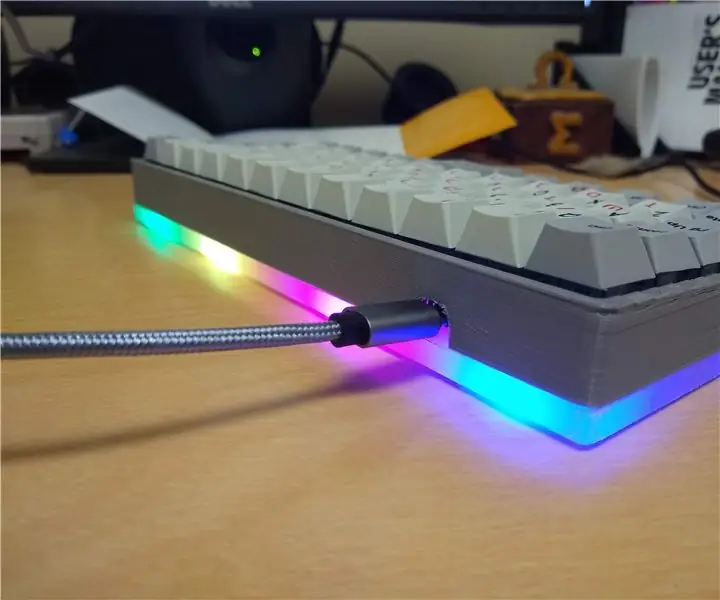
Spisu treści:
- Krok 1: 507 ruchów mechanicznych
- Krok 2: Projekt i model 3D
- Krok 3: AKTUALIZACJA 1.01.2020
- Krok 4: Sprzęt
- Krok 5: Elektronika i programowanie
- Krok 6: Złóż podstawę
- Krok 7: Dodaj przełączniki chwilowe
- Krok 8: Dodaj płytę montażową i wyłączniki krańcowe
- Krok 9: Dodaj silniki krokowe i przekładnie
- Krok 10: Dodaj stojaki
- Krok 11: Dodaj słupki godzin i minut
- Krok 12: Dodaj lupy
- Krok 13: Wyciągnięte wnioski
2025 Autor: John Day | [email protected]. Ostatnio zmodyfikowany: 2025-06-01 06:10
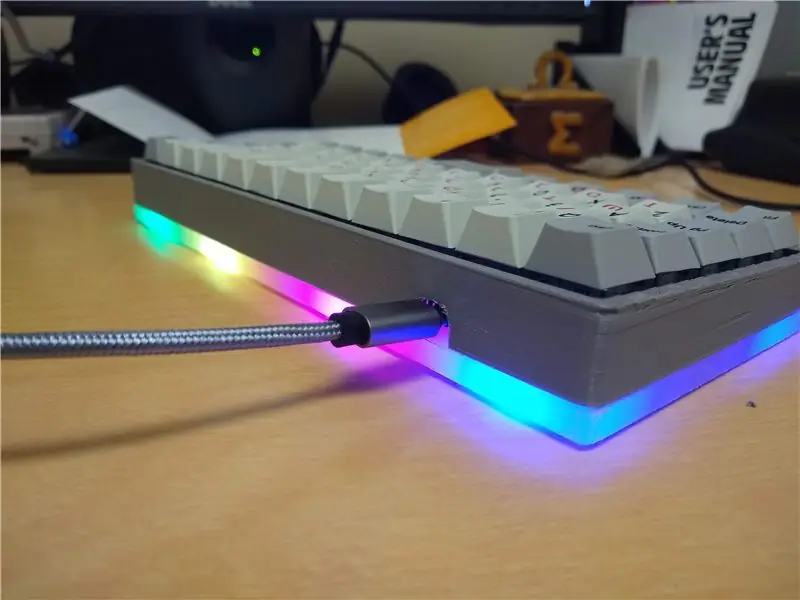
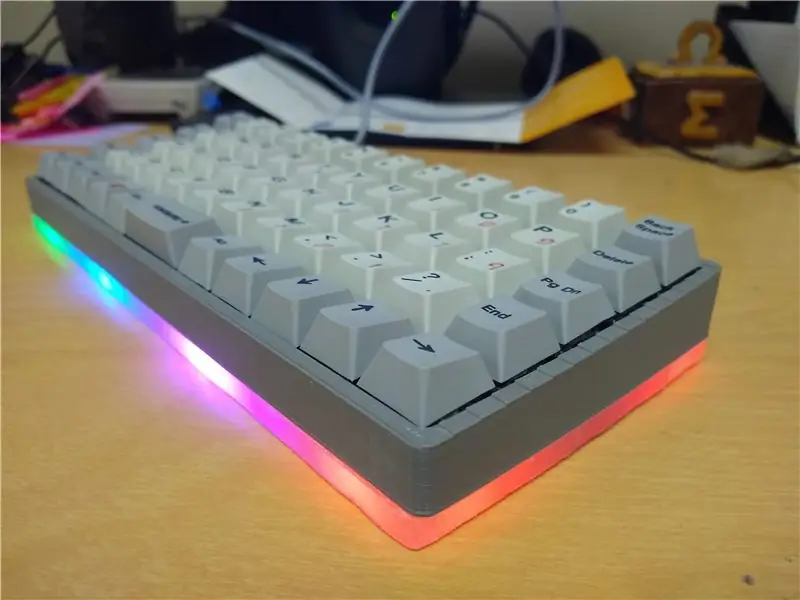
Projekty Fusion 360 »
Bez względu na to, co powie Ci Deepak Chopra, czas jest liniowy. Mam nadzieję, że ten zegar jest trochę bliższy rzeczywistości niż okrągłe zegarki, do których wszyscy jesteśmy przyzwyczajeni. Pięciominutowe interwały wydają się mniej neurotyczne niż precyzyjne co do minuty, a każda liczba jest powiększana, przypominając ci o skupieniu się na teraźniejszości.
Zrobiłem to przy użyciu prawie każdej maszyny w Pier 9 (strumień wody, piaskarka, wycinarka laserowa, drukarka 3D, laboratorium elektroniczne itp.). Wykonany jest z aluminium 6061, stalowego osprzętu (śruby, nakrętki, łożyska), wydrukowanych w 3D kół zębatych, Arduino Uno, a panele godzin i minut są wycinane laserowo / trawione ze sklejki.
Oczywiście wiem, że ten projekt nie jest dostępny dla prawie wszystkich, którzy nie mają szalenie szczęścia, że mają dostęp do takiego sklepu, ale mam nadzieję, że uznasz to za inspirujące.
Fusion 360 jest darmowy dla studentów i hobbystów i oferuje mnóstwo wsparcia edukacyjnego. Jeśli chcesz nauczyć się modelować 3D rodzaj pracy, którą wykonuję, myślę, że jest to najlepszy wybór na rynku. Kliknij poniższe linki, aby się zarejestrować:
Uczeń/Nauczyciel
Hobbysta/Startup
Prowadziłem również szereg zajęć webinarowych związanych z projektami modelowania 3D z częściami ruchomymi. Podczas tych seminariów internetowych poznasz funkcje Fusion 360, takie jak zaawansowane zespoły mechaniczne (co oznacza interakcję dwóch lub więcej połączeń) i renderowanie. Ostatnie seminarium internetowe skupiło się na modelowaniu tego projektu zegara w Fusion 360. Cały film można obejrzeć tutaj:
Jeśli jesteś zainteresowany, sprawdź pozostałe dwa webinaria z tej serii, podczas których nauczysz się projektować lampę Giant Knob i zegar wieczny z Arduino.
Krok 1: 507 ruchów mechanicznych
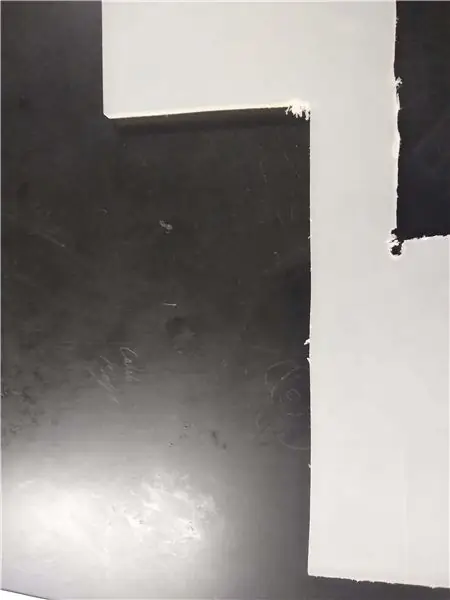
507 Mechanical Movements to encyklopedia powszechnych mechanizmów z lat 60-tych XIX wieku, która służy jako dobre odniesienie do tego rodzaju rzeczy. Ten mechanizm bazuje na Ruchu 113, „Rack and Pinion”. To będzie długi projekt, więc jeśli masz jakiś konkretny mechanizm, który chciałbyś, żebym wykonał, możesz zgłosić prośbę w komentarzach!
Krok 2: Projekt i model 3D
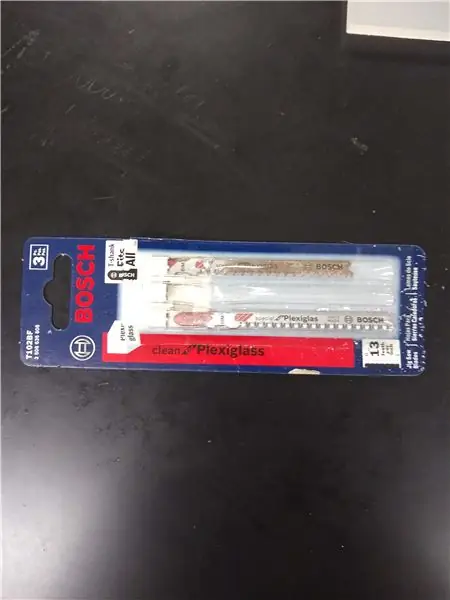
Powyższy film jest nagraniem seminarium internetowego, które przeprowadziłem dla części projektu dotyczącej projektowania zębatki i zębnika.
Najtrudniejszą częścią projektu był zespół zębatki i zębnika. Matematyka projektowania kół zębatych może być dość skomplikowana (w rzeczywistości są inżynierowie, którzy w zasadzie tylko z tego powodu projektują zespoły kół zębatych), ale w oparciu o świetny samouczek na Youtube autorstwa Roba Duarte stworzyłem własny szablon, który działa z najnowszą wersją dodatku Spur Gear do Fusion.
Powyższy film przedstawia proces tworzenia zespołu zębatki i zębnika, ale jeśli chcesz dokładniejszy samouczek, dołącz do mnie na webinarium Design Now Hour Of Making in Motion, które odbędzie się 5 kwietnia. zostanie nagrany, a wideo opublikuję tutaj.

Szablon (link poniżej) ma już wprowadzone wszystkie parametry pokazane powyżej. Nie zajmę się tutaj matematyką, ale jeśli będziesz postępować zgodnie z instrukcjami, to powinno zadziałać.
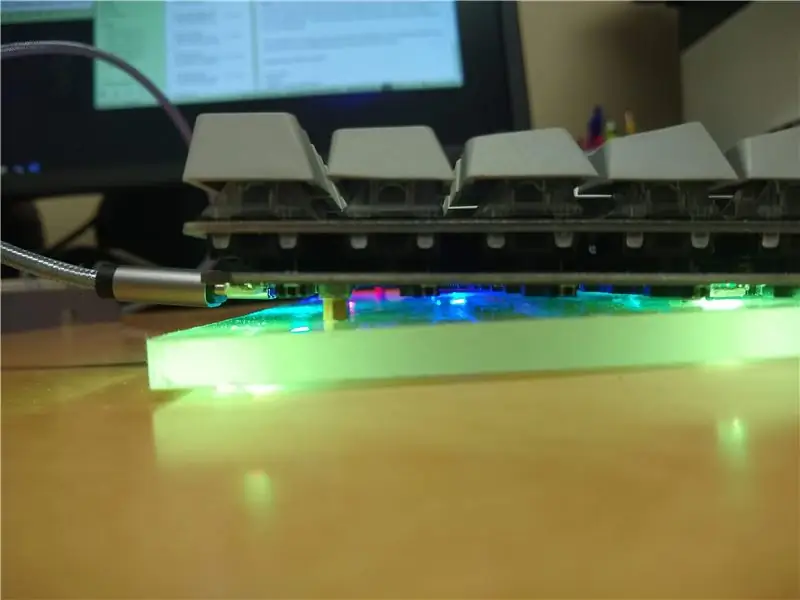
Użyj dodatku Spur Gear, przechodząc do DODATKI > Skrypty i dodatki… > Spur Gear > Uruchom. Gdy pojawi się okno pokazane powyżej, wprowadź parametry. Liczba zębów nie pozwala na użycie parametru jako wartości, więc po prostu upewnij się, że odpowiada ona wartości teethNum, jeśli ją zmienisz. Musisz również pomnożyć nazwane parametry przez 1, jak pokazano powyżej.
Pamiętaj, że po wykonaniu sprzętu możesz go edytować tak jak każdy inny obiekt w Fusion.
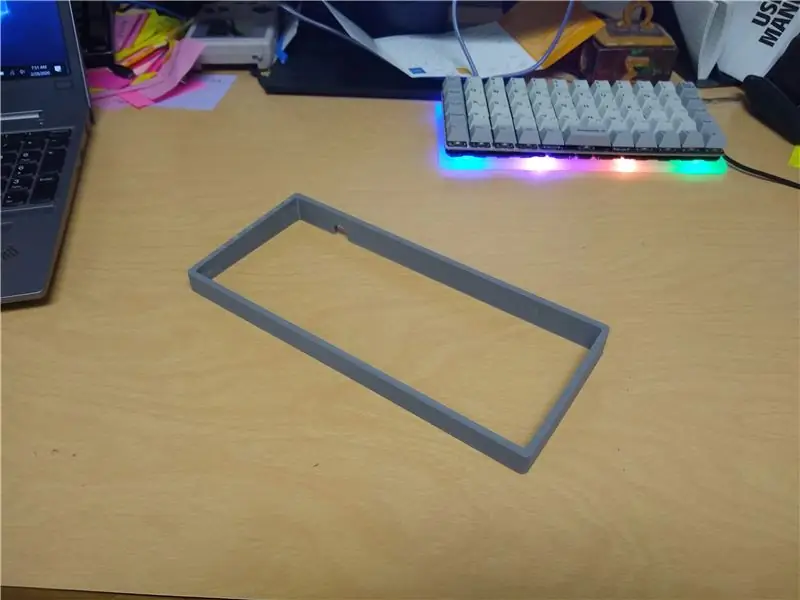
Jak pokazano w demonstracji wideo, jest to przykład konstrukcji profilu zęba przy użyciu parametrów.
Oto linki do szablonu, którego możesz użyć do stworzenia własnej zębatki i zębnika w Fusion:
Szablon z parametrami:
Po opracowaniu zębatki i zębnika spędziłem dużo czasu na modelowaniu silników, przełączników i innych części elektronicznych, a następnie dopracowywaniu wszystkich szczegółów. Dzięki opisanemu powyżej linkowi ruchu udało mi się uzyskać dobry obraz tego, jak będzie wyglądał w ruchu.
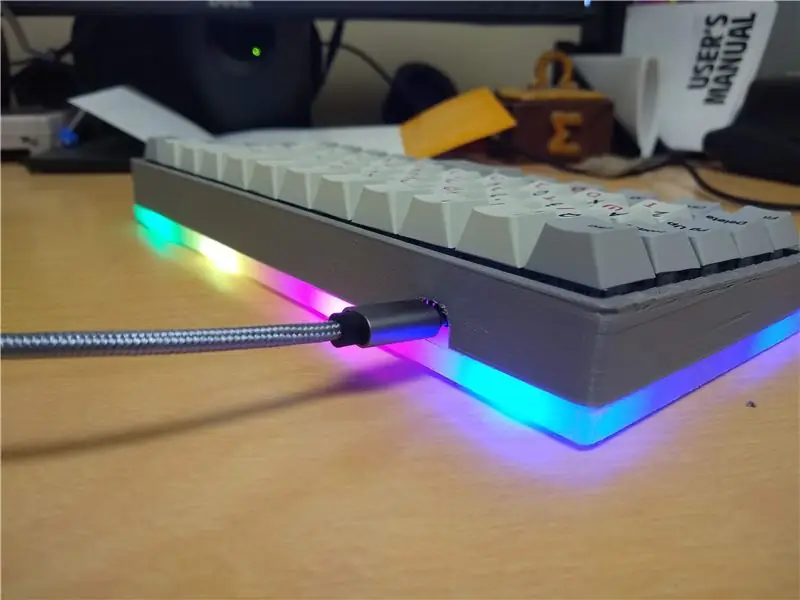
Możesz uzyskać dostęp do pliku za pomocą poniższego linku i bawić się nim, a nawet spróbować utworzyć własną wersję z pliku. Po wykonaniu części było sporo majsterkowania i przeróbek, więc nie oczekuj, że będziesz w stanie po prostu wyciąć laserem wszystkie części i otrzymać gotowy produkt. Ten projekt był drogi i zajmował dużo czasu! Jeśli naprawdę poważnie myślisz o tym i potrzebujesz pomocy, po prostu skomentuj poniżej, a zrobię co w mojej mocy, abyś mógł zacząć.
Gotowy projekt zegara:
Jeśli nie jesteś jeszcze użytkownikiem Fusion 360, zapisz się na moje bezpłatne zajęcia z drukowania 3D. To szybki kurs tworzenia Fusion, a Lekcja 2 zawiera wszystkie informacje, których potrzebujesz, aby uzyskać Fusion za darmo.
Krok 3: AKTUALIZACJA 1.01.2020
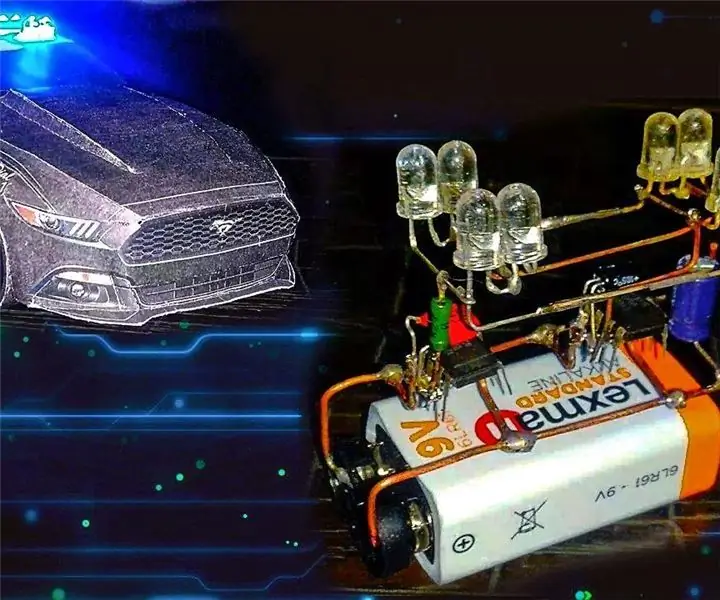
Po zbudowaniu pierwszego prototypu zacząłem od kilku ulepszeń w projekcie. Jeden z moich kolegów z zespołu elektroników zaprojektował niestandardowy obwód do napędzania silników, a istnieją czujniki magnetyczne, które pomagają wykryć położenie (indeksowane przez magnesy wciskane w szyny).
Wszystkie komponenty w modelu mają numery części, większość pochodzi od McMaster Carr lub DigiKey. Jest to znacznie lepszy projekt, ponieważ pozwala uniknąć problemu z regałami wynikającymi z ciężaru szyny po całkowitym wysunięciu, a także ponieważ indeksowanie czujnika magnetycznego zapewnia prawidłową pozycję za każdym razem, gdy silniki się poruszają.
Kompletny montaż Fusion 360:
Krok 4: Sprzęt
- Panele: aluminium 6061 o grubości 6 mm (przypuszczalnie sklejka też by się sprawdziła)
- Panel numeryczny: sklejka 3 mm
- Arduino Uno:
- Osłona silnika Adafruit:
- Silniki krokowe 5V: https://www.adafruit.com/products/858 (polecam używanie zamiast nich silników 12V)
- Wyłączniki krańcowe (4):
- Przełączniki chwilowe (2):
Krok 5: Elektronika i programowanie
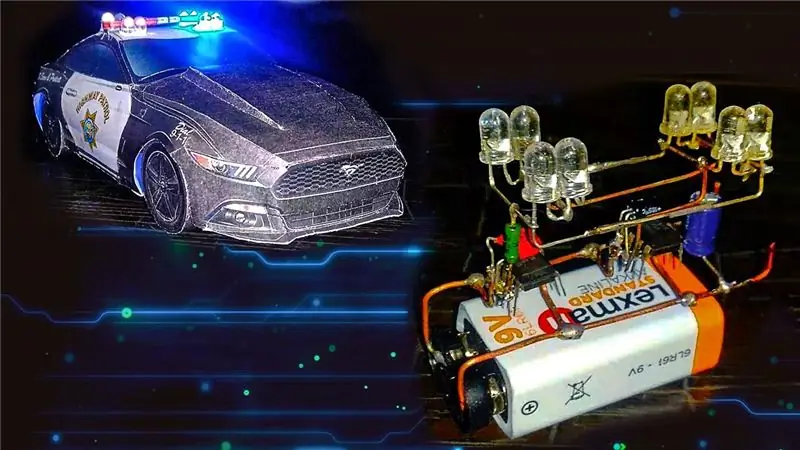

Cała elektronika jest wykonana z Arduino Uno i Adafruit Motor Shield.
Oto podstawowa idea, jak chcę, żeby to działało:
- Gdy urządzenie jest włączone, steppery przesuwają zębatki z powrotem, aż zostaną uruchomione wyłączniki krańcowe po lewej stronie. To ustawia pozycję na zero. Następnie steppery przesuwają zębatki do przodu, aż 1 będzie wyśrodkowane na panelu godzinowym, a 00 będzie wyśrodkowane na panelu minutowym.
- Po wyśrodkowaniu godziny i minuty zębatki przesuwają się do przodu w czasie. Pełna pozycja porusza się na dole z pełną prędkością co 5 minut, a pełna pozycja na górze co godzinę.
- Przełączniki chwilowe (kołki 6-7) przesuwają zębatki do przodu o jedną pozycję (około 147 kroków), a następnie kontynuują odliczanie zegara.
- Ruchy godzinowe i minutowe mają liczniki, które wysyłają słupki z powrotem do lewych wyłączników krańcowych i resetują je do zera, gdy godzina minie 12, a minuty przekroczą 55.
Nadal nie wiem, co dokładnie mam zrobić z kodem. W teorii działa to z poniższym kodem otrzymanym od Randofo. Ten kod przesuwa pasek minut o jeden krok do przodu co 200 ms (chyba) po uruchomieniu jednego z wyłączników krańcowych. To działa, ale dość szybko wychodzę z głębi podstawowej pracy, którą tutaj wykonałem. Wydaje się to dość łatwym problemem dla doświadczonego użytkownika Arduino, ale robię projekt z jednym tylko raz w roku i za każdym razem, gdy to robię, w zasadzie zapomniałem wszystkiego, czego nauczyłem się w ostatnim projekcie.
/*************************************************************
Demo Motor Shield Stepper autorstwa Randy'ego Sarafan
Aby uzyskać więcej informacji zobacz:
www.instructables.com/id/Arduino-Motor-Shi…
*************************************************************/
#include #include #include "narzędzie/Adafruit_MS_PWMServoDriver.h"
// Utwórz obiekt osłony silnika z domyślnym adresem I2C
Adafruit_MotorShield AFMS = Adafruit_MotorShield(); // Lub utwórz go z innym adresem I2C (powiedzmy dla stosu) // Adafruit_MotorShield AFMS = Adafruit_MotorShield(0x61);
// Podłącz silnik krokowy z 200 krokami na obrót (1,8 stopnia)
// do portu silnika #2 (M3 i M4) Adafruit_StepperMotor *myMotor1 = AFMS.getStepper(300, 1); Adafruit_StepperMotor *myMotor2 = AFMS.getStepper(300, 2);
int delaylegnth = 7;
pusta konfiguracja () {
//uruchom połączenie szeregowe Serial.begin(9600); //skonfiguruj pin2 jako wejście i włącz wewnętrzny rezystor podciągający pinMode(2, INPUT_PULLUP);
// Serial.początek(9600); // skonfiguruj bibliotekę szeregową na 9600 bps
Serial.println("Test krokowy!");
AFMS.początek(); // utwórz z domyślną częstotliwością 1,6KHz
//AFMS.początek(1000); // LUB z inną częstotliwością, powiedzmy 1KHz myMotor1->setSpeed(100); // 10 obr/min }
pusta pętla () {
//odczytaj wartość przycisku do zmiennej int sensorVal = digitalRead(2); czujnikVal == NISKI; int opóźnienieL = 200; if (sensorVal == LOW) { Serial.println("Minuty ++"); //mójMotor1->krok(1640, WSTECZ, PODWÓJNIE); for (int i=0; i step(147, BACKWARD, DOUBLE); //analogWrite(PWMpin, i); delay(delayL); } Serial.println("Godziny ++"); myMotor1->step(1615, DO PRZODU, PODWÓJNY);
//myMotor2->krok(1600, WSTECZ, PODWÓJNIE);
myMotor2->krok(220, DO PRZODU, PODWÓJNIE); //opóźnienie(opóźnienieL); } w przeciwnym razie {
//Serial.println("Kroki z podwójną cewką");
myMotor1->krok(0, DO PRZODU, PODWÓJNIE); mójMotor1->krok(0, DO TYŁU, PODWÓJNIE); } }
Krok 6: Złóż podstawę
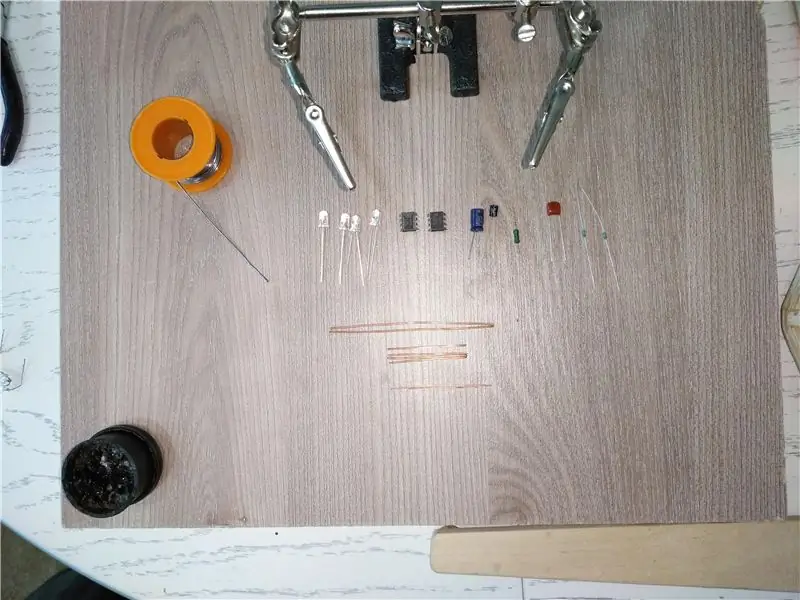
Podstawa składa się z dwóch płytek z przekładkami łączącymi je ze sobą. Śruby mocuje się do płyty przez otwory gwintowane. Część numer 6 na tym rysunku to kolejna wydrukowana w 3D część - przekładka, która jest również kołyską dla zacisku zasilania silników krokowych.
Krok 7: Dodaj przełączniki chwilowe
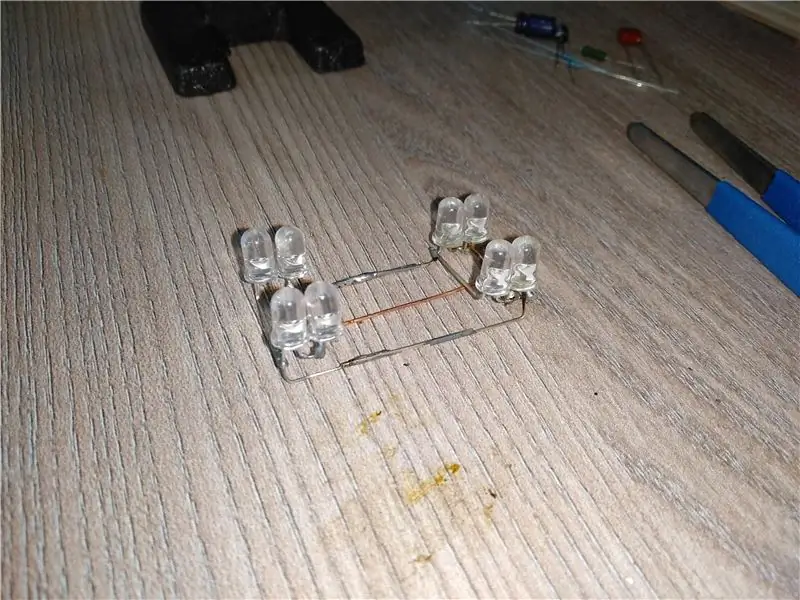
Przełączniki chwilowe, Arduino i wyłączniki krańcowe są przymocowane do płyty przedniej, dzięki czemu dostęp do elektroniki w celu wprowadzenia zmian jest łatwy - wystarczy zdjąć tylną płytę i można sięgnąć po wszystko.
Krok 8: Dodaj płytę montażową i wyłączniki krańcowe
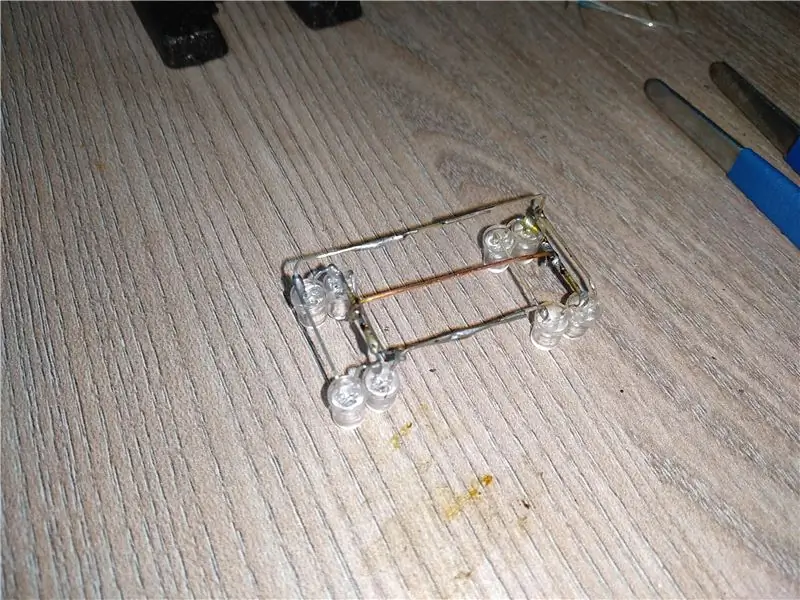
Płyta montażowa zawiera wyłączniki krańcowe i zespół łożysk dla zębatek. Ta część może również pozostać razem podczas edycji elektroniki.
Krok 9: Dodaj silniki krokowe i przekładnie
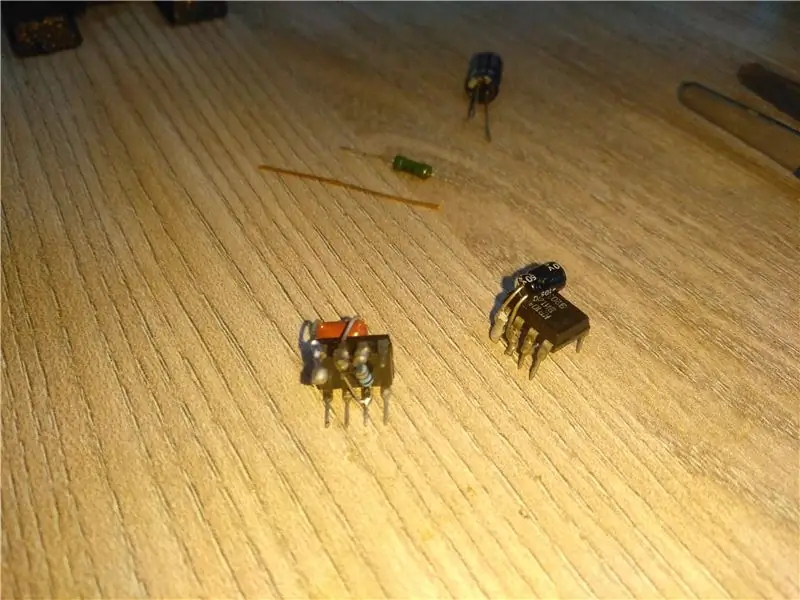
Silniki krokowe są mocowane do panelu za pomocą śrub M4 przez otwory gwintowane, a wydrukowane w 3D koła zębate są wciskane na słupki silnika. Użyłem zacisku na spuście, aby je dopasować i spłukać.
Krok 10: Dodaj stojaki
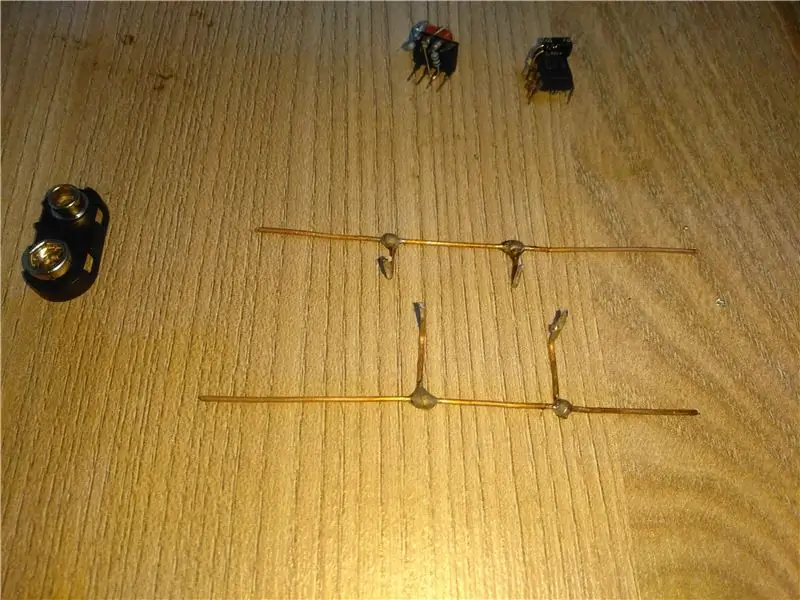
Regały mają wycięte w nich szczeliny, które opierają się na dwóch łożyskach kulkowych. Pomiędzy łożyskami a szczelinami znajduje się niewielka szczelina (0,1 mm), która umożliwia swobodne poruszanie się stelaża.
Łożyska są umieszczone pomiędzy niestandardowymi przekładkami drukowanymi w 3D, aby uzyskać dokładne dopasowanie, którego potrzebowałem. Z przodu znajduje się płyta stojaka, która działa jak podkładka utrzymująca stojaki na miejscu.
Krok 11: Dodaj słupki godzin i minut
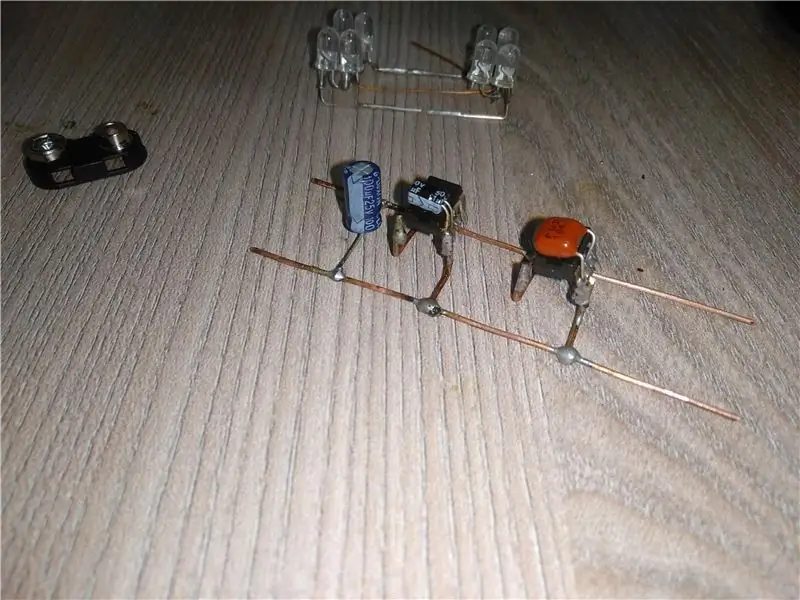
Pręty godzinowe i minutowe mocowane są do stojaków za pomocą przekładek 12mm, tworząc szczelinę, która umożliwia prześwit między prętami a stojakami.
Krok 12: Dodaj lupy
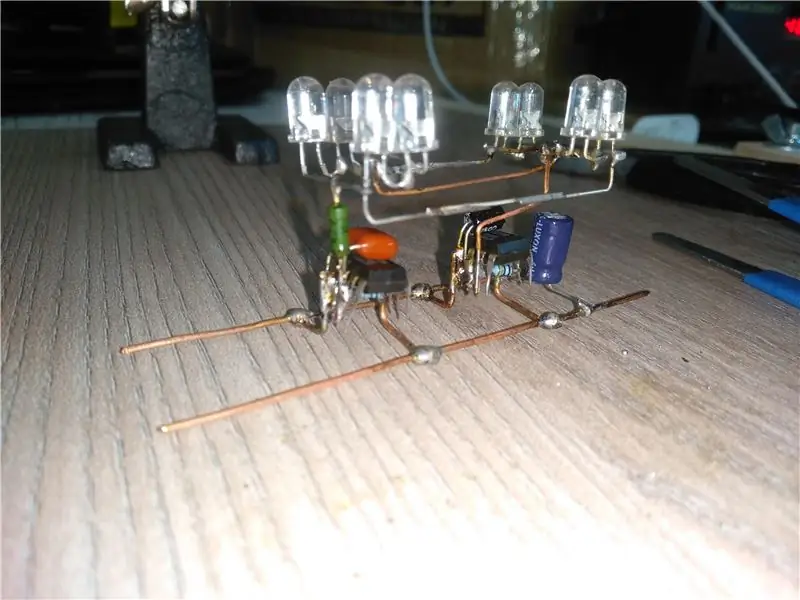
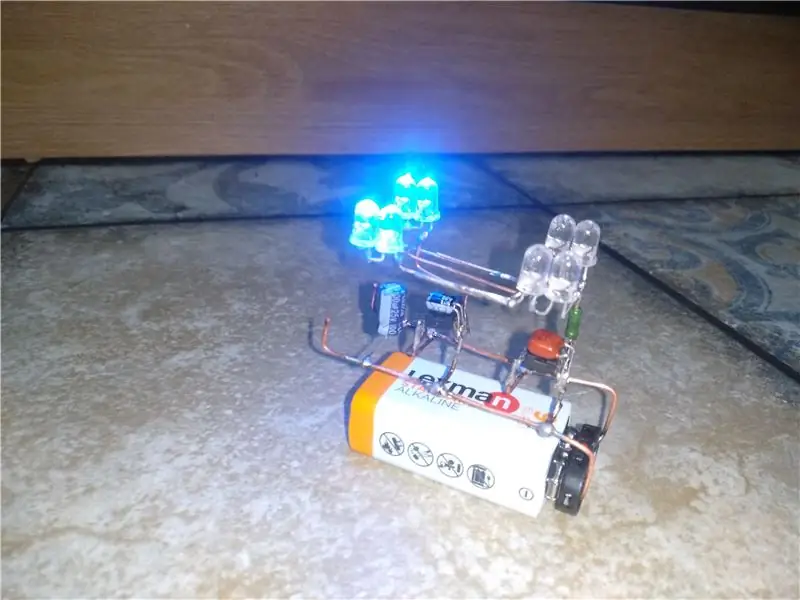
Lupy to tanie kieszonkowe lupy, które znalazłem na amazon. Są one odsunięte od przedniej części kierownicy za pomocą przekładek 25mm.
Krok 13: Wyciągnięte wnioski
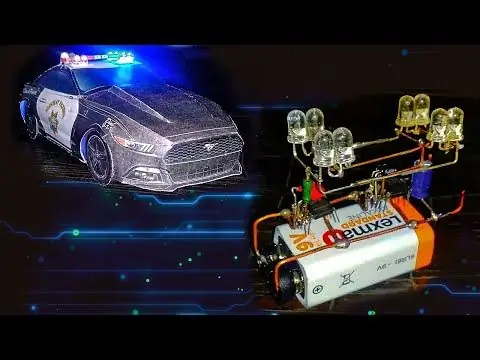
Dzięki temu projektowi wiele się nauczyłem o ruchu liniowym. Tolerancja, którą zastosowałem między łożyskami a szczelinami na zębatkach, była trochę za duża, więc gdybym miał zrobić to ponownie, prawdopodobnie przeciąłbym go na pół. Luka po bokach luk też była trochę za duża.
Silniki działają, ale im dłuższy jest wspornik, tym więcej muszą pracować. Pewnie wybrałbym steppery 12V zamiast 5V.
Luz też powinien być większy, może 0,25mm. Przy pierwszych biegach, które wypróbowałem, koła zębate zbyt mocno opadały na zębatki.
Zalecana:
Zegar WiFi, zegar i stacja pogodowa, sterowanie Blynk: 5 kroków (ze zdjęciami)
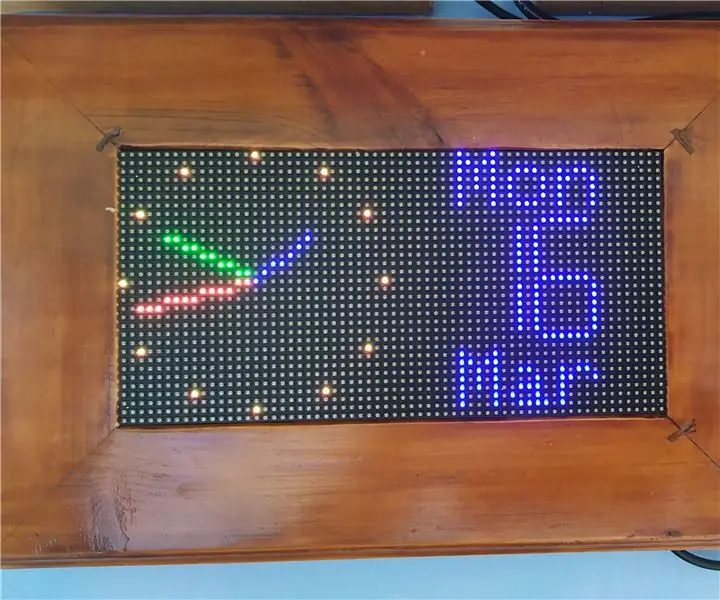
Zegar WiFi, timer i stacja pogodowa, sterowanie Blynk: jest to zegar cyfrowy Morphing (dzięki Hari Wiguna za koncepcję i kod morfingu), jest to również zegar analogowy, stacja raportowania pogody i minutnik kuchenny. Jest kontrolowany w całości przez Aplikacja Blynk na smartfonie przez Wi-Fi.Aplikacja umożliwia
Zasilacz liniowy sterowany cyfrowo: 6 kroków (ze zdjęciami)
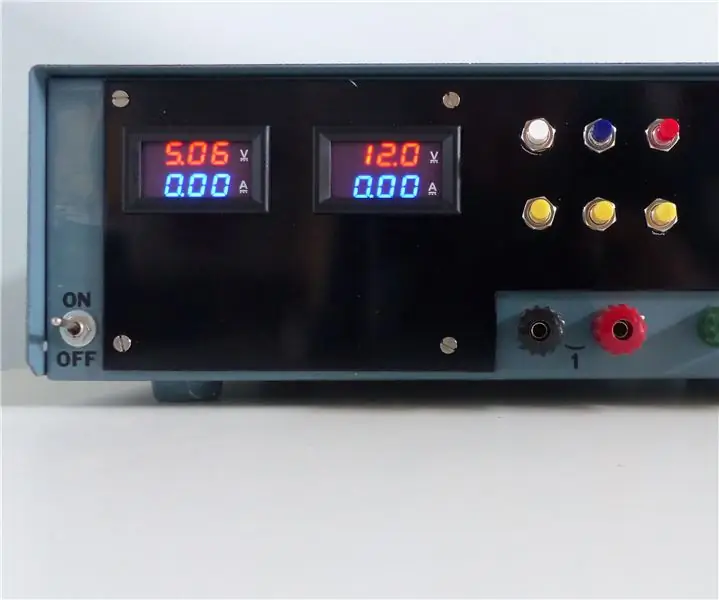
Sterowany cyfrowo zasilacz liniowy: W moich nastoletnich latach, około 40 lat temu, stworzyłem podwójny liniowy zasilacz. Schemat dostałem z magazynu „Elektuur”, obecnie zwanego „Elektor” w Holandii. Ten zasilacz wykorzystywał jeden potencjometr do regulacji napięcia
Regulowany zasilacz liniowy z podwójnym wyjściem: 10 kroków (ze zdjęciami)
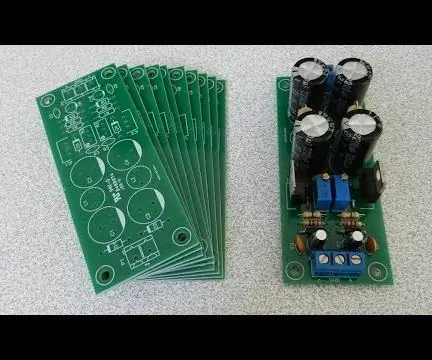
Regulowany zasilacz liniowy z podwójnym wyjściem: Cechy: Konwersja AC – DC Podwójne napięcia wyjściowe (dodatnie – uziemienie – ujemne) Regulowane szyny dodatnie i ujemne Tylko pojedynczy transformator AC z pojedynczym wyjściem Szum wyjściowy (20 MHz-BWL, bez obciążenia): około 1,12 mVpp niski hałas i stabilne wyjścia (idealne
ESP8266 Zegar sieciowy bez zegara RTC - Nodemcu NTP Zegar bez RTC - PROJEKT ZEGAR INTERNETOWY: 4 kroki
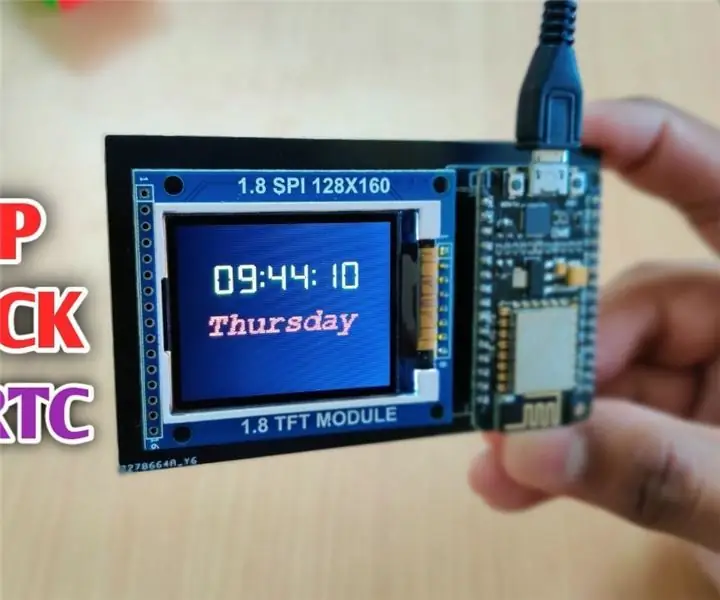
ESP8266 Zegar sieciowy bez zegara RTC | Nodemcu NTP Zegar bez RTC | PROJEKT ZEGARA INTERNETOWEGO: W projekcie będzie wykonywany projekt zegara bez RTC, będzie pobierał czas z internetu za pomocą wifi i wyświetli go na wyświetlaczu st7735
Zegar liniowy za pomocą Arduino + DS1307 + Neopixel: ponowne użycie sprzętu.: 5 kroków
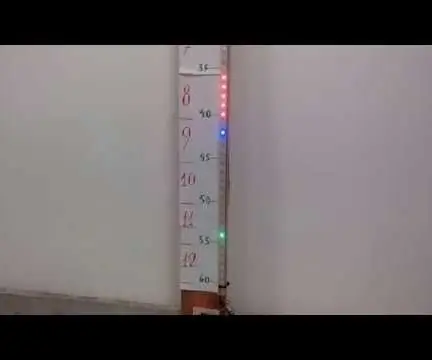
Zegar liniowy przy użyciu Arduino + DS1307 + Neopixel: ponowne użycie niektórych urządzeń.: Z poprzednich projektów został mi pasek LED Arduino UNO i Neopixel i chciałem zrobić coś innego. Ponieważ pasek Neopixel ma 60 diod LED, pomyślano, aby używać go jako dużego zegara. Do wskazania godzin używany jest czerwony segment 5-LED (60 LED