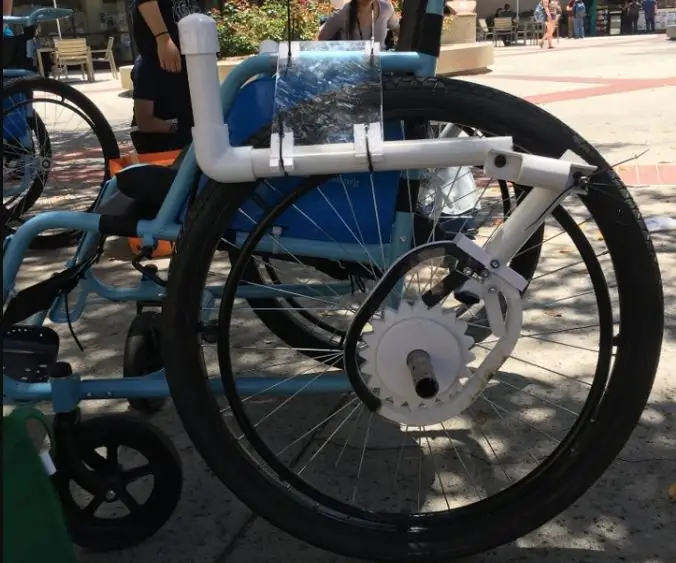
Spisu treści:
- Krok 1: Utwórz zewnętrzną pokrywę obudowy dla korpusu w SolidWorks
- Krok 2: Utwórz bryłę w SolidWorks
- Krok 3: Utwórz połączenie w SolidWorks
- Krok 4: Utwórz ramię/uchwyt dźwigni w SolidWorks
- Krok 5: Utwórz podłokietnik w SolidWorks
- Krok 6: Utwórz koło zębate w SolidWorks
- Krok 7: Utwórz zapadkę w SolidWorks
- Krok 8: Utwórz pokrętło kierunku w SolidWorks
- Krok 9: Utwórz uchwyt do rur
- Krok 10: Rozpocznij złożenie w SolidWorks
- Krok 11: Zamów części od McMaster-Carr
- Krok 12: Uzyskaj części ze sklepu ze sprzętem
- Krok 13: Produkcja części
- Krok 14: Połącz wszystkie części
- Krok 15: Testowanie iteracyjne
- Krok 16: Strona z wkładami
2025 Autor: John Day | [email protected]. Ostatnio zmodyfikowany: 2025-01-23 15:03
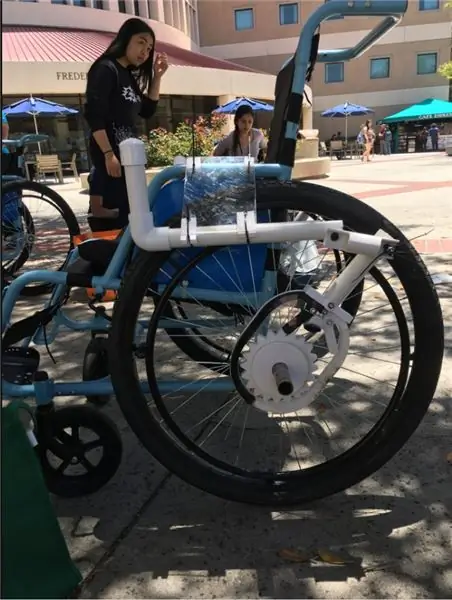
Zwykły wózek inwalidzki ma wiele wad dla osób z osłabieniem kończyn górnych lub ograniczonymi zasobami. Nasz zespół miał za zadanie zaprojektować dźwignię dźwigni do wózków inwalidzkich z misji Free Wheelchair Mission, która pozwoliłaby użytkownikom jechać dalej na krzesłach i pomagać osobom z osłabieniem kończyn górnych w korzystaniu z krzeseł. Sterownik dźwigni wózka inwalidzkiego Support System to ekonomiczne urządzenie, które znacznie zmniejsza potrzebę ruchu ramion i rozwiązuje poziom zmęczenia poprzez zastosowanie dźwigni poziomych zamiast pionowych, co byłoby odpowiednie dla osłabionych pacjentów i pacjentów na obszarach wiejskich. Typowy sterownik pionowego ramienia dźwigni zbyt mocno koncentruje się na mięśniach ramion i barków, co może powodować komplikacje u pacjentów z osłabieniem kończyn górnych. Dlatego nasz zespół zaprojektował poziomy sterownik dźwigni, który miał na celu wykorzystanie mięśni klatki piersiowej, aby ułatwić osobom, które nie mogą wykorzystać mięśni ramion.
Rynek i propozycja wartości
Jako sposób na ból barku i zmęczenie związane z korzystaniem z wózka inwalidzkiego u osób, szczególnie z wiejskich wiosek z nieutwardzonymi drogami, nasz sterownik dźwigni ma na celu złagodzenie problemu, stosując ruch do przodu/do tyłu zamiast ruchu w górę/w dół wraz z ulepszony podłokietnik zapewniający wygodę i wsparcie. Ponieważ wiejskie wsie i nieutwardzone drogi są zwykle bardzo kamieniste i nierówne, pacjent musiałby użyć jeszcze większej siły do ramienia dźwigni, aby przesunąć wózek inwalidzki na pewną odległość w porównaniu z gładką ścieżką. Dlatego osoby z osłabieniem kończyn górnych na obszarach wiejskich są jeszcze bardziej utrudnione, ponieważ potrzebują więcej ruchu i siły, aby przemieszczać się z miejsca na miejsce, co powoduje problemy, ponieważ stale stają się słabsze, ponieważ nadal wykorzystują mięśnie ramion na co dzień. Tak więc, dzięki zastosowaniu poziomego mechanizmu dźwigni, osoby z obszarów wiejskich z osłabionymi kończynami górnymi będą mogły nie tylko swobodnie się poruszać, ale także w sposób, który zmniejszy uciążliwe użycie mięśni ramion, ponieważ zamiast tego używają siły w klatce piersiowej.
Analiza kosztów
Zdecydowaliśmy się na zastosowanie PVC, akrylu i ABS. Był to kompromis siły i kosztów. Te trzy materiały są stosunkowo tańsze, ale wystarczająco mocne, aby prawidłowo funkcjonować. Szacowany koszt to około 170 USD. Pierwotnie planowaliśmy użycie aluminium do większości elementów naszego sterownika dźwigni, takich jak obudowa zewnętrzna i uchwyty ramion, ponieważ aluminium jest tańsze niż stal. Jednak po przeprowadzeniu badań stwierdziliśmy, że stosowanie grubych blach i prętów aluminiowych nie byłoby idealne ze względu na ogromne koszty uzyskania znacznych ilości metalu. Zamiast tego znaleźliśmy tańsze alternatywy, używając różnych materiałów do różnych części. Użyliśmy dużego arkusza akrylowego do zewnętrznej obudowy i pocięliśmy go laserowo na mniejsze części, co wyszło około 25 USD. Dla porównania, duże blachy aluminiowe kosztowałyby ponad 70 dolarów. Ponadto zamiast prętów metalowych zdecydowaliśmy się zastosować rury PVC do uchwytów na ramię, ponieważ rury PVC są nie tylko wytrzymałe, ale również bardzo tanie. Chociaż aluminiowe pręty mogły być mocniejsze, wydalibyśmy około 30 dolarów na każdą stronę wózka. W przeciwieństwie do tego, rury z PVC kosztowały około 5 USD. Większość naszych kosztów pochodzi z drukowania 3D ABS. Ponieważ wydrukowaliśmy trzy części naszego systemu, łączny czas wydrukowania wszystkich tych części wyniósł łącznie około 32 godziny. W rezultacie, przy stawce godzinowej za korzystanie z drukarki 3D, suma wyniosła 130 USD.
Materiały i projektowanie prototypów
- Rura PVC ~ 2,16 USD
- Zaślepka gniazda PCV ~ 1,66 USD
- Kolanko PVC 90 stopni ~ 2,28 $
- Arkusz akrylowy ~ 24,98 USD
- Zębatki ABS, zapadki ABS, gałki ABS ~ $130
- Śruby stalowe ~ 6,92 USD
- Gumki ~ $3,18
- Klej rzemieślniczy E6000 ~ 4,29 USD
Krok 1: Utwórz zewnętrzną pokrywę obudowy dla korpusu w SolidWorks
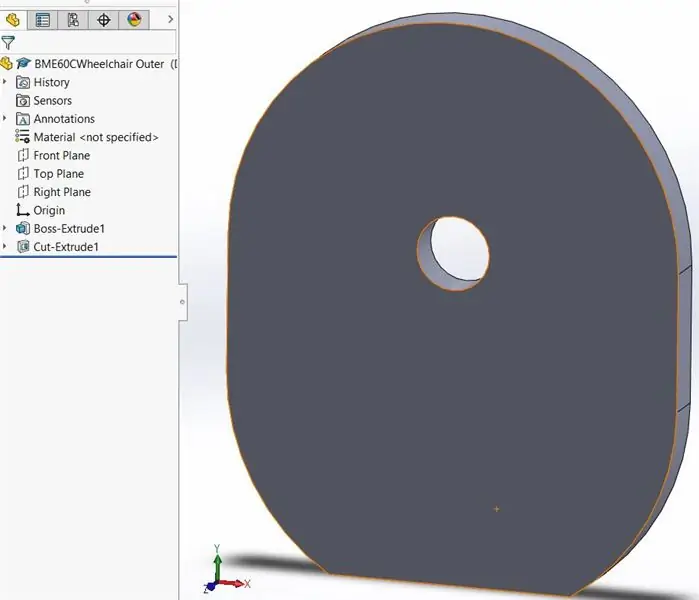
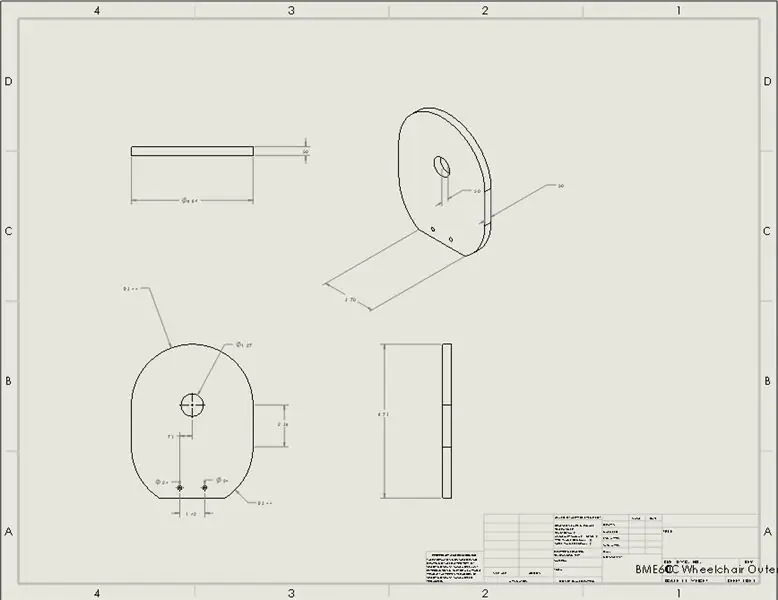
Przed rozpoczęciem całego projektu ustaw wymiary za pomocą MMGS.
Używając płaszczyzny przedniej, utwórz nowy szkic i narysuj okrąg na początku o średnicy 175 mm. Następnie naszkicuj dwie pionowe linie na stycznych okręgu, które mają obie 60 mm. Następnie narysuj łuki styczne na końcu obu linii i połącz je linią poziomą. Następnie, korzystając z funkcji „przytnij elementy”, przytnij dolną połowę okręgu wewnątrz regionu.
Po zakończeniu szkicu, wyciągnij szkic kominka używając ślepego wyciągnięcia o 12,70 mm. Po zakończeniu wyciskania otwórz nowy szkic i narysuj okrąg wyrównujący się z górną częścią linii stycznych o średnicy 32,20 mm i wytnij wyciągnięcie używając „przez wszystko” zrób otwór.
Aby utworzyć dwa dolne okręgi, otwórz nowy szkic i narysuj dwa okręgi o średnicy 6 mm i umieść je 15 mm od dołu i 58,84 mm od środka łuku stycznego. Gdy szkic jest gotowy, użyj wyciągnięcia wycięcia, używając „przez wszystko”, aby zrobić dwa otwory.
Krok 2: Utwórz bryłę w SolidWorks
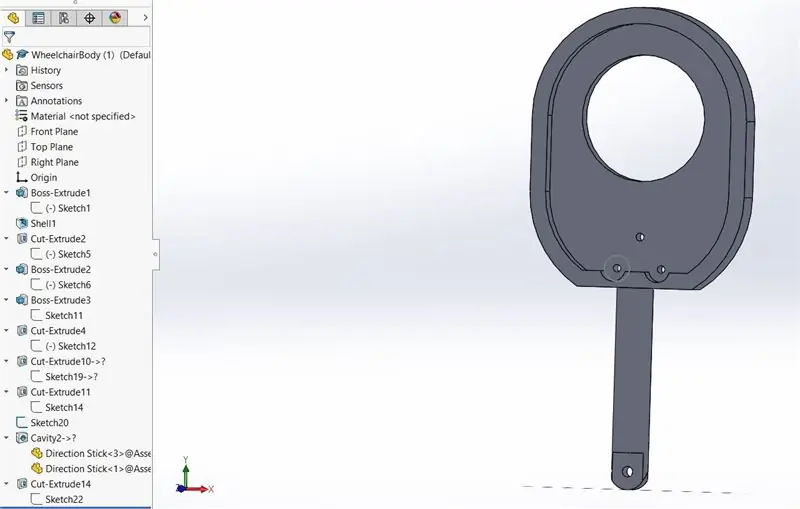
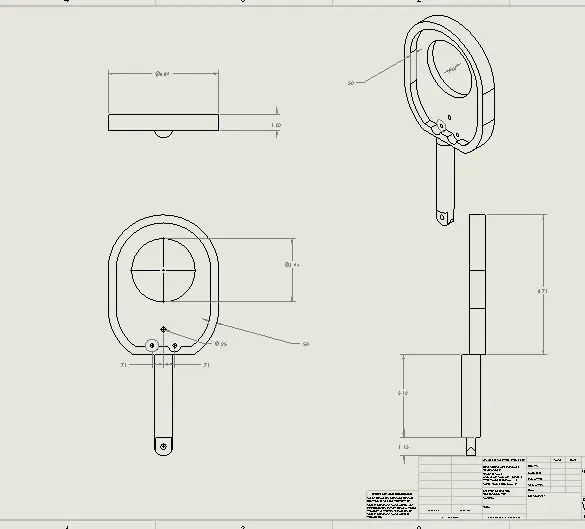
Aby rozpocząć korpus, powtórz szkic jak w części pierwszej, aby utworzyć ogólny kształt korpusu i wyciągnij go 25,40 mm. Po wyciągnięciu części użyj opcji skorupy na jednej z powierzchni części o wymiarze 12,70 mm.
Następnie otwórz nowy szkic i narysuj okrąg w środku części o średnicy 100 mm, czyli 133,84 mm od dołu i 87,50 mm od boków części. Po zakończeniu szkicu wytnij wyciągnięcie, używając ponownie „przez wszystko”, aby utworzyć otwór.
Aby utworzyć dźwignię, utwórz nowy szkic na górnej płaszczyźnie i obróć część w dół. Zacznij szkic od wykonania okręgu o średnicy 28,74 mm u podstawy poprzedniej części i wyciągnij go 130 mm.
Po utworzeniu dźwigni utwórz nowy szkic u podstawy dźwigni. Narysuj dwie poziome linie w równej odległości od początku o długości 25,10 mm. Następnie połącz dwie linie łukami stycznymi o wysokości 14mm. Gdy szkic jest gotowy, ślepo wyciągnij nowy szkic o 30 mm.
Używając najnowszej wyciągniętej części, utwórz nowy szkic na przedniej płaszczyźnie i naszkicuj okrąg oddalony o 14,95 mm od góry i 12,55 mm od boku. Następnie przetnij wytłoczkę przez wszystkie, aby utworzyć otwór.
W całym korpusie naszkicuj dwa otwory na dole korpusu o średnicach 6 mm i odległości 36 mm od siebie, 15 mm od dołu i 58,84 mm od góry łuków stycznych. Następnie wytnij wytłaczanie przez wszystkie, aby utworzyć dwa otwory.
Na dole części utwórz nowy szkic. Zrób proste linie po obu stronach, które mają 14,93 mm. Wykonaj poziomą linię o długości 28,74 mm, aby połączyć dwie linie. Narysuj okrąg o promieniu 14,37 mm i wyrównaj go już z okręgiem w środku. Przytnij go, aby zrobić półkole. Wytnij wytłoczkę przez całą figurę w kształcie rampy na dole części, aby pozostawić zaokrągloną krawędź.
*Aby przygotować się do ubytku, utwórz nowy szkic w tylnej płaszczyźnie. Narysuj okrąg o promieniu 20,57 mm 15 mm od dołu i 58,84 od bocznego łuku stycznego. Po złożeniu wszystkich elementów, edytuj część w zespole i użyj funkcji stempla do utworzenia półokręgów.
Na płaszczyźnie przedniej zrób nowy szkic. Narysuj okrąg pośrodku o średnicy 6,35 mm między dużym okręgiem a dwoma małymi okręgami u dołu. Zrób okrąg 40,13 mm od dołu i 33,70 mm od łuku stycznego po bokach. Następnie wytnij wytłoczkę przez wszystkie, aby utworzyć mały okrąg pośrodku.
*Ten krok należy kontynuować później, po złożeniu wszystkich elementów.
Krok 3: Utwórz połączenie w SolidWorks
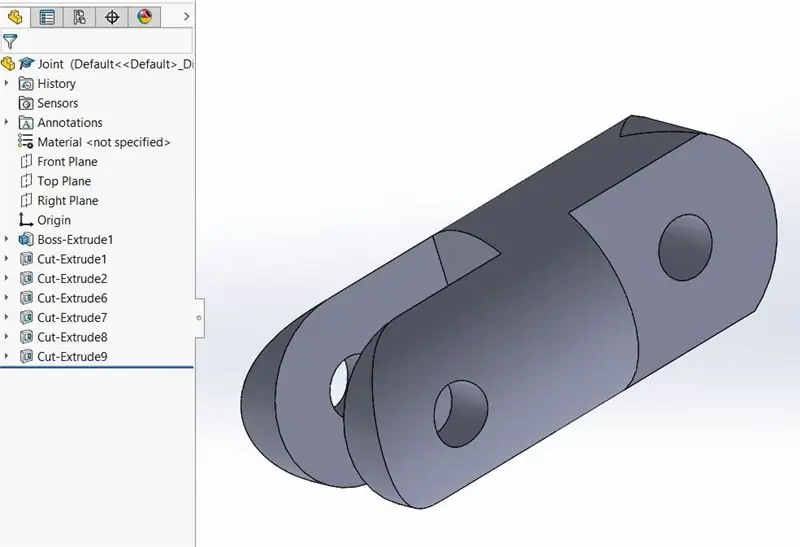
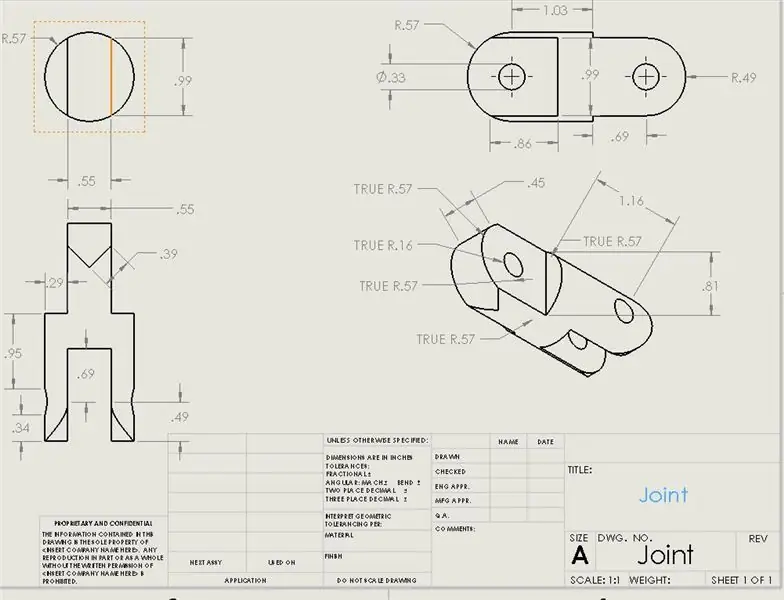
Aby rozpocząć łączenie, zacznij od stworzenia nowego szkicu na płycie czołowej i narysuj okrąg o średnicy 28,74 mm. Ślepy wyciągnij okrąg, który właśnie został naszkicowany, 120 mm.
Następnie obróć część i szkicuj z tyłu. Narysuj dwie pionowe linie o długości 25,10 mm i 7,37 mm od krawędzi okręgu. i wytnij wytłoczkę za pomocą "ślepego" i głębokości 30mm dla obu regionów.
Następnie, patrząc z prawej płaszczyzny, naszkicuj okrąg na obszarze, który właśnie wycięliśmy. Średnica powinna wynosić 8,38 mm z odległością 12,55 mm od górnej krawędzi i 14,95 mm od krawędzi bocznej. Wykonaj cięcie na ślepo, które ma 30 mm.
Na prawej płaszczyźnie zrób proste linie po obu stronach o długości 15,05 mm. Wykonaj pionową linię o długości 28,74 mm, aby połączyć dwie linie. Narysuj okrąg o promieniu 14,37 mm i wyrównaj go już z okręgiem w środku. Przytnij go, aby zrobić półkole. Wytnij wytłoczkę przez całą figurę w kształcie rampy na dole części, aby pozostawić zaokrągloną krawędź.
Następnie, patrząc od tylnej płaszczyzny, naszkicuj dwie pionowe linie o długości 25,10 mm i 7 mm od środka. Wykonać cięcie na ślepo o głębokości 35mm.
Na prawej płaszczyźnie naszkicuj okrąg po prawej stronie ze środkiem oddalonym o 17,24 mm od lewej krawędzi części, wytnij ślepo przez wszystko, aby utworzyć okrąg
Na prawej płaszczyźnie powtórz figurę w kształcie rampy po lewej stronie części.
Krok 4: Utwórz ramię/uchwyt dźwigni w SolidWorks
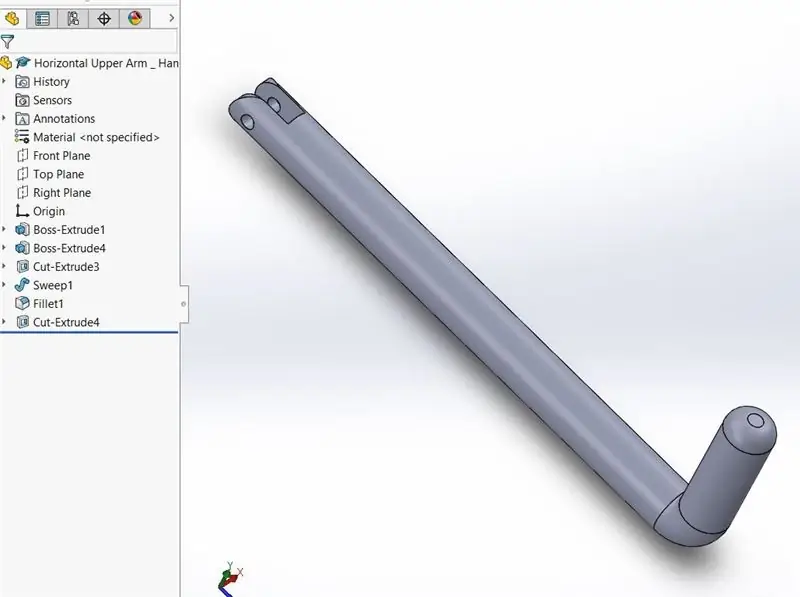
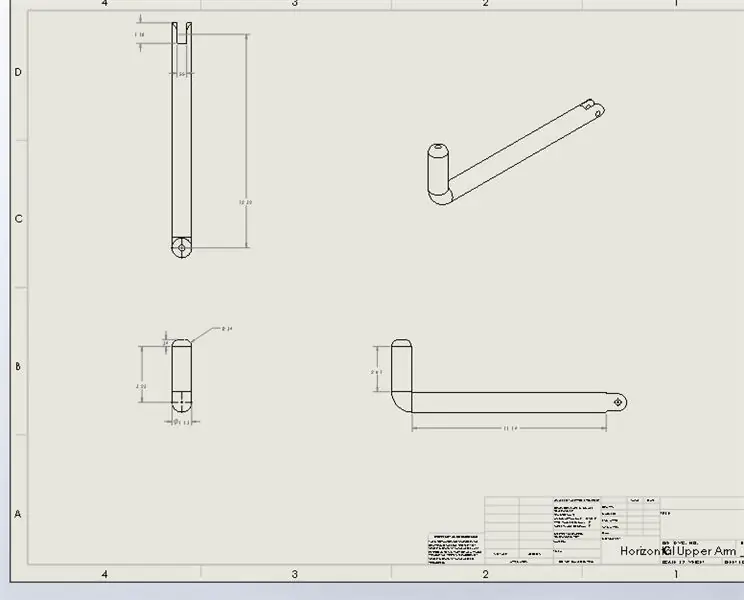
Na płaszczyźnie przedniej naszkicuj okrąg o średnicy 28,75 mm w punkcie początkowym. Boss wyciągnij go 275mm.
Następnie przejdź do tylnej płaszczyzny i naszkicuj dwie pionowe linie o długości 25,10 mm w odległości 7 mm od środka. Wyciągnij dwie linie tak, aby pośrodku była szczelina o wymiarze wyciągnięcia 35 mm.
Na części, którą właśnie wytłoczyliśmy, naszkicuj okrąg o średnicy 8,40 mm w odległości 17,76 mm od środka okręgu do krawędzi i 12,56 mm od dołu części. Wytnij wytłoczkę przez wszystkie, aby utworzyć otwór.
Na prawej płaszczyźnie utwórz krótką linię o długości 9,24 mm, która łączy się z lewą stroną części. Narysuj łuk o promieniu 30 mm. Następnie narysuj pionową linię łączącą drugi koniec łuku o długości 76,39 mm. Po zakończeniu szkicu przeciągnij szkic.
Następnie filetujemy górną część części, którą właśnie przesunęliśmy o 10 mm.
Na koniec, na prawej płaszczyźnie, wykonaj proste poziome linie po obu stronach części z utworzonym przez nas otworem o długości 17,78 mm. Wykonaj pionową linię o długości 25,10 mm, aby połączyć dwie linie. Narysuj okrąg o promieniu 12,56 mm i wyrównaj go już z okręgiem w środku. Przytnij go, aby zrobić półkole. Wytnij wytłoczkę przez całą figurę w kształcie rampy na dole części, aby pozostawić zaokrągloną krawędź.
Krok 5: Utwórz podłokietnik w SolidWorks
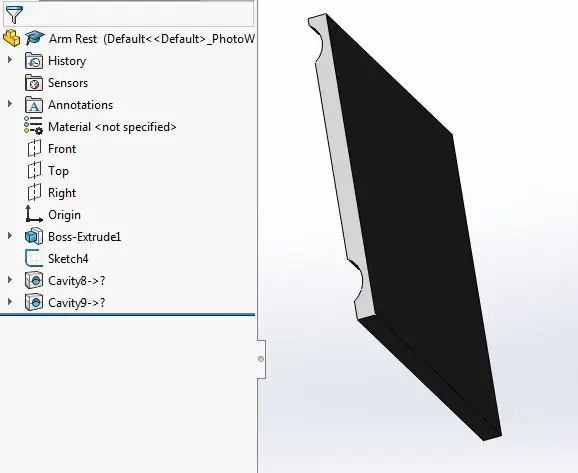
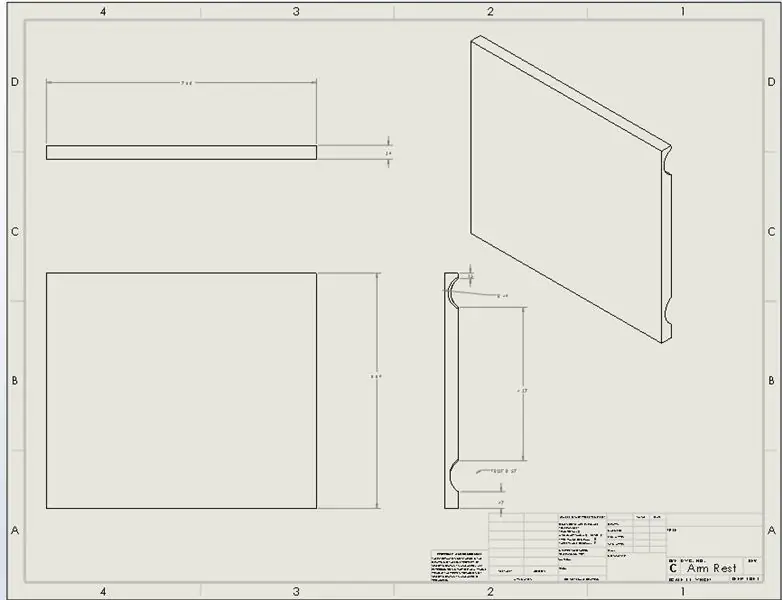
Na płaszczyźnie czołowej naszkicuj prostokąt o wysokości 170mm i długości 195mm i wykonaj profil ślepy 10mm.
*Po złożeniu użyj funkcji wnęki, aby utworzyć wcięcia na pryzmacie prostokątnym
Krok 6: Utwórz koło zębate w SolidWorks
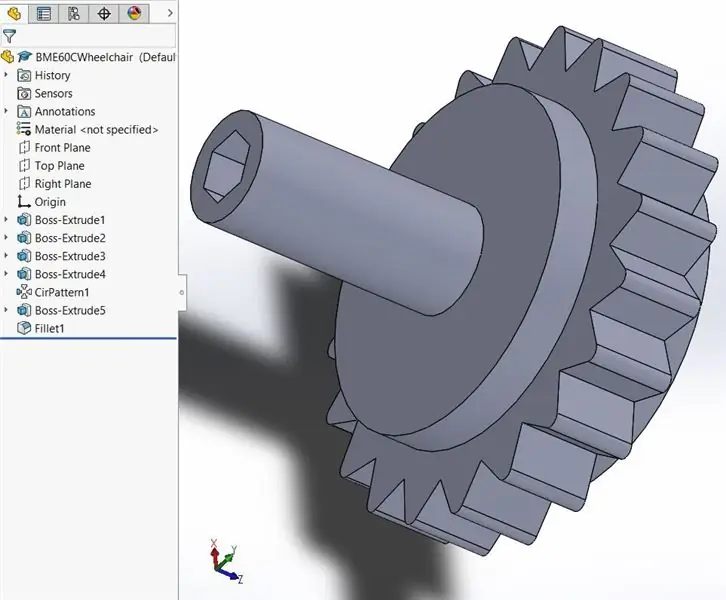
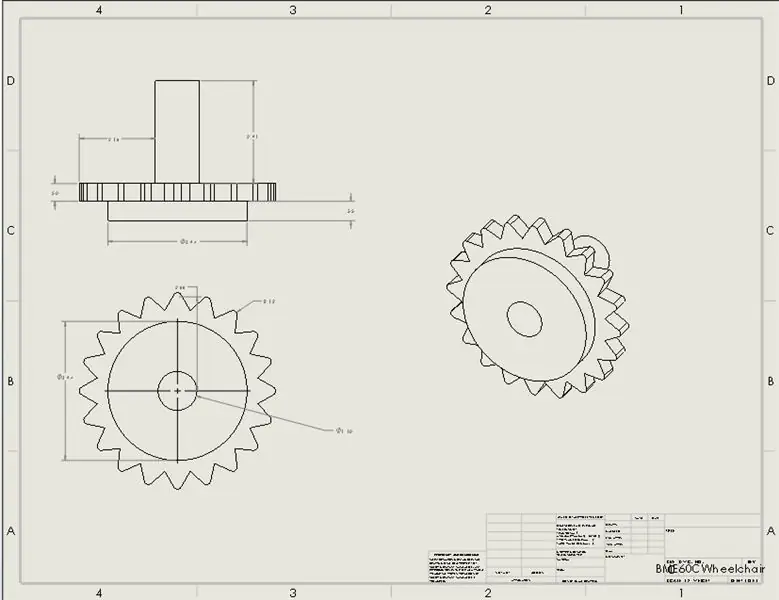
Aby rozpocząć koło zębate, utwórz nowy szkic na przedniej płaszczyźnie i narysuj dwa okręgi z tego samego punktu o średnicach 25,40 mm i 31,75 mm. Następnie wyciągnij występ przy użyciu ślepego wyciągnięcia na 30 mm.
Po zakończeniu wyciskania utwórz kolejny szkic na przedniej płaszczyźnie i narysuj kolejny okrąg o średnicy 31,75 mm i wyciągnij 20 mm.
Następnie naszkicuj na przedniej płaszczyźnie okrąg o średnicy 100mm i wyciągnij go 12,70mm.
Na wierzchu części, którą właśnie wycięliśmy, narysuj trójkąt równoboczny o bokach 30 mm. Wyciągnij trójkąt 12,70 mm.
Po zakończeniu wyciskania użyj funkcji szyku kołowego, aby uzyskać 20 jednolitych trójkątów wokół części. Następnie zaokrąglij wszystkie krawędzie trójkątów.
Na płaszczyźnie przedniej naszkicuj kolejny okrąg o średnicy 100 mm i wyciągnij go 13,97 mm.
Aby utworzyć otwór w środku koła zębatego, naszkicuj okrąg na tylnej płaszczyźnie o średnicy 27,94 mm i wytnij wyciągnięcie do powierzchni.
Krok 7: Utwórz zapadkę w SolidWorks
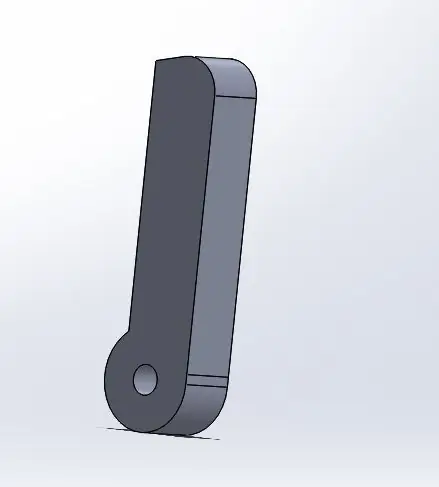
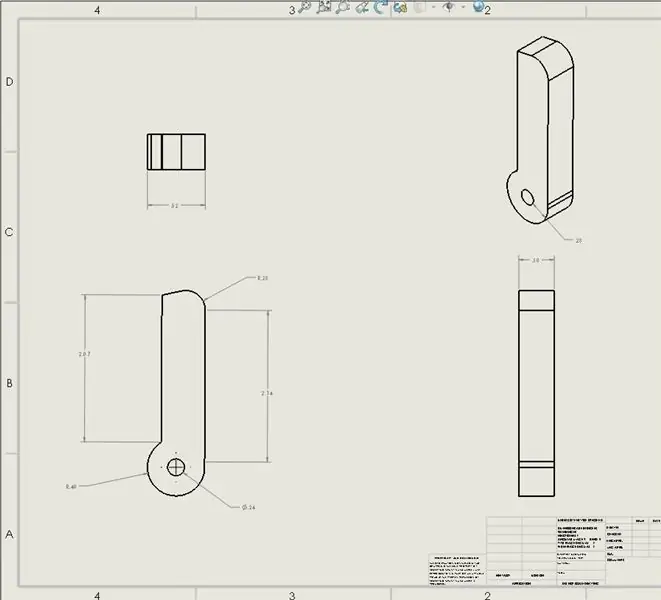
Na płaszczyźnie przedniej narysuj pionową linię o długości 2,07 cala. Następnie narysuj łuk o promieniu 0,40 cala łączący się z dolną częścią pionowej linii. Narysuj również poziomą linię połączoną z górną krawędzią linii pionowej. Używając inteligentnych wymiarów, kliknij górną krawędź, a następnie linię pionową i ustaw kąt na 78,00 stopni.
Po ustawieniu kąta narysuj kolejną pionową linię, która łączy się z linią ukośną o długości 2,14 cala. Następnie zaokrąglij krawędź tej linii linią poziomą o promieniu 0,28 cala.
Gdy szkic jest gotowy, wyciągnij kominek używając ślepego wyciągnięcia 0,5 cala. Aby utworzyć otwór w środku, naszkicuj okrąg o promieniu 0,12 cala w środku części i użyj wycięcia wyciągnięcia przez wszystko.
Krok 8: Utwórz pokrętło kierunku w SolidWorks
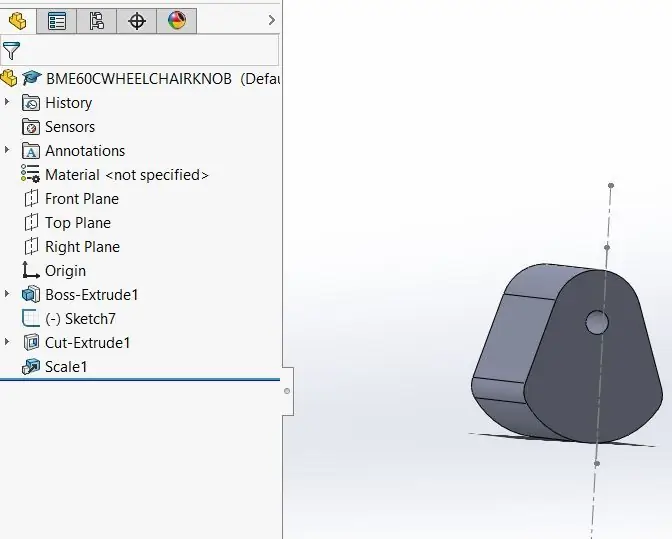
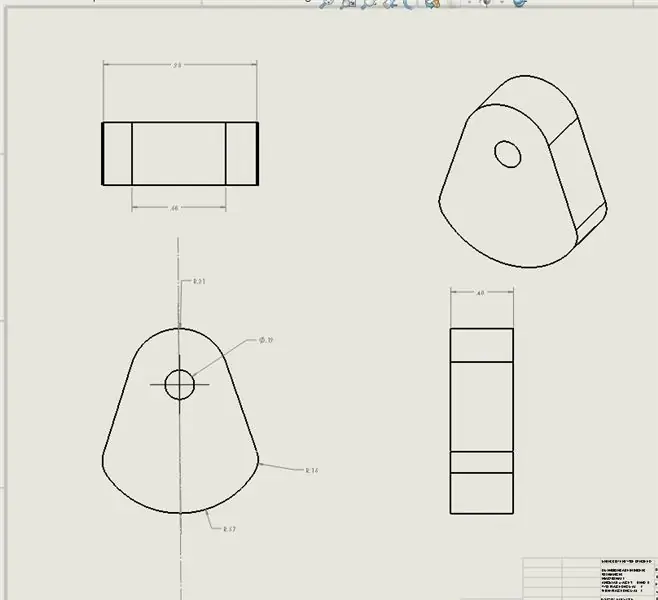
Na płaszczyźnie przedniej naszkicuj pionową linię środkową. Następnie u góry linii środkowej naszkicuj łuk o promieniu 10 mm. Następnie po obu stronach narysuj skośne linie o długości 18,26mm. Następnie narysuj łuk po obu stronach o promieniu 5 mm. Aby połączyć obie strony, narysuj kolejny łuk o promieniu 18mm. Wyciągnij szkic używając ślepego wyciągnięcia 12,70 mm.
Aby utworzyć otwór, naszkicuj okrąg o średnicy 5,90 mm, którego środek znajduje się 8 mm od początku. Użyj wycięcia wyciągnięcia do powierzchni.
Skaluj część wokół środka ciężkości ze współczynnikiem skali 0,8 mm.
Krok 9: Utwórz uchwyt do rur
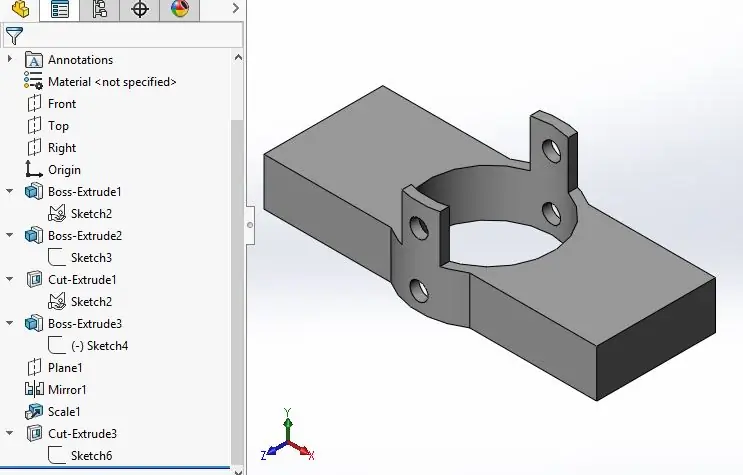
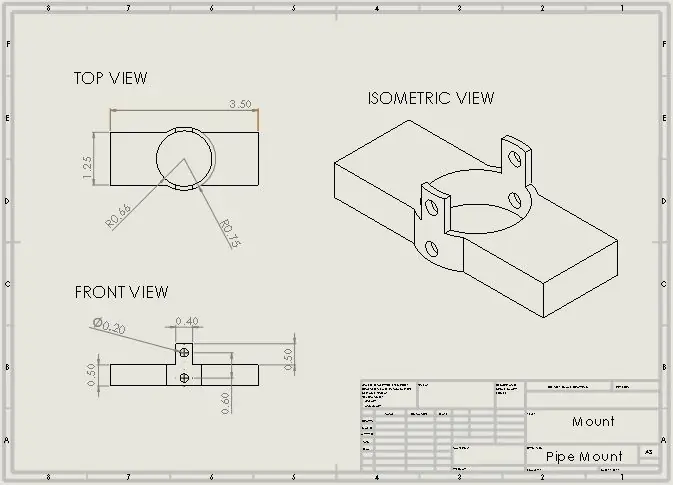
Aby stworzyć uchwyt do rur, który przymocuje ramię dźwigni do korpusu przekładni, zacznij od szkicu dwóch okręgów. Wewnętrzny okrąg powinien mieć średnicę rury PVC, aby mógł się łatwo przesuwać wokół niego, dlatego powinien wynosić 1,3125 cala. Zewnętrzny okrąg powinien mieć około 1,5 cala. Upewnij się, że dwa okręgi są koncentryczne i wyciągnij część między dwoma okręgami o 0,5 cala. Następnie naszkicuj prostokąt, który pasuje do dolnej powierzchni zewnętrznej obudowy koła zębatego. Byłby to prostokąt o wymiarach 3,5 cala na 1,25 cala. Wyśrodkuj prostokąt wokół okręgu, ustawiając dłuższą krawędź prostokąta w odległości 1,75 cala od środka okręgu, a krótszą krawędź prostokąta w odległości 0,63 cala od środka okręgu. Wyciągnij prostokąt o 0,5 cala. Ponieważ niektóre części prostokąta leżą w wewnętrznym okręgu, wytnij i wyciągnij wewnętrzny okrąg, aby go wyczyścić. Następnie, od górnej płaszczyzny części, naszkicuj linię środkową od okręgu do zewnętrznej części wyciągniętej krawędzi. Od tego punktu środkowego na wyciągniętej krawędzi, naszkicuj prostokąt, który rozciąga się na 0,2 cala w obie strony. Wyciągnij ten mały prostokąt o 0,5 cala. Utwórz skierowaną do przodu płaszczyznę odniesienia przechodzącą przez środek części i użyj funkcji lustra, aby utworzyć identyczny wyciągnięty prostokąt po drugiej stronie okręgu.
Podczas drukowania części 3D zawsze dobrze jest przeskalować wszystko nieco w górę, aby uniknąć zakłóceń podczas umieszczania części na zespole. W tym przypadku cała część została przeskalowana o 1,05. Na koniec naszkicuj dwa okręgi o średnicy 1/4 cala ustawione na przedniej powierzchni środka części z jednym na małym prostokącie i jednym z boku okręgu. Upewniając się, że dwa koła są ze sobą powiązane w pionie, można je następnie przeciąć przez całą część, wycinając w sumie cztery koła. Są to otwory, w które można umieścić śruby, aby połączyć PVC z głównym korpusem obudowy przekładni.
Krok 10: Rozpocznij złożenie w SolidWorks
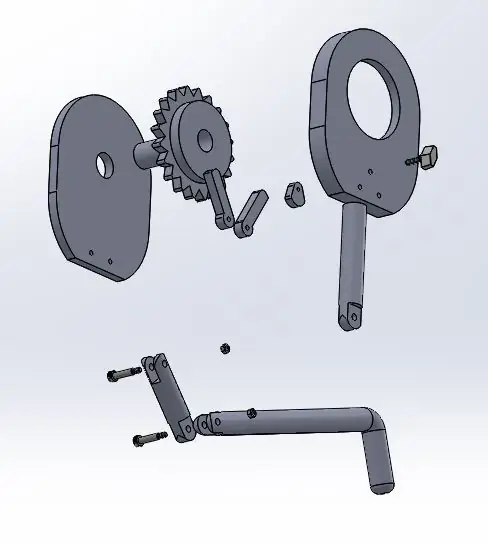
Najpierw włóż wszystkie części, które zostały utworzone w poprzednich krokach, wraz z dostępnym pokrętłem zewnętrznym, śrubami i nakrętkami, dzięki czemu korpus wózka inwalidzkiego stanie się elementem podstawowym.
Zacznij od połączenia korpusu i koła zębatego, klikając krawędź koła zębatego i krawędź korpusu i użyj wiązania koncentrycznego. Następnie kliknij powierzchnię koła zębatego i bryłę, aby utworzyć wspólne wiązanie.
Następnie sparuj korpus i pokrętło kierunkowe, klikając powierzchnię pokrętła kierunkowego i korpus, aby utworzyć wspólne wiązanie.
Teraz połącz zewnętrzne pokrętło i korpus wózka inwalidzkiego, klikając zarówno powierzchnię zewnętrznego pokrętła, jak i korpus, aby utworzyć wspólne wiązanie.
Utwórz wiązanie koncentryczne, klikając lico korpusu i lico zewnętrznego pokrętła.
Następnie wykonaj wiązanie koncentryczne, klikając powierzchnię pokrętła kierunkowego i krawędź korpusu.
Teraz kliknij powierzchnie ciała i zapadki, aby utworzyć wspólne wiązanie i powtórz dla drugiej zapadki.
Utwórz wiązanie styczne, klikając powierzchnię pokrętła kierunku i zapadki, a następnie powtórz dla drugiej zapadki.
Następnie utwórz wiązanie pokrywające się, klikając lico bryły i zewnętrznej obudowy, a następnie utwórz wiązanie koncentryczne, klikając lico bryły i krawędź obudowy zewnętrznej. Następnie ustaw równolegle powierzchnię korpusu i powierzchnię zewnętrznej obudowy.
Utwórz kąt graniczny, który ma maksymalną wartość 78 stopni i minimalną wartość 35 stopni dla powierzchni ciała i powierzchni zapadki i powtórz dla drugiej zapadki
Następnie połącz staw i ciało, klikając powierzchnię obu, aby utworzyć koncentryczne wiązanie. Następnie utwórz wyśrodkowane wiązanie szerokości dla obu powierzchni stawu i korpusu.
Następnie utwórz wiązanie koncentryczne dla krawędzi ramienia dźwigni i krawędzi połączenia. Utwórz kolejne wyśrodkowane wiązanie szerokości dla obu powierzchni połączenia i ramienia dźwigni.
Wykonaj kolejne wiązanie koncentryczne dla powierzchni złącza i śruby. Następnie utwórz wiązanie styczne, klikając powierzchnię połączenia i powierzchnię śruby.
Na prawej płaszczyźnie naszkicuj dwie linie osi dla przyszłego odniesienia do łączenia, przy czym pierwsza linia to miejsce, w którym korpus styka się ze złączem, a druga to miejsce, w którym złącze styka się z ramieniem dźwigni.
Następnie utwórz wiązanie koncentryczne, klikając powierzchnię ramienia dźwigni i drugą śrubę. Po wiązaniu utwórz kolejne wiązanie styczne z obydwoma powierzchniami obu komponentów.
Przy wcześniej narysowanej pierwszej osi, połącz krawędź pierwszej nakrętki i oś, aby utworzyć wiązanie koncentryczne.
Użyj wspólnego wiązania dla powierzchni pierwszej śruby i pierwszej nakrętki i powtórz dla drugiej śruby i nakrętki.
Wykonaj wiązanie koncentryczne z krawędzią drugiej nakrętki i drugiej osi.
Utwórz kolejne wiązanie koncentryczne z powierzchnią korpusu i zewnętrzną powierzchnią pierwszej śruby. Dodatkowo stwórz wiązanie przypadkowe dla tych części.
Wykonaj wiązanie koncentryczne dla czoła zapadki i zewnętrznej powierzchni trzeciej śruby.
Utwórz wspólne wiązanie z powierzchnią korpusu i zewnętrzną powierzchnią trzeciej śruby.
Następnie utwórz kolejne wiązanie koncentryczne, klikając powierzchnię zewnętrznej obudowy i zewnętrzną powierzchnię trzeciej śruby i ustaw je na siebie.
Wykonaj koncentryczne wiązanie, klikając lico ciała i lico zapadki, tak aby były zbieżne. Powtórz dla drugiej zapadki.
Wykonaj wiązanie koncentryczne, klikając powierzchnię pokrętła kierunkowego i zewnętrznego pokrętła.
Na koniec połącz powierzchnię korpusu i krawędź pokrętła kierunkowego, aby utworzyć wiązanie koncentryczne.
Krok 11: Zamów części od McMaster-Carr
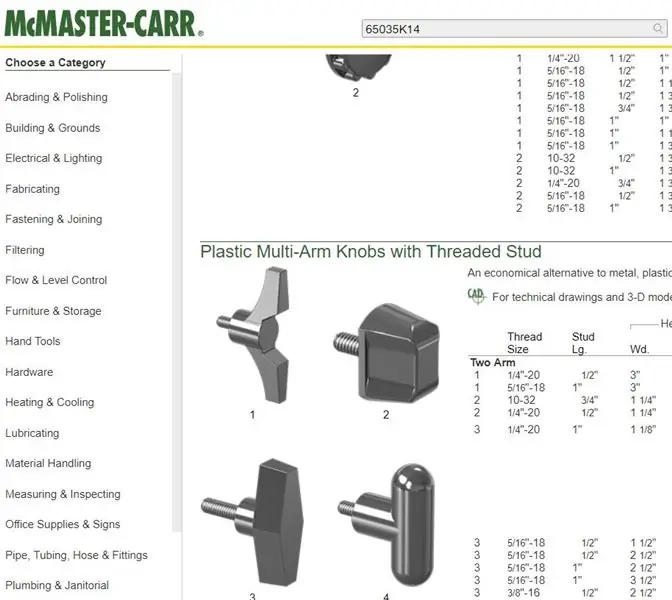
Zamów plastikowe dwuramienne pokrętło (pokrętło zewnętrzne), śrubę ze stali stopowej, stalowe nakrętki sześciokątne i opaski kablowe w firmie McMaster-Carr. Numery pozycji to odpowiednio 65035K14, 92981A205, 90592A016 i 70215K61.
Krok 12: Uzyskaj części ze sklepu ze sprzętem
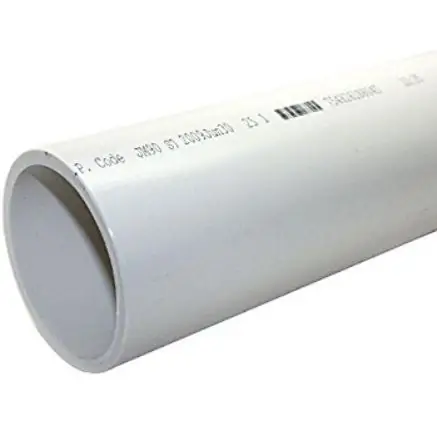
W lokalnym sklepie ze sprzętem uzyskaj następujące informacje:
-18 "x 24" x.220 "Arkusz akrylowy)
- przezroczysty klej (klej E6000)
- Zaślepka gniazda PCV 1 (2)
- Rura z gładkiego końca PCV o wymiarach 1 "x 10";
- Kolanko 1 PVC 90 stopni (2)
Krok 13: Produkcja części
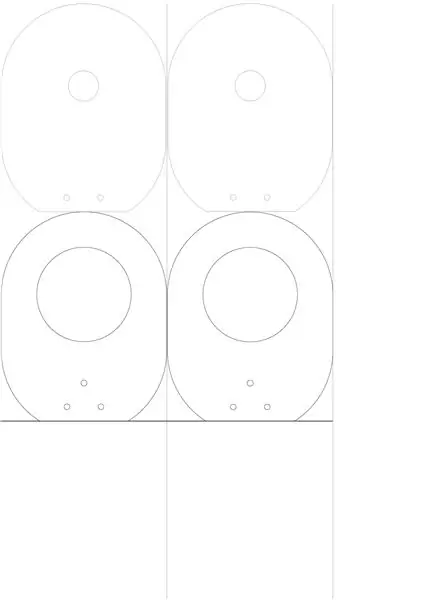
Części drukowane 3D: Przygotuj części SolidWorks i przekonwertuj je na pliki STL. Stamtąd umieść części w oprogramowaniu Makerware i ułóż części, które mają zostać wydrukowane (skorupa korpusu, koła zębate, element montażowy, zapadki, pokrętło kierunku, wgłębienia podłokietnika*). Jeśli części nie mieszczą się na stole drukarki, poczekaj na ponowne wydrukowanie. Podczas drukowania pamiętaj, aby dodać podpory i tratwy, aby zapobiec uszkodzeniu wydruków.
Części wycinane laserowo: Przy użyciu akrylu o wymiarach 18 na 24 cale można wyprodukować przednią i tylną płytę zewnętrznej obudowy korpusu. Można to zrobić, biorąc przednie powierzchnie obu płyt w SolidWorks i zapisując je jako plik DWG. Można je następnie przesłać do oprogramowania do cięcia laserowego (w tym przypadku Epilog), w którym można ustawić ich orientację, jak pokazano na obrazie. Z akrylu wycięte zostaną dwa z każdego, a z pozostałego materiału wycięte zostaną dwa prostokąty. Prostokąty posłużą jako podłokietniki.
Części cięte ręcznie: Weź rury i pokrój je na różne długości (dwie po 4,5 cala na rączkę, dwie po 4,5 cala na złącze, dwie po 6,5 cala na dźwignię i dwie po 13,25 cala na ramię). Stamtąd wytnij części ramienia 13,25 cala na jednym końcu (30 lub 35 mm) w środku drugiej strony rury i wywierć otwór 1/4 15 mm od krawędzi rury. Wytnij i wywierć dwa Złącza 4,5 cala w ten sam sposób, ale po obu stronach złącza rury PVC. Zrób to samo (wytnij i wywierć) z jednej strony ramienia dźwigni, rury 6,5 cala.
*Można użyć nacięć podłokietnika lub całego podłokietnika z poprzedniego kroku.
Krok 14: Połącz wszystkie części
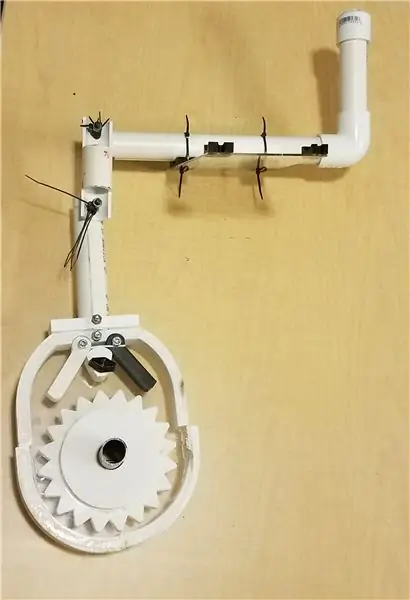
Montaż korpusu:
Weź wycięte laserowo zewnętrzne części ciała i wydrukowane w 3D kawałki skorupy. Weź jedną stronę pancerza i przyklej elementy skorupy odpowiednio do krawędzi pancerza. Następnie weź gumkę i owiń ją wokół dwóch zapadek. Umieść zapadki w odpowiednich miejscach i użyj częściowo gwintowanej śruby i przełóż ją przez otwór korpusu i zapadki. Następnie weź pokrętło kierunkowe i plastikowe pokrętło. Przełóż plastikowe pokrętło przez pancerz i skręć je razem z pancerzem pomiędzy nimi. Na koniec umieść koło zębate w odpowiednim otworze i załóż górną pokrywę pancerza na koło zębate i przyklej skorupę do górnej części pancerza. Niech siedzą i wyschną. Pamiętaj, aby po założeniu i przyklejeniu górnej pokrywy do skorupy zabezpieczyć również dwie częściowo gwintowane śruby nakrętkami sześciokątnymi.
Weź 6,5-calową dźwigniową rurę PVC i przyklej ją do dolnej powierzchni korpusu. Stamtąd pozwól mu usiąść i wyschnąć. Weź zamontowany element i przesuń go przez rurę, aż ułoży się płasko na dolnej powierzchni korpusu. Weź wiertło 1/4 cala i wywierć otwory na rurze i przez korpus w odpowiednich miejscach. Zabezpiecz śruby nakrętką sześciokątną.
Montaż podłokietnika:
Za pomocą podłokietnika po prostu umieść i przyklej nacięcia w 4 rogach podłokietnika. Następnie wywierć dwa otwory (otwory 5/32'') po każdej stronie nacięć i przełóż przez nie opaski. Większe nacięcia można następnie wyrównać i przymocować do ramienia dźwigni 13-calowej rury PVC. Mniejsze wcięcie należy wyrównać, a następnie przymocować do ramienia wózka przed użyciem.
Montaż ramienia dźwigni:
Umieść nasadkę na rurze uchwytu 4,5 cala i umieść kolano bezpiecznie po drugiej stronie. Przy drugim otworze kolanka umieść 13-calową rurę ramienia i połącz ją z jedną stroną złącza (rura 4,5 cala) za pomocą śruby pasowanej. Po drugiej stronie złącza weź kolejną śrubę pasowaną i połącz ją z elementem ramienia dźwigni (rurka 6,5 cala). Weź nakrętkę sześciokątną i zabezpiecz śrubę pasowaną. Ponieważ śruby pasowane są częściowo gwintowane, połączenia, w których są mocowane, mogą być cienkie. Aby połączenia były bardziej ciasne i bezpieczne, umieść około pięciu zamków wokół każdej śruby barkowej, aby dokręcić każde połączenie.
Krok 15: Testowanie iteracyjne
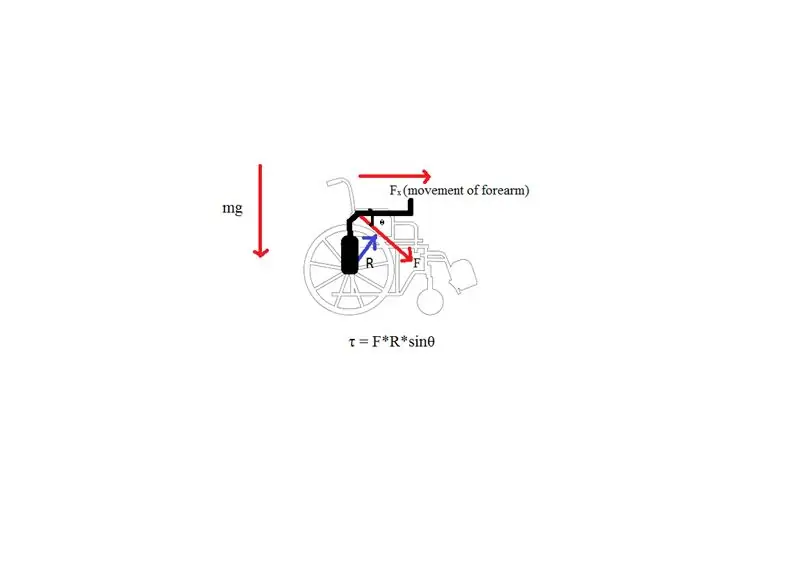
Aby przetestować, upewnij się, że masz dostęp do jednego z wózków inwalidzkich.
Przymocuj ramię dźwigni do koła. Upewnij się, że części pasują tam, gdzie powinny być, i upewnij się, że niektóre części są równoległe do odpowiednich części wózka inwalidzkiego, na przykład podłokietnik. Upewnij się, że otwory wywiercone w aluminiowej rurze i korpusie ramienia dźwigni są wyrównane. Jeśli części są nieproporcjonalne, wróć i dokonaj pewnych zmian wymiarów.
Gdy wymiary i relacje są prawidłowe, niech tester usiądzie na wózku inwalidzkim i użyje ramienia dźwigni. Jak pokazano na schemacie swobodnego ciała, tester przesunie się poziomo do przodu, aby wytworzyć siłę ukośną, która zostałaby wykorzystana do wytworzenia momentu obrotowego i napędzania wózka do przodu. Przeanalizuj wszelkie problemy: niestabilność połączenia, nadmiar lub brak przestrzeni poziomej, pękanie części itp.
Przeanalizuj problemy i ponownie zaprojektuj.
W naszym prototypie wózek poruszał się, ale w wolnym tempie. Część ciała nie skończyła sklejać na czas, więc ramię dźwigni pękło podczas naszego testu. Ponadto złącze mogło być zbyt duże i luźne, a także może nie być wystarczającej przestrzeni poziomej i ruchu na ramieniu dźwigni, co ogranicza siłę wywieraną na naciśnięcie.
Krok 16: Strona z wkładami
Indywidualne składki na system wsparcia
Kierownik projektu: Sophia Ynami 12732132
- Kierownik projektu, Sophia Ynami, była odpowiedzialna za dopilnowanie, aby każdy członek grupy został pociągnięty do odpowiedzialności za swoje obowiązki i że wszystkie zadania zostały wykonane na czas. Pomagałem w końcowym procesie montażu oraz testowałem i wprowadzałem poprawki do urządzenia przed ostatecznym uruchomieniem.
Producent: Yvonne Szeto 94326050
- Producent Yvonne Szeto był odpowiedzialny za przygotowanie poszczególnych komponentów do montażu. Byłem odpowiedzialny za uzyskanie surowców laserowo wycinanych, wierconych i drukowanych w 3D różnych części. Złożyłem też ze sobą różne komponenty.
Inżynier materiałowy: Willis Lao 15649487
- Inżynier materiałowy, Willis Lao, był odpowiedzialny za podjęcie decyzji, jakich materiałów użyć do każdego elementu projektu i zamówienie/odbiór ich w McMaster Carr/Home Depot. Przyczyniłem się również do tworzenia Instructables, pisząc wstęp, analizę kosztów, krok po kroku proces tworzenia części i montaż.
Tester: Mateusz Maravilla 25352925
- Tester, Matthew Maravilla, był odpowiedzialny za nadzorowanie i analizę iteracyjnej metody testowania, w tym testowanie ramienia dźwigni i wymiaru raportowania lub zmian części, które należy dostosować. Byłem również odpowiedzialny za zarys i większość instrukcji.
Główny projektant: Anthony Cheuk 30511803
- Główny projektant, Anthony Cheuk, był odpowiedzialny za opracowanie wykonalnego projektu z uwzględnieniem różnych materiałów, które mogą być użyte, oraz przygotowanie plików i projektu gotowego do produkcji (druk 3D i cięcie laserowe).
Zalecana:
Zagłówek wózka inwalidzkiego: 17 kroków
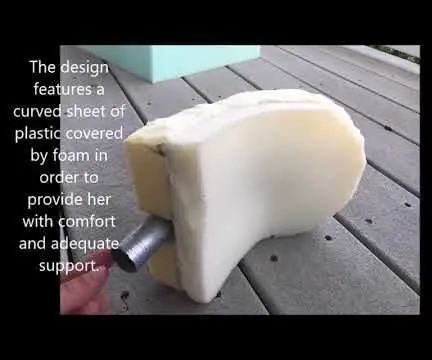
Zagłówek wózka inwalidzkiego: wprowadzenie Osoba w Seven Hills ma problemy z zagłówkiem wózka inwalidzkiego. W okresach dużego niepokoju i stresu miewa konwulsje spastyczne. Podczas tych epizodów jej głowę można opchnąć wokół boku i dołu zagłówka. Ta pozycja
Kamera cofania do elektrycznego wózka inwalidzkiego: 10 kroków (ze zdjęciami)
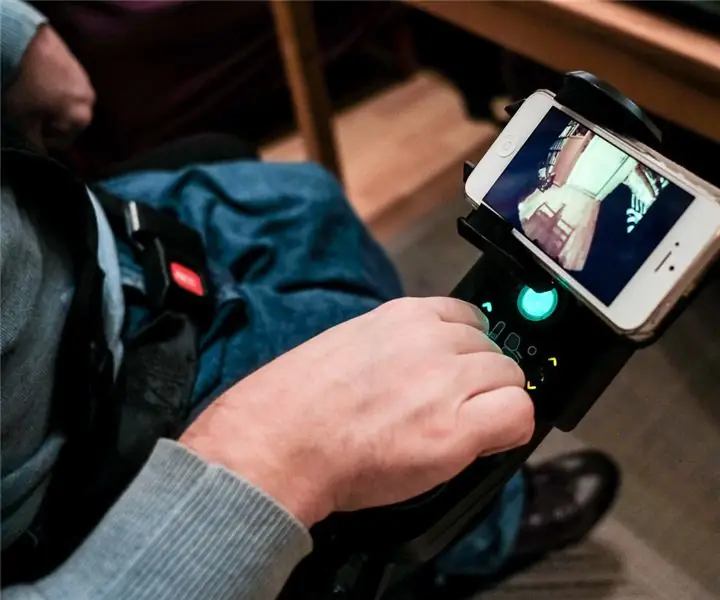
Kamera cofania do elektrycznego wózka inwalidzkiego: Mój brat używa elektrycznego wózka inwalidzkiego Invacare TDX, którym łatwo manewrować we wszystkich kierunkach, ale z powodu ograniczonej widoczności do tyłu trudno jest jechać do tyłu w ograniczonej przestrzeni. Celem projektu jest zbudowanie kamery cofania
Podświetlenie wózka inwalidzkiego: 9 kroków (ze zdjęciami)
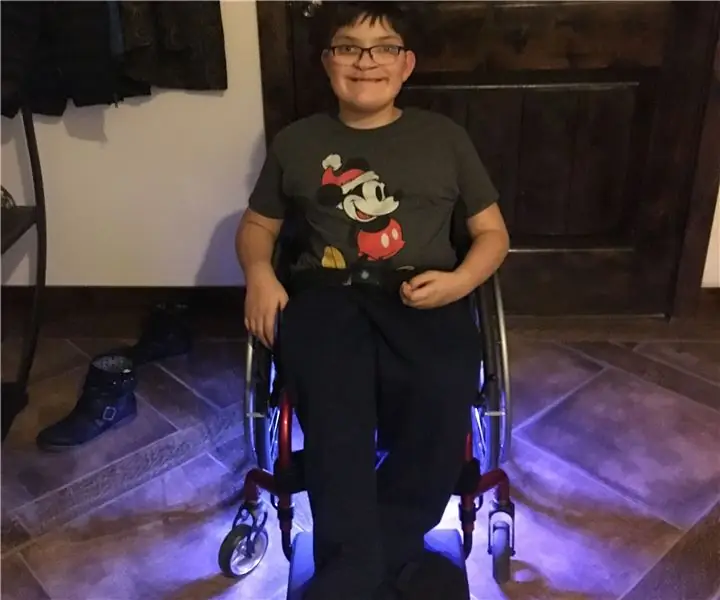
Podświetlenie wózka inwalidzkiego: Po pierwsze, zgłosiłem ten Instruktaż do kilku konkursów. Będę wdzięczny za głosowanie, jeśli uważasz, że zasługuje na jeden lub dwa. Kontynuuj program: Siedzę więc na rodzinnym przyjęciu bożonarodzeniowym i pytam mojego siostrzeńca (który jest zagorzałym fanem BYU), dlaczego jego w
Usuń hamulec silnika wózka inwalidzkiego: 6 kroków (ze zdjęciami)
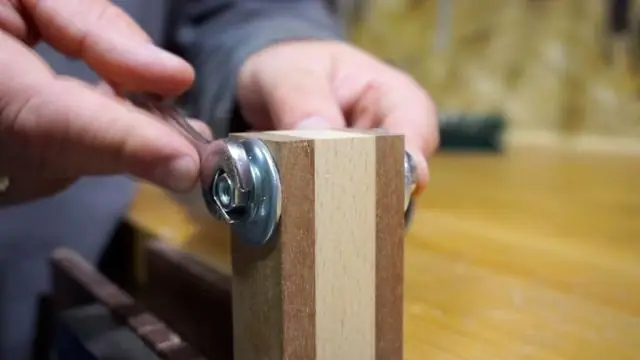
Usuń hamulec silnika wózka inwalidzkiego: Usunięcie elektrycznego hamulca bezpieczeństwa z silnika wózka inwalidzkiego jest szybkie i łatwe. Te instrukcje są przeznaczone dla osób, które mają nadzieję na ponowne wykorzystanie silnika wózka inwalidzkiego w projektach DIY. Wyłączenie hamulca bezpieczeństwa sprawia, że sterowanie elektr
Jak zrobić system dźwiękowy wózka na zakupy na imprezy uliczne: 10 kroków
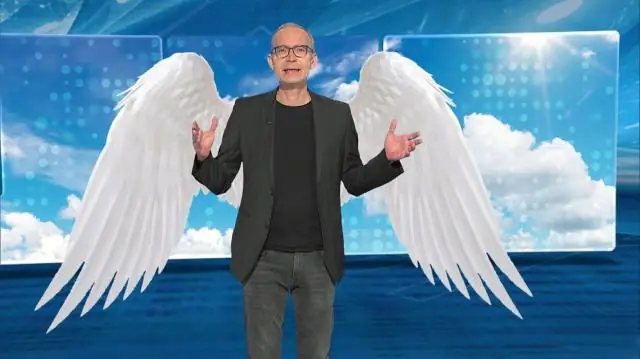
Jak zrobić system dźwiękowy wózka na zakupy na imprezy uliczne: Ten instruktaż pokaże Ci, jak stworzyć samodzielny mobilny system dźwiękowy w koszyku na zakupy. Ta konfiguracja może być używana na wszelkiego rodzaju zgromadzeniach publicznych, w tym podczas protestów, imprez tanecznych na ulicy, bitew rapowych na parkingu, a nawet