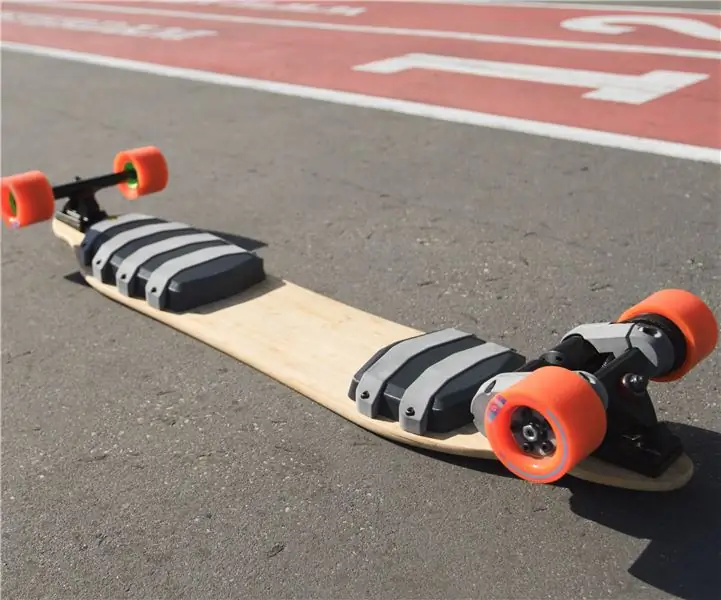
Spisu treści:
2025 Autor: John Day | [email protected]. Ostatnio zmodyfikowany: 2025-01-23 15:03
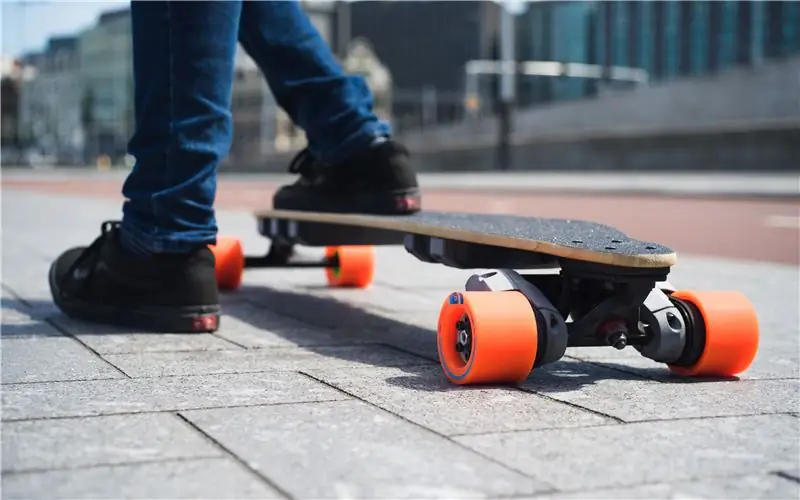
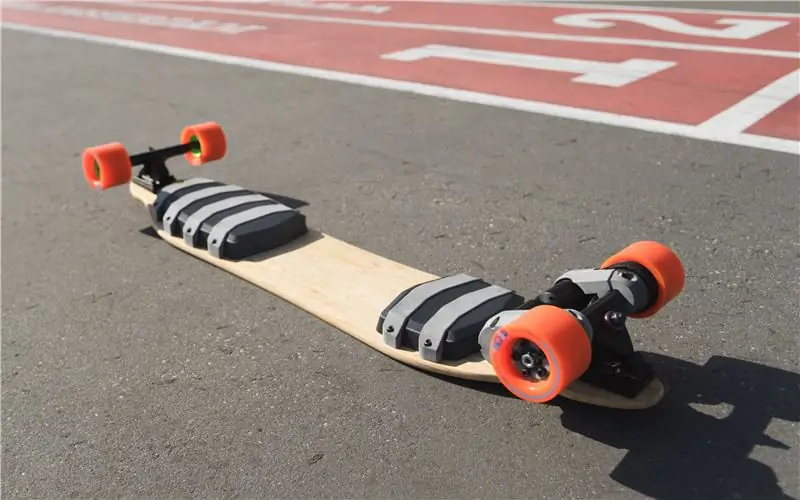
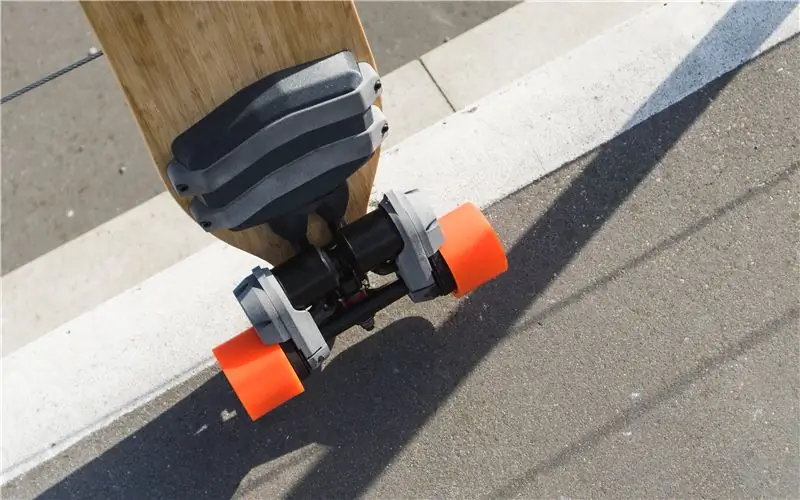
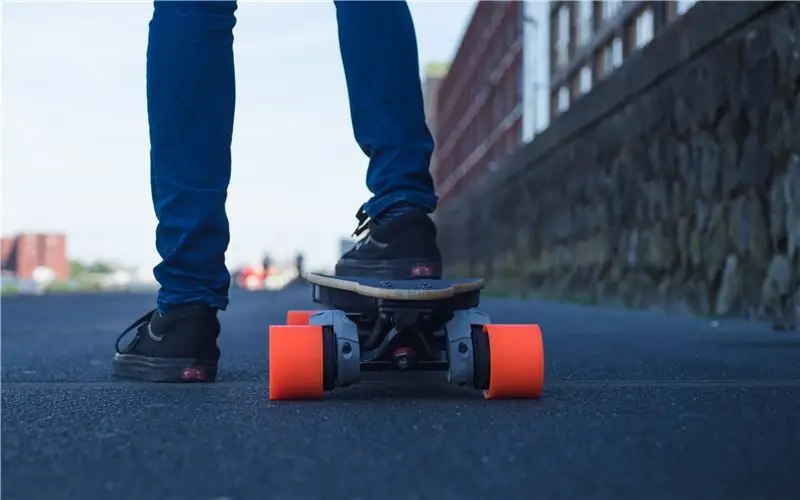
Ta instrukcja jest przeglądem procesu budowy tablicy elektronicznej Fusion, którą zaprojektowałem i zbudowałem podczas pracy w 3D Hubs. Projekt został zlecony w celu promowania nowej technologii HP Multi-Jet Fusion oferowanej przez 3D Hubs oraz pokazania wielu technologii drukowania 3D i sposobów ich efektywnego łączenia.
Zaprojektowałem i zbudowałem longboard z napędem elektrycznym, który może być używany do krótkich lub umiarkowanych podróży lub w połączeniu z transportem publicznym, aby zapewnić znacznie szerszy zasięg podróżowania. Ma dużą prędkość maksymalną, jest bardzo zwrotny i można go łatwo przenosić, gdy nie jest używany.
Krok 1: Proces projektowania
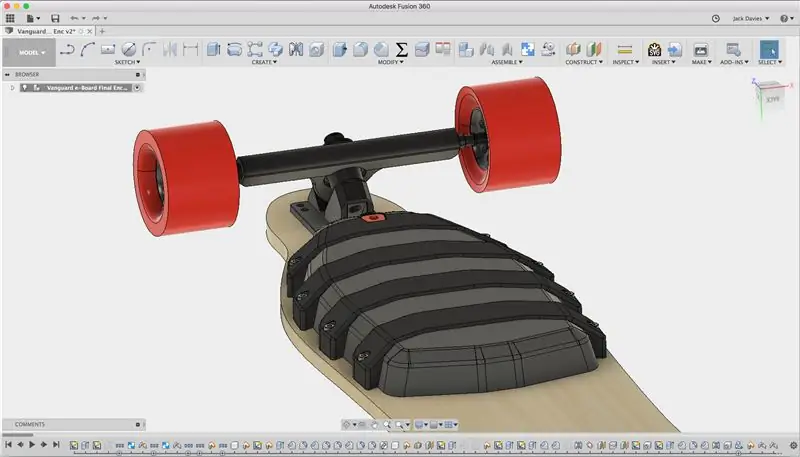
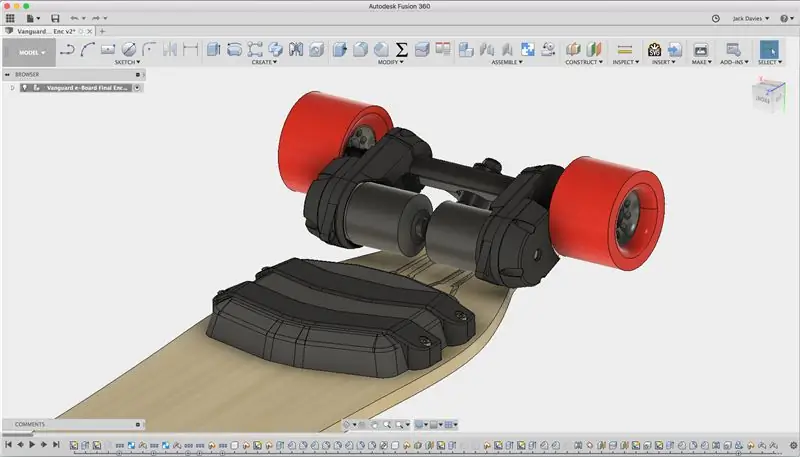
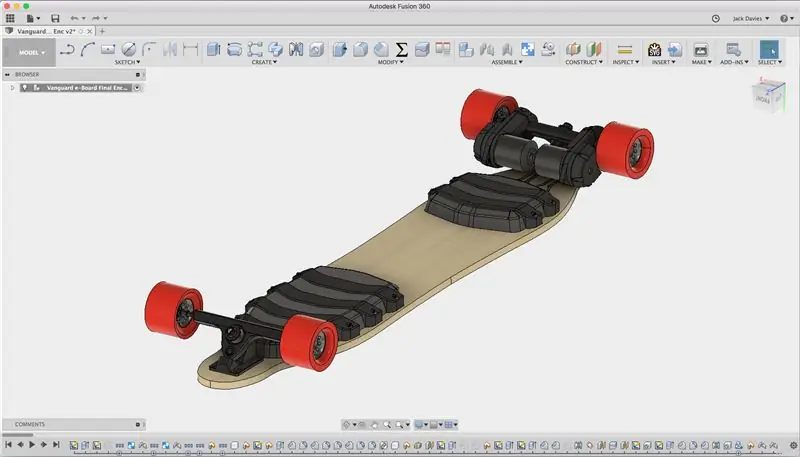
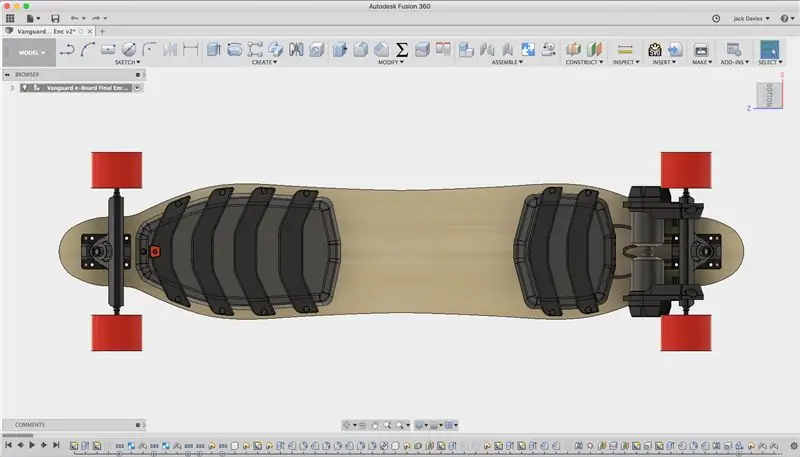
Zacząłem projekt od zidentyfikowania głównych standardowych elementów longboardu; ciężarówki, pokład i koła. Były to części z półki, więc wykorzystałem je jako punkt wyjścia do projektu. Pierwszym etapem było zaprojektowanie układu napędowego, w tym mocowań silnika, konfiguracji przekładni i pewnych modyfikacji ciężarówek. Rozmiar i położenie mocowań silnika dyktowałyby rozmiar i położenie obudów, dlatego ważne było, aby zostało to wykonane jako pierwsze. Obliczyłem żądaną prędkość maksymalną i wymagania dotyczące momentu obrotowego, co pozwoliło mi wybrać silniki i akumulator do płyty. Obliczono również przełożenie i dobrano rozmiary kół pasowych oraz długość pasa napędowego. Umożliwiło mi to wypracowanie odpowiedniego rozmiaru mocowań silnika, co zapewniało dobrze napięty pasek.
Kolejnym etapem było zaprojektowanie obudowy akumulatora i regulatora prędkości (ESC). Wybrany blat składa się głównie z bambusa, więc jest dość elastyczny, zginając się zasadniczo w środku. Ma to zalety, że jest wygodny w prowadzeniu, ponieważ pochłania nierówności na drodze i nie przenosi ich na jeźdźca. Jednak oznacza to również, że potrzebna jest dzielona obudowa, aby pomieścić baterię i elektronikę, ponieważ obudowa o pełnej długości nie byłaby w stanie zginać się z płytą i miałaby kontakt z ziemią podczas pracy. Elektroniczne regulatory prędkości (ESC) zostały umieszczone najbliżej silników ze względu na ograniczenia elektryczne. Ponieważ silniki są mocowane za pośrednictwem ciężarówek, pozycja zmienia się podczas skrętów, więc obudowa musiała być zaprojektowana tak, aby umożliwić prześwit między silnikami.
System akumulatorów został umieszczony na drugim końcu pokładu i mieścił elektronikę związaną z zasilaniem. Obejmował on pakiet baterii składający się z 20 ogniw litowo-jonowych 18650, system zarządzania baterią, włącznik/wyłącznik i gniazdo ładowania.
Użyłem Autodesk Fusion360 do całego procesu projektowania, to oprogramowanie umożliwiło mi szybkie modelowanie komponentów wewnątrz głównego złożenia, co znacznie przyspieszyło czas rozwoju. Wykorzystałem również funkcje symulacji w Fusion360, aby upewnić się, że części będą wystarczająco mocne, zwłaszcza mocowania silnika. Umożliwiło mi to faktyczne zmniejszenie rozmiaru mocowań, ponieważ mogłem zweryfikować wymagania dotyczące wytrzymałości i ugięcia oraz usunąć materiał, zachowując jednocześnie odpowiedni współczynnik bezpieczeństwa. Po zakończeniu procesu projektowania bardzo łatwo było wyeksportować poszczególne części do druku 3D.
Krok 2: Układ napędowy
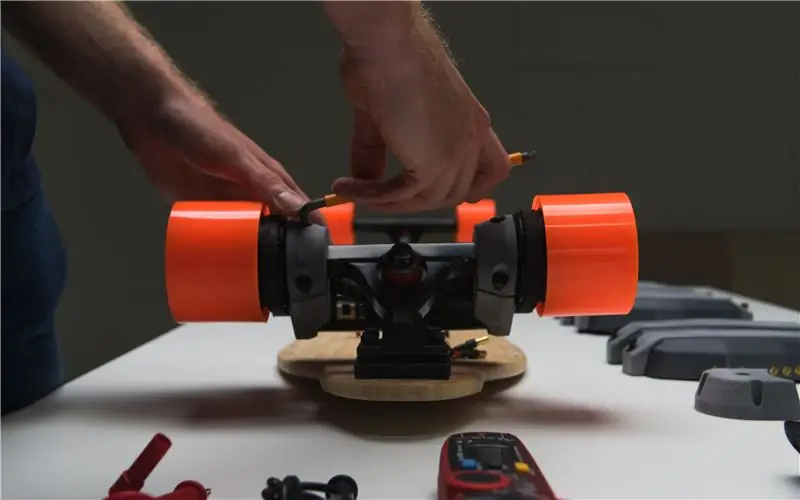
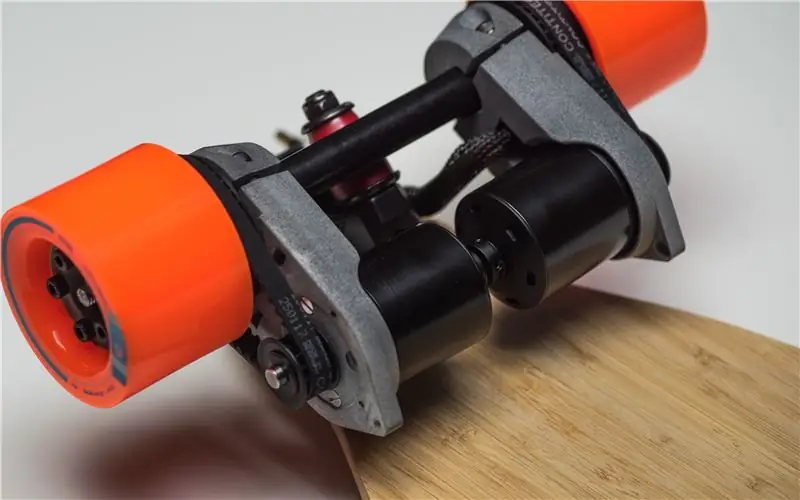
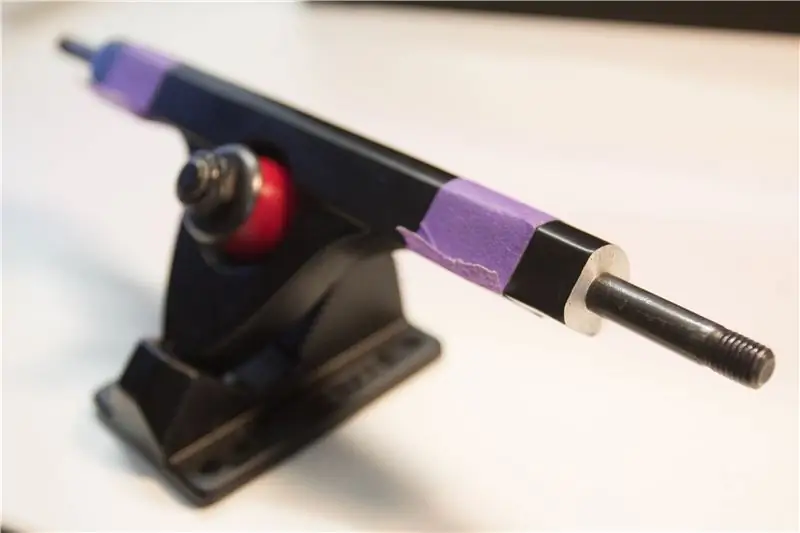
Najpierw ukończyłem budowę układu napędowego, aby zapewnić odpowiedni prześwit dla obudowy elektroniki. Wybrałem ciężarówki Calibre, ponieważ mają kwadratowy profil, który idealnie nadaje się do mocowania mocowań silnika. Jednak oś była nieco za krótka, aby umożliwić użycie dwóch silników w tej samej ciężarówce, więc musiałem ją przedłużyć, aby umożliwić dopasowanie kół.
Osiągnąłem to, wycinając część aluminiowego nadwozia wieszaka ciężarówki, odsłaniając więcej stalowej osi. Następnie odciąłem większość osi, pozostawiając około 10 mm, które mogłem następnie gwintować za pomocą matrycy M8.
Następnie można było przykręcić sprzęg i dodać kolejną oś gwintowaną, skutecznie wydłużając oś. Użyłem pasty mocującej Loctite 648, aby trwale zabezpieczyć sprzęg i nową oś, aby nie odkręcały się podczas użytkowania. Umożliwiło to dopasowanie dwóch silników do ciężarówki i zapewniło dużo miejsca na koła.
Układ napędowy został przede wszystkim wydrukowany przy użyciu technologii HP Multi-Jet Fusion, aby zapewnić sztywność i wytrzymałość podczas dużych przyśpieszeń i hamowania, gdzie przenoszone byłyby największe siły.
Zaprojektowano specjalne koło pasowe do blokowania w tylnych kołach, które następnie zostało połączone z kołem pasowym silnika za pomocą paska HTD 5M. Dodano wydrukowaną w 3D osłonę, aby zapewnić ochronę zespołu koła pasowego.
Krok 3: Obudowy żeber
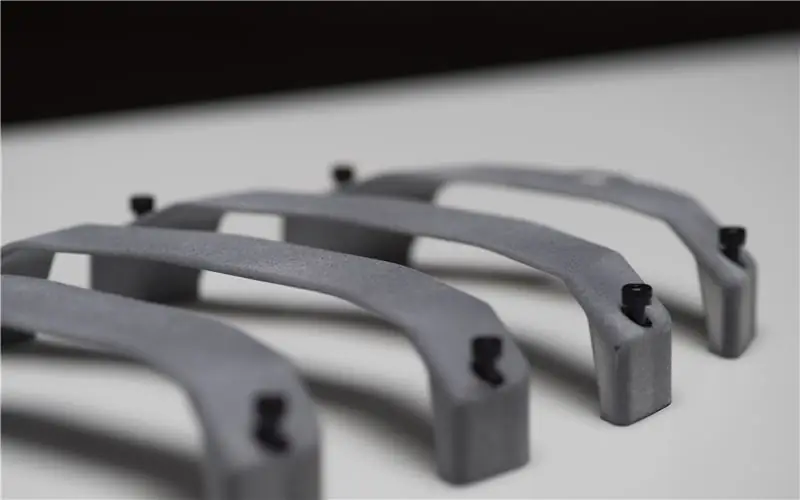
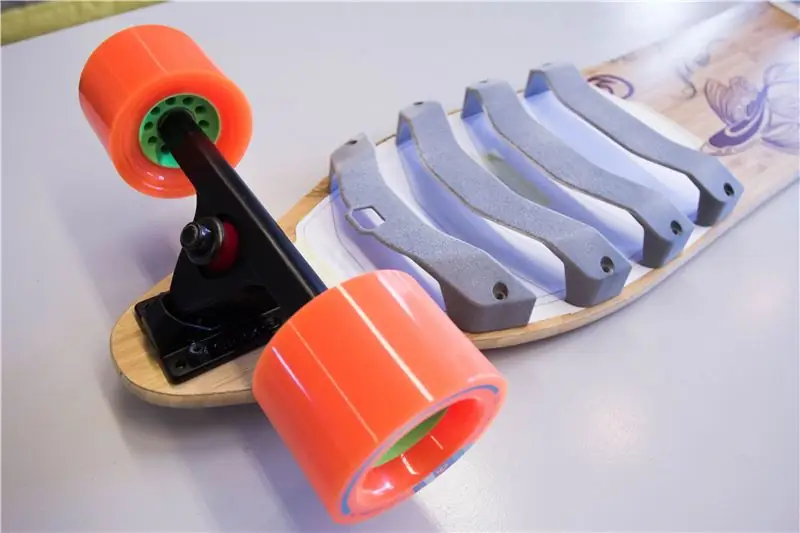
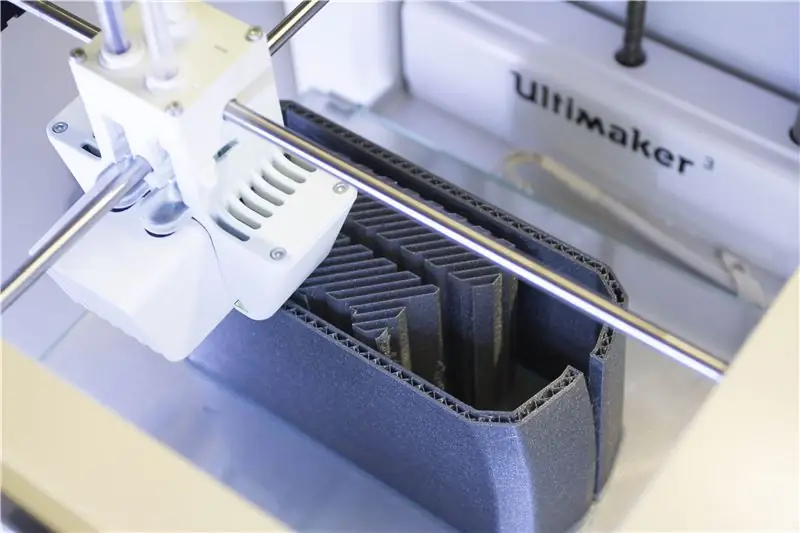
Jedną z głównych decyzji projektowych, jakie podjąłem, było oddzielenie obudów, co zaowocowało czystym wyglądem i umożliwiło funkcjonowanie elastycznego pokładu bez dodatkowej sztywności obudowy. Chciałem przekazać funkcjonalne aspekty technologii HP Multi Jet Fusion, więc zdecydowałem się wydrukować główny korpus obudów metodą FDM, co obniżyło koszty, a następnie użyć części HP do podparcia i zamocowania ich na pokładzie. Zapewniło to ciekawą estetykę, a jednocześnie było bardzo funkcjonalne.
Obudowy z nadrukiem FDM zostały podzielone na pół, aby ułatwić drukowanie, ponieważ materiał podporowy można było wyeliminować z powierzchni zewnętrznej. Linia podziału została starannie umieszczona, aby zapewnić jej ukrycie przez część HP po przymocowaniu do deski. Dodano otwory na połączenia silnika i przyklejono pozłacane złącza kulowe, aby
Gwintowane wkładki zostały osadzone w bambusowym pokładzie, aby przymocować obudowy do deski, i zostały wyszlifowane równo z powierzchnią deski, aby zapewnić brak szczeliny między deską a obudową.
Krok 4: Elektronika
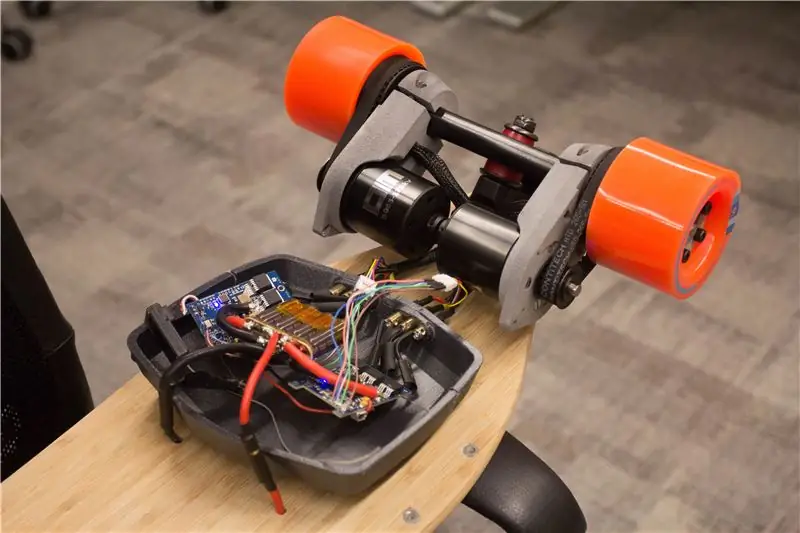
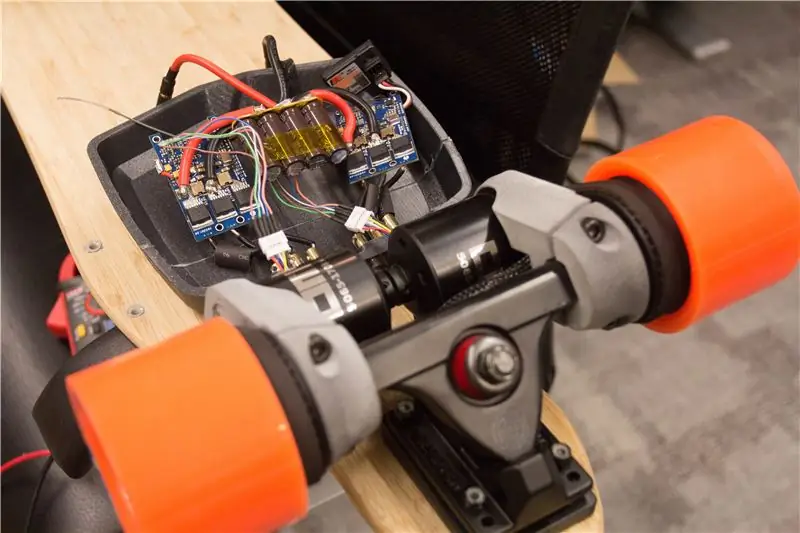
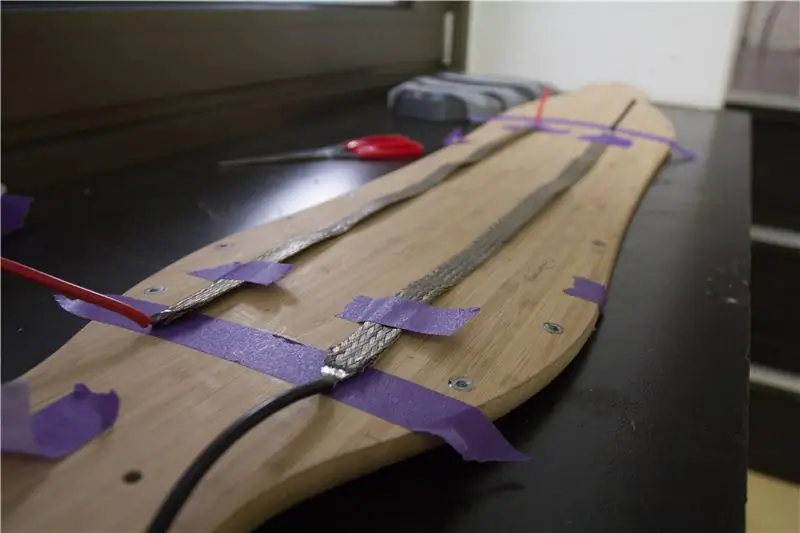
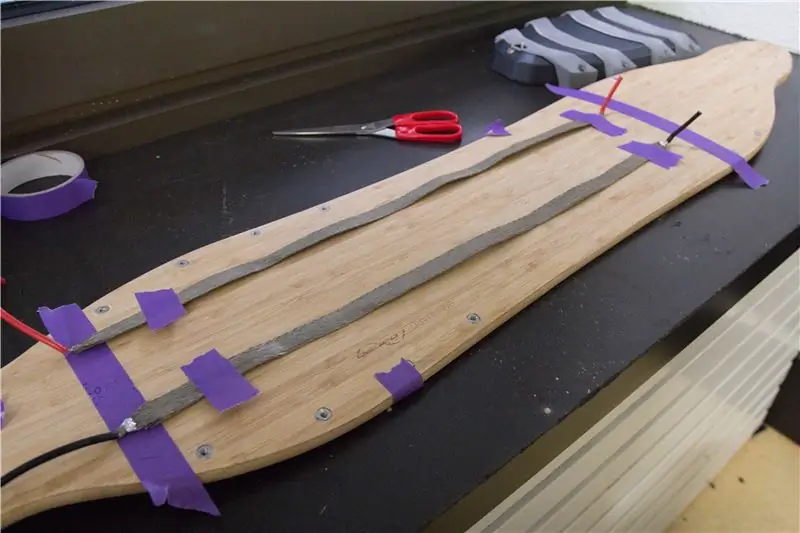
Elektronika została starannie dobrana, aby zapewnić, że płyta jest wydajna, ale także intuicyjna w użyciu. Ta płyta może być potencjalnie niebezpieczna, jeśli wystąpią jakiekolwiek awarie, więc niezawodność jest bardzo ważnym czynnikiem.
Pakiet akumulatorów składa się z 20 pojedynczych ogniw litowo-jonowych 18650, które są zgrzewane punktowo, tworząc pakiet 42v. 2 ogniwa są spawane równolegle, a 10 szeregowo; używane przeze mnie ogniwa to Sony VTC6. Użyłem zgrzewarki punktowej do zgrzania zakładek niklowych, aby utworzyć pakiet, ponieważ lutowanie wytwarza zbyt dużo ciepła, które może uszkodzić ogniwo.
Moc z obudowy akumulatora była przekazywana do skrzynki kontrolera prędkości za pomocą płaskiego kabla w oplocie, który był prowadzony tuż pod griptape na górnej stronie decku. Pozwoliło to na „ukrycie” kabli i wyeliminowało potrzebę prowadzenia kabli od spodu, które wyglądałyby brzydko.
Ponieważ jest to płyta z dwoma silnikami, do niezależnego sterowania każdym silnikiem wymagane są dwa kontrolery prędkości. Do tej konstrukcji użyłem kontrolera prędkości VESC, który jest kontrolerem specjalnie zaprojektowanym do deskorolek elektrycznych, co czyni go bardzo niezawodnym do tego zastosowania.
Zastosowane silniki to 170kv 5065 out-runners, które mogą wytwarzać 2200W każdy, co stanowi dużo mocy dla tej płyty. Przy obecnej konfiguracji przełożeń maksymalna prędkość deski wynosi około 35 MPH i bardzo szybko przyspiesza.
Ostatnim etapem było stworzenie pilota do sterowania deską. Preferowano system bezprzewodowy ze względu na łatwiejszą obsługę. Jednak ważne było zapewnienie wysokiej niezawodności transmisji, ponieważ spadek komunikacji może mieć poważne problemy z bezpieczeństwem, szczególnie przy dużych prędkościach. Po przetestowaniu kilku protokołów transmisji radiowej zdecydowałem, że częstotliwość radiowa 2,4 GHz będzie najbardziej niezawodna dla tego projektu. Użyłem gotowego nadajnika samochodowego RC, ale znacznie zmniejszyłem rozmiar, przenosząc elektronikę do małej podręcznej obudowy, która została wydrukowana w 3D.
Krok 5: Gotowa tablica i film promocyjny
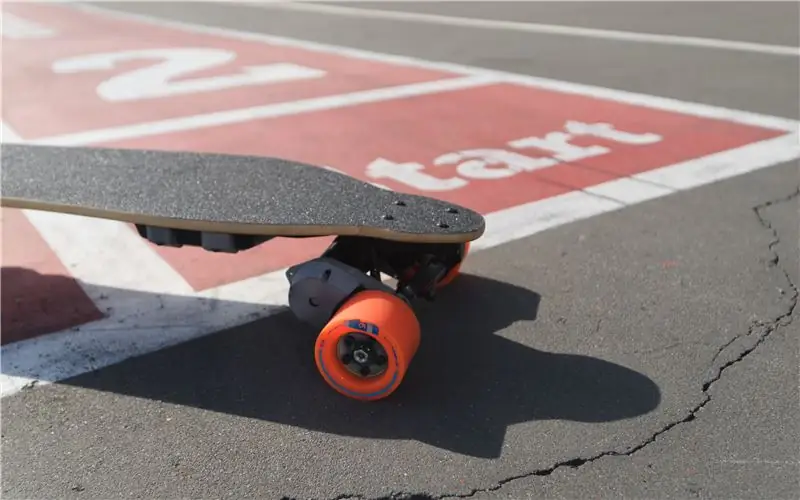
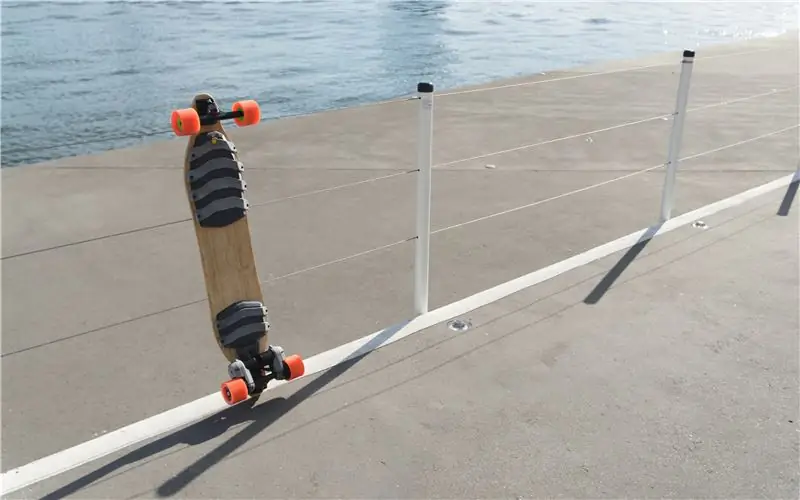
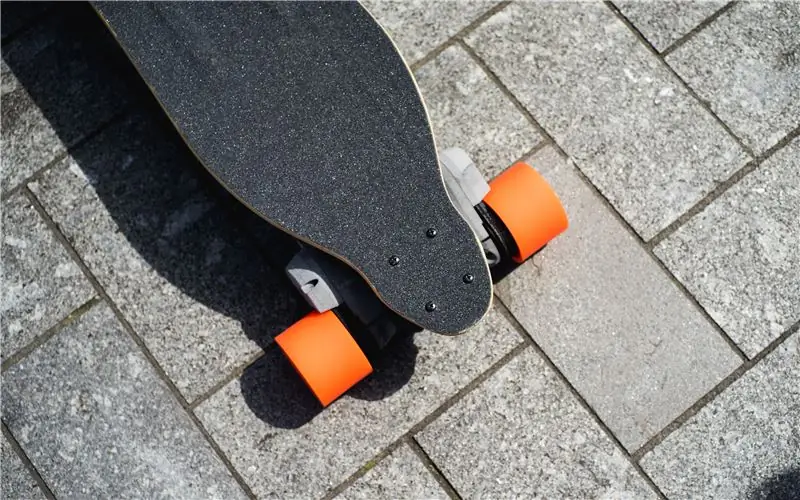
Projekt zakończony! Stworzyliśmy całkiem niesamowite wideo z tablicy w akcji, możesz to sprawdzić poniżej. Ogromne podziękowania dla 3D Hubs za umożliwienie mi wykonania tego projektu - sprawdź je tutaj, jeśli chodzi o wszystkie Twoje potrzeby związane z drukowaniem 3D! 3dhubs.com
Zalecana:
Elektryczna gitara na cygara: 18 kroków (ze zdjęciami)
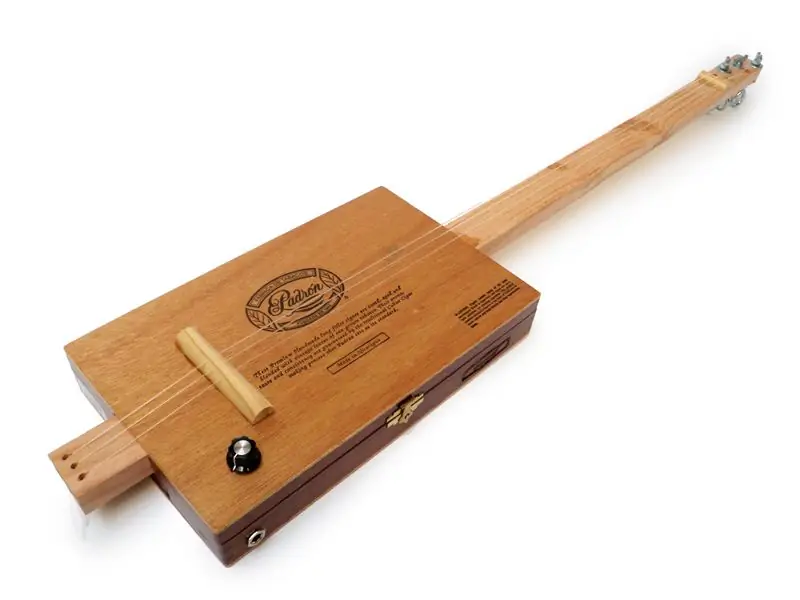
Elektryczna gitara cygarowa: Chociaż produkcja gitar przeszła długą drogę w ciągu ostatnich stu lat, jest długa historia pokazująca, że nie trzeba wiele, aby zrobić gitarę. Wszystko czego potrzebujesz to pudełko do rezonowania dźwięku, deska, która będzie działać jak podstrunnica, kilka śrub
Świeca elektryczna zasilana świecą: 8 kroków (ze zdjęciami)
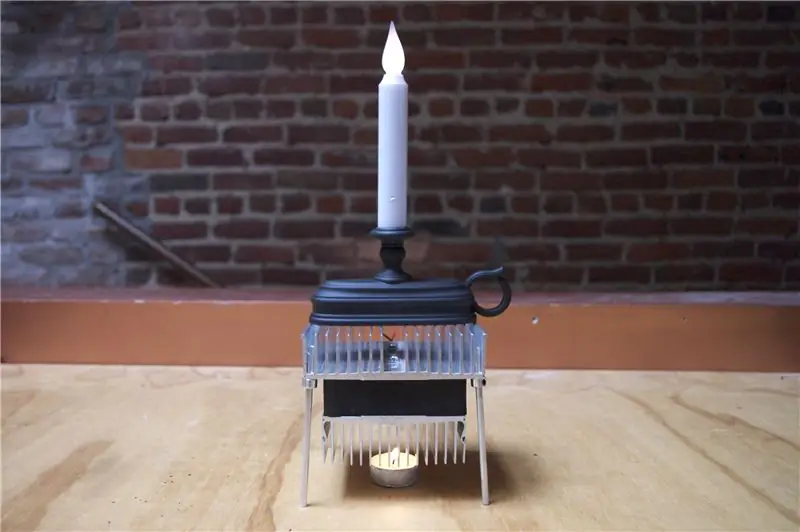
Świeca elektryczna zasilana świecą: Po obejrzeniu doniesień prasowych o huraganie Sandy i wysłuchaniu próby, przez którą przeszła cała moja rodzina i przyjaciele w Nowym Jorku i New Jersey, zaczęłam myśleć o mojej własnej gotowości na wypadek awarii. San Francisco - w końcu - znajduje się na bardzo
Bezpieczniejsza elektryczna kuchenka do hot dogów: 14 kroków (ze zdjęciami)
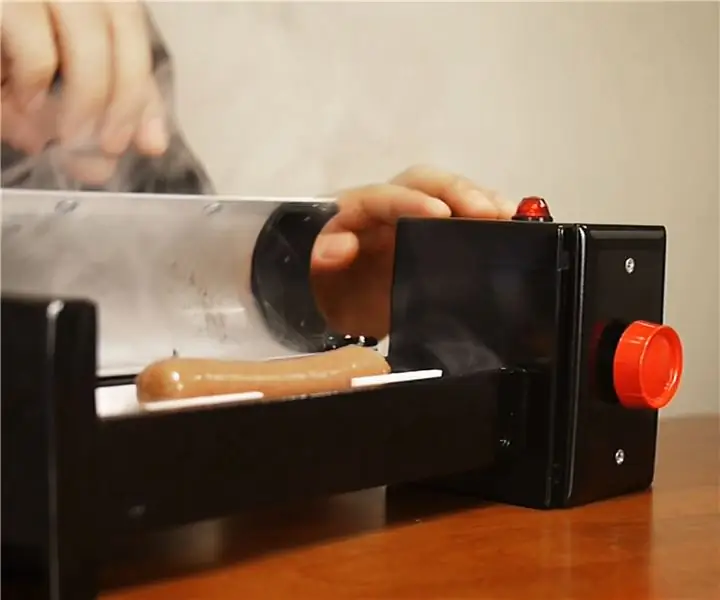
Bezpieczniejsza elektryczna kuchenka do hot dogów: Kiedy byłem studentem fizyki, gotowaliśmy hot dogi, podłączając je bezpośrednio do gniazdka 120 V. Była to stosunkowo niebezpieczna operacja, ponieważ po prostu przymocowaliśmy końce przedłużacza do dwóch śrub, które zostały włożone do h
PODGRZEWANA ELEKTRYCZNA BUTELKA WODY DIY (USB): 11 kroków (ze zdjęciami)
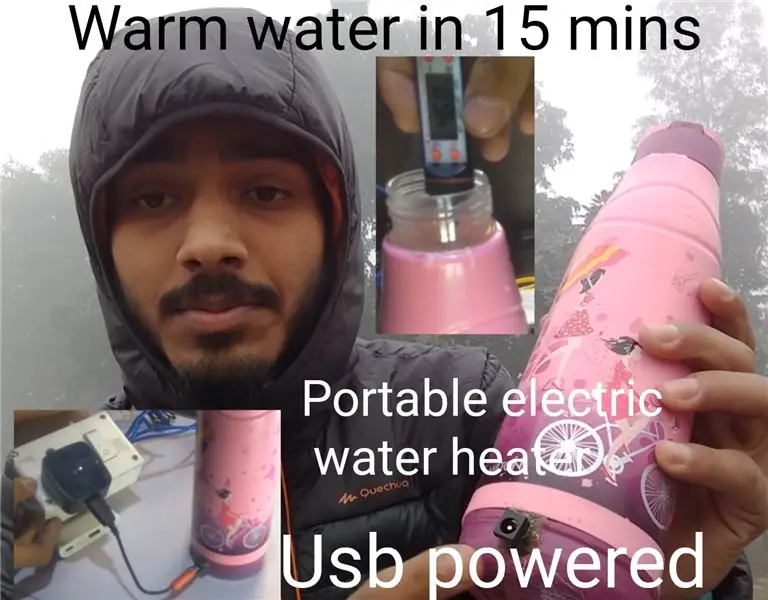
DIY ELEKTRYCZNA BUTELKA NA WODĘ PODGRZEWAJĄCĄ (USB): To jest coś, co do tej pory nie istnieje na świecie, chcę wiedzieć, dlaczego ludzie, dlaczego nie zrobiliście czegoś podobnego dla siebie. to jeden z moich najprostszych i najłatwiejszych projektów, nawet jeśli się kwalifikuje dla mojej najbardziej przydatnej listy projektów. dla in-de
Zbuduj własną gitarę elektryczną!: 8 kroków (ze zdjęciami)
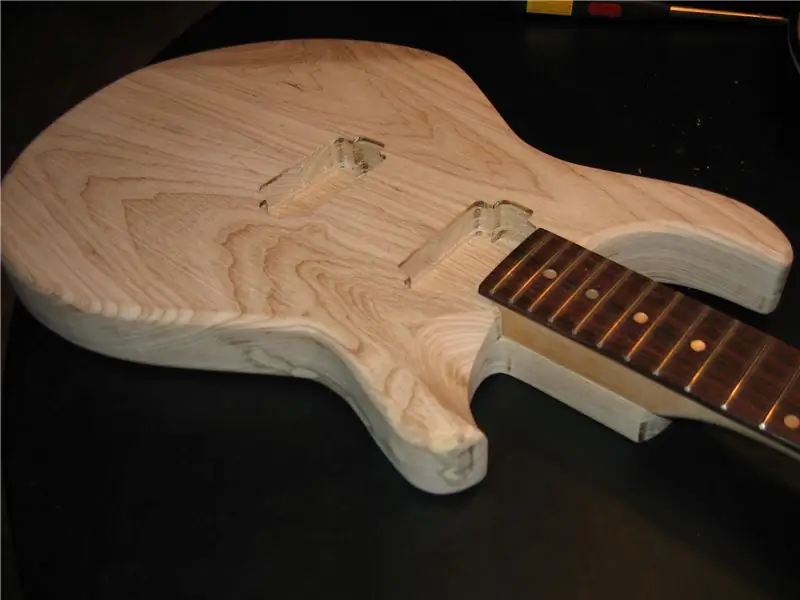
Zbuduj własną gitarę elektryczną!: Czy kiedykolwiek spojrzałeś na gitarę i zastanawiałeś się: „Jak oni to robią?” Albo pomyślałeś sobie: „Założę się, że mógłbym zbudować własną gitarę”, ale nigdy tego nie wypróbowałeś? Zbudowałem kilka gitar elektrycznych na przestrzeni lat i przez próby i er