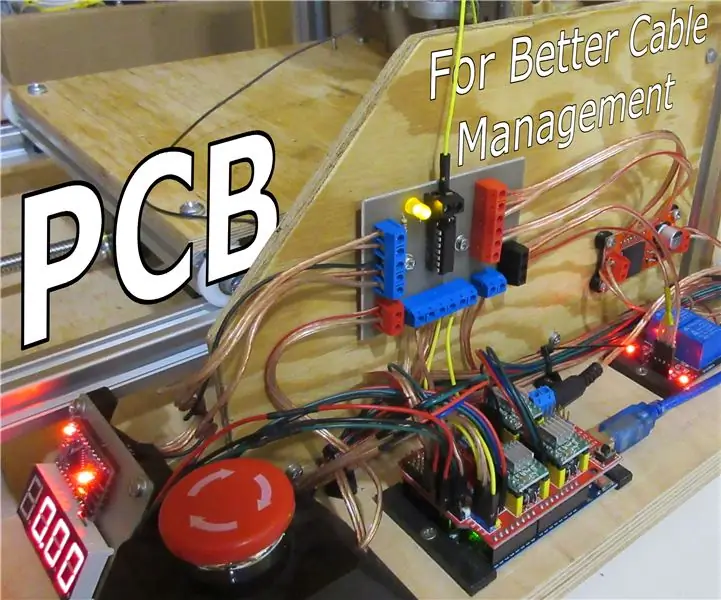
Spisu treści:
2025 Autor: John Day | [email protected]. Ostatnio zmodyfikowany: 2025-06-01 06:10
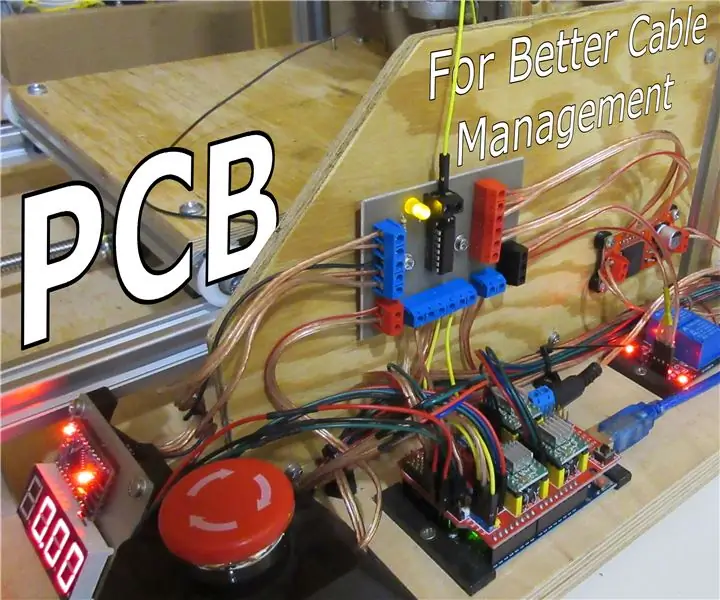
Jakiś czas temu wykonałem niestandardową stacjonarną frezarkę CNC. Od tego czasu rozbudowywałem go o nowe komponenty. Ostatnim razem dodałem drugie Arduino z 4-cyfrowym wyświetlaczem, aby kontrolować obroty mojego wrzeciona za pomocą pętli PID. Musiałem połączyć go z podstawową płytką Arduino za pomocą 5 przewodów, aby mogły się komunikować. Ale podczas mojego pierwszego testu zepsułem sterownik silnika, więc kupiłem nowy, mocniejszy. Miał też 5 dodatkowych przewodów, które musiałem podłączyć. W tym momencie pin +5V na płycie głównej został podzielony na 4 oddzielne połączenia i po prostu nie miałem ochoty ponownie dzielić przewodu. Więc zrobiłem coś innego.
Krok 1: Szkicowanie połączeń
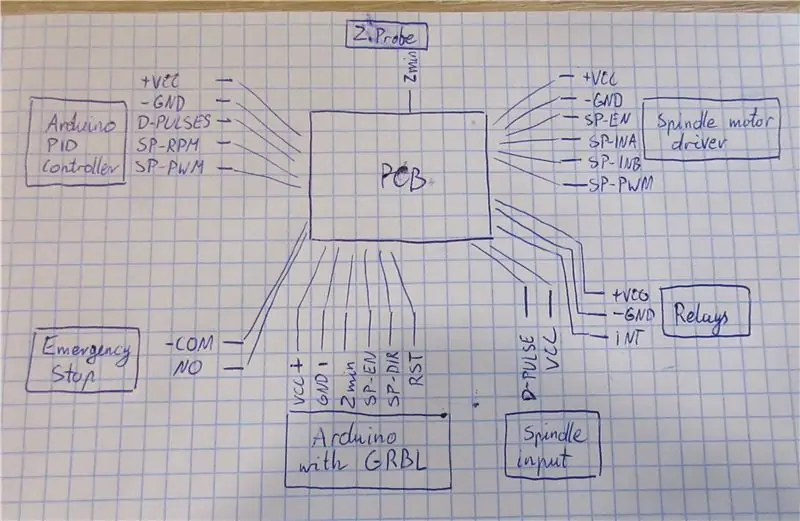
Naszkicowałem wszystkie potrzebne połączenia (z wyjątkiem przewodów silnika i ograniczników, ponieważ idą bezpośrednio do kontrolera GRBL i nigdzie indziej). Wprowadziłem również kilka zmian w już istniejących połączeniach - zatrzymanie awaryjne resetuje teraz również główne Arduino i używa tylko normalnie otwartego styku, gdzie wcześniej używał zarówno NO, jak i NC do sterowania przekaźnikiem. Dzięki nowemu sterownikowi silnika uproszczono również połączenie z przekaźnikami.
Krok 2: Problemy z połączeniami
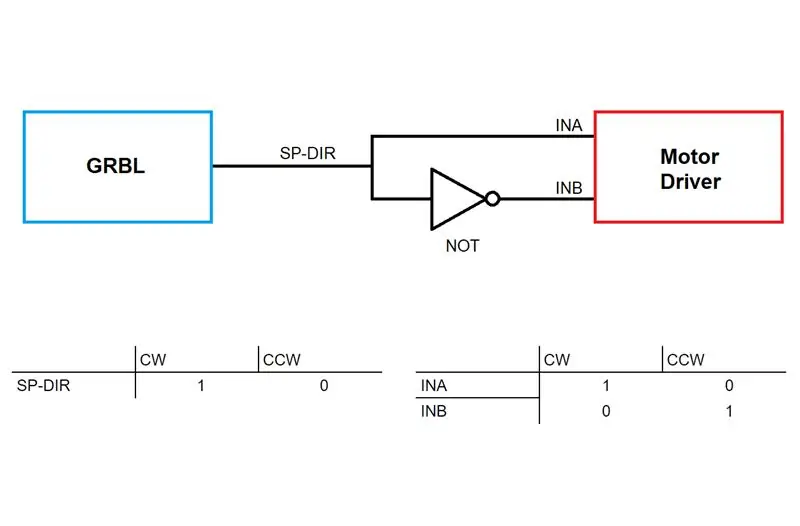
Poprzedni sterownik silnika, którego używałem, to prosta płytka z transoptorem i mosfetem. Mogła obracać wrzeciono tylko w jednym kierunku, więc nie było potrzeby używania kołka kierunkowego. Nowy jest nieco bardziej skomplikowany. Ma piny o nazwie INA i INB, i w zależności od tego, czy chcę obracać się zgodnie z ruchem wskazówek zegara, czy przeciwnie, muszę pociągnąć jeden z nich do VCC. Nie brzmi to tak skomplikowanie, problem polega na tym, że GRBL ma tylko jeden pin zwany SP-DIR (pin kierunku wrzeciona), który jest przeciągany do VCC dla ruchu zgodnego z ruchem wskazówek zegara i do GND dla ruchu przeciwnego do ruchu wskazówek zegara. Nie wiem, czy można to zmienić w GRBL (jest to dla mnie trochę zbyt skomplikowany program), więc zrobiłem to inną metodą.
Właśnie dodałem bramkę logiczną NOT do schematu, która odwróci sygnał SP-DIR i umieści go w INB. Dlatego gdy pin DIR jest wysoki, INA jest również wysoki (są one połączone), a INB jest odwrócony do niskiego (CW), a gdy DIR jest niski, INA jest również niski, a INB jest wysoki (CCW).
Krok 3: Inteligentny, ale nie tak prosty projekt
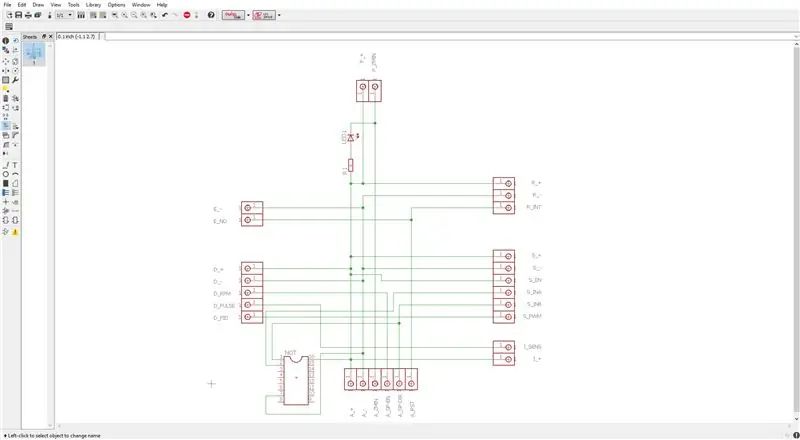
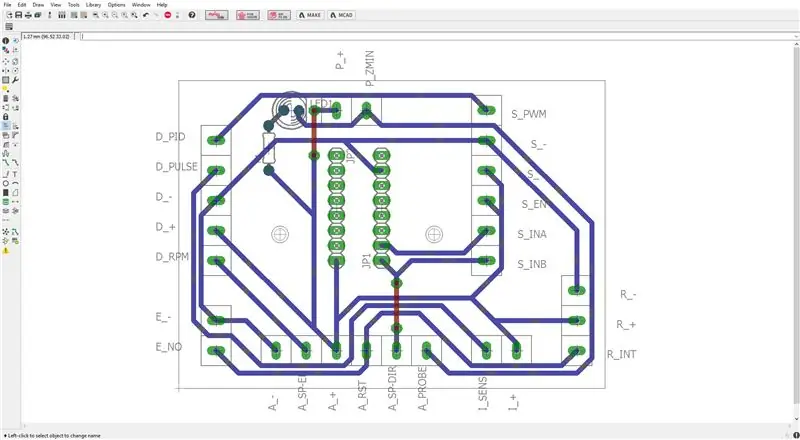
Następnie zaprojektowałem płytkę drukowaną w Eagle, która miała wszystkie niezbędne połączenia wewnątrz. Ale przy tylu przewodach nie było to takie proste.
Najpierw stworzyłem niestandardową bibliotekę Eagle dla moich bloków terminali. Jest bardzo prosty, w zasadzie to zwykły pin, tylko większy - rozstaw 5,08 mm (0,2”).
Frezowałbym go na CNC i dlatego chciałem, aby była to płytka jednostronna. Ale z 26 listwami zaciskowymi i kilkoma wewnętrznymi połączeniami z bramką logiczną zaprojektowanie tego było trudnym zadaniem. Można to zrobić, ale z dużą ilością zworek. To jest powód, dla którego wszystkie moje listwy zaciskowe (w Eagle) są tylko pojedynczymi pinami. W ten sposób mogę je przenosić w obszarze roboczym płytki i unikać używania przewodów połączeniowych. Wadą jest to, że lokalizacja niektórych połączeń wydaje się przypadkowa. Na przykład patrząc od spodu mamy GND, potem SP-EN, a potem VCC, co jest bardzo rzadkie. Ale w ten sposób mogłem zredukować liczbę zworek do zaledwie 2 i łatwiej mi było wykonać PCB.
Specjalne są również nazwy bloków zacisków. Zostały one pogrupowane tak, że np. A oznacza Arduino, więc wszystkie zaciski śrubowe o nazwie A_ należy umieścić na spodzie płytki, ponieważ Arduino z GRBL znajduje się pod płytką.
Na koniec dodałem również prostą diodę LED wskazującą stan sondy Z.
Krok 4: Tworzenie tablicy
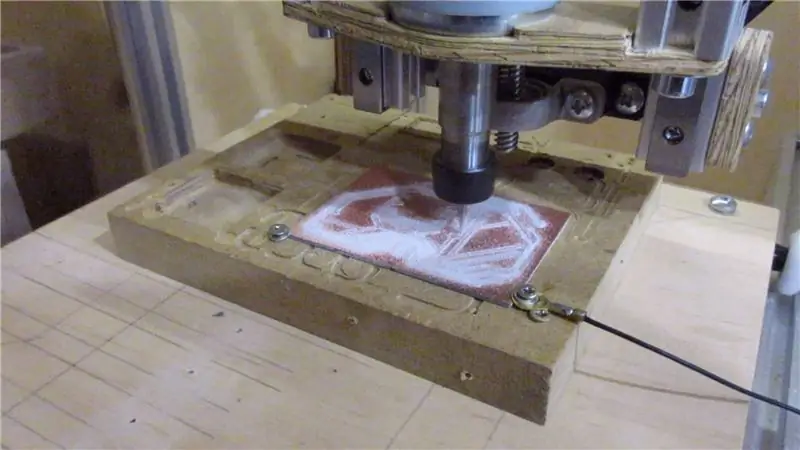
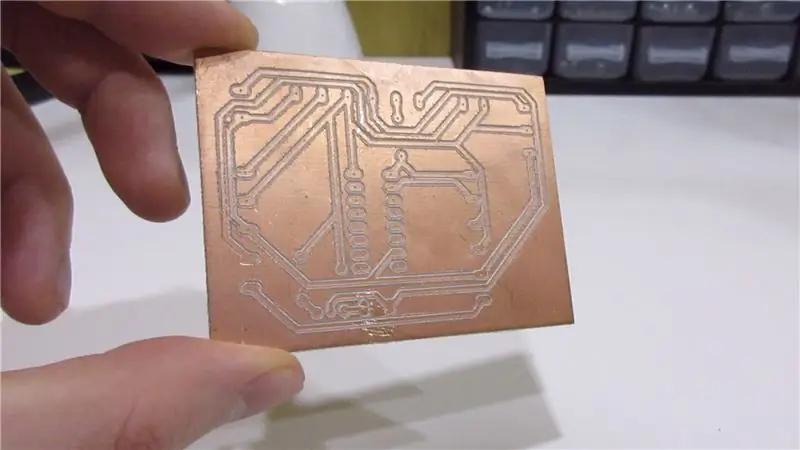
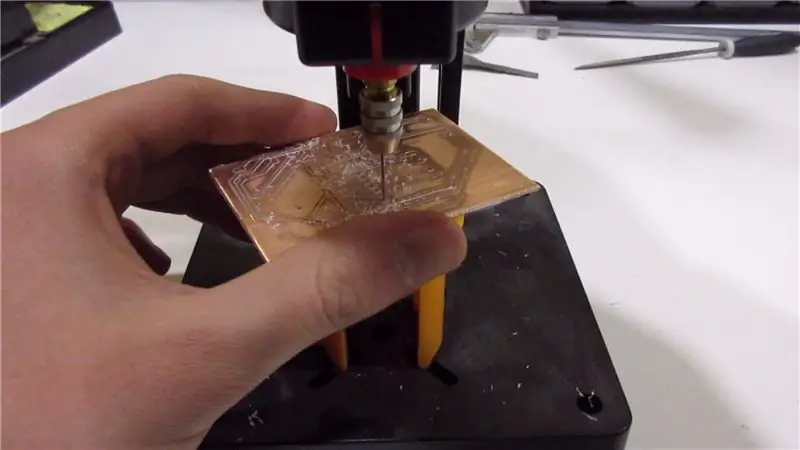
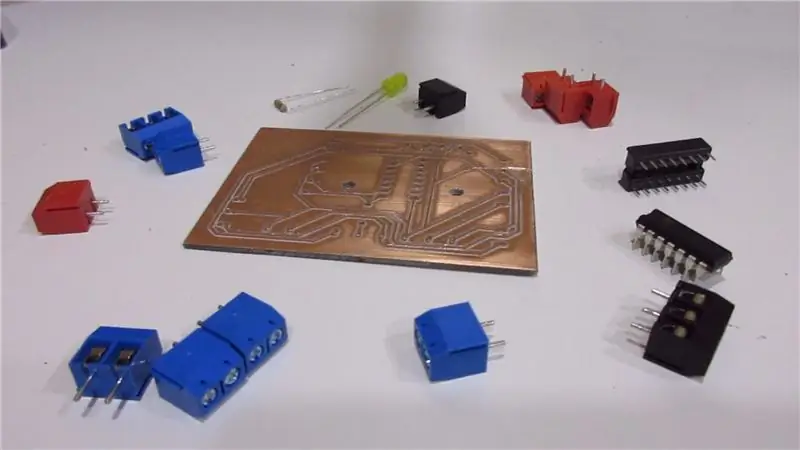
Jak powiedziałem wcześniej, wyfrezowałem płytkę na moim DIY CNC, wywierciłem otwory i przylutowałem wszystkie elementy. W tym procesie nie było nic szczególnego, co sprawiało, że PCB była jak każda inna.
Jeśli nie posiadasz CNC możesz wykonać PCB metodą termotransferu lub zamówić u profesjonalnego producenta.
Nie zapomnij również sprawdzić wszystkich połączeń za pomocą multimetru, aby znaleźć i naprawić ewentualne błędy.
Krok 5: Łączenie wszystkiego razem
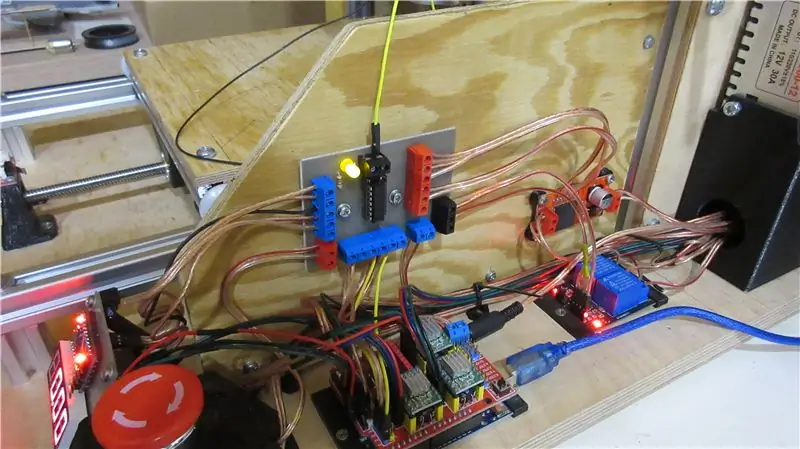
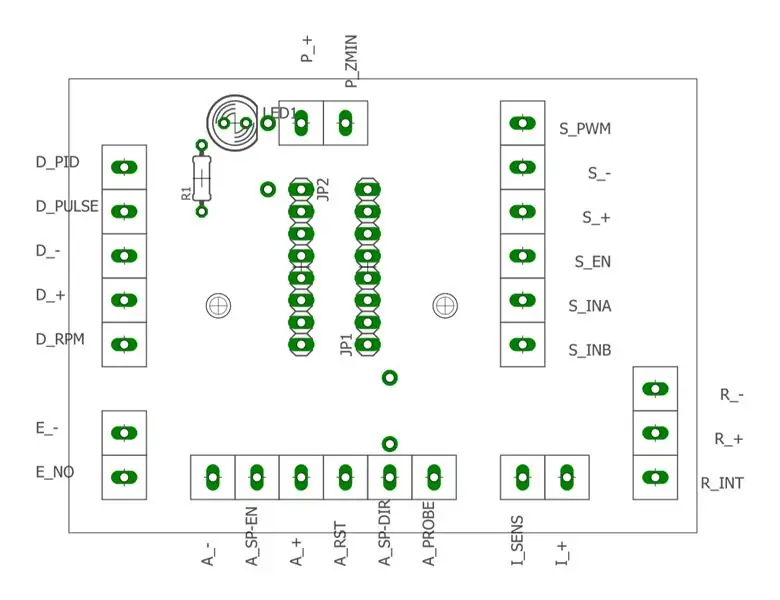
Jednym z ostatnich kroków było umieszczenie gotowej płytki PCB w maszynie i podłączenie wszystkich przewodów. Wydrukowałem mały schemat płytki, aby pomóc mi podłączyć każdy przewód tam, gdzie powinien być. Po ponownym sprawdzeniu połączeń był gotowy do testów!
Zalecana:
Nawigacja głosowa Raspberry Pi pomaga niewidomym: 7 kroków (ze zdjęciami)
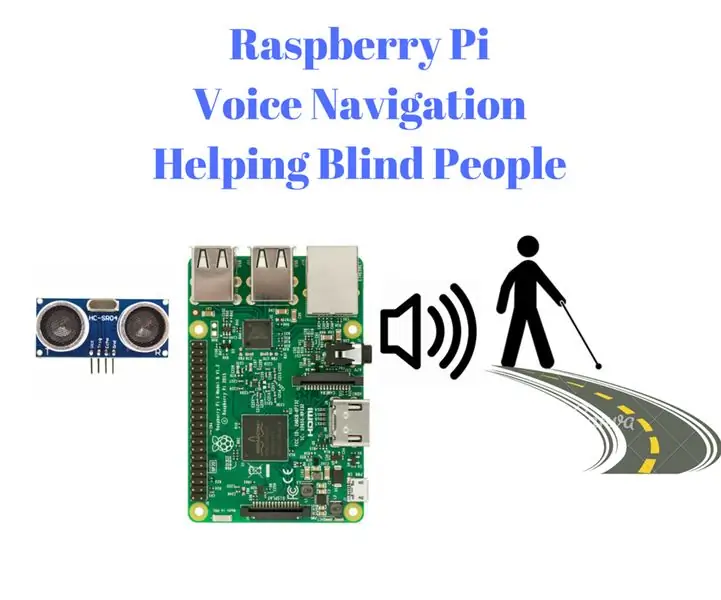
Nawigacja głosowa Raspberry Pi pomagająca osobom niewidomym: Cześć W tej instrukcji zobaczymy, jak raspberry pi może pomóc osobom niewidomym za pomocą instrukcji głosowych zdefiniowanych przez użytkownika. Tutaj za pomocą wejścia czujnika ultradźwiękowego do pomiaru odległości możemy głos prowadzi niewidomych do podążania
ANTYDYSTRAKCJA: uchwyt do smartfona, który pomaga skupić się: 7 kroków (ze zdjęciami)
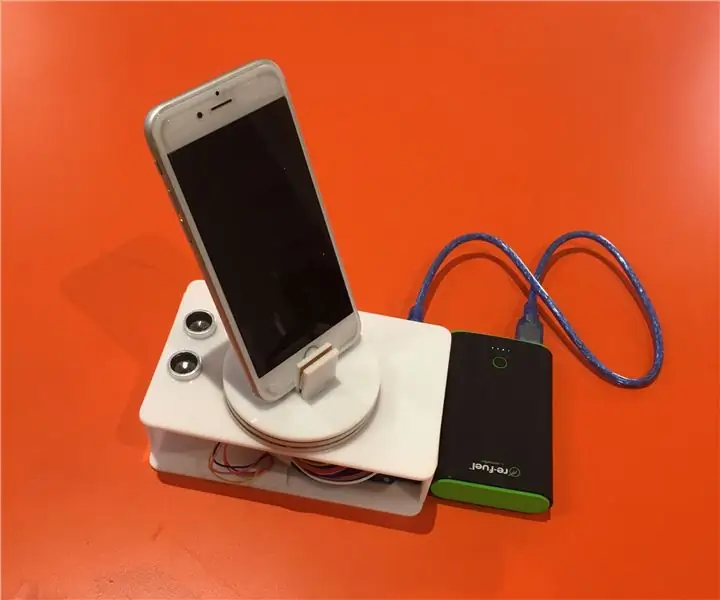
ANTiDISTRACTION: uchwyt do smartfona, który pomaga Ci się skupić: Nasze urządzenie ANTIDISTRACTION ma na celu przerwanie wszelkich form rozproszenia przez komórki w okresach intensywnego skupienia. Maszyna działa jak stacja ładująca, na której zamontowane jest urządzenie mobilne, aby zapewnić środowisko wolne od zakłóceń
Wtyki Arduino Mega RJ45 do zarządzania kablami: 5 kroków

Wtyki Arduino Mega RJ45 do zarządzania kablami: Arduino Mega ma mnóstwo pinów - to duży powód, aby kupić jeden, prawda? Chcemy wykorzystać wszystkie te szpilki! Okablowanie może jednak szybko stać się bałaganem spaghetti bez zarządzania kablami. Możemy skonsolidować przewody za pomocą wtyczek Ethernet. Piny danych na
Skrzynka ładująca IKEA - nigdy więcej bałaganu z kablami! Bardzo łatwe do zrobienia: 3 kroki
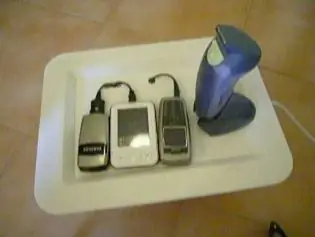
Skrzynka ładująca IKEA - nigdy więcej bałaganu z kablami! Bardzo łatwe do zrobienia: Opierając się na tym, co przeczytałem w Internecie na temat bałaganu i bałaganu na kablach (telefon komórkowy, PDA, iPod itp. - ładowarki), wymyśliłem, jak zrobić proste i bardzo łatwe do zrobienia pudełko z ładowarką. to szczególnie w odniesieniu do jego prostoty, a dlaczego nie, dyskretnego i ko
Przenośne zarządzanie kablami: 16 kroków (ze zdjęciami)
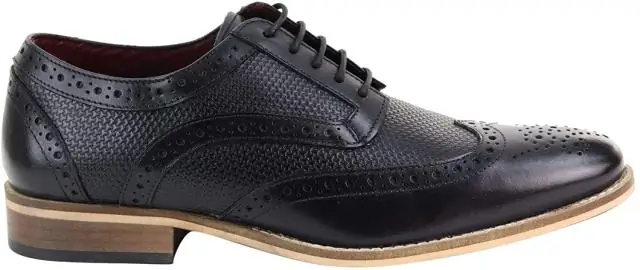
Przenośne zarządzanie kablami: Elektronika użytkowa zamieszkuje codzienną przestrzeń osobistą, miniaturyzacja umożliwia im mobilność i samodzielność. To jest dochodzenie w sprawie zarządzania przenośnymi przewodami. Obowiązuje tu zarówno elektronika użytkowa, jak i profesjonalna, choć temat będzie szerzej