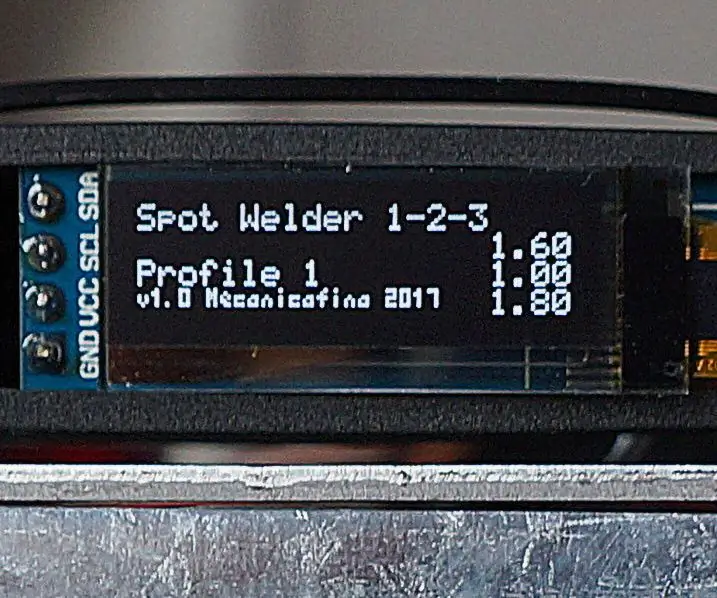
Spisu treści:
2025 Autor: John Day | [email protected]. Ostatnio zmodyfikowany: 2025-01-23 15:02
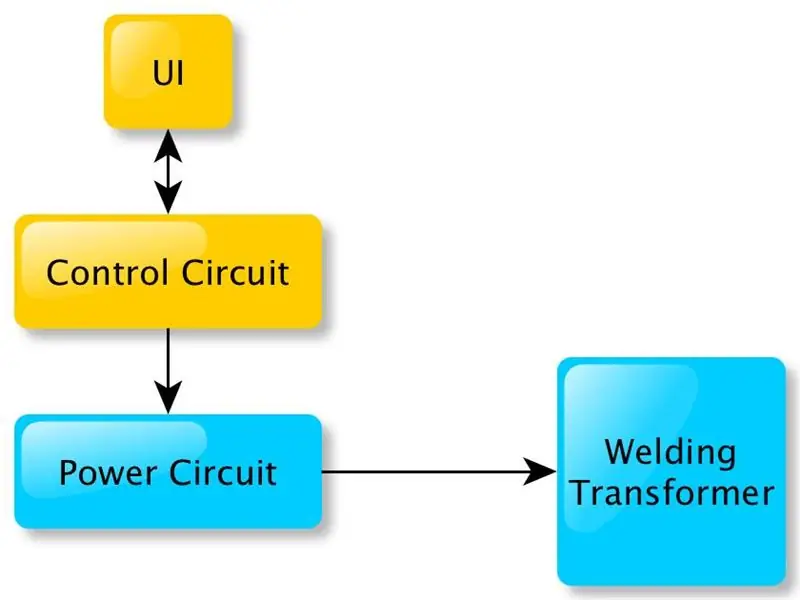

Dlaczego kolejny projekt zgrzewarki punktowej?
Budowa zgrzewarki punktowej to jeden z (prawdopodobnie nielicznych) przypadków, w których można zbudować coś za ułamek ceny komercyjnej wersji o porównywalnej jakości. I nawet jeśli budowa przed zakupem nie była zwycięską strategią, jest to świetna zabawa!
Postanowiłem więc rozpocząć projekt i przyjrzałem się, jak zrobili to inni ludzie. W sieci jest dosłownie mnóstwo ciekawych informacji i filmów na ten temat, z dość dużym zróżnicowaniem jakości projektu i wykonania.
Jakość konstrukcji, którą można realistycznie osiągnąć, zależy od dostępnych narzędzi, maszyn i urządzeń, więc nie było zaskoczeniem spore zróżnicowanie na tym froncie. Z drugiej strony nie spodziewałem się, że większość projektów używa prostego ręcznego przełącznika do uruchamiania i zatrzymywania procesu spawania.
W rzeczywistości dokładna kontrola czasu spawania ma kluczowe znaczenie dla jakości spawów, a nie można tego osiągnąć, ręcznie przestawiając przełącznik.
Poczułem, że o ile zbudowanie zgrzewarki punktowej to temat, który prawdopodobnie został już pobity na śmierć, to może można by zrobić lepszą maszynę, używając trzystopniowego procesu zgrzewania z dokładnymi czasami, tak jak robią to profesjonalne maszyny. Postawiłem sobie więc pięć głównych celów projektowych dla mojego projektu:
Wsparcie dla trzyetapowego procesu spawania
Dokładne i konfigurowalne czasy
Możliwość trwałego przechowywania i odzyskiwania profili spawalniczych
Prostota projektowania i budowy
Stosowanie wyłącznie powszechnie dostępnych komponentów
Rezultatem jest moja zgrzewarka punktowa 1-2-3 i w tej instrukcji wyjaśnię część projektu dotyczącą kontroli procesu spawania. Film i ta instrukcja pokazują zdjęcia prototypowej spawarki testowej, zanim wszystkie komponenty zostaną zamontowane w odpowiedniej obudowie. Tablica do tego projektu jest opisana w osobnej instrukcji.
Jeśli chcesz zapoznać się z pojęciem zgrzewania oporowego i jak można wykonać spawarkę za pomocą transformatora mikrofalowego, zrób to przed lekturą. Skoncentruję się na kontroli spawacza, a nie na tym, jak spawacz pracuje lub jak go zbudować. Czuję, że jest to dobrze omówione gdzie indziej.
Krok 1: Przepis
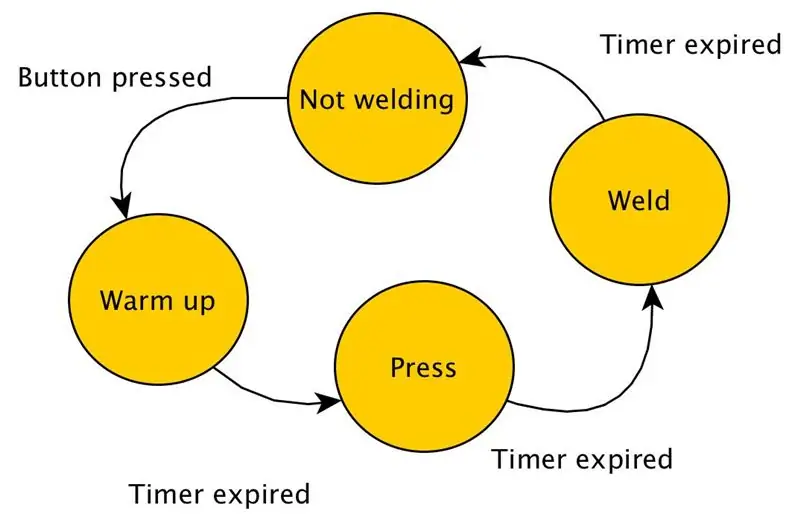
Przyjrzyjmy się składom zgrzewarki oporowej:
Transformator spawalniczy. Zapewnia wyjście niskiego napięcia/wysokiego prądu niezbędne do zgrzewania oporowego poprzez konwersję napięcia sieciowego AC. W przypadku spawacza samodzielnie wykonanego transformator spawalniczy jest zwykle uzyskiwany przez przekształcenie transformatora kuchenki mikrofalowej na niskonapięciowe, wysokoprądowe wyjście. Odbywa się to poprzez usunięcie uzwojenia wtórnego wysokiego napięcia z MOT i nawinięcie nowego wtórnego składającego się z kilku zwojów bardzo grubego kabla miedzianego. Na YouTube jest wiele filmów, które pokazują, jak to zrobić
Obwód zasilania. Włącza i wyłącza transformator spawalniczy, a jego działaniem steruje obwód sterujący. Obwód zasilania działa pod napięciem sieciowym
Obwód sterowania. Kontroluje wszystkie operacje dla spawacza:
- Umożliwia użytkownikowi przechowywanie i odczytywanie czasów spawania.
- I wreszcie, co nie mniej ważne, umożliwia użytkownikowi rozpoczęcie procesu spawania poprzez wysyłanie poleceń do obwodu zasilania, który włącza i wyłącza transformator.
Umożliwia użytkownikowi ustawienie i zmianę czasów spawania
interfejs użytkownika. Użytkownik komunikuje się z Obwodem Sterującym za pośrednictwem Interfejsu Użytkownika
Ta instrukcja opisuje interfejs użytkownika i obwód sterowania. Proponowany przeze mnie projekt interfejsu użytkownika i obwodu sterującego jest w rzeczywistości całkiem niezależny od innych bloków i można go łatwo doposażyć w istniejącą zgrzewarkę punktową, pod warunkiem, że twoje obecne wcielenie obwodu zasilania może obsłużyć cyfrowy sygnał wyjściowy z obwodu sterującego. Jeśli więc masz już spawarkę z przełączaniem elektronicznym, możesz dodać opisane tutaj elementy sterowania i interfejsu użytkownika bez żadnych innych modyfikacji.
Jeśli masz teraz tylko ręczny wyłącznik zasilania, będziesz musiał również zbudować obwód zasilania.
Zanim opiszemy działanie oprogramowania układowego dla obwodu sterującego, przyjrzyjmy się nieco bardziej szczegółowo, jak działa proces spawania.
Krok 2: Spawanie 1-2-3
Profesjonalne spawarki nie spawają w jednym kroku; używają zautomatyzowanej trzyetapowej sekwencji. Zgrzewanie oporowe trójetapowe składa się z:
Rozgrzewka. Transformator spawalniczy jest włączony, prąd płynie przez elektrody przez obrabiane elementy. Ma to na celu po prostu rozgrzanie metalu
Krok prasy: Transformator spawalniczy jest wyłączony; obrabiane elementy są mocno dociśnięte do siebie. Zmiękczone powierzchnie gorących elementów metalowych zapewniają teraz bardzo dobry kontakt mechaniczny i elektryczny
Krok spawania: Transformator spawalniczy zostaje ponownie włączony. Metalowe powierzchnie znajdujące się teraz w bliskim kontakcie są zgrzewane pod ciśnieniem
Czas trwania poszczególnych kroków jest generalnie niejednorodny i zależy od dostępnego prądu od spawacza, rodzaju materiału, który próbujemy zgrzewać (głównie jego wytrzymałości i temperatury topnienia) oraz grubości obrabianych elementów.
Wiele samodzielnie zbudowanych spawarek, o których się dowiedziałem, nie posiada automatycznej kontroli czasu, co bardzo utrudnia powtarzalną i niezawodną pracę.
Niektóre mają możliwość ustawienia czasu zgrzewania, często za pomocą potencjometru. Kerry Wong zrobił bardzo fajny w tej klasie z dodatkową parą elektrod specjalnie do spawania akumulatorów.
Bardzo niewielu spawaczy samodzielnie zbudowanych jest w stanie automatycznie wykonać trzy kroki spawania, jak opisano powyżej. Niektóre mają tylko jeden zestaw ustalonych czasów trwania, taki jak ten i ten. W przypadku innych możesz zmienić niektóre czasy trwania, tak jak w przypadku tego. Ma ustalony czas trwania kroków nagrzewania i prasowania, a czas trwania kroku spawania można zmienić za pomocą potencjometru.
To sprawia, że proces jest częściowo regulowany, ale ponowne znalezienie ustawienia może być trudne, gdy po pewnym czasie zechcesz ponownie zgrzać ten konkretny materiał wypustki akumulatora. Po znalezieniu odpowiednich czasów dla określonej kombinacji materiału i grubości, nie chcesz robić tego od nowa. To strata czasu (i materiałów) i może być trochę frustrująca.
To, czego (cóż, ja) naprawdę chcesz tutaj, to pełna elastyczność (konfigurowalność) dla wszystkich czasów oraz możliwość przechowywania i pobierania ustawień, gdy już je uzyskamy.
Na szczęście nie jest to takie trudne. Zobaczmy, jak kontrolować trzystopniowe zgrzewanie oporowe.
Krok 3: 1-2-3 Kontrola spawania
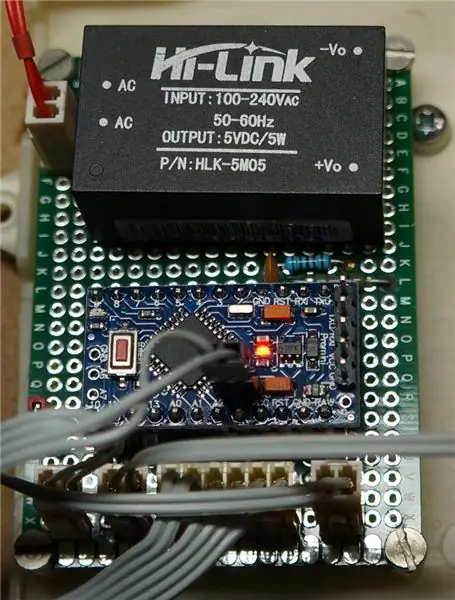
Realizujemy Obwód Sterujący z mikrokontrolerem (MCU). Oprogramowanie układowe MCU działa jako maszyna stanów z czterema stanami, jak widzieliśmy w poprzednim kroku:
o Stan 0: Brak spawania
o Stan 1: Spawanie, etap rozgrzewania
o Stan 2: Spawanie, naciśnij krok
o Stan 3: Spawanie, krok spawania
Używam pseudokodu w stylu C, aby opisać tutaj przepływ programu, ponieważ łatwo jest powiązać go z rzeczywistym kodem MCU napisanym w C/C++.
Po etapie konfiguracji pętla główna MCU obsługuje dane wejściowe użytkownika i zmiany stanu w następujący sposób:
01: pętla
02: switch (stan) { 03: przypadek 0: 04: readUserInput 05: przypadek 1, 2, 3: 06: if (zegar spawalniczy wygasł) { 07: // przejdź do następnego stanu 08: stan = (stan + 1) % 4; 09: przełącz sterowanie mocą 10: jeśli (stan jest inny niż 0) { 11: ustaw nowy czas trwania kroku i zrestartuj timer spawania 12: } 13: } 14: zakończenie pętli
Jeśli bieżący stan wynosi 0, odczytujemy stan interfejsu użytkownika, aby przetworzyć dane wejściowe użytkownika i przejść do następnej iteracji.
Używamy timera zgrzewania, aby kontrolować czas trwania kroków zgrzewania. Załóżmy teraz, że sekwencja spawania właśnie się rozpoczęła, gdy wprowadzamy instrukcję switch. Kontrola mocy jest włączona, transformator spawalniczy jest pod napięciem, a aktualny stan wynosi 1.
Jeśli czas zgrzewania nie wygasł, warunek warunkowy (wiersz 6) przyjmuje wartość false, wychodzimy z instrukcji switch i przechodzimy do następnej iteracji pętli zdarzeń.
Jeśli czas zgrzewania wygasł, wprowadzamy warunek (linia 6) i przechodzimy dalej:
1. Oblicz i zapisz następny stan (wiersz 8). Używamy arytmetyki modulo 4, aby śledzić prawidłową sekwencję stanów 1-2-3-0. Jeśli obecny stan to 1, przechodzimy teraz do stanu 2.
2. Następnie przełączamy sterowanie mocą (linia 9). W stanie 1 sterowanie mocą było włączone, więc teraz jest wyłączone (tak jak powinno być w stanie 2, naciśnij krok, gdy transformator spawalniczy nie jest pod napięciem).
3. Stan jest teraz 2, więc wpisujemy warunek w linii 10.
4. Ustaw zegar spawania na nowy czas trwania kroku (czas trwania kroku prasy) i uruchom ponownie zegar spawania (wiersz 11).
Kolejne iteracje pętli głównej będą przebiegać bez zakłóceń, dopóki licznik czasu spawania nie upłynie ponownie, tj. etap prasowania zostanie zakończony.
W tym momencie wchodzimy do ciała warunku w linii 6. Kolejny stan (stan 3) jest obliczany w linii 8; ponownie włącza się zasilanie transformatora (linia 9); zegar zgrzewania jest ustawiany na czas trwania kroku zgrzewania i uruchamiany ponownie.
Gdy licznik czasu wygaśnie ponownie, następny stan (stan 0) jest obliczany w linii 8, ale teraz linia 11 nie jest wykonywana, więc licznik czasu nie jest restartowany po zakończeniu cyklu spawania.
W następnej iteracji pętli wracamy do przetwarzania danych wejściowych użytkownika (linia 4). Gotowe.
Ale jak w ogóle rozpocząć proces spawania? Cóż, zaczynamy, gdy użytkownik naciśnie przycisk spawania.
Przycisk spawania jest podłączony do pinu wejściowego MCU, który jest podłączony do przerwania sprzętowego. Naciśnięcie przycisku powoduje wystąpienie przerwania. Program obsługi przerwania rozpoczyna proces spawania poprzez ustawienie stanu na 1, ustawienie timera spawania na czas trwania kroku nagrzewania, uruchomienie timera spawania i włączenie regulatora mocy:
19: startSpawanie
20: stan = 1 21: ustaw czas trwania kroku nagrzewania i uruchom zegar spawania 22: włącz sterowanie mocą 23: koniec startu spawania
Krok 4: Zarządzanie interfejsem użytkownika, tryb gotowości i inne komplikacje dotyczące oprogramowania układowego
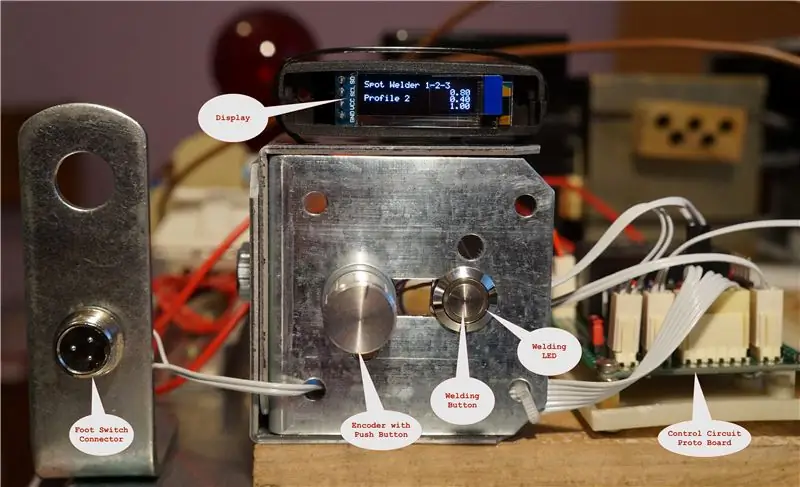
Interfejs użytkownika składa się z wyświetlacza, enkodera z przyciskiem, przycisku chwilowego i diody LED. Są używane w następujący sposób:
Wyświetlacz dostarcza użytkownikowi informacji zwrotnych dotyczących konfiguracji i pokazuje postęp podczas spawania
Enkoder z przyciskiem steruje wszystkimi interakcjami z oprogramowaniem układowym, z wyjątkiem uruchamiania sekwencji spawania
Chwilowy przycisk jest wciśnięty, aby rozpocząć sekwencję spawania
Dioda świeci się podczas sekwencji spawania i jest wielokrotnie zapalana i gaszona w trybie gotowości
Istnieje wiele rzeczy, które oprogramowanie układowe musi zrobić poza kontrolowaniem procesu spawania, jak wyjaśniono w poprzednim kroku:
Odczytywanie danych wprowadzonych przez użytkownika. Wiąże się to z odczytem pozycji enkodera i stanu przycisku. Użytkownik może obrócić enkoder w lewo lub w prawo, aby przejść z jednej pozycji menu do następnej i zmienić parametry na wyświetlaczu, lub może nacisnąć przycisk enkodera, aby potwierdzić wprowadzoną wartość lub przejść o jeden poziom w górę struktury menu
-
Aktualizacja interfejsu użytkownika.
Wyświetlacz jest aktualizowany w celu odzwierciedlenia działań użytkownika
Wyświetlacz jest aktualizowany w celu odzwierciedlenia postępu procesu spawania (pokazujemy wskaźnik obok czasu trwania bieżącego kroku w sekwencji spawania)
Dioda zapala się, gdy zaczynamy spawanie i gaśnie, gdy kończymy
Czekaj. Kod śledzi, jak długo użytkownik był nieaktywny i przechodzi w stan czuwania, gdy okres nieaktywności przekroczy ustawiony limit. W trybie czuwania wyświetlacz jest wyłączony, a dioda na interfejsie użytkownika jest wielokrotnie włączana i wyłączana, sygnalizując stan czuwania. Użytkownik może wyjść ze stanu wstrzymania, obracając enkoder w dowolnym kierunku. W trybie gotowości interfejs użytkownika nie powinien reagować na inne interakcje użytkownika. Zwróć uwagę, że spawacz może przejść w stan czuwania tylko wtedy, gdy jest w stanie 0, np. nie podczas spawania
Zarządzanie ustawieniami domyślnymi, przechowywanie i pobieranie profili. Oprogramowanie sprzętowe obsługuje 3 różne profile spawania, tj. ustawienia dla 3 różnych materiałów/grubości. Profile są przechowywane w pamięci flash, więc nie zostaną utracone po wyłączeniu spawarki
Jeśli się zastanawiasz, dodałem funkcję czuwania, aby zapobiec wypaleniu wyświetlacza. Gdy spawarka jest zasilana, a nie korzystasz z interfejsu użytkownika, znaki wyświetlane na wyświetlaczu nie zmieniają się i mogą powodować wypalenie. Twój przebieg może się różnić w zależności od technologii wyświetlania, jednak używam wyświetlacza OLED i są one podatne na palić się dość szybko, jeśli nie zostaniesz zaniedbany, więc dobrym pomysłem jest automatyczne wyłączanie wyświetlacza.
Wszystko powyższe komplikuje oczywiście „prawdziwy” kod. Widać, że jest trochę więcej do zrobienia niż to, na co patrzyliśmy w poprzednich krokach, aby uzyskać ładnie opakowany kawałek oprogramowania.
Potwierdza to zasadę, że w przypadku oprogramowania implementacja tego, co zbudujesz wokół podstawowej funkcjonalności, jest często bardziej złożona niż sama implementacja podstawowej funkcjonalności!
Pełny kod znajdziesz w linku do repozytorium na końcu tej instrukcji.
Krok 5: Obwód sterowania
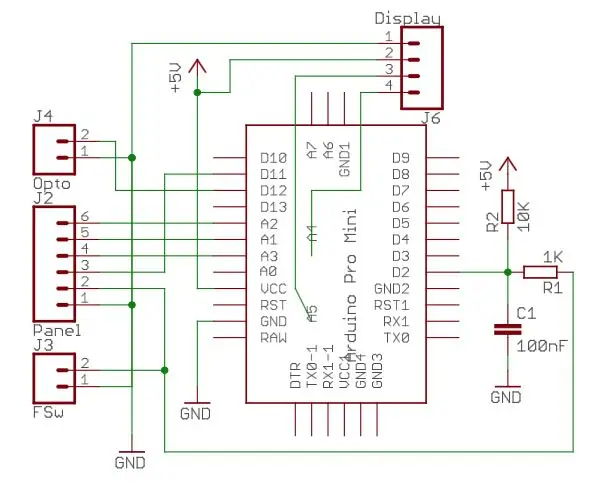
Oprogramowanie układowe zostało opracowane i przetestowane przy użyciu następujących komponentów:
-
Obwód sterowania:
Arduino Pro Mini 5V 16MHz
-
interfejs użytkownika:
- Enkoder obrotowy z przyciskiem
- 0,91” 128x32 I2C biały wyświetlacz OLED DIY oparty na SSD1306
- Chwilowy przycisk z wbudowaną diodą LED
Oczywiście nie musisz używać dokładnie tych komponentów w swojej kompilacji, ale być może będziesz musiał dokonać pewnych modyfikacji kodu, jeśli tego nie zrobisz, zwłaszcza jeśli zmienisz interfejs wyświetlania, typ lub rozmiar.
Przypisanie pinów Arduino:
-
Wejście:
- Piny A1 A2 A3 do enkodera obrotowego służącego do wyboru/zmiany profili i parametrów
- Pin 2 podłączony do tymczasowego przycisku, który jest wciśnięty w celu rozpoczęcia spawania. Przycisk jest zwykle montowany na panelu obok enkodera i może być podłączony równolegle do przełącznika nożnego.
-
Wyjście:
- Piny A4/A5 dla I2C sterujące wyświetlaczem.
- Pin 11 dla wyjścia cyfrowego do diody LED, która jest włączana podczas cyklu spawania i włączana i wyłączana w trybie gotowości. Na schemacie nie ma rezystora ograniczającego prąd dla diody led, ponieważ użyłem diody wbudowanej w przycisk spawania, który był dostarczany z rezystorem szeregowym. Jeśli używasz oddzielnej diody LED, musisz albo dodać rezystor szeregowo między pinem 11 Pro Mini a pinem 3 złącza J2 lub przylutować go szeregowo z diodą LED na panelu przednim.
- Pin 12 dla wyjścia cyfrowego do obwodu zasilania sieciowego (wejście do obwodu zasilania). Ten kołek jest zwykle NISKI i będzie przechodził WYSOKI-NISKI-WYSOKI podczas cyklu spawania.
Po wykonaniu prototypu na płytce stykowej, zamontowałem obwód sterujący na samodzielnej płytce proto zawierającej moduł zasilania sieciowego (HiLink HLK-5M05), kondensator i rezystory do odbicia przycisku spawalniczego oraz złącza do wyświetlacza, enkodera, diody, przycisk i wyjście obwodu zasilania. Połączenia i komponenty są pokazane na schemacie (z wyjątkiem modułu zasilania sieciowego).
Jest też złącze (na schemacie J3) dla włącznika nożnego połączone równolegle z przyciskiem spawalniczym, dzięki czemu spawanie można rozpocząć albo z panelu, albo za pomocą włącznika nożnego, co uważam za dużo wygodniejsze.
Złącze J4 jest podłączone do wejścia transoptora obwodu mocy, które w prototypie jest zamontowane na osobnej płytce proto.
Do połączenia z wyświetlaczem (złącze J6) okazało się, że łatwiej jest użyć 4-żyłowego płaskiego kabla z dwoma przewodami prowadzącymi do dwupinowego złącza (odpowiadającego pinom 1, 2 J6) i dwóch przewodów z żeńskim Dupont złącza idące bezpośrednio do pinów A4 i A5. W A4 i A5 przylutowałem dwupinowe męskie złącze bezpośrednio na górze płytki Pro Mini.
Prawdopodobnie dodam również debouncing dla przycisku enkodera w ostatecznej wersji. Ulepszony projekt PCB dla tego projektu jest opisany w osobnej instrukcji.
Krok 6: Obwód zasilania
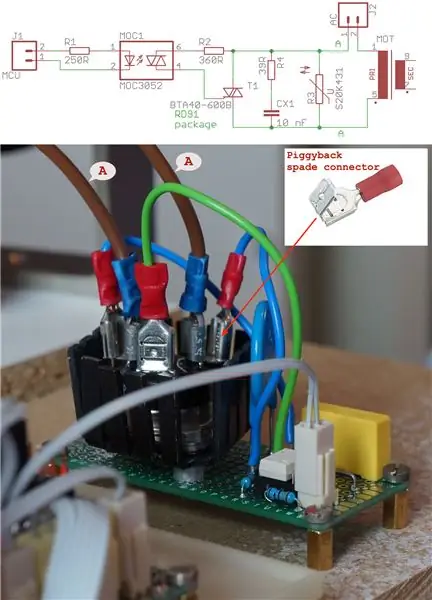
OSTRZEŻENIE: Obwód zasilania działa przy napięciu sieciowym o prądach wystarczających do zabicia cię. Jeśli nie masz doświadczenia z obwodami napięcia sieciowego, nie próbuj ich budować. Do wykonywania wszelkich prac na obwodach napięcia sieciowego należy używać co najmniej transformatora izolującego.
Schemat obwodu mocy jest bardzo standardowy dla kontroli obciążenia indukcyjnego za pomocą triaka. Sygnał z obwodu sterującego steruje stroną emiterową transoptora MOC1, strona detektora z kolei steruje bramką triaka T1. Triak przełącza obciążenie (MOT) za pośrednictwem sieci tłumiącej R4/CX1.
Transoptor. MOC3052 to transoptor z losową fazą, a nie z przejściem przez zero. Używanie przełączania losowo-fazowego jest bardziej odpowiednie niż przełączanie z przejściem przez zero w przypadku dużych obciążeń indukcyjnych, takich jak MOT.
TRIAK. Triak T1 to BTA40 przystosowany do ciągłego prądu w stanie włączenia 40A, co może wydawać się przesadą pod względem prądu pobieranego przez MOT w stanie ustalonym. Biorąc jednak pod uwagę, że obciążenie ma dość wysoką indukcyjność, ocena, o którą musimy się martwić, to nie powtarzalny szczytowy prąd w stanie włączenia. Jest to prąd rozruchowy obciążenia. Będzie on pobierany za każdym razem podczas stanu nieustalonego włączenia przez MOT i będzie kilkakrotnie wyższy niż prąd w stanie załączenia. BTA40 charakteryzuje się niepowtarzającym się szczytowym prądem przepięciowym 400 A przy 50 Hz i 420 A przy 60 Hz.
Pakiet TRIAK. Kolejnym powodem, dla którego warto wybrać BTA40, jest to, że jest on dostarczany w opakowaniu RD91 z izolowaną klapką i ma męskie końcówki widełkowe. Nie wiem jak wy, ale raczej wolę izolowaną zakładkę do półprzewodników mocy na napięcie sieciowe. Dodatkowo męskie zaciski widełkowe oferują solidne połączenie mechaniczne, które pozwala całkowicie utrzymać ścieżkę wysokoprądową (przewody oznaczone na schemacie jako A) z dala od proto lub płytki PCB. Ścieżka wysokoprądowa przebiega przez (grubsze) brązowe przewody oznaczone na rysunku A. Brązowe przewody są podłączone do zacisków widełkowych triaka za pomocą zacisków typu piggyback, które są również podłączone do sieci RC na płycie za pomocą (cieńszych) niebieskich przewodów. Dzięki tej sztuczce montażowej ścieżka wysokiego prądu jest poza proto lub płytką PCB. W zasadzie to samo można by zrobić z drutami lutowniczymi na nogach bardziej popularnego pakietu TOP3, ale montaż byłby mniej niezawodny mechanicznie.
W przypadku prototypu zamontowałem triak na małym radiatorze z zamiarem wykonania kilku pomiarów temperatury i ewentualnego zamontowania go na większym radiatorze lub nawet w bezpośrednim kontakcie z metalową obudową w celu ostatecznego zbudowania. Zauważyłem, że triak ledwo się nagrzewa, częściowo dlatego, że jest odpowiednio przewymiarowany, ale głównie dlatego, że większość rozpraszanej mocy w złączu wynika z przełączania stanu przewodzenia, a triak wyraźnie nie przełącza się często w tej aplikacji.
Sieć tłumiąca. R4 i CX1 to sieć tłumiąca, która ogranicza szybkość zmian widzianych przez triak, gdy obciążenie jest wyłączone. Nie używaj żadnego kondensatora, który możesz mieć w pojemniku na części zamienne: CX1 musi być kondensatorem typu X (lub lepiej typu Y) przystosowanym do pracy z napięciem sieciowym.
Warystor. R3 to warystor zwymiarowany zgodnie z wartością szczytową napięcia sieciowego. Schemat przedstawia warystor o napięciu znamionowym 430 V, który jest odpowiedni dla napięcia sieciowego 240 V (uwaga, napięcie znamionowe w kodzie warystora jest wartością szczytową, a nie wartością skuteczną). Użyj warystora o wartości szczytowej 220 V dla napięcia sieciowego 120 V.
Awaria komponentu. Dobrą praktyką jest zadać sobie pytanie, jakie byłyby konsekwencje awarii komponentów i zidentyfikować najgorsze scenariusze. Złą rzeczą, która może się zdarzyć w tym obwodzie, jest awaria triaka i zwarcie zacisków A1/A2. Jeśli tak się stanie, MOT będzie stale pod napięciem, dopóki triak jest zwarty. Gdybyś nie zauważył brzęczenia transformatora i spawał z MOT na stałe, przegrzałbyś / zniszczył obrabiany przedmiot / elektrody (nieładne) i prawdopodobnie przegrzał / stopił izolację kabla (bardzo źle). Dlatego dobrym pomysłem jest wbudowanie ostrzeżenia o tym stanie awarii. Najłatwiej jest podłączyć lampę równolegle do pierwotnego MOT. Lampka zaświeci się, gdy MOT jest włączony i zapewni wizualną wskazówkę, że spawacz pracuje zgodnie z przeznaczeniem. Jeśli światło zapali się i pozostanie włączone, wiesz, że nadszedł czas, aby wyciągnąć wtyczkę. Jeśli oglądałeś film na początku, być może zauważyłeś, że podczas spawania w tle zapala się i gaśnie czerwona żarówka. Tym właśnie jest to czerwone światło.
MOT nie jest zbyt dobrym obciążeniem, ale mimo początkowego zaniepokojenia niezawodnością przełączania przez obwód mocy, nie widziałem żadnych problemów.
Krok 7: Uwagi końcowe
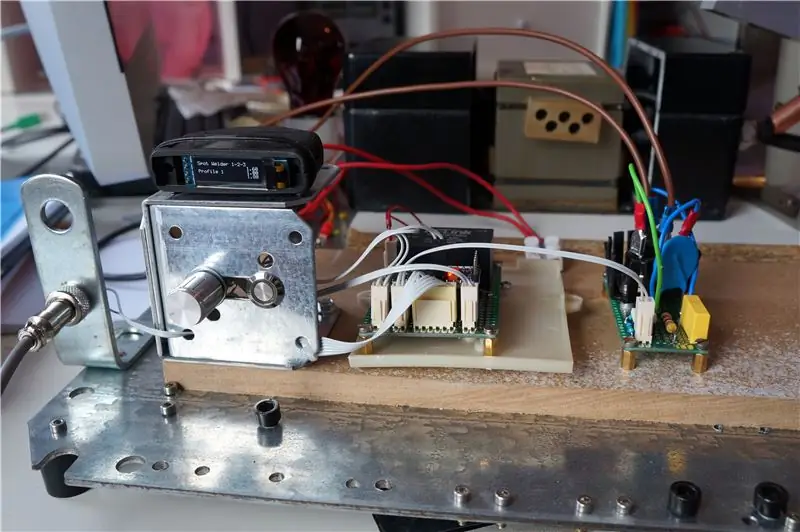
Cóż, po pierwsze wielkie podziękowania dla wielu ludzi, którzy poświęcili czas na wyjaśnienie w sieci, jak zbudować zgrzewarkę punktową za pomocą przerobionego transformatora do kuchenki mikrofalowej. To był ogromny bootstrap dla całego projektu.
Jeśli chodzi o oprogramowanie sprzętowe Spot Welder 1-2-3, napisanie kodu bez abstrakcji zapewnianych przez szereg bibliotek oprócz standardowego Arduino IDE byłaby długą i żmudną pracą. Uważam, że te biblioteki timera (RBD_Timer), kodera (ClickEncoder), menu (MenuSystem) i EEPROM (EEPROMex) są bardzo przydatne.
Kod oprogramowania sprzętowego można pobrać z repozytorium kodów Spot Welder 1-2-3.
Jeśli planujesz to zbudować, zdecydowanie sugeruję użycie opisanego tutaj projektu PCB, który zawiera szereg udoskonaleń.
Zalecana:
Zgrzewarka punktowa 1-2-3 Płytka drukowana Arduino: 4 kroki
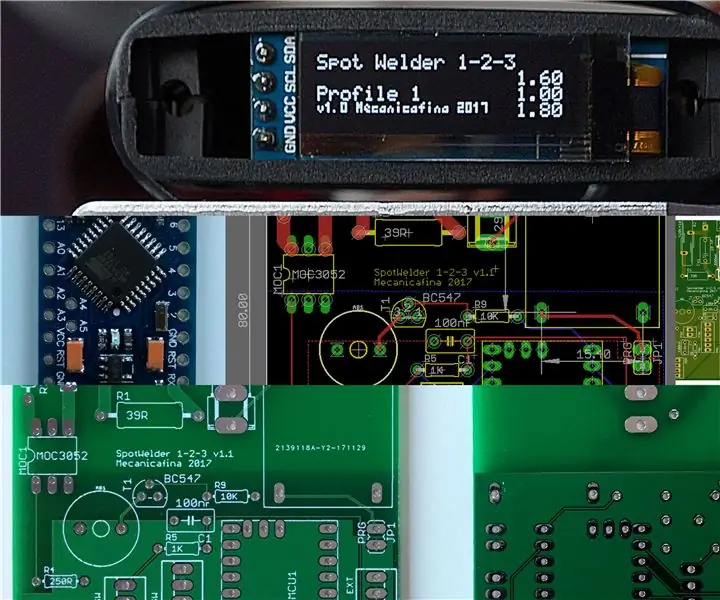
Spot Welder 1-2-3 Arduino Printed Circuit Board: Jakiś czas temu napisałem instrukcję, w której wyjaśniłem, jak w wyrafinowany sposób sterować zgrzewarką punktową za pomocą Arduino i powszechnie dostępnych części. Wiele osób zbudowało obwód sterujący i otrzymałem bardzo zachęcające opinie. To jest
Prosta zgrzewarka punktowa wykorzystująca akumulator samochodowy do budowy akumulatora litowo-jonowego: 6 kroków
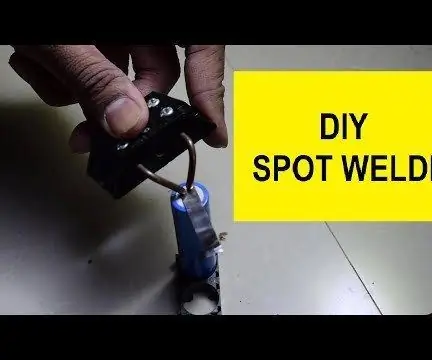
Prosta zgrzewarka punktowa wykorzystująca akumulator samochodowy do budowy akumulatora litowo-jonowego: W ten sposób wykonałem zgrzewarkę punktową z akumulatorem samochodowym, który jest przydatny do budowy akumulatorów litowo-jonowych (litowo-jonowych). Za pomocą tego zgrzewarki punktowej udało mi się zbudować pakiet 3S10P i wiele spoin. Ta instrukcja zgrzewarki punktowej obejmuje blok funkcjonalny Dia
Zgrzewarka punktowa Mini DIY 18650: 10 kroków
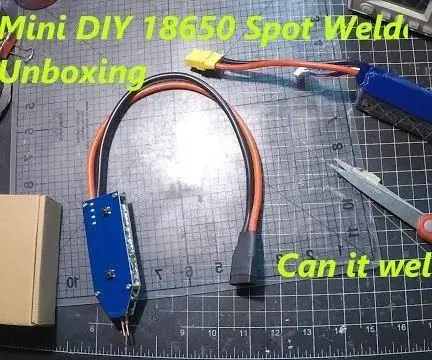
Mini DIY 18650 Spot Welder: Zauważyłem na grupach na Facebooku i oglądam inne filmy, majsterkowiczów pytających, czy ci spawacze są warci niewielkiej ceny. Pewnego dnia surfowałem po Amazonce i zauważyłem, że są one lokalne w stanach. Kupiłem więc 5 z nich i zdecydowałem, że
Łatwy DIY 12V 220CCA 340CA Akumulator samochodowy 18650 Zgrzewarka punktowa (#4. kompilacja): 4 kroki
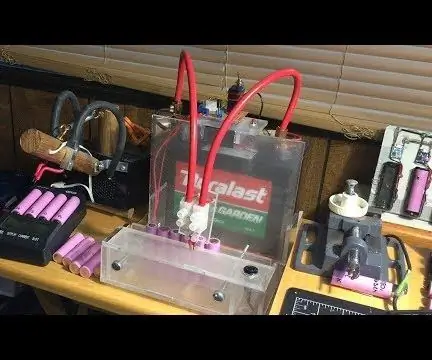
Łatwy DIY 12V 220CCA 340CA Akumulator samochodowy 18650 Zgrzewarka punktowa (#4th Build): Oto czwarta zgrzewarka do kart, którą do tej pory stworzyłem. Pro Tip dla tego Instructable to sposób na zbudowanie taniej i wydajnej spawarki z zakładkami baterii za mniej niż 30 USD. (bez wymyślnego ogrodzenia) Można to łatwo zbudować za mniej niż 40 USD. Ten postanowiłem
Domowa zgrzewarka punktowa DIY: 4 kroki
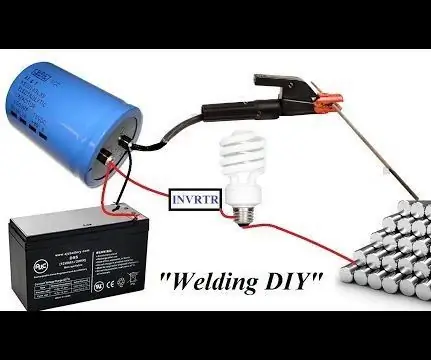
Domowa zgrzewarka punktowa DIY: Hej chłopaki!!!! W tej instrukcji dowiesz się, jak zrobić zgrzewarkę punktową w domu za pomocą baterii kondensatorów. Ta konfiguracja jest oszałamiająca do spawania w odległych obszarach, a nawet w drodze. Mimo że wielu z nas ma już spawarki elektrodowe b