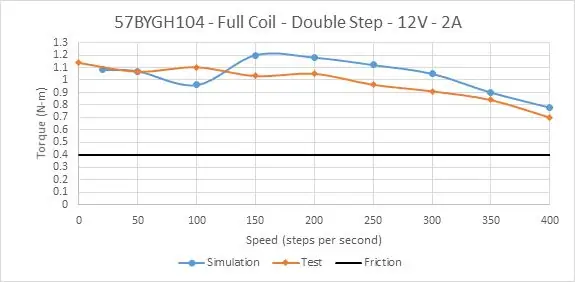
Jeśli prądy uzwojenia zostaną zwiększone do 2A, a moment obrotowy wzrośnie, jak pokazano powyżej, ale nie tak bardzo, jak przewidywała symulacja. Tak więc w rzeczywistości dzieje się coś, co ogranicza moment obrotowy przy tych wyższych prądach.
Krok 12: Dokonywanie ostatecznego wyboru

Wykorzystanie pełnej cewki zamiast połowy jest zdecydowanie lepsze, ale nie jest pożądane w przypadku silnika 207 ze względu na wymagane wyższe napięcie. Silnik 104 umożliwia pracę przy niższym przyłożonym napięciu. Dlatego wybrano ten silnik.
Pełna rezystancja cewki silnika 57BYGH104 wynosi 2,2 oma. Rezystancja sterownika FETS w DRV8871 wynosi około 0,6 oma. Typowa rezystancja okablowania do iz silników wynosi około 1 oma. Tak więc moc rozpraszana w jednym obwodzie silnika to kwadrat prądu uzwojenia razy 3,8 oma. Całkowita moc jest dwa razy większa, ponieważ oba uzwojenia są napędzane jednocześnie. Dla rozważanych prądów uzwojeń wyniki przedstawiono w tej tabeli.
Ograniczenie prądów silnika do 1,6 A pozwala nam na zastosowanie mniejszego i tańszego zasilacza 24 W. Utracono bardzo mały margines momentu obrotowego. Również silniki krokowe nie są cichymi urządzeniami. Prowadzenie ich przy wyższym prądzie sprawia, że są głośniejsze. Tak więc w celu zmniejszenia mocy i cichszej pracy, limit prądu został wybrany na 1,6 ampera.
Zalecana:
Użyj silnika krokowego jako enkodera obrotowego: 9 kroków (ze zdjęciami)
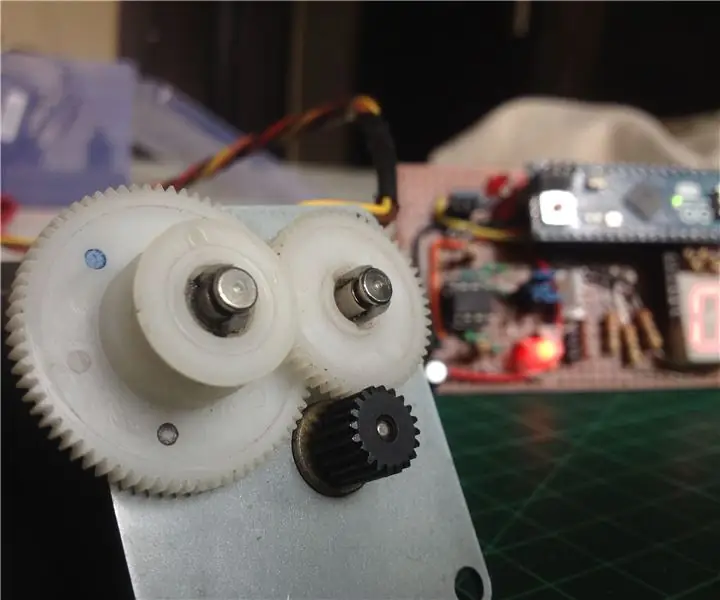
Użyj silnika krokowego jako enkodera obrotowego: Enkodery obrotowe doskonale nadają się do stosowania w projektach mikrokontrolerów jako urządzenie wejściowe, ale ich wydajność nie jest zbyt płynna i zadowalająca. Poza tym, mając dużo zapasowych silników krokowych, postanowiłem nadać im cel. Więc jeśli masz trochę steppera
Kontroluj swój komputer za pomocą silnika krokowego!: 9 kroków (ze zdjęciami)
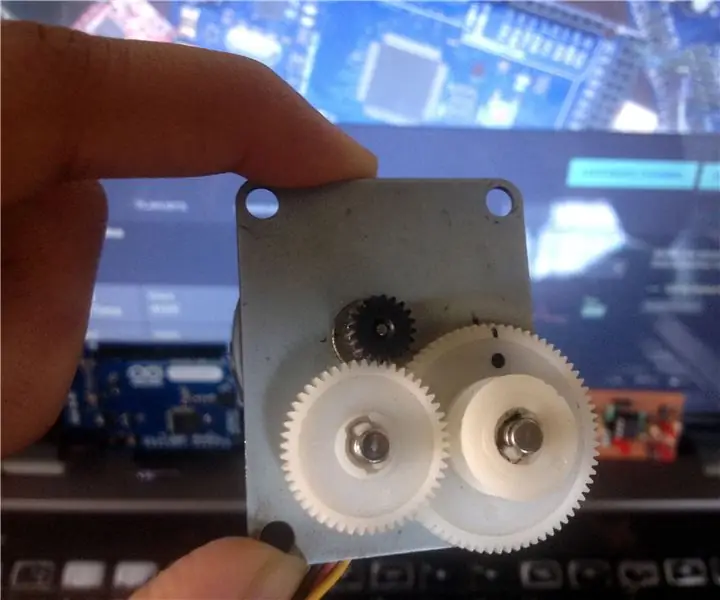
Kontroluj swój komputer za pomocą silnika krokowego!: W jednym z moich poprzednich podręczników pokazałem, jak używać silnika krokowego jako enkodera obrotowego. W tej instrukcji nauczmy się, jak możemy jej użyć do sterowania naszym komputerem. Więc bez zbędnych ceregieli, zaczynajmy
DIY sterownik silnika krokowego: 6 kroków (ze zdjęciami)
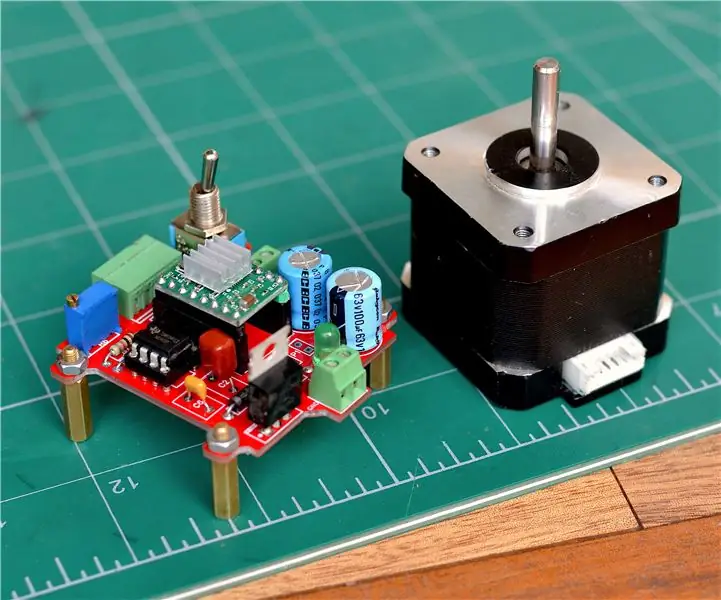
DIY sterownik silnika krokowego: pamiętaj o tych silnikach prądu stałego, wszystko, co musisz zrobić, to podłączyć dodatnie i ujemne przewody do akumulatora i ogłosić, że zaczyna działać. Ale kiedy zaczęliśmy robić bardziej złożone projekty, te silniki prądu stałego wydają się nie zapewniać tego, czego potrzebujesz …. tak, mam na myśli
Moduł projektu końcowego sterownika krokowego: 5 kroków
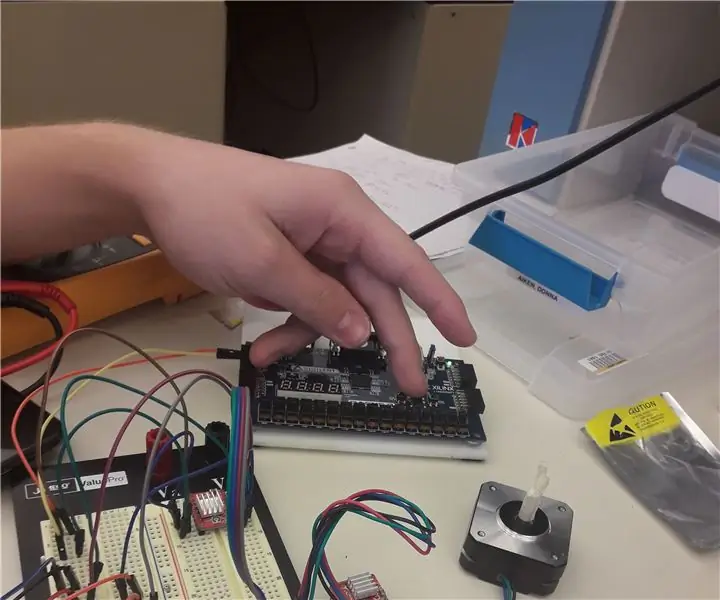
Moduł projektu końcowego sterownika krokowego: Marquis Smith i Peter Moe-Lange
Odtwarzaj utwory za pomocą silnika krokowego !!: 11 kroków (ze zdjęciami)
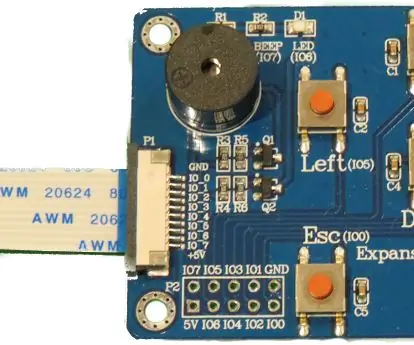
Odtwarzaj utwory za pomocą silnika krokowego!!: Ten projekt dotyczy zaprojektowania prostego dynamicznego interfejsu, który pozwoli na interakcję z silnikiem krokowym na dwa różne sposoby. Pierwszy interfejs będzie kontrolował kierunek i prędkość silnika krokowego za pomocą prosty GUI, który h